Erklärung zum Umbau:
Der hier beschriebene Umbau und die daraus resultierende Dokumentation stellt keine Bauanleitung oder Betriebsanweisung dar! Es ist mein Hobby, ich arbeite an meinem Fahrzeug und ich habe alle Arbeiten nach meinem Wissen und meiner Erfahrung ausgeführt. Für Fehler oder falsche Informationen auf dieser Seite kann ich keine Garantie erteilen oder haftbar gemacht werden.
DER ZETEC – MOTOR:
3. JANUAR 2017
Ich habe das Projekt “ Aufbau Zetec – Motor “ aufgegeben. Der Westfield steht zum Verkauf, ich kann und will das Projekt nicht beenden.
25. APRIL 2016
Meine neue Garage soll jetzt Ende April geliefert werden. Hoffentlich, damit es endlich wieder weiter geht am Motor. Im Moment habe ich die Lager hier liegen, jedoch fehlt mir schlicht und einfach meine Werkstatt. Ich bin umgezogen und im neuen Haus habe ich nun zwar die neue Werkstatt fast komplett eingerichtet, aber der Platz für den Westfield und die Motorenwerkbank fehlt. Das Fundament für die neue Garage ist fast komplett fertig und ich warte auf die Lieferung der Holzgarage. Diese war für Anfang März , dann Ende März und nun für Ende April angesagt. Aus 4 Wochen Lieferzeit sind nun fast 3 Monate vergangen.Das ist mehr als ärgerlich aber ausser warten kann ich nicht viel machen.
26. MÄRZ 2016
Viele werden sich fragen oder haben mir geschrieben dass es nicht weiter geht. Das stimmt, hat aber auch seinen Grund. Ich habe erhebliche Probleme die Kurbelwellenlager und Pleuellager in STD Ausführung zu bekommen. Mein Motorenbauer hat diese nicht bis jetzt noch nicht bekommen und so liegt mein Motor seit Wochen unberührt auf der Werkbank. Ich habe BURTON angerufen und so wie es aussieht könnte BURTON die Lager liefern. Wenn nicht werden wir die Kurbelwelle und die Pleuel abschleifen und die Kurbelwellenlager 0.25 einbauen. Ich werde noch die nächste Woche abwarten, sollten die Lager bis dahin nicht eingetroffen sein werden wir die engeren Lager in 0.25 einbauen. Gott sei Dank habe ich noch einen Zetec im Westfield eingebaut und kann wenigstens fahrenn wenn das Wetter endlich besser wird.
10. FEBRUAR 2016
Der Motor steht noch immer beim Motoreninstandsetzer. Der Zetec müsste jedoch nächste Woche fertig werden und dann kann ich endlich mit dem Zusammenbau beginnen. Komplett kann ich den Motor jedoch nicht zusammenbauen da ich mir eine neue Werkstatt mit Garage baue. Die Werkstatt ist fast fertig, den Aufbau der Garage, es handelt sich um eine Holzgarage, kann ich wegen des dauernd schlechten Wetters nicht beginnen.
08. JANUAR 2016
Die Kurbelwellenlager in STD Ausführung sind laut Ford nicht mehr lieferbar. Im Zubehörhandel wie Mahle Motorsport, Burton, sehr wohl noch. Aber die Lieferungen dauern ewig. In der Zwischenzeit werde ich meinen Motorblock zum Motoreninstandsetzer bringen damit der Block geplant werden kann. Mit der Zeit ist jeder Block uneben geworden durch die Hitze. Im mittleren Bereich bei Zylinder 2 und 3 am meisten weil dort die Temperaturen am höchsten sind. Die Bilder und weitere Infos folgen
03. JANUAR 2016
Die
neuen Kurbelwellenlager sind eingebaut. Diese wurden vor dem Einsetzen
der Kurbelwelle sehr sorgfältig gereinigt und alle Reste des Plastigage
wurden sehr sorgfältig entfernt. Die Lager wurden dann eingeölt. Die
Kurbelwelle vorsichtig in die Kurbelwellenlager einlegen und vorsichtig
drehen. Das hat bei mir mit den verwendeten Kurbelwellenlager nicht
funktioniert. Schon beim Einlegen der Kurbelwelle bemerkte ich ein
leichtes Klemmen. Erst ein Telefongespräch mit “ RS – Andreas „, ein
Kollege aus dem Gelben Forum, brachte Licht ins Dunkle. Ich habe
schlicht und einfach die falschen Kurbelwellenlager bekommen. Ich wollte
Kurbelwellenlager in der STD – Ausführung und habe Kurbelwellenlager in
0.25 bekommen. Die neuen STD Kurbelwellenlager sind bereits bei Mahle
bestellt und so könnte ich die Kurbelwelle Ende der Woche einbauen.
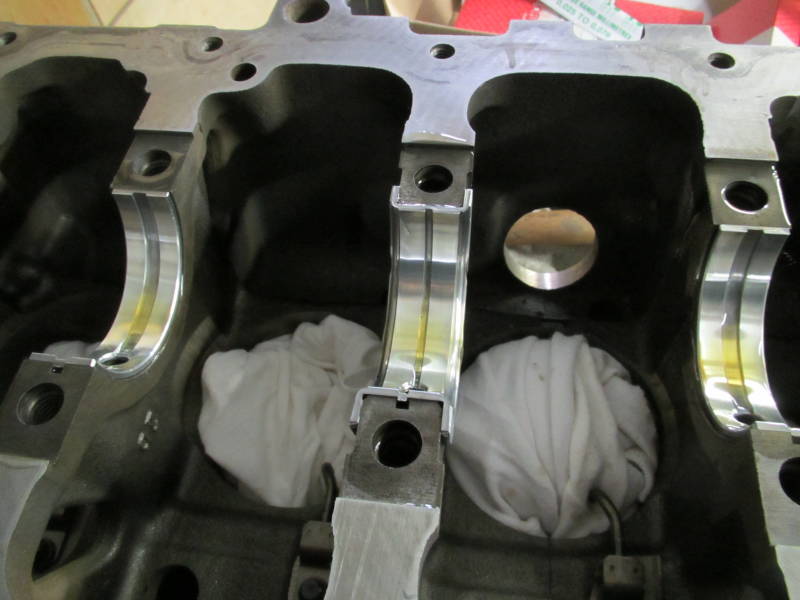
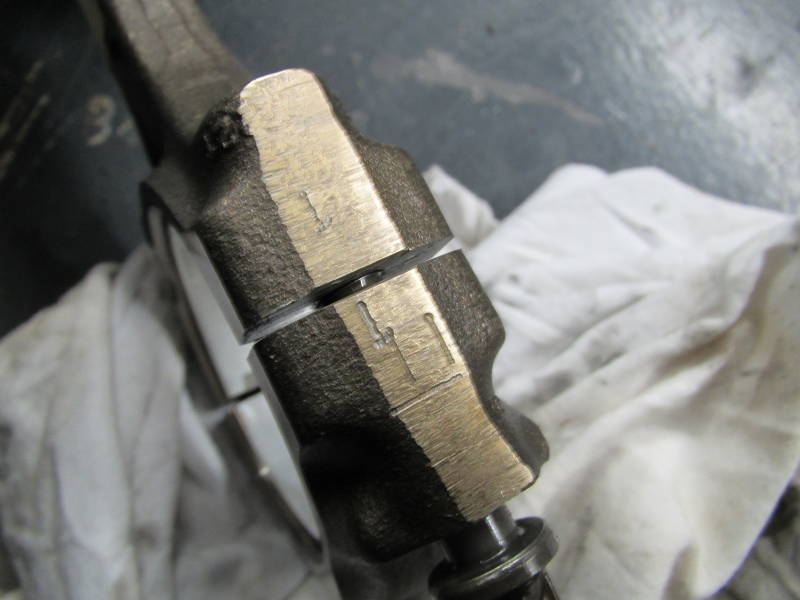
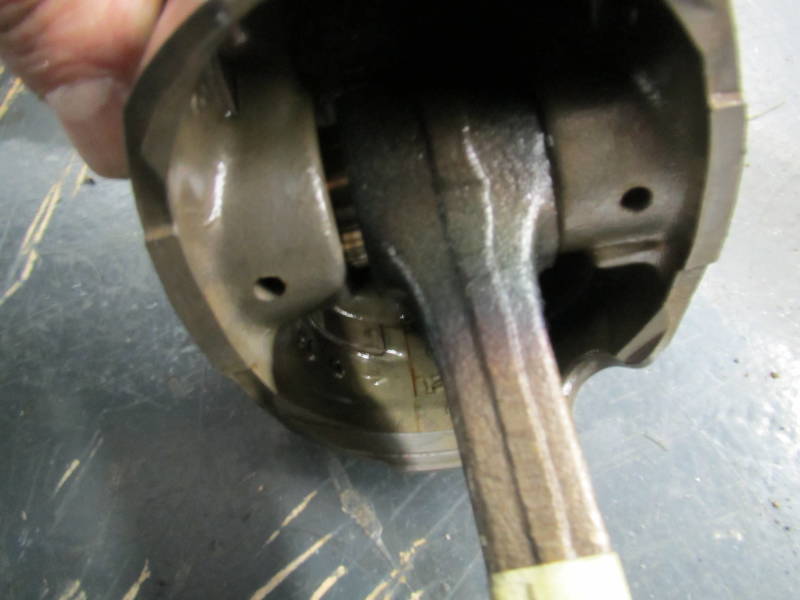
Auf
dem rechten Foto ist der Kolben des Zetec – Motors zu sehen. Im Innern
des Kolbens, unten zu sehen, ist ein Pfeil vorhanden. Dieser Pfeil zeigt
auf die Zahnriemenseite. Der Kolben muss auch unbedingt in dieser
Richtung eingebaut werden. Desweiteren gibt es auf der rechten Seite am
Pleuelauge rechts auch diesen Alugusswulst. Dieser Wulst zeigt auch
immer zur Zahnriemenseite. Die Kolben sind noch in einem sehr guten
Zustand und bekommen neue Kolbenringe.
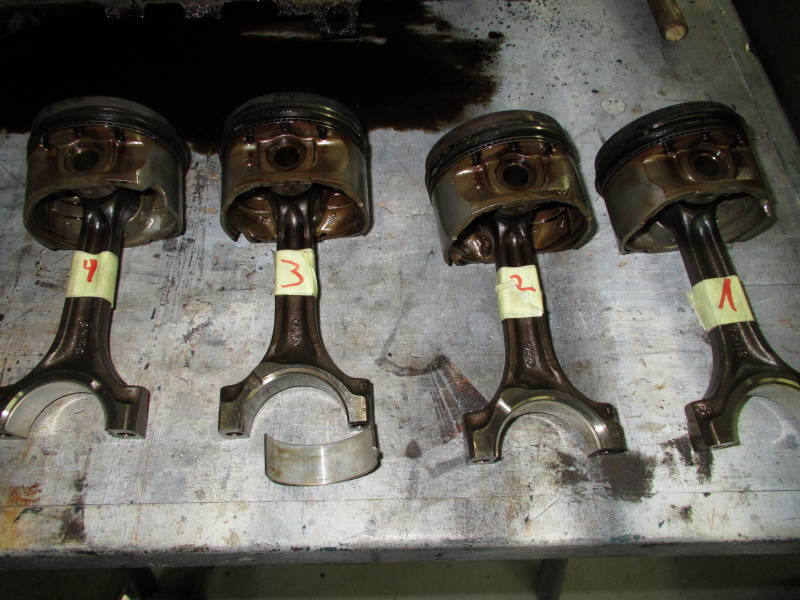
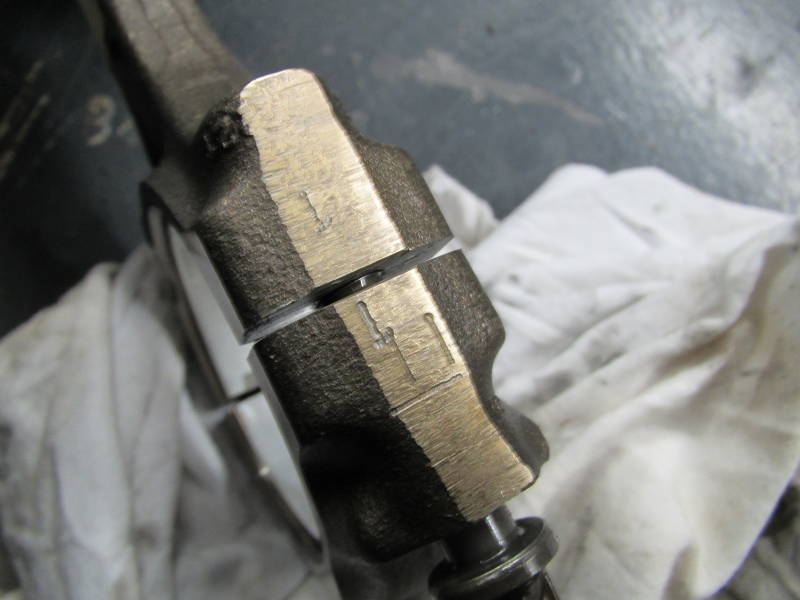
Auf dem rechten Foto ist die Zetec – Ölpumpe zu sehen. Diese wurde sorgfältig gereinigt und könnte auch so wieder eingebaut werden. Aber ich denke ich werde eine neue Ölpumpe einbauen.
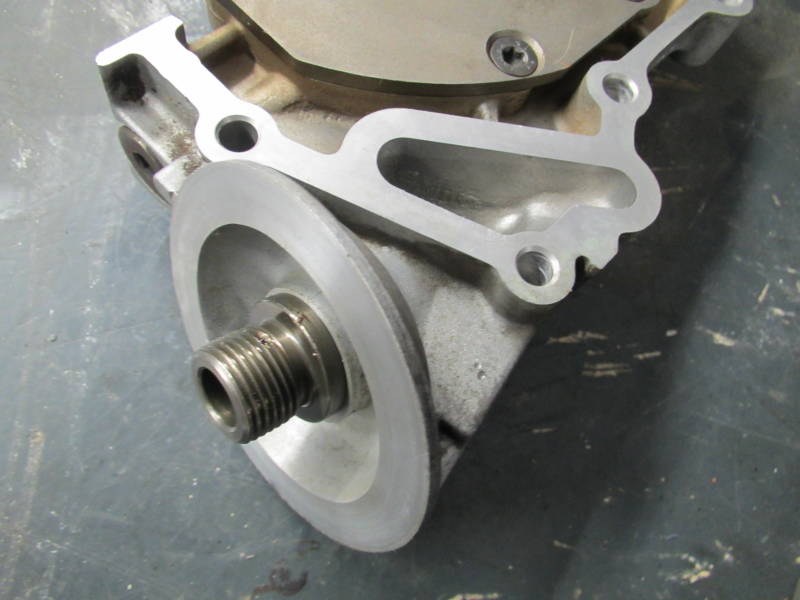
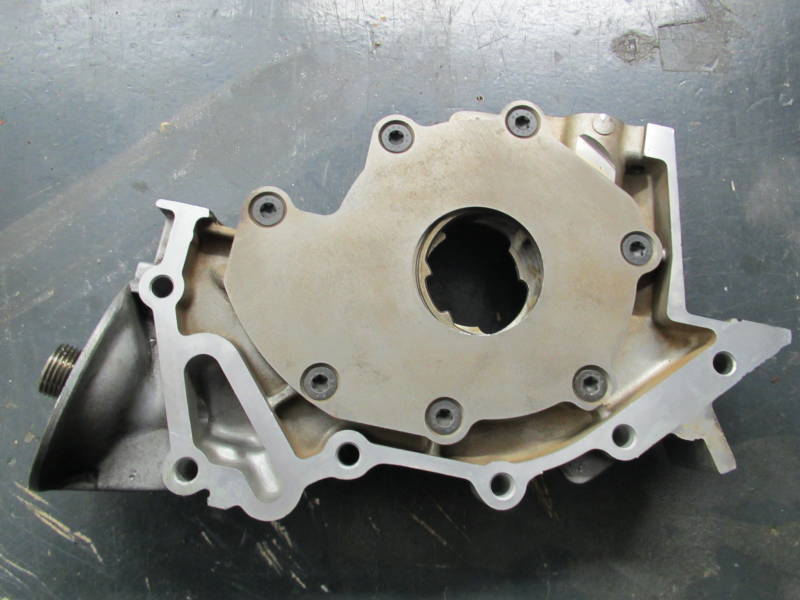
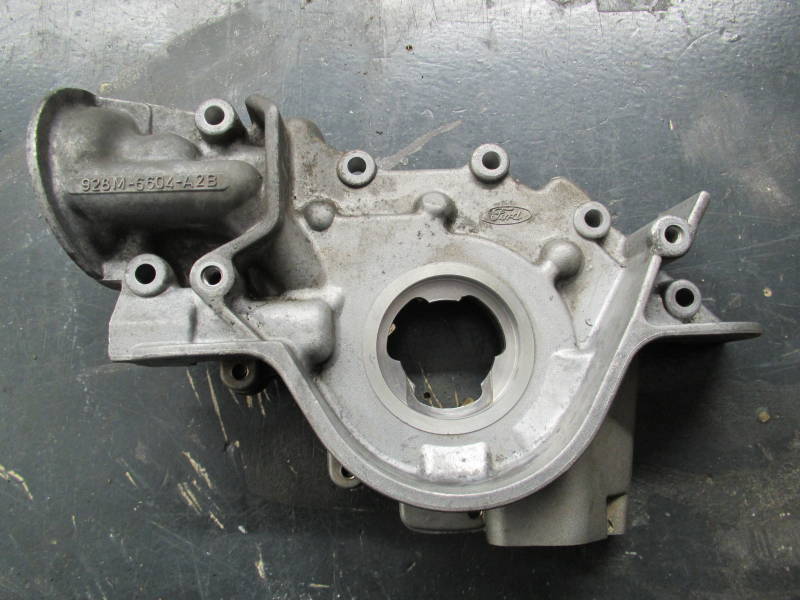
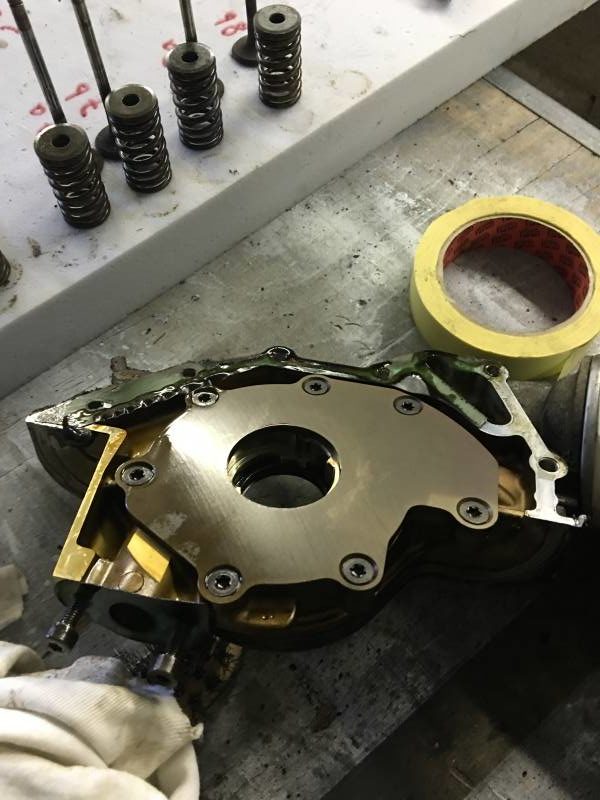
30. DEZEMBER 2015
Die Ölpumpe:
Die originale Ölpumpe des Zetec Motors ist sehr hochwertig und tadellos im Betrieb. Die Fördermenge der Ölpumpe ist durch ihre Baugröße begrenzt. Durch den normalen Verschleiß an der Ölpumpe, der durch den längeren Betrieb entsteht, sinkt auch die Leistung der Ölpumpe. Die Ölpumpen für den Zetec Motor kosten nicht die Welt und ich würde wenn Zweifel bestehen stets eine neue Ölpumpe einbauen. Da ich im Moment 2 Zetec Motoren aufbaue und mir die genauen gefahrenen Kilometerzahlen nicht bekannt sind werde ich beide Ölpumpen austauschen. In meinem Fall denke ich, wenn beide Motoren schon mal komplett zerlegt sind, kommt es auf die Mehrkosten aus dem Kauf einer neuen Ölpumpe auch nicht mehr an und ich gehe damit auf Nummer sicher. Bitte nicht falsch verstehen, Ölpumpen halten in der Regel ein Motor- Leben locker aus. Nur in meinem Fall kannte ich das Vorleben beider Motoren nicht und die gelaufenen Kilometer waren mir auch nicht bekannt. Nur aus dem Grund würde ich wie folgt vorgehen:
Ein neu aufgebauter Motor sollte eine neue Ölpumpe bekommen wenn:
- die Kilometerzahl des Motors nicht bekannt ist.
- das genaue Vorleben oder die Herkunft des Motors nicht bekannt ist.
- wenn jegliche Unterlagen zu dem Motor, wie Inspektionen, Rechnungen usw., fehlen.
- die Kilometerzahl jenseits der 100.000 km liegt.
Kolben und Pleuelstangen:
Die Frage ob ein Kolben ersetzt werden muss oder nicht hängt sehr oft vom Zustand der oberen Ringnut des Kolbens ab. Weitere Kriterien sind der Zustand des Kolbenhemds und die Tatsache ob sich am Kolben Risse befinden. Die in den meisten modernen Motoren verwendeten Kolben sind gegossene Kolben. Moderne Motoren, wie der Zetec Motor haben bereits Hochleistungskolben verbaut die durch Öleinspritzdüsen von unten zusätzlich gekühlt werden. Die original eingebauten Serienkolben des Ford Zetec Motors können gelegentliche Drehzahlspitzen von 8000 U/min aushalten. ( keine Gewähr ) Für permanente hohe Drehzahlen sind diese Kolben nicht geeignet. Das Aluminiummaterial des Kolbens wird durch die permanent hohe Drehzahl und die dadurch resultierende höhere Temperatur weicher. Der Verschleiß an der oberen Ringnut und am Kolbenhemd nimmt zu. Für permanente hohe Drehzahlen des Motors, wird der Einbau von höherwertigen Kolben , wie Schmiedekolben, notwendig.
Die meisten Pleuelstangen in modernen Motoren halten problemlos Drehzahlen von 6000 – 6500 U/min locker aus. Die serienmäßig verbauten Pleuelstangen des Zetec Motors sind sehr hochwertig und halten diese Drehzahlen locker aus, wenn diese nicht permanent anliegen. Da ich meinen Zetec Motor nicht auf der Rennstrecke oder an Bergrennen einsetzen werde, sondern nur gelegentlich gerne mal schnell bewegen möchte, werde ich die originalen Kolben und Pleuelstangen weiter verwenden. Der Einbau von Schmiedekolben und Stahlpleuel ist sehr schön, die dadurch entstehenden Mehrkosten sind auch durchaus nachvollziehbar, aber wenn der Motor nicht dauernd bei hohen Drehzahlen über 6000 U/min bewegt wird ist der Einbau von Schmiedekolben und Stahlpleuel meiner Meinung nicht notwendig.
Die Kurbelwelle des Zetec Motors ist 5 fach gelagert und verträgt Drehzahlen bis 7000 U/min problemlos. Meine Kurbelwelle wurde neu gelagert und mit dem erleichterten Schwungrad ausgewuchtet.
27. DEZEMBER 2015
Kurbelwellenlager und Pleuellager:
Kurbelwellenlager und Pleuellager müssen sehr sorgfältig zusammengebaut werden. Dabei müssen die Lager mit den genauen Lagerspielen und Toleranzen eingebaut werden. Einfach mal so die Kurbelwellenlager und Pleuellager zusammen bauen und hoffen…….funktioniert nicht. Die Kurbelwellenlager haben eine Nase welche genau in die Hauptlagerbohrung oder Hauptlagerbrücke passt. Die Kurbelwellenlagerschale wird mit der Nase genau in die dafür vorgesehene Vertiefung im Block eingesetzt. Man lässt die Lagerschale ca 4-5mm am Ende überstehen um anschließend die Lagerschale von Hand sorgfältig in die Bohrung hinein zu drücken. Dabei achten dass beide Enden der Lagerschale niveaugleich zum Block stehen. Dh. beide Enden müssen eben mit dem Block sein. Beim Einlegen der Lagerschalen unbedingt darauf achten dass die Bohrungen und die Vertiefungen für die Lagerschalennasen absolut sauber sind. Diese am besten mit einem Papiertuch ( nicht mit einem Baumwolle – Tuch o.ä. ) und einer Verdünnung reinigen. Absolute Sauberkeit ist eine gute Voraussetzung dass die Lagerschalen auf der größtmöglichen Fläche in der Bohrung des Motorblocks oder der Hauptlagerbrücke oder Kurbelwellenlagerdeckel sitzt. Den Motorblock auf einem sauberen und stabilen Tisch o. Werkbank abstellen. Am besten mit Papiertüchern arbeiten und nicht mit Baumwolle – Tüchern, wegen der Fusel. Kurbelwelle und Lager nicht auf dem Boden ablegen, sondern immer auf einem sauberen Tuch oder auf einer sauberen Holzunterlage ablegen. Die Lagerschalen für die Bohrungen im Motorblock weisen meisten eine Rille in der Mitte der Lagerschale auf.
Das Einsetzen der Pleuellagerschalen passiert in der gleiche Reihenfolge oder werden unter den gleichen Voraussetzungen eingesetzt wie die Kurbelwellenlagerschalen. Zum Einsetzen kann das Pleuel in einen Schraubstock, natürlich mit Schutzvorrichtung, gespannt werden aber dieses in der Hand halten funktioniert auch sehr gut.
22. DEZEMBER 2015
Ich
habe heute mein Kurbelwellenlagerspiel mit Plastigage gemessen. Wie
bereits geschrieben wird der Plastigage – Faden in das Lager gelegt. Auf
den Fotos sieht man dass ich den Plastigage – Faden auf die
Kurbelwellenlagerfläche gelegt habe. Dann wird der
Kurbelwellenlagerdeckel vorsichtig aufgesetzt und die
Kurbelwellenlagerschrauben mit 80 Nm angezogen. Man beginnt auf der
Zahnriemenseite mit Kurbelwellenlagerdeckel 1. Beim Messvorgang darf die
Kurbelwelle auf keinen Fall gedreht werden! Sind die Schrauben mit dem
vorgeschriebenen Drehmoment angezogen, werden diese sofort wieder gelöst
und der Kurbelwellenlagerdeckel wird vorsichtig abgebaut. Der
Plastigage – Faden wurde platt gedrückt und man erkennt deutlich die
breitere “ Spur “ des Fadens. Mit der Plastigage – Lehre kann man das
Kurbelwellenlagerspiel relativ leicht ermitteln. Laut FORD soll das
Kurbelwellenlagerspiel zwischen 0,020mm und 0,042mm betragen. Bei meinen
Kurbelwellenlagerschalen beträgt das Kurbelwellenlagerspiel 0,038mm,
also noch im „grünen“ Bereich.
WICHTIG: Die Kurbelwelle darf während des Messvorgangs nicht gedreht werden und die Kurbelwelle muss trocken in die Kurbelwellenlagerschalen gelegt werden.
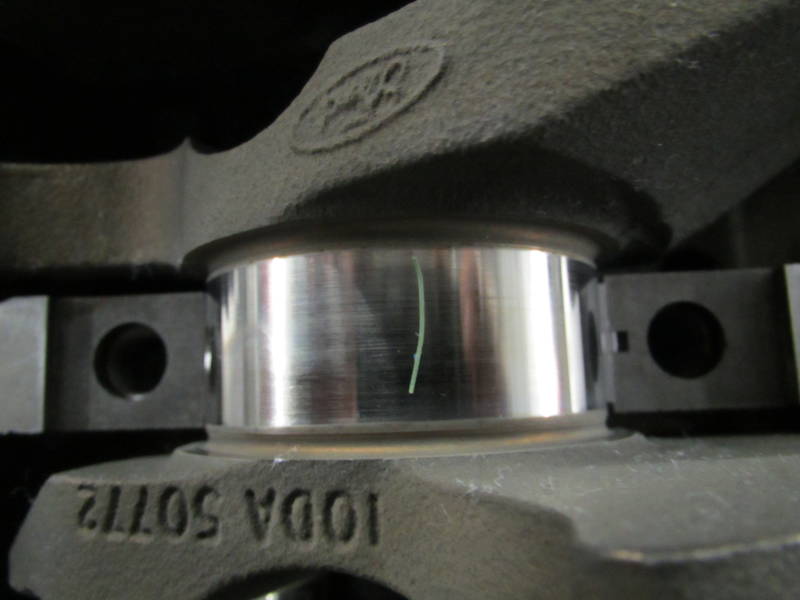
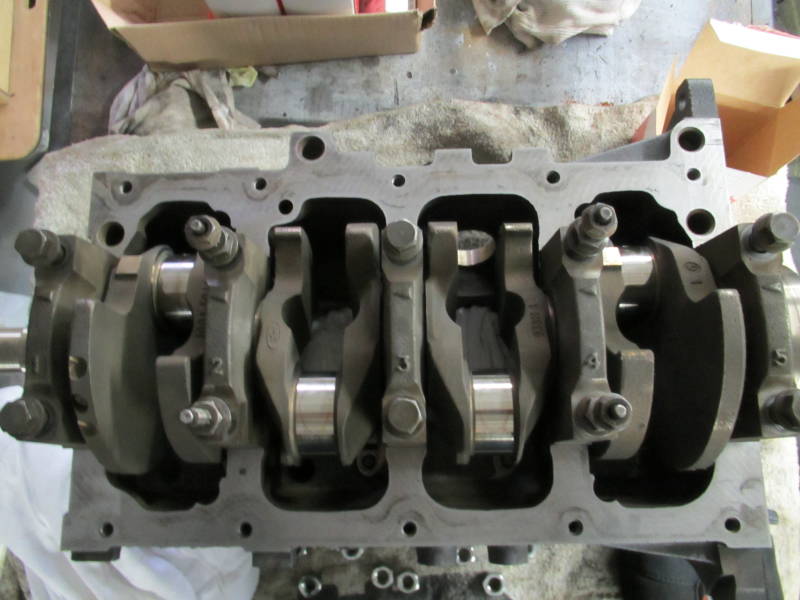
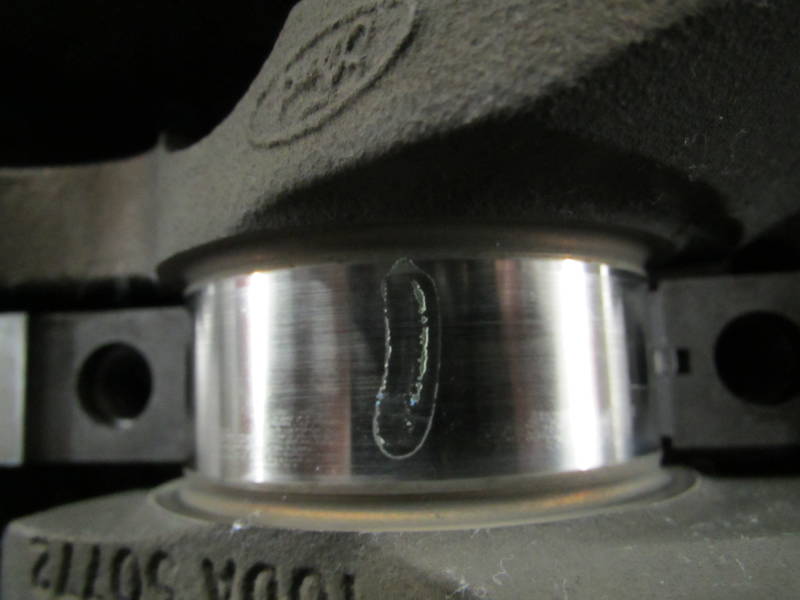
Kurbelwellenlagerdeckel 1 vorsichtig aufsetzen und mit dem vorgeschriebenen Drehmoment von 80 Nm anziehen. Auf dem rechten Foto wurde der Kurbelwellenlagerdeckel bereits abgebaut und man erkennt deutlich die breitere spur des Plastigage – Fadens.
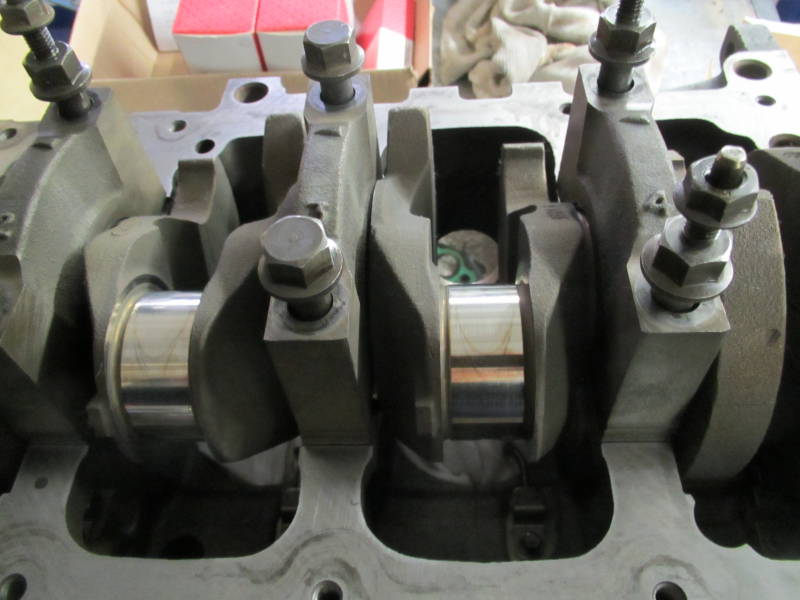
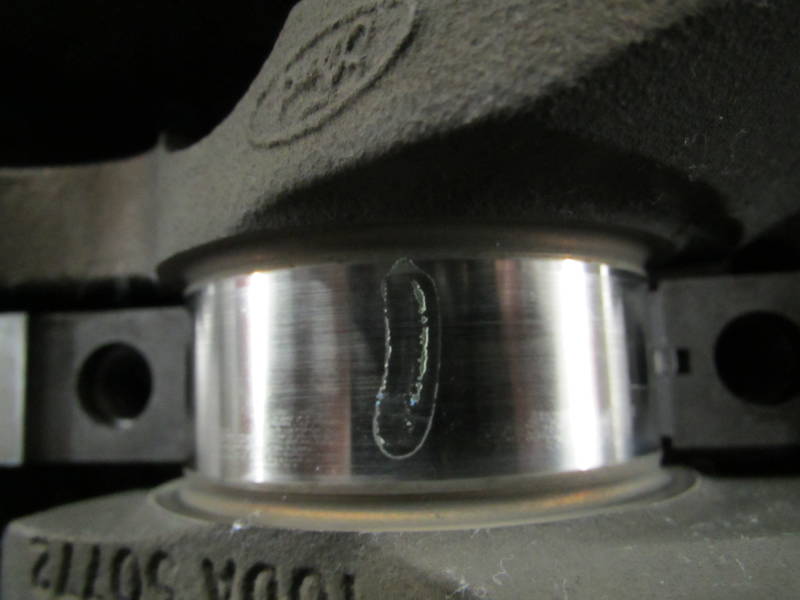
Mit der Plastigage- Lehre wird das Kurbelwellenlagerspiel ermittelt. In diesem Fall beträgt es 0,038mm , erkennbar in dem weißen Feld der Plastigage – Lehre.
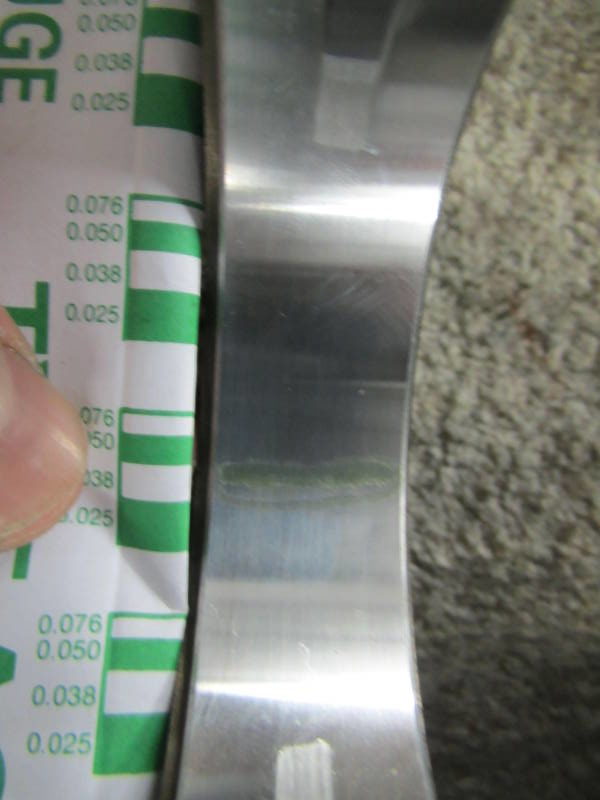
20. DEZEMBER 2015
Die neuen Kurbelwellenlager sind angekommen. Da es bei FORD die original Grössen nicht mehr gibt, sobdern nur noch Stufe 1 -3 mit Übermass, war ich gezwungen Stufe 1 zu nehmen. Sollte das Kurbelwellenlagerspiel unter 0,025mm liegen muss ich die Kurbelwelle zum Motorinstandsetzer bringen. Da mir aber Plastigage zum Messen des Kurbelwellenlagerspiels fehlt konnte ich das Lagerspiel nicht ermitteln. Die Lager sind eingebaut und die Kurbelwelle liegt trocken in den Lagerschalen.
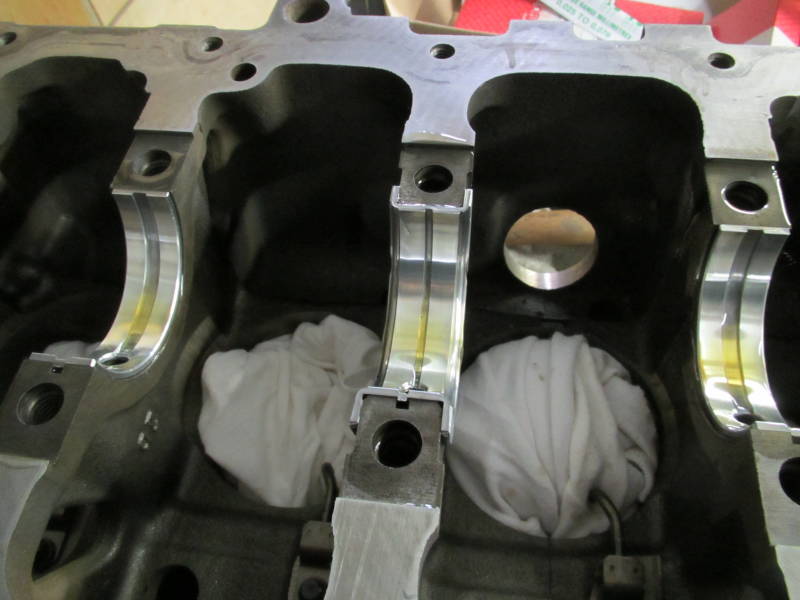
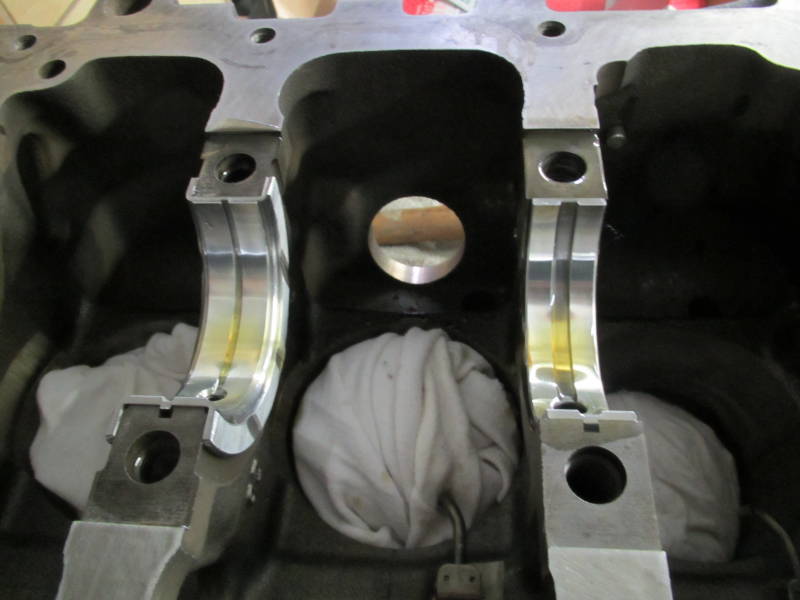
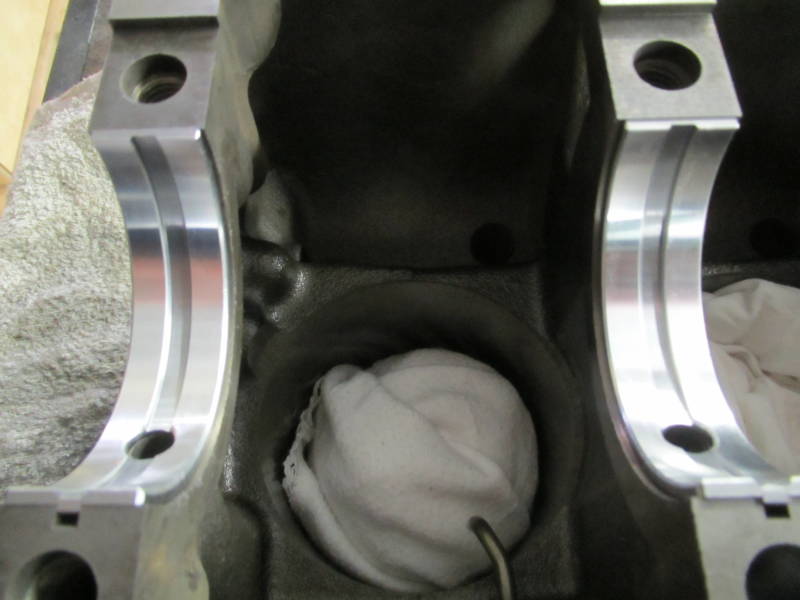

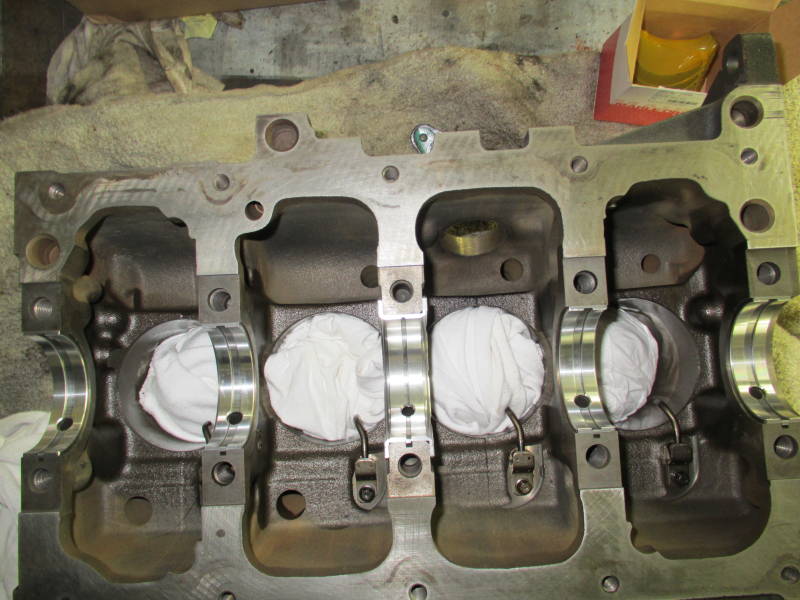
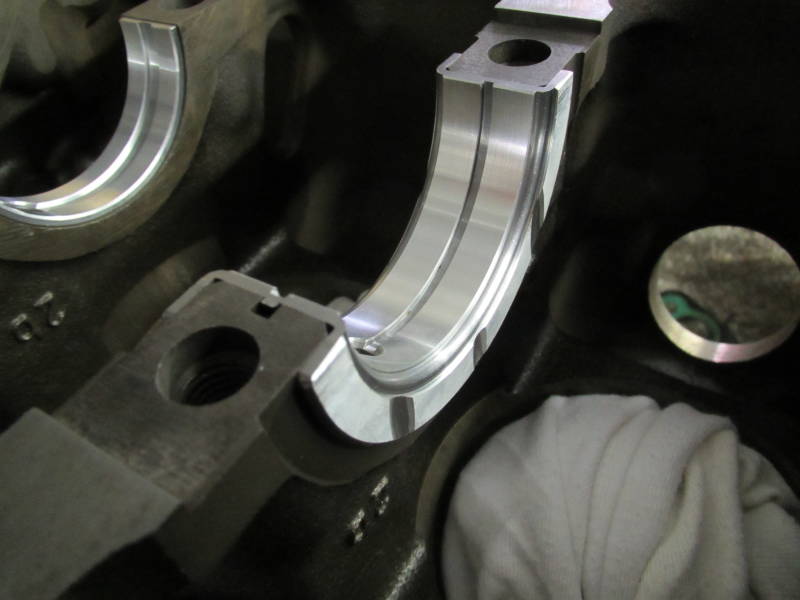
Auf diesen Fotos erkennt man dass die Hauptkurbelwellenlagerschalen mit den neuen Lagerschalen von 1 – 5 bereits eingebaut sind. Die Schrauben der Kurbelwellenlagerschalen sind nur lose eingedeht. Beim Messen des Kurbelwellenlagerspiels werden diese, beginnend bei Lagerschale 1 , mit 80 Nm angezogen. Das gleiche wiederholt sich bei den anderen Lagerschalen.
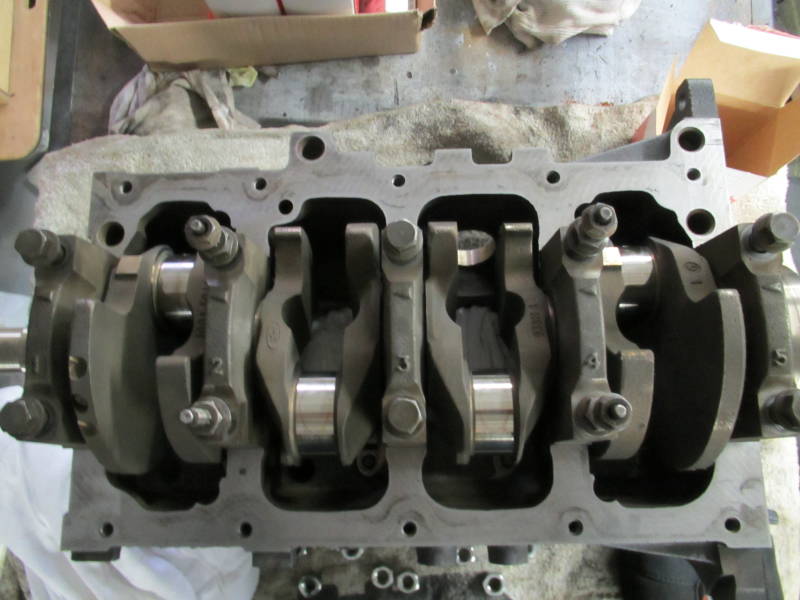
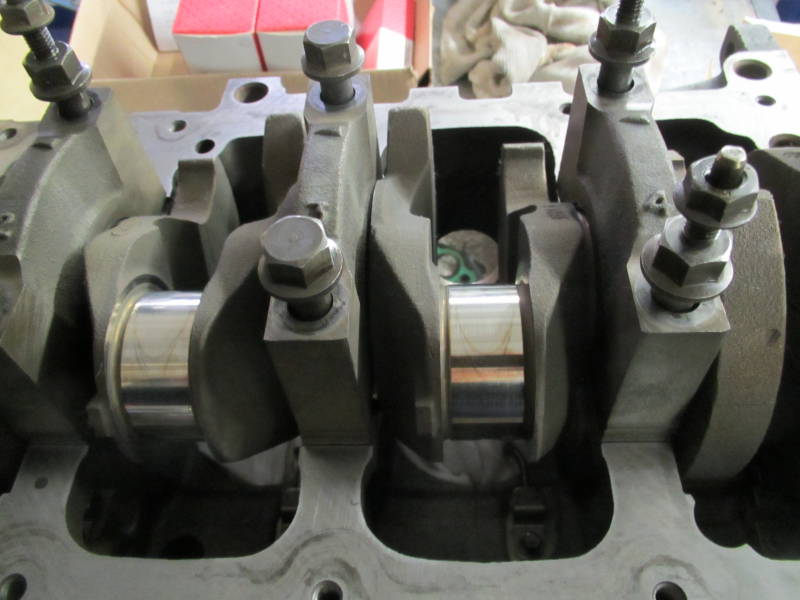
Auf
dem Foto links erkennt man meine erleichterte Schwungscheibe links auf
dem Bild. Rechts ist die originale Schwungscheibe zu sehen. Auf dem
rechten Foto ist die erleichterte Schwungscheibe einzeln zu sehen.
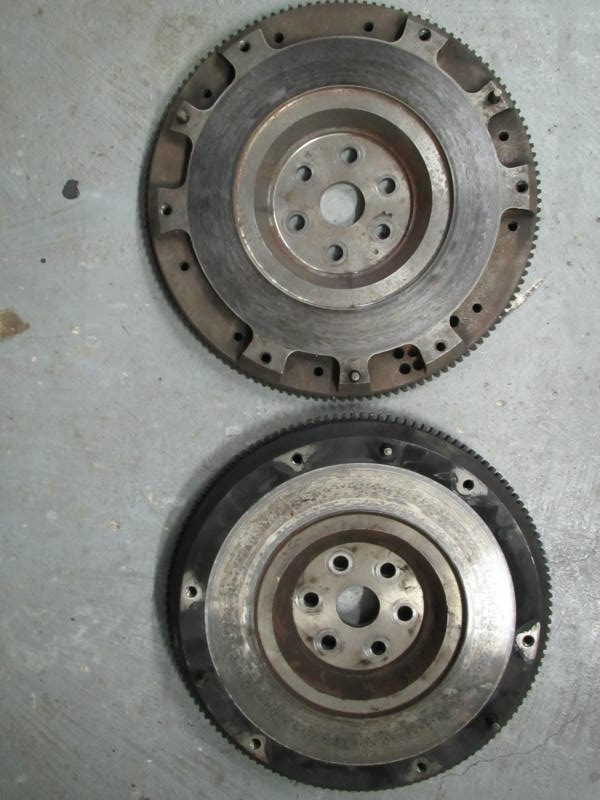
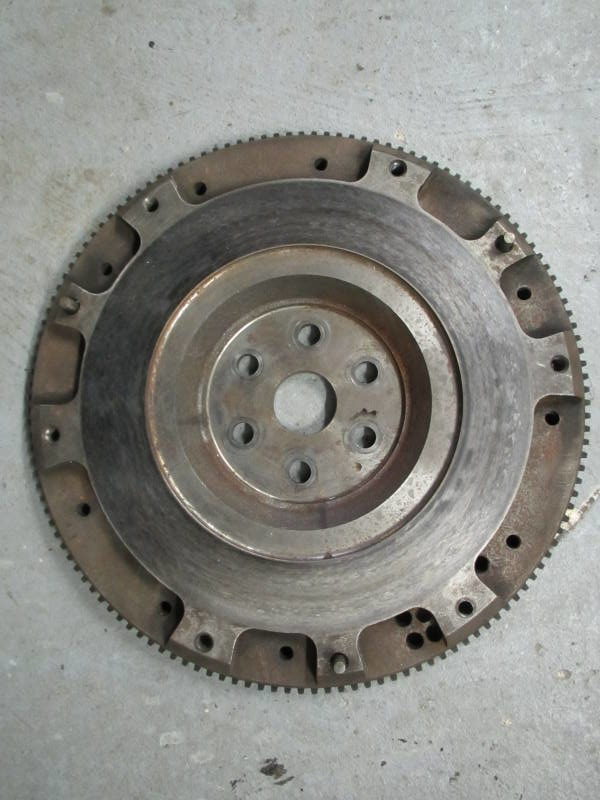
Unten die originale FORD Schwungscheibe. Oben die erleichterte Schwungscheibe
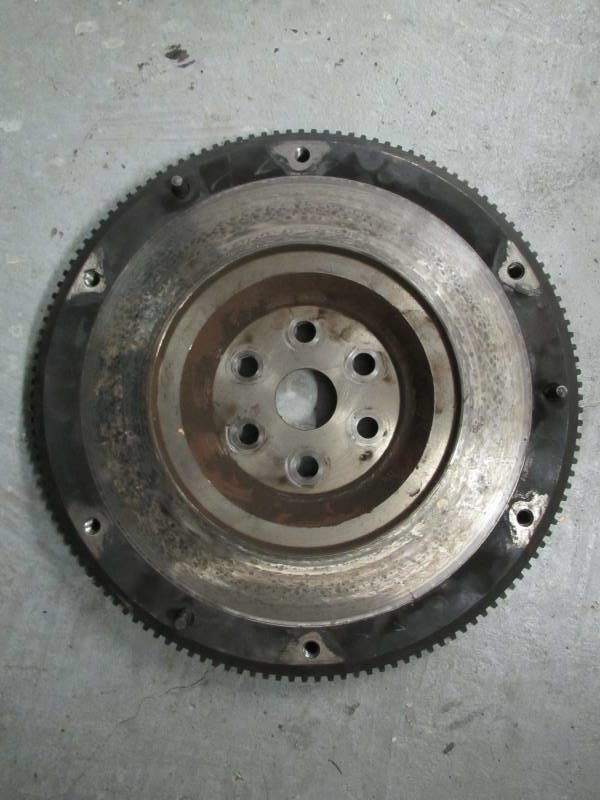
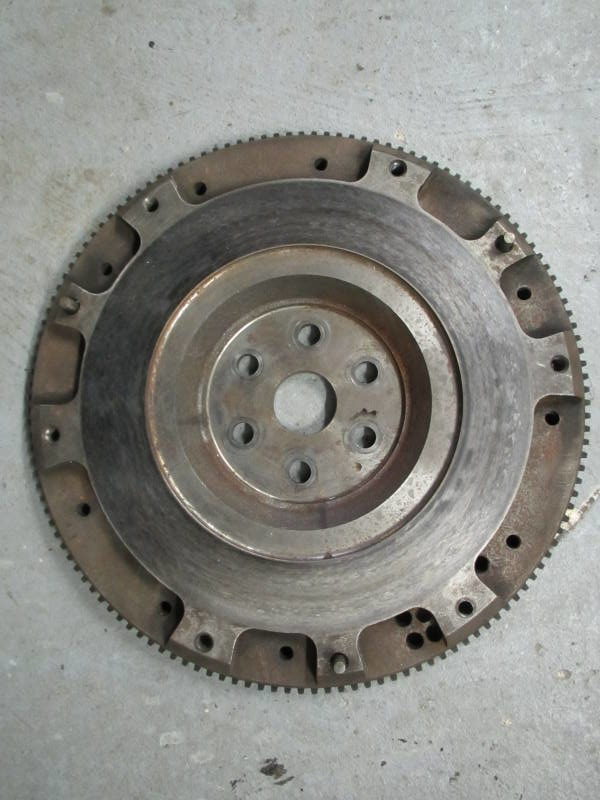
13.DEZEMBER.2015
Heute habe ich mein Schwungrad inspiziert. Das Schwungrad des Zetec 2 ist deutlich leichter als das originale Ford Zetec Schwungrad. Ich werde beide Schwungräder morgen wiegen damit der Unterschied deutlich wird. Im Innern des Schwungrads wurde reichlich Material abgetragen. Der Gewichtsunterschied zwischen beiden Schwungrädern ist deutlich merkbar. Bilder folgen .
12.DEZEMBER.2015
Die geänderte Ölwanne:
Auf den Fotos sieht man die umgeänderte Ölwanne des Zetec Motor 2. Die Ölwanne ist unten flach und wurde dadurch vom Volumen her deutlich vergrößert. Deutlich erkennt man im Innern der Ölwanne die aufgeschweißten Schwallbleche. Auf den unteren Fotos erkennt man meine originale Ölwanne in orange. Die Ölwanne wurde heute komplett gereinigt und lackiert in RAL 2009. Die Ölpumpe wurde komplett gereinigt und der Radialdichtring wurde entfernt. Der Radialdichtringträger für die Kurbelwelle hinten mit dem großen Radialdichtring wurde gereinigt und der Radialdichtring wurde entfernt. Beide Radialdichtringe, Ölpumpe und Kurbelwelle hinten werden erneuert. An dem Radialdichtringträger wurden 2 verschiedene Befestigungsschrauben verwendet. Einmal Schrauben der Festigkeitsklasse 8.8 und 10.9. Bei der Montage auf die verschiedenen Anzugsdrehmomente achten.
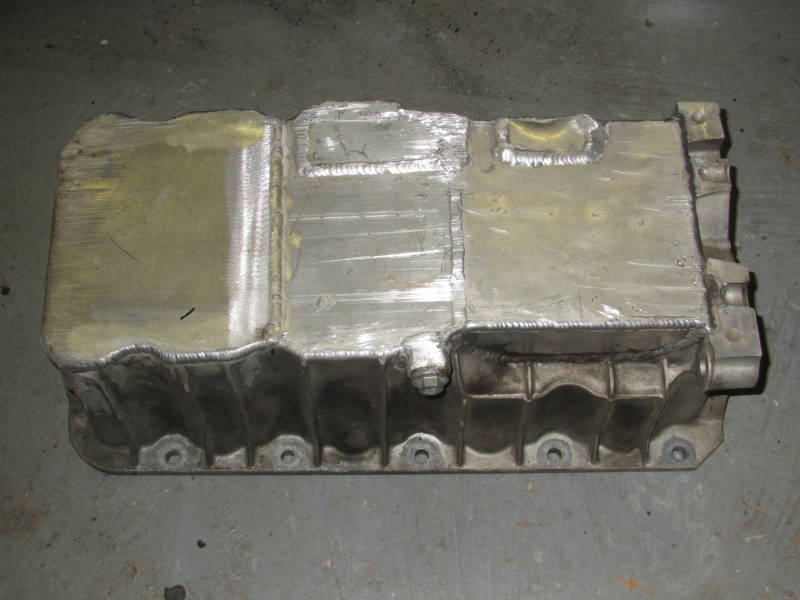
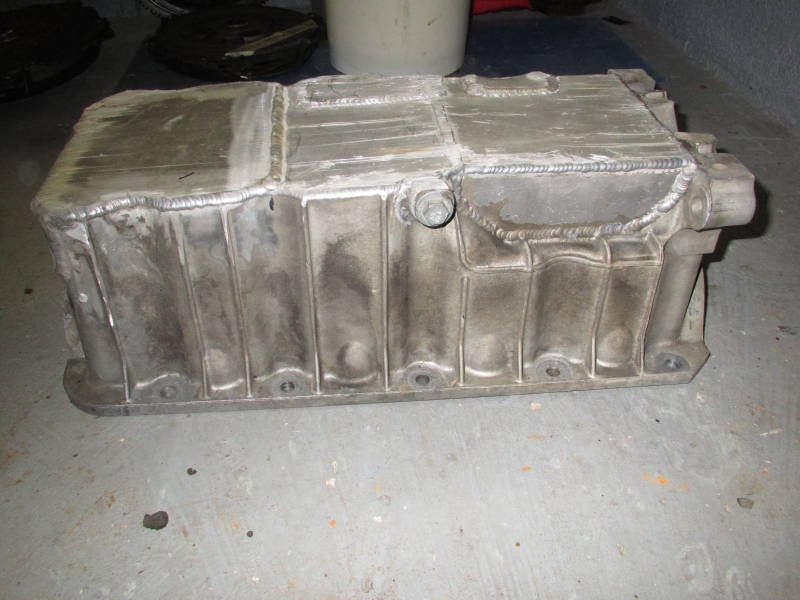
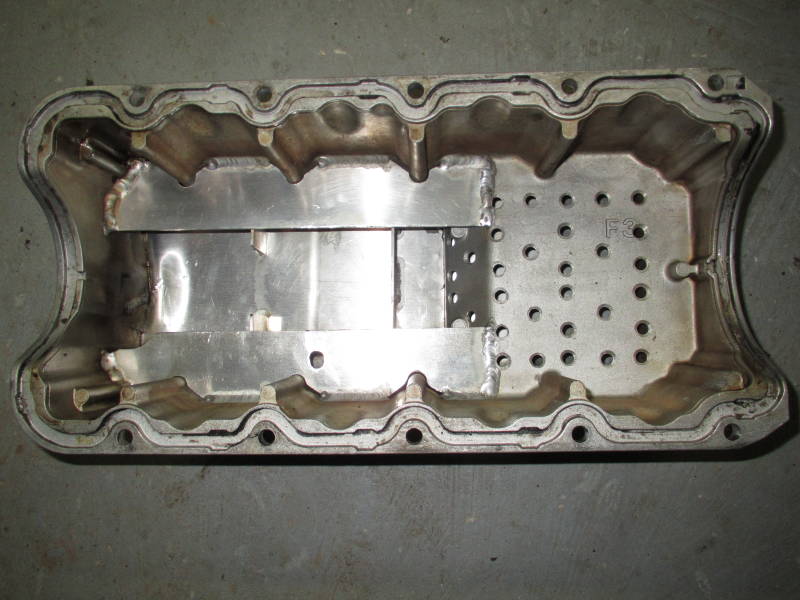
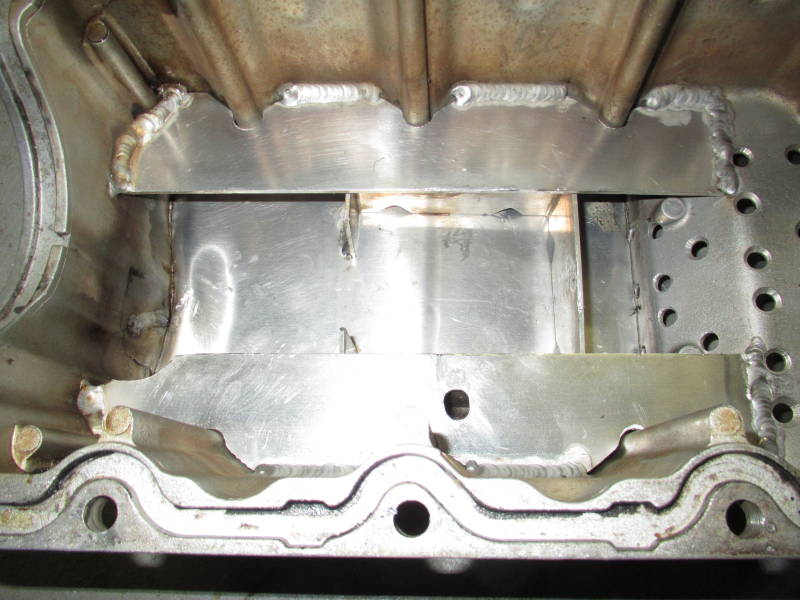
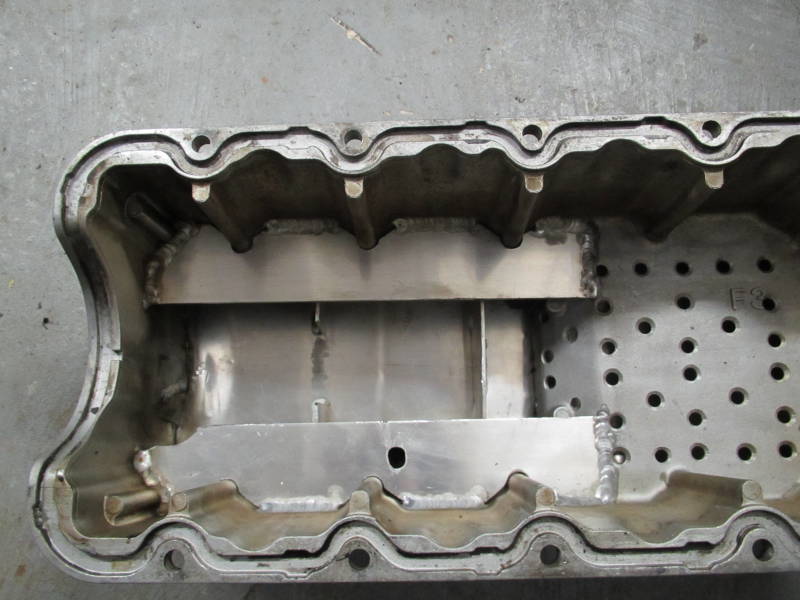
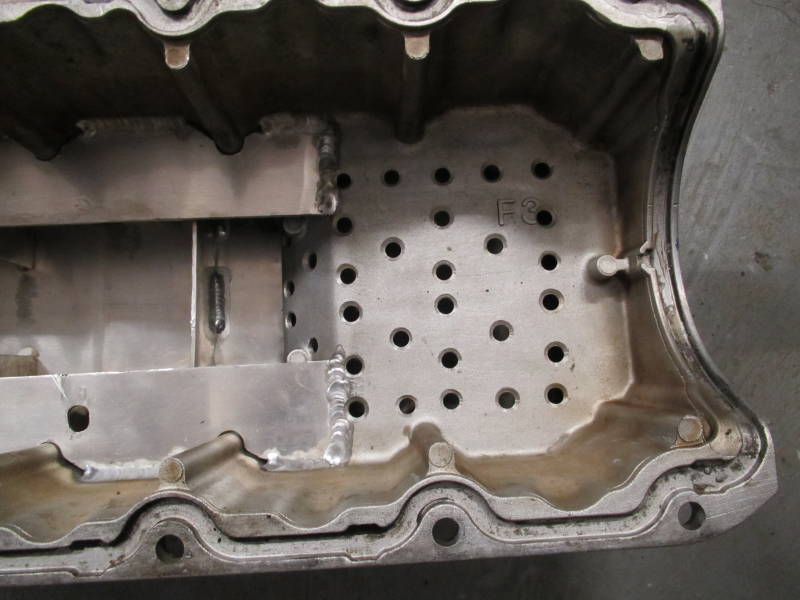
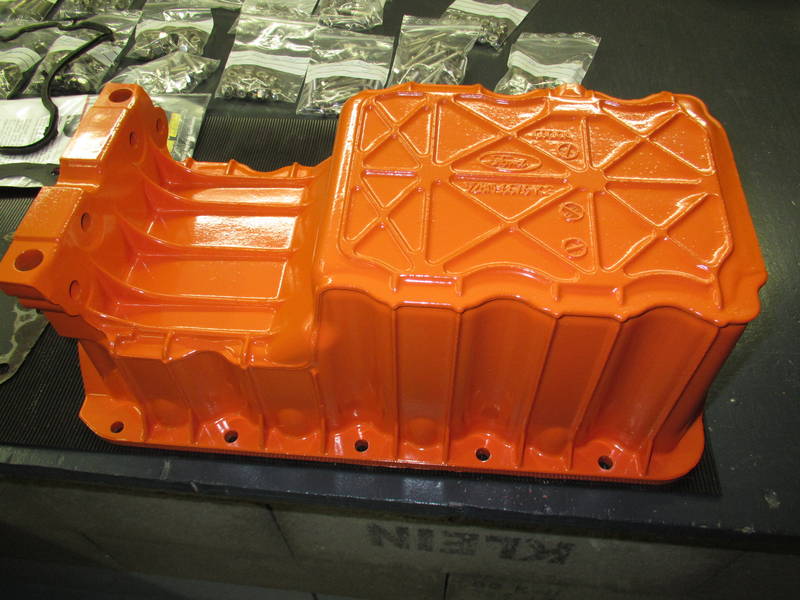
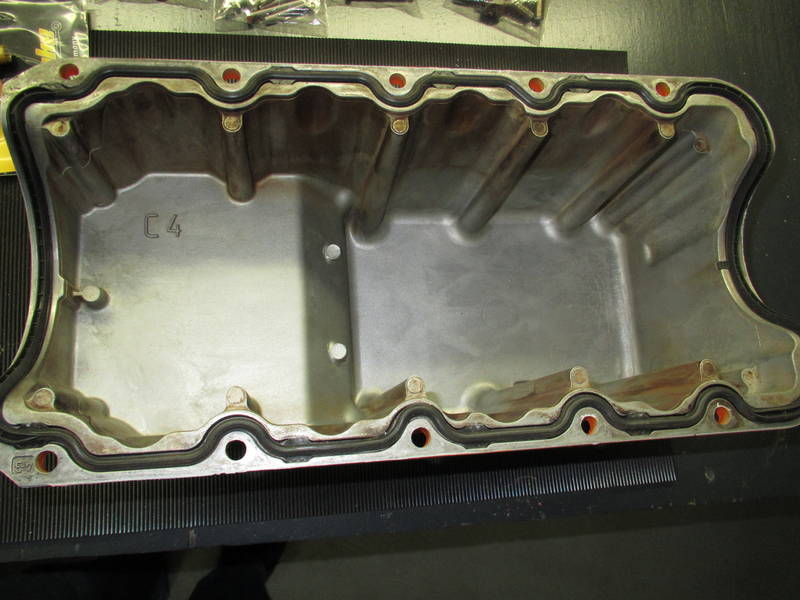
5. DEZEMBER 2015
MONTAGE o. ZUSAMMENBAU DES ZETEC MOTOR 1:
Folgendes Spezialwerkzeug war vorhanden:
- Werkzeug 21-168 Halter zum Blockieren des Schwungrades.
- Einstellwerkzeug 21-162 B Nockenwellen in OT Stellung
- Werkzeug 21-167 Steckschlüssel Zylinderkopfschrauben
- Drehmomentschlüssel 1/2 „
- Steckschlüsselsatz 1/2″ u. 3/8″ u. 1/4″
- Steckschlüssel Torx innen und außen
- Kolbenringspannband
- Kolbenringzange
- Plastigage zum Messen des Kurbellager und Pleuellagerspiels
Zusammenbau Motorblock:
Der Motorblock wurde sehr sorgfältig gereinigt. Ich habe ein Kaltreinigerbad verwendet mit 50 Liter Kaltreiniger. Der Motorblock und alle anderen Teile wurden in diesem Bad komplett gewaschen und anschließend mit einer Verdünnung und Benzin gereinigt. Dichtungsreste wurden sorgfältig entfernt. Alle Dichtungsflächen, wie Auflage am Motorblock für den Zylinderkopf ( nicht Zylinderkopf selbst ), Ölpumpe, Wasserpumpe und alle anderen Auflageflächen wurden sorgfältig mit feinem Sandpapier geschliffen. Anschließend wurde der Motorblock wieder im Kaltreinigerbad gewaschen und mit Pressluft ausgeblasen. Die Ölkanäle, Wasserkanäle wurden ausgeblasen sowie alle Gewindebohrungen. Der gesamte Motorblock muss trocken und sehr sauber sein. Den Motorblock mit der Zylinderkopfseite nach unten auf eine Schutzschicht wie zb. ein Holzbrett legen. Dabei zeigen die 5 Kurbelwellenlageraufnahmen nach oben.
Kurbelwellenlagerspiel ermitteln:
Werden neue Kurbelwellenlagerschalen verwendet ist es wichtig das Laufspiel der Kurbelwellenlager zu ermitteln. Das Laufspiel wird mit Plastigage, einem dünnen Plastikdraht ermittelt. Dazu die 5 neuen Kurbelwellenlager trocken in die Kurbelwellenlageraufnamen des Motorblocks einbauen. Dabei auf die Nasen der Kurbelwellenlager achten. Diese müssen in die Aussparungen der Kurbelwellenlageraufnahme passen. Die Kurbelwelle sorgfältig und behutsam in die neuen Kurbelwellenlager einlegen und ein Stück Plastigage quer auf die trockene und fettfreie Lagerflächen der Kurbelwelle legen. Dabei beginnt man in der Mitte bei Kurbelwellenlager 3. Wie bereits geschrieben Plastigage auf die Lagerfläche der Kurbelwelle quer einlegen und den Hauptlagerdeckel mit einem neuen Kurbelwellenlager einbauen und mit dem vorgeschriebenen Drehmonent von 80 Nm anziehen. Beim Messvorgang darf die Kurbelwelle nicht gedreht werden. Das Laufspiel darf nicht zusammen an allen Kurbelwellenlagern gleichzeitig ermittelt werden sondern muss Lager für Lager ausgemessen werden. Der Pastikdraht wird quer zwischen der Kurbelwellenlauffläche und dem Kurbelwellenlager gelegt. Nach dem Anziehen mit dem vorgeschriebenen Drehmonent von 80 Nm wird der Plastikdraht zusammengedrückt. Nach dem Anziehen die Schrauben des Hauptlagerdeckels wieder lösen und den Hauptlagerdeckel wieder entfernen. Der plattgedrückte Plastikdraht haftet entweder an dem Kurbelwellenlager oder auf der Lagerfläche der Kurbelwelle. Der plattgedrückte Plastikdraht hat eine gewisse Breite. Mit dem Platigage wird auch eine Lehre mitgeliefert. Anhand der Breite des plattgedrückten Drahtes lässt sich mit Hilfe der Lehre das Lagerspiel leicht ermitteln. Dazu den plattgedrückten Plastigagefaden mit der Plastigage Skala an der Lehre vergleichen. Ist das Laufspiel grösser als der vorgeschriebene Wert müssen andere Kurbelwellenlager verwendet werden.
Das Hauptlagerspiel sollte zwischen 0,020 und 0,042 mm betragen.
Erhältlich für die Zetec – Motoren sind folgende abgestufte Kurbelwellenlager:
- Stufe A grün 2,152 mm – 2,145 mm
- Stufe B braun 2,147 mm – 2,140 mm
- Stufe C gelb 2,142 mm – 2,135 mm
- Stufe D blau 2,137 mm – 2,130 mm
Bilder folgen:
Zusammenbau des Motorblocks und der Kurbelwelle:
Nach der Ermittlung des Laufspiels mit Plastigage sind die Kurbelwellenlager im Motorblock bereits eingebaut. Wenn diese nicht eingebaut sind, bitte in dieser Reihenfolge vorgehen:
Die
Lagerflächen trocken reiben und 5 neue Lager trocken einbauen. Die 5
Kurbelwellenlager von Hand sorgfältig in die Lageraufnahme des
Motorblocks einlegen. Das Kurbelwellenlager 3 ( Mitte ) ist ein
geflanschtes Kurbelwellenlager für die Aufnahme des Axialspiels der
Kurbelwelle. Dabei aufpassen dass alle Nasen der Kurbelwellenlager in
den Aussparungen der Kurbelwellenlageraufnahme im Motorblock sitzen.
Sind alle 5 Kurbelwellenlager eingebaut, diese gut einölen und
Kurbelwelle vorsichtig in die Kurbelwellenlager einlegen. Dann
die Kurbelwellenlager der Hauptlagerdeckel trocken in diese einlegen.
Wieder auf die Nasen der Kurbelwellenlager achten. Die Kurbelwellenlager
gut einölen und die Hauptlagerdeckel in der richtigen Position
einbauen. Die Hauptlagerdeckel sind von 1 – 5 beschriftet. Der Einbau
beginnt mit dem Hauptlagerdeckel 1 an der Zahnriemenseite und endet mit
Hauptlagerdeckel 5 an der Schwungradseite. Hauptlagerdeckel 2 + 4 haben
andere Schrauben und zwar Stiftschrauben zur Aufnahme des
Ölleitbleches. Der Pfeil auf den Hauptlagerdeckel zeigt immer in
Richtung des Zahnriemens. Die Schrauben der Hauptlagerdeckel mit
der Hand anziehen. Dann mit dem Drehmomentschlüssel und einer 15 er Nuss
die Hauptlagerdeckelschrauben von der Mitte aus , beginnend bei
Hauptlagerdeckel 3 nach links zu 2 +1 und nach rechts zu 4 +5 in 3
Stufen auf das vorgeschriebene Drehmoment von 80 Nm anziehen. Ich habe
mit einem Drehmoment von 30 Nm begonnen, dann in der 2.Stufe ein
Drehmoment von 55 Nm gewählt und abschließend in der 3. Stufe mit einem
Drehmoment von 80 Nm abgeschlossen.
Erklärungen zu den Fotos unten:
Auf den Fotos erkennt man den RDB Motorblock ( 105 PS ) ohne Kolbenbodenkühlung. Dieser wurde im Kaltreinigerbad komplett gereinigt und alle Dichtungsreste wurden sorgfältig entfernt. Alle Kurbelwellenlager sind entfernt. Bei diesem Motor habe ich beschlossen die alten Kurbelwellenlager weiter zu verwenden. Diese sahen noch sehr gut aus und aus dem Grund konnte ich diese weiter verwenden.
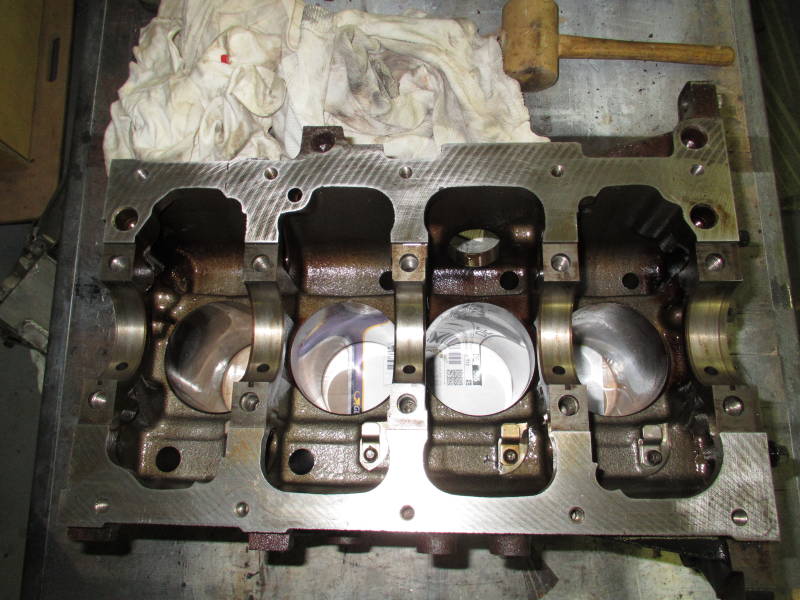
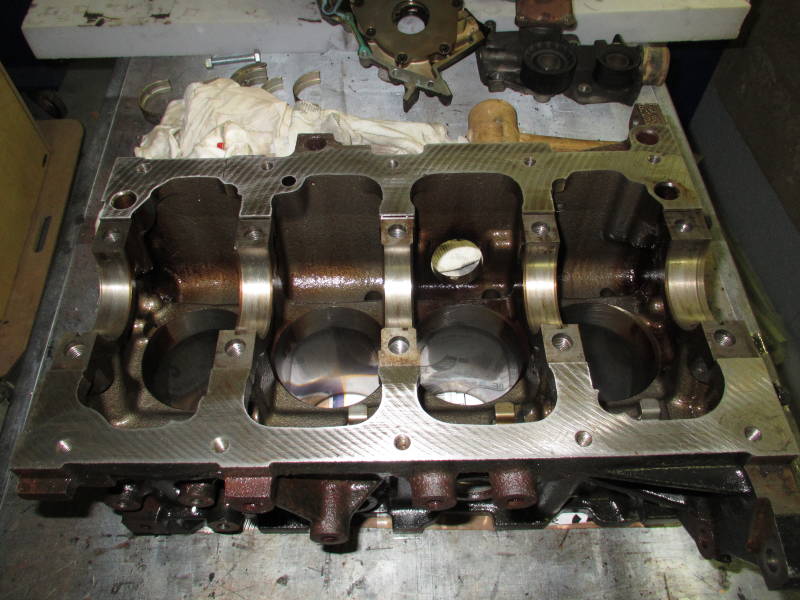
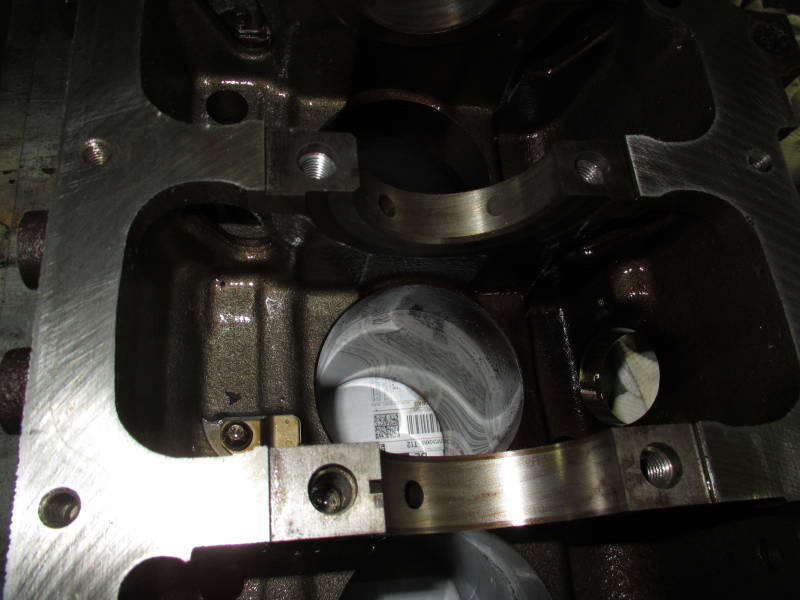
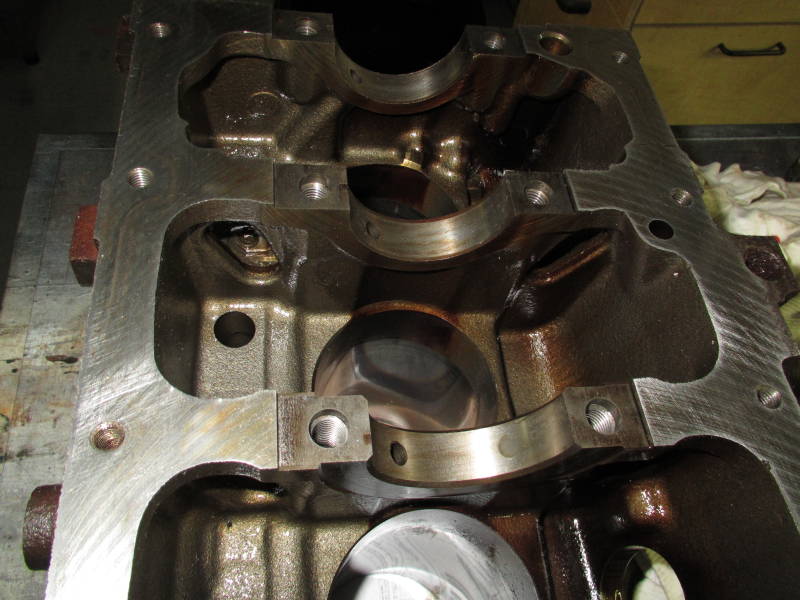
Die Kurbelwellenlager sind trocken in die Kurbelwellenlageraufnahmen eingelegt worden. Deutlich sieht man das geflanschte Kurbelwellenlager 3 welches das Axialspiel aufnimmt. Auf dem rechten Bild ist die Kurbelwelle bereits in die eingeölten Kurbelwellenlager eingelegt worden.
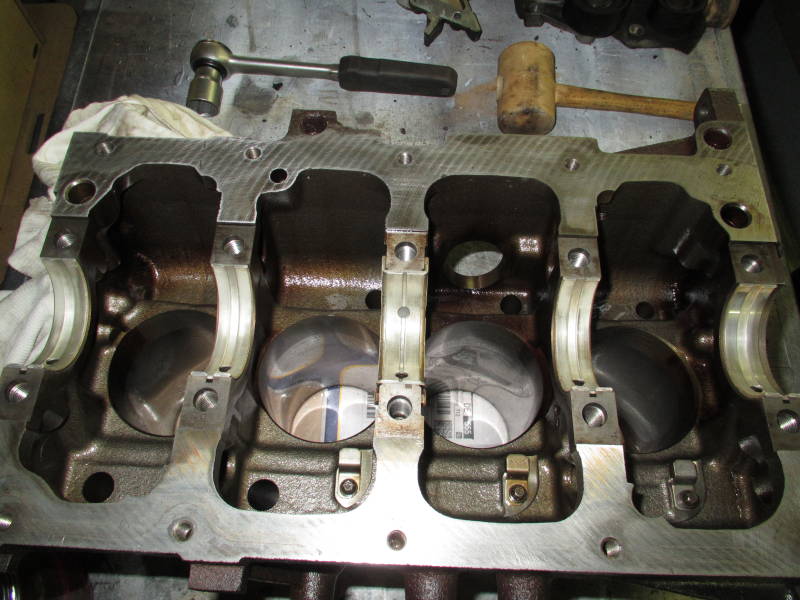
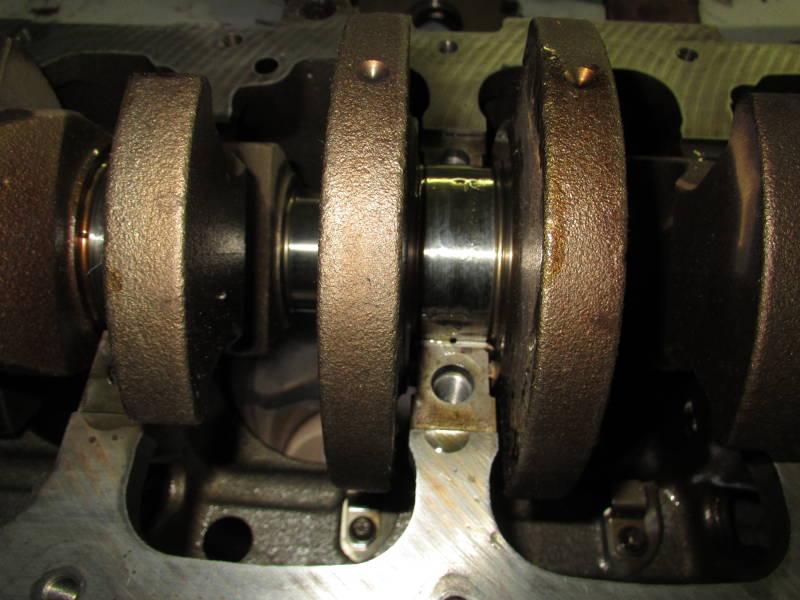
Auf dem Foto rechts erkennt man einen Hauptlagerdeckel mit dem Kurbelwellenlager das bereits eingeölt worden ist. Die Hauptlagerdeckel mit den Kurbelwellenlager sind alle montiert und werden mit einem vorgeschriebenen Drehmoment von 80 Nm mit einem Drehmomentschlüssel in 3 Stufen angezogen. Bei diesem Zusammenbau handelt es sich um meinen Zetec – Motor 1 , wie bereits geschrieben ein RDB Motor ohne Kolbenbodenkühlung. Dieser Motor wird später mit anderen Nockenwellen, grösserer Drosselklappe und anderem Mapping +/- 130 PS haben.
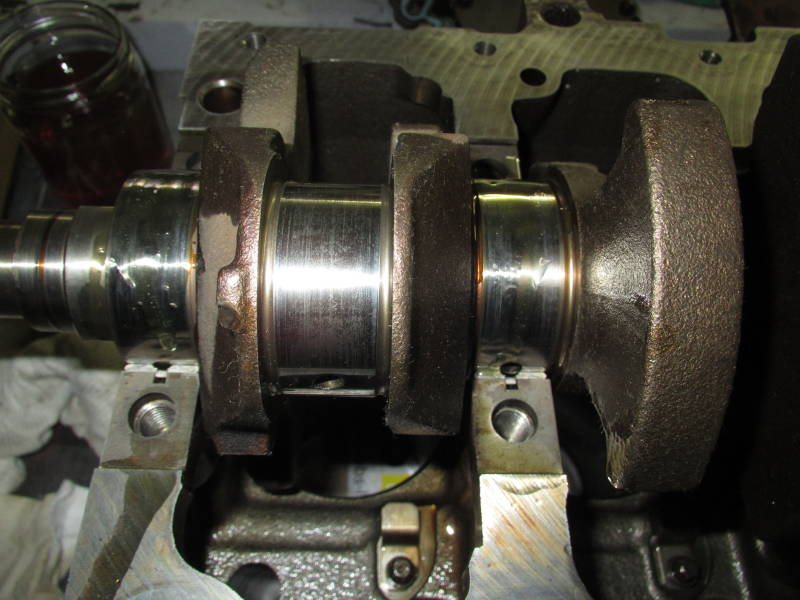
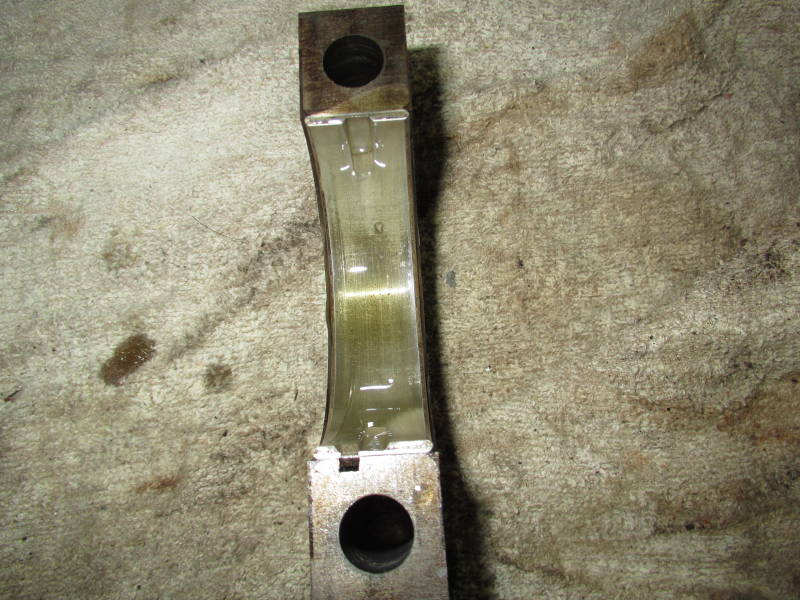
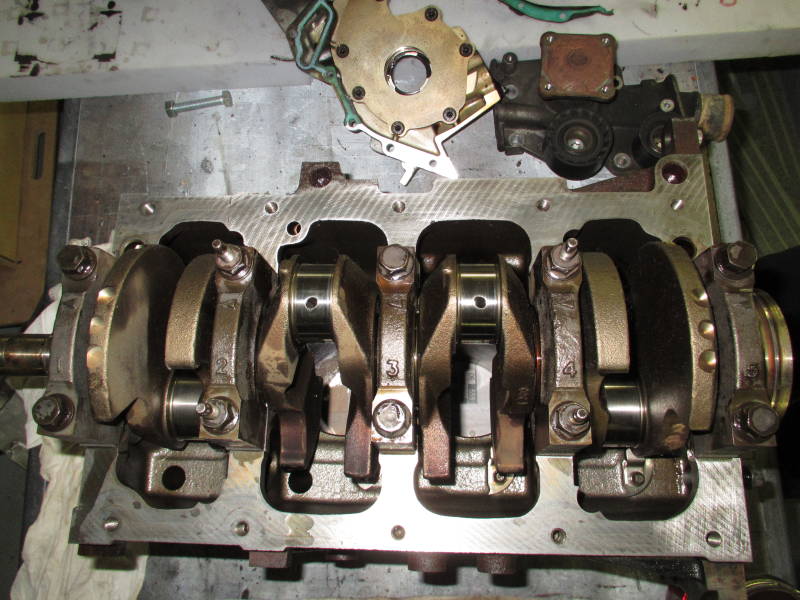
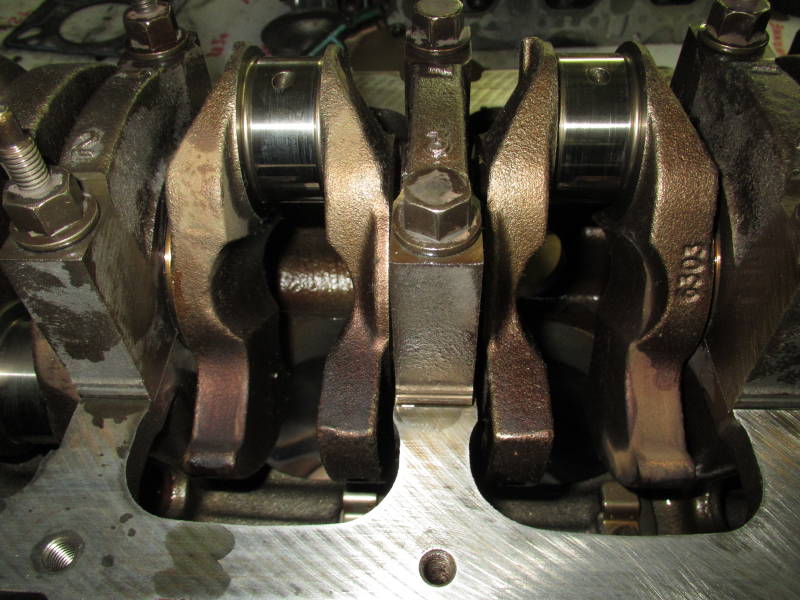
Zusammenbau
des Zetec – Motor 2 ein RQB Motor mit 130 PS in der Serie und mit
Kolbenbodenkühlung. Auf den Fotos ist der ungereinigte Motorblock zu
erkennen. Dieser Motor habe ich weiter unten komplett demontiert. Der
nächste Arbeitsschritt wird das Reinigen im Kaltreinigerbad sein.
Anschliessend werden alle Dichtungsreste entfernt und der gesamte
Motorblock mit Pressluft ausgeblasen. Dieser Motor wird neue
Kurbelwellenlager bekommen, die Kurbelwelle wird gewuchtet.
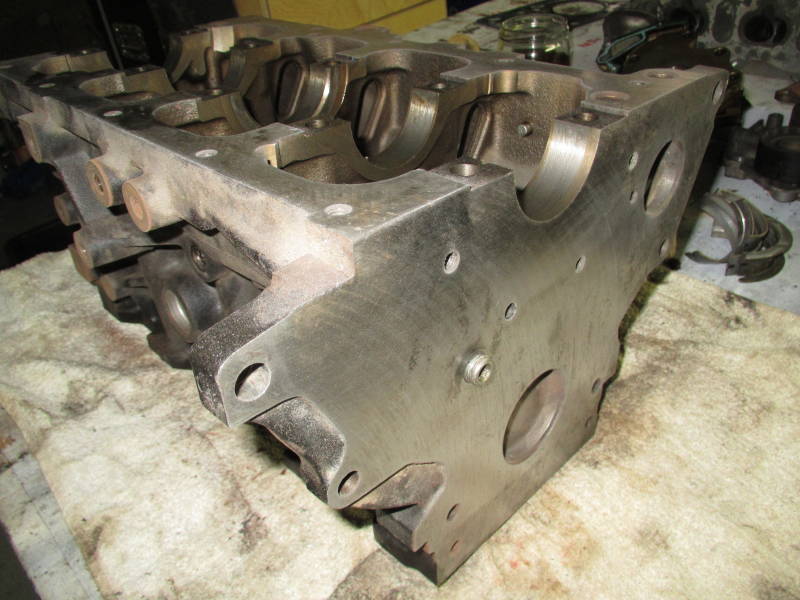
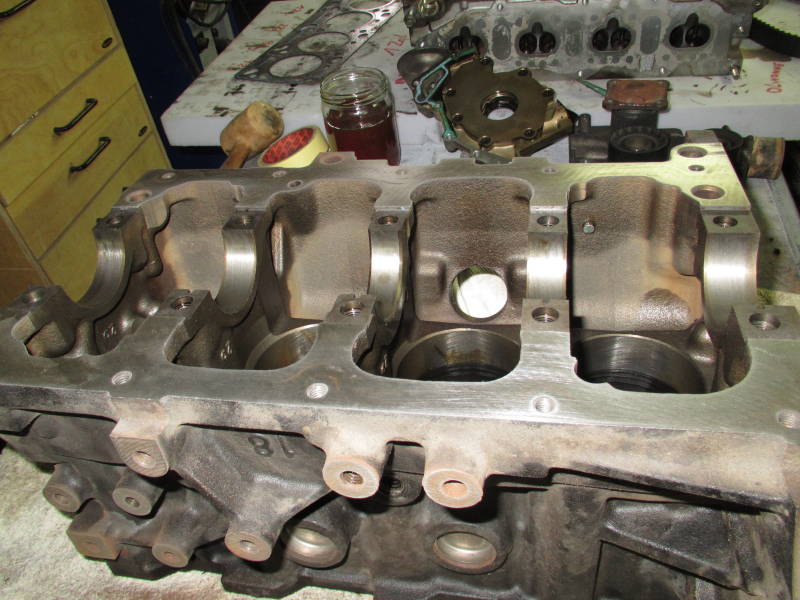
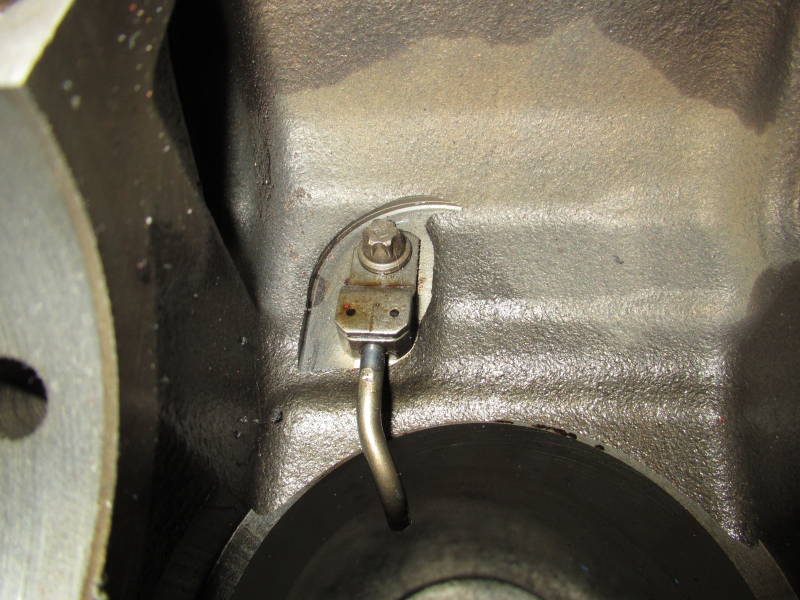
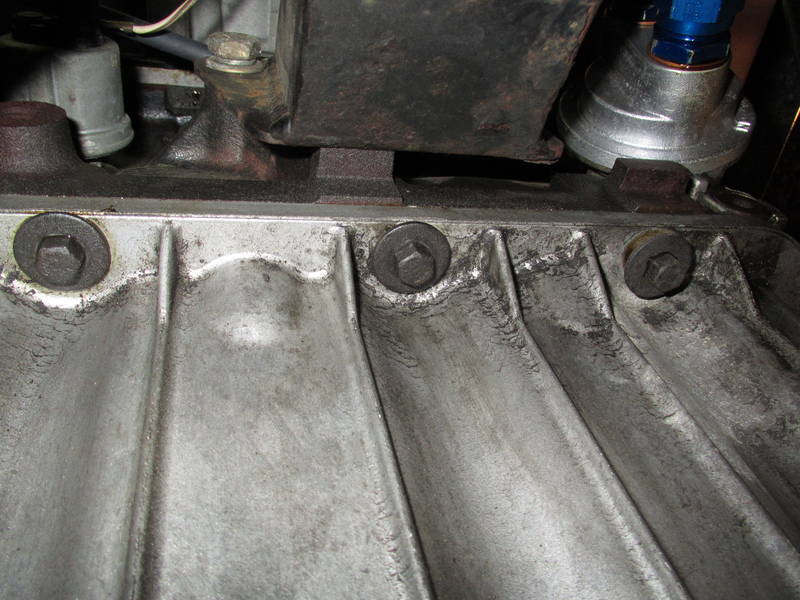
Auf diesen Bildern ist die Öleinspritzdüse der Kolbenbodenkühlung zu erkennen. Der Motorblock ist komplett gereinigt und alle Dichtungsreste sind bereits entfernt. Ich werde den Motorblock mit einem Thermolack neu lackieren.
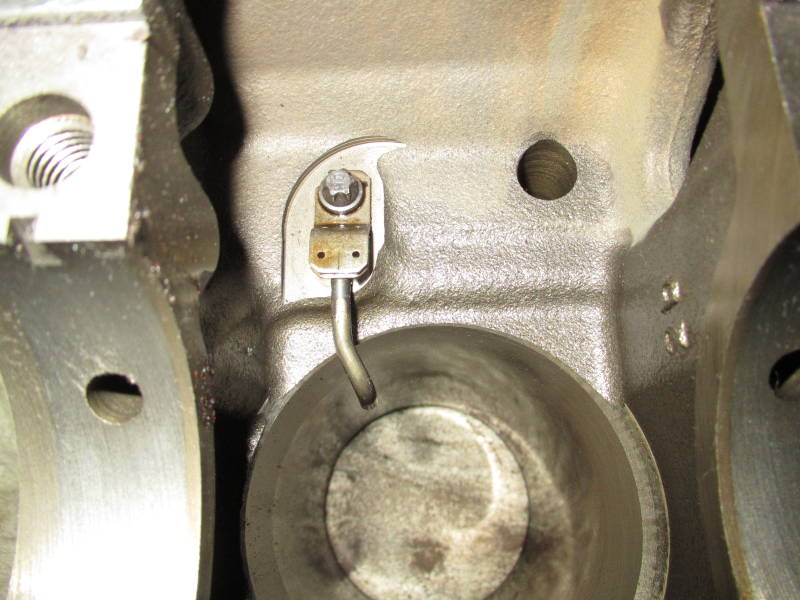
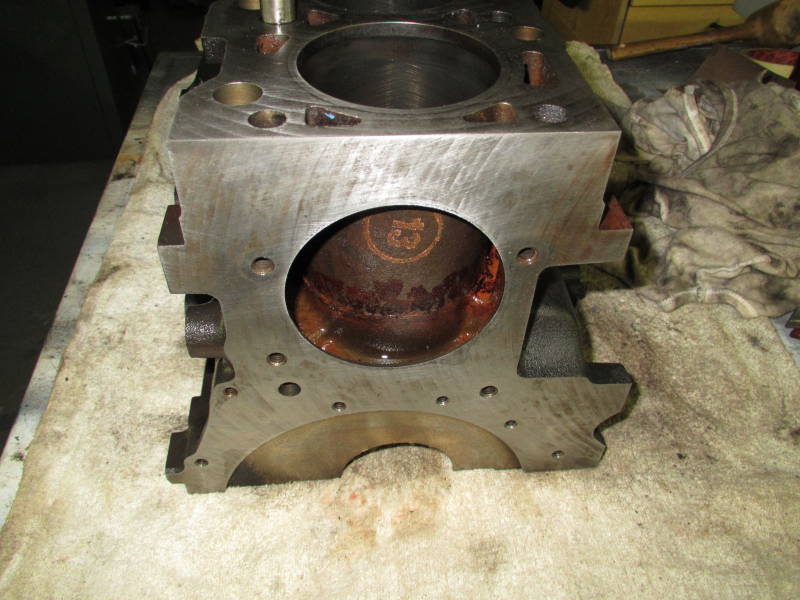
Auf diesen beiden Fotos erkennt man den gereinigten Motorblock.
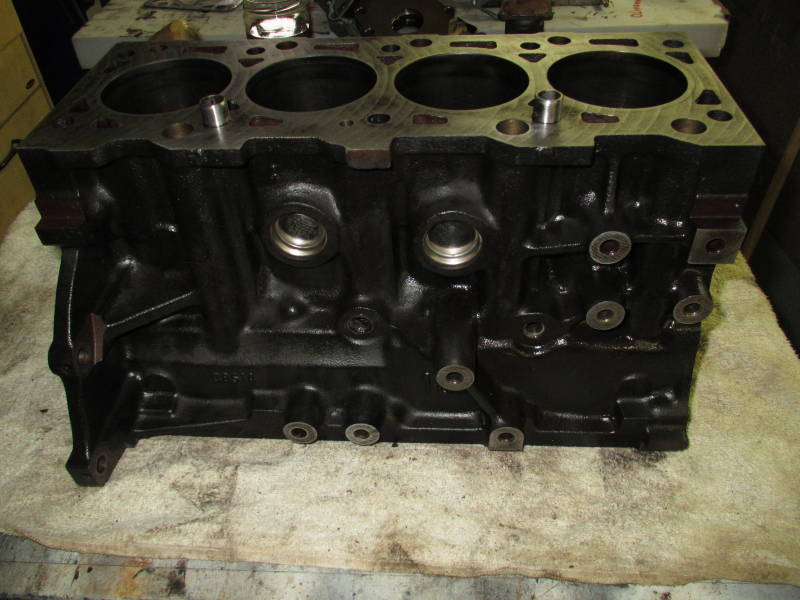
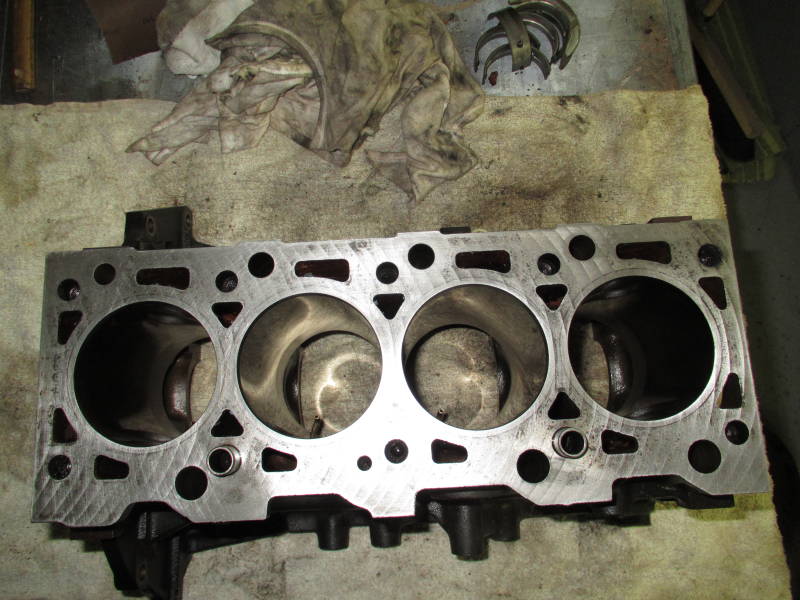
4. DEZEMBER 2015
Habe heute meine Nockenwelle gemessen. Höhe der Nocken: 45,3mm. Grundkreis:36,1mm
30. NOVEMBER 2015
DEMONTAGE DES 2. Zetec Motor
Folgendes Spezialwerkzeug war vorhanden:
- Werkzeug 21-168 Halter zum Blockieren des Schwungrades.
- Einstellwerkzeug 21-162 B Nockenwellen in OT Stellung
- Werkzeug 21-167 Steckschlüssel Zylinderkopfschrauben
- Steckschlüsselsatz 1/2″ u. 3/8″ u. 1/4 „
- Steckschlüssel Torx außen und innen
Am
Samstag den 28.11.2015 habe ich den 2. Zetec – Motor bei GS in Essen
abgeholt. Ich werde diesen komplett zerlegen da dieser Zetec-Motor einen
kleinen Lagerschaden aufweist. Auf den Fotos erkennt man den 2. Zetec –
Motor in meiner kleinen Werkstatt. Das Motoröl ist abgelassen und das
Zerlegen kann beginnen.
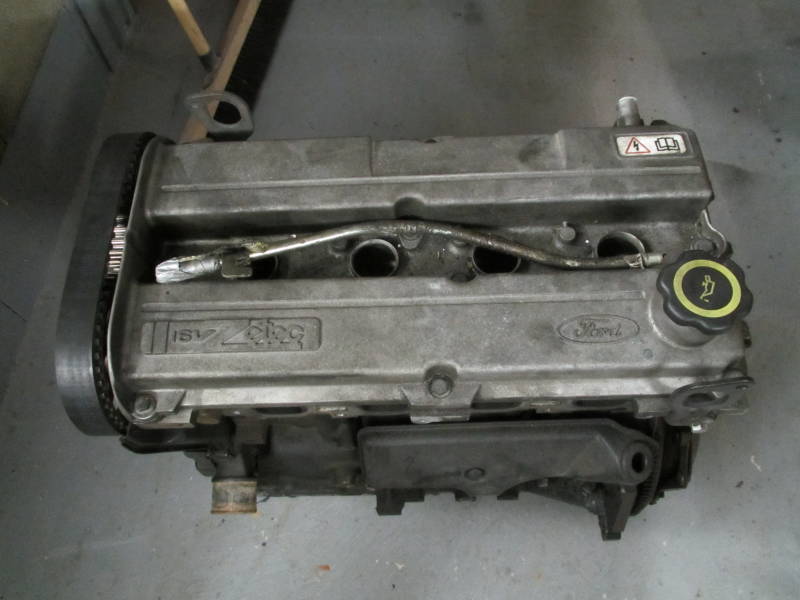
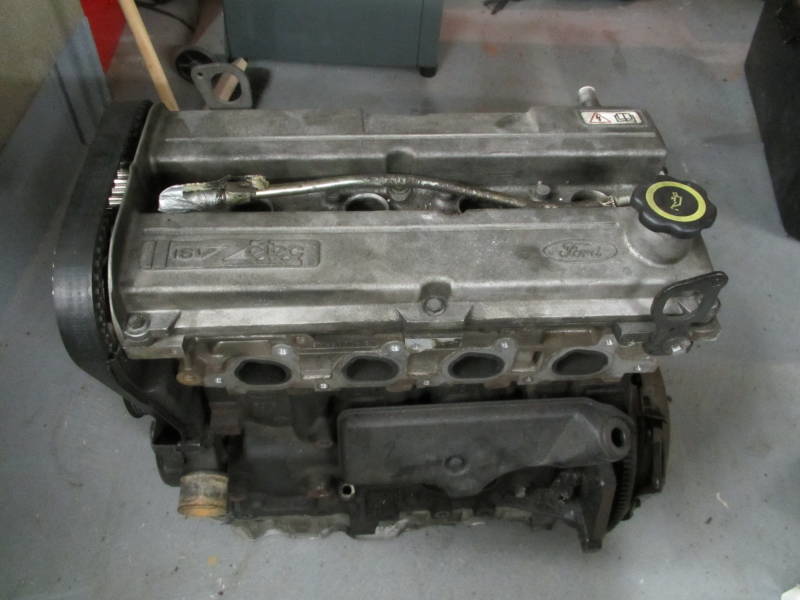
Der Ventildeckel ist abgebaut und man erkennt die Nockenwellen. Der Motor sieht innen sehr sauber aus. Die eingebauten Nockenwellen sehen anders aus als die original Nockenwellen.

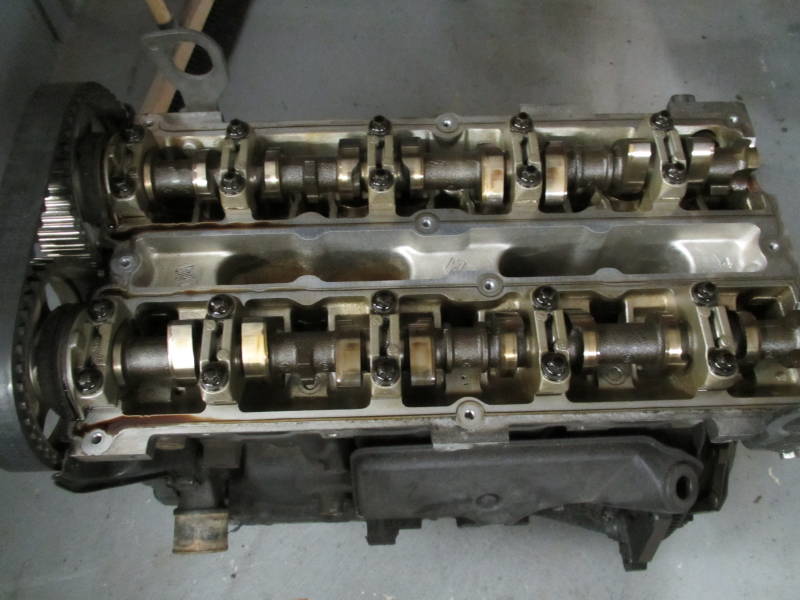
Die Auslassnockenwelle ist bereits ausgebaut und auf dem Foto rechts sind beide ausgebauten Nockenwellen zu sehen. Ich habe beide NW mit Tesaband beschriftet damit diese nicht verwechselt werden können.
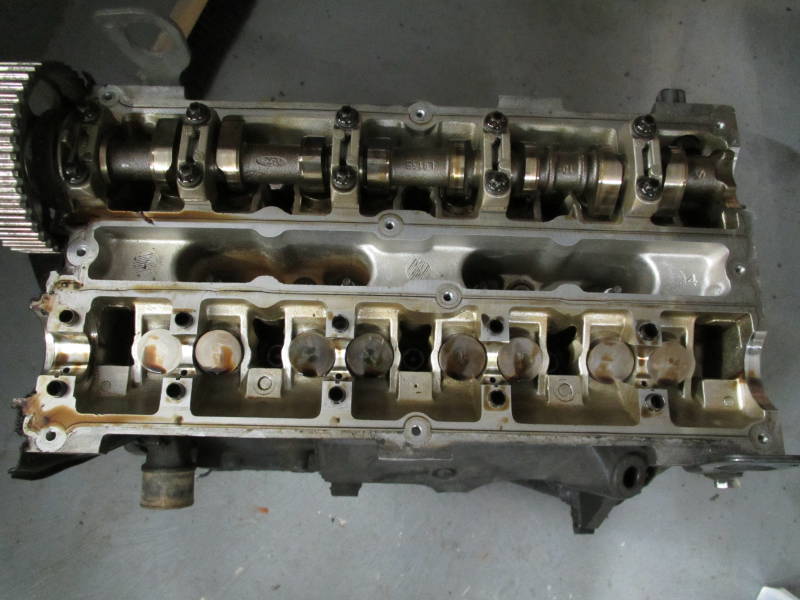
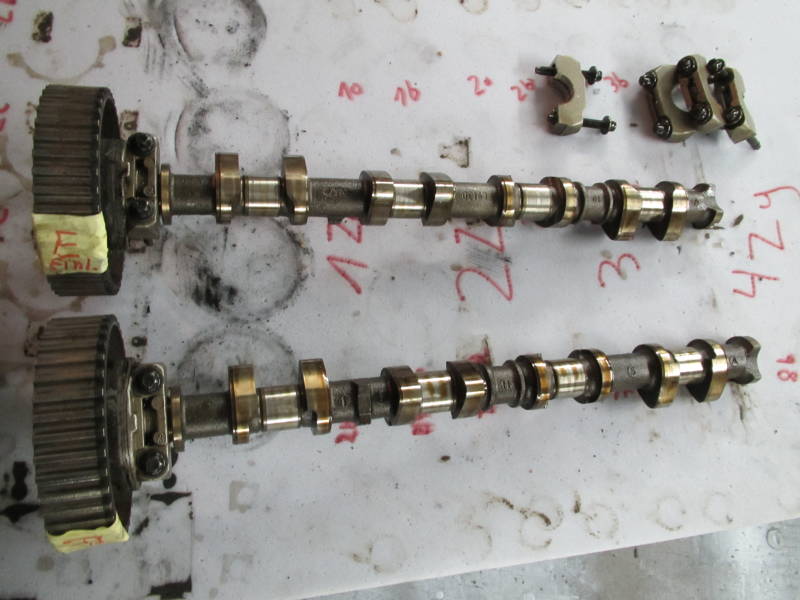
Ich würde gerne wissen welche Nockenwellen das sind. Leider kann ich keine Gradzahl ablesen, aber vielleicht kann Günter mir etwas zu den eingebauten Nockenwellen sagen.
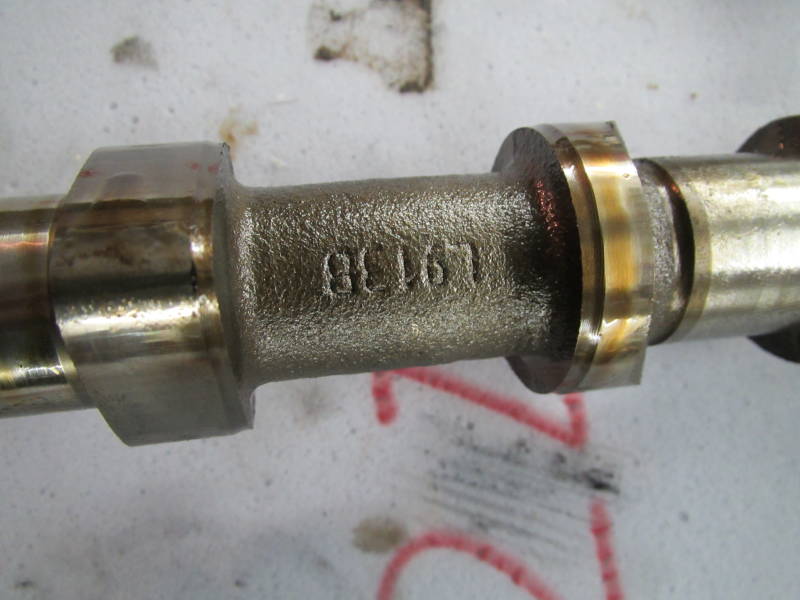
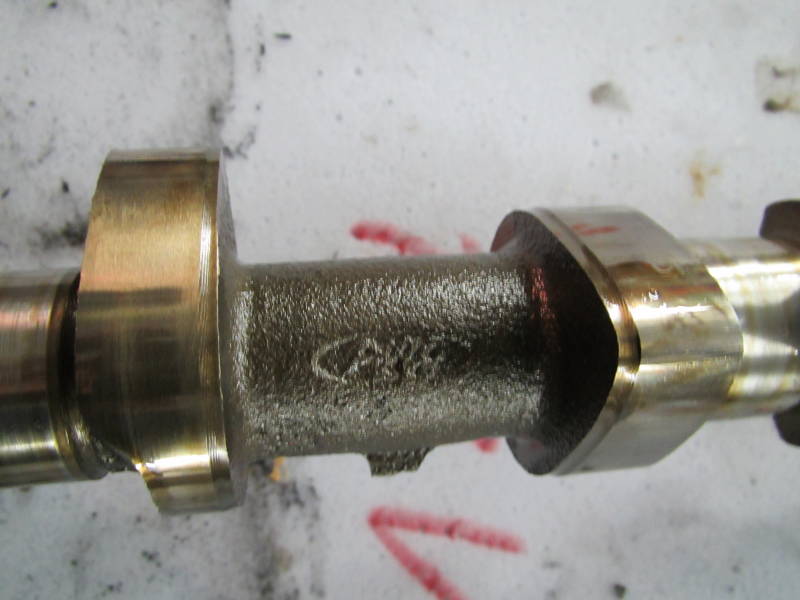
Die beiden Nockenwellen sind komplett ausgebaut und wurden sorgfältig gereinigt und eingepackt. Diese Fotos dienen mir später als Gedächnissstütze beim Zusammenbau des Motors.
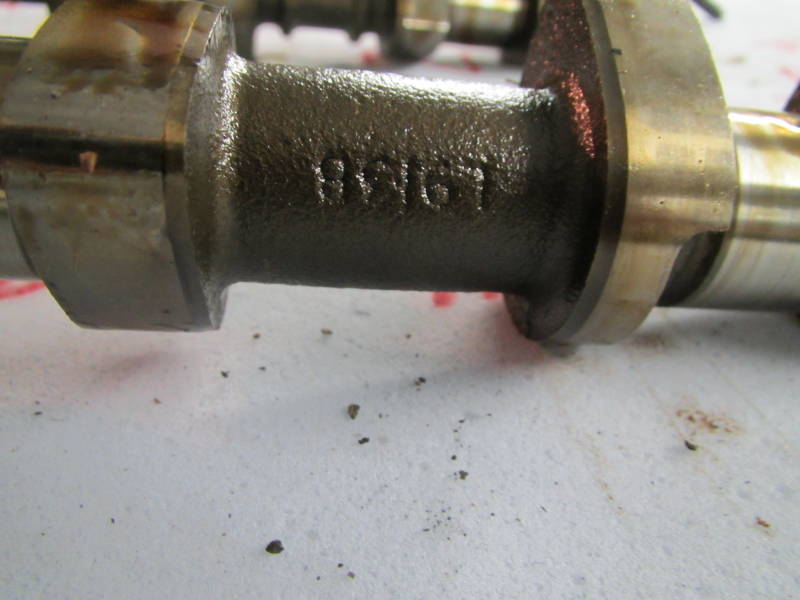
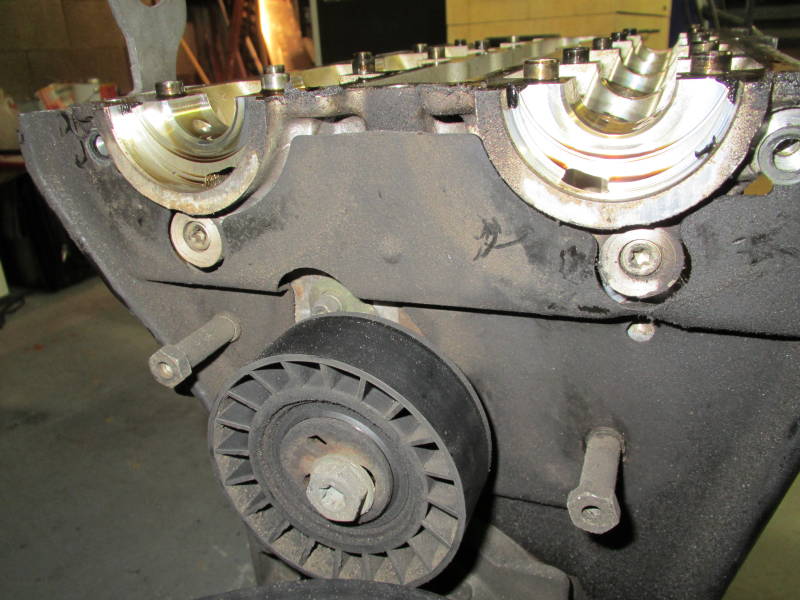
Der
Zylinderkopf ist komplett ausgebaut. Auf dem rechten Foto erkennt man
die Zylinderkopfdichtung. Diese sieht recht neu aus so dass ich annehme
dass diese noch nicht lange eingebaut war.
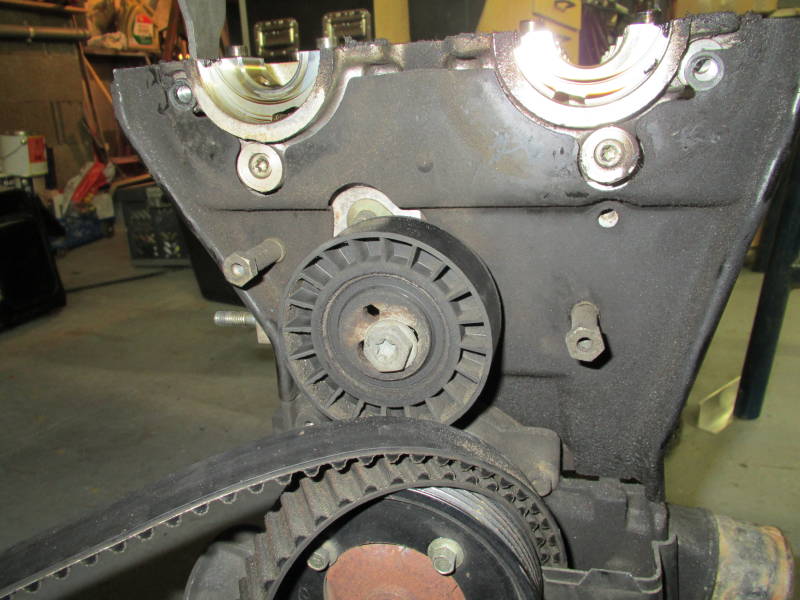
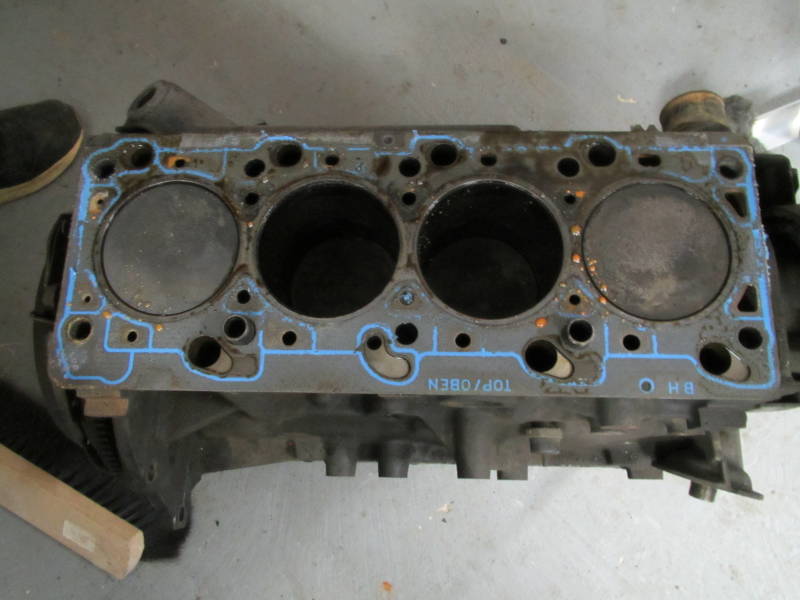
Der Motorblock mit ausgebautem Zylinderkopf. Alles sieht sehr sauber aus. Nun wird die modifizierte Ölwanne ausgbaut damit ich die Kurbelwellenlager ausbauen kann.
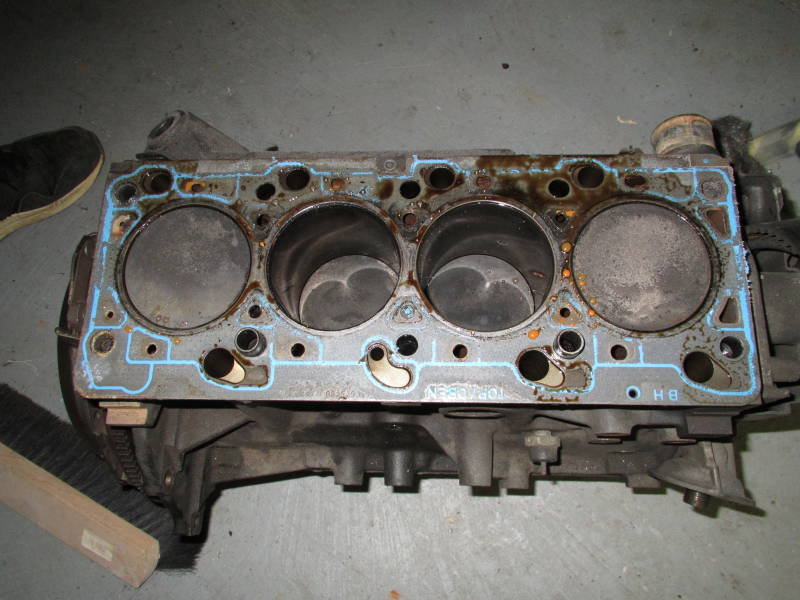
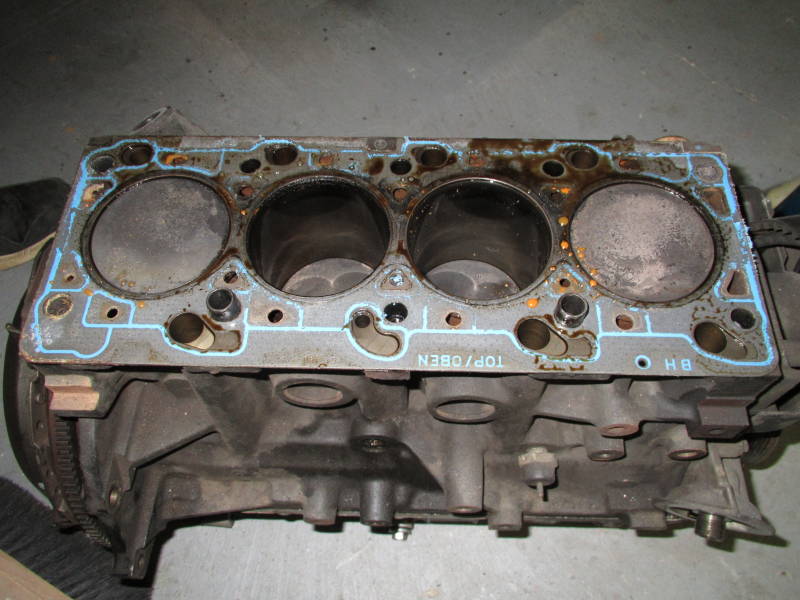
Die komplette Ölwanne ist ausgebaut und liegt in der Wanne mit Kaltreiniger. Nun wird das Schwungrad mit einem Spezialwerkzeug gehalten und abgebaut.
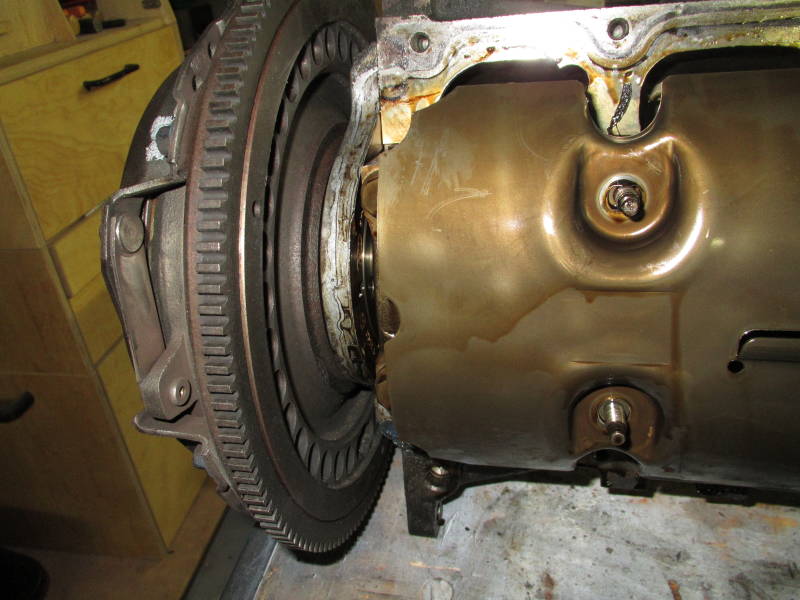
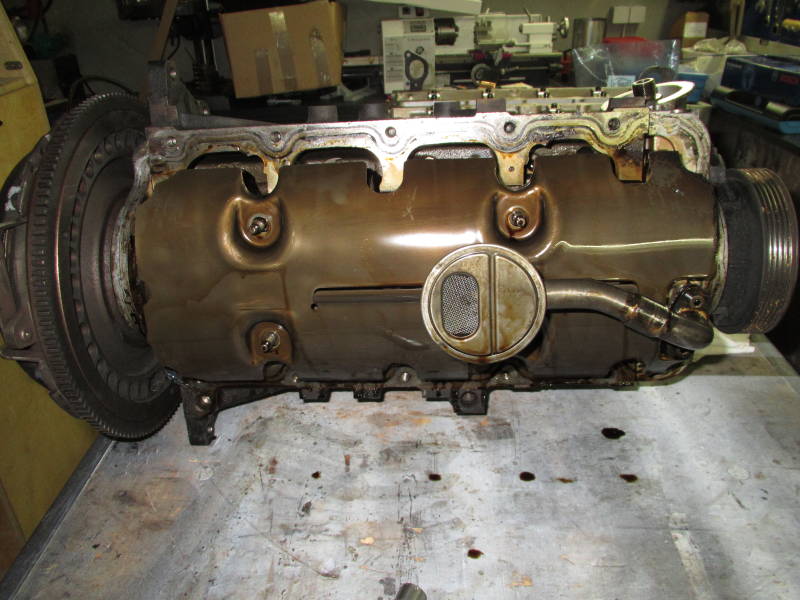
Die Ölpumpe wird ausgebaut und sorgfältig gereinigt. Auf den Fotos erkennt man die Kurbelwellenlagerschalen und einen Teil der Öleinspritzdüsen der Kolbenbodenkühlung.
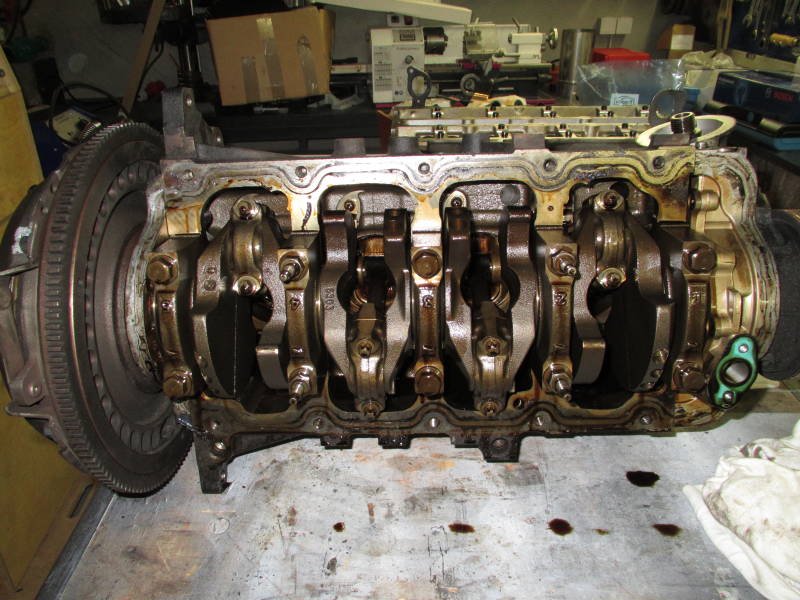
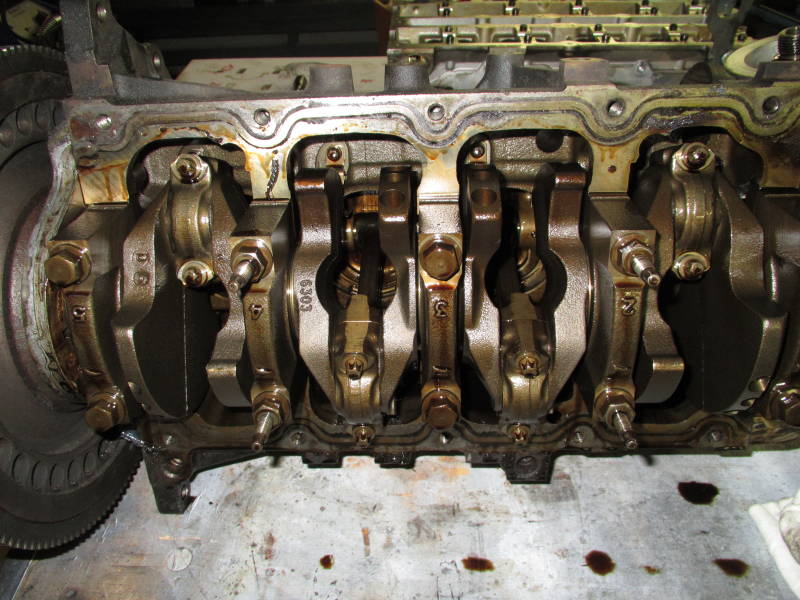
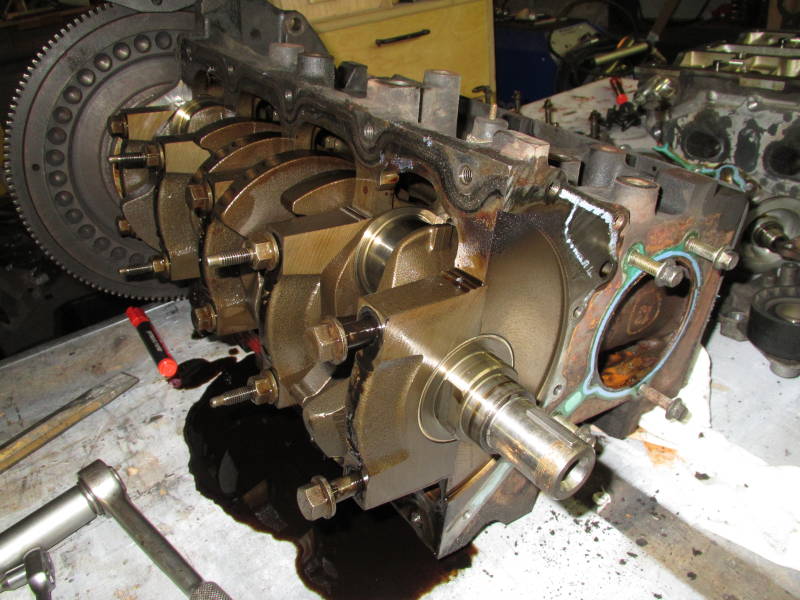
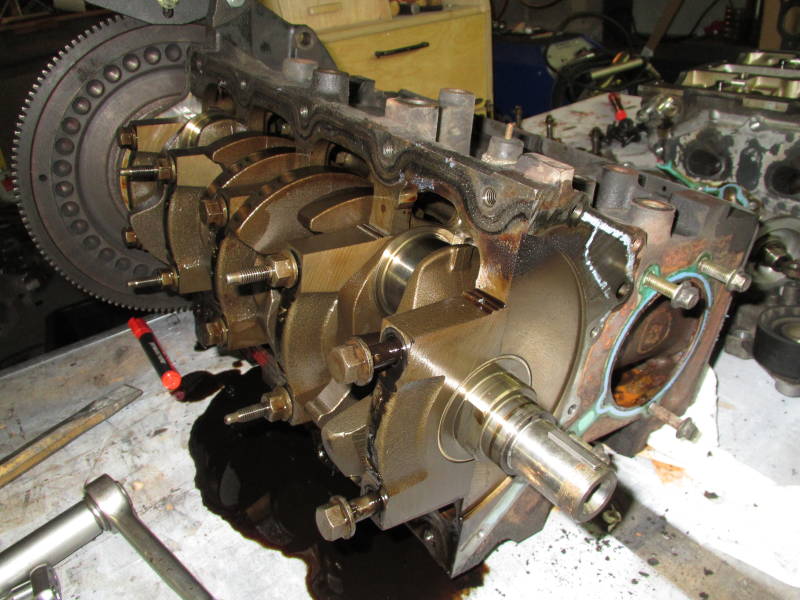
Die
ausgebauten Kurbelwellenlager sind auf diesen Fotos zu sehen. Der
Lagerschaden erweist sich als ein sehr minimaler Schaden. Ich werde die
Kurbelwellenlager komplett ersetzen. Die Kurbelwelle hat keinen
erkennbaren Schaden und kann so wieder eingebaut werden.
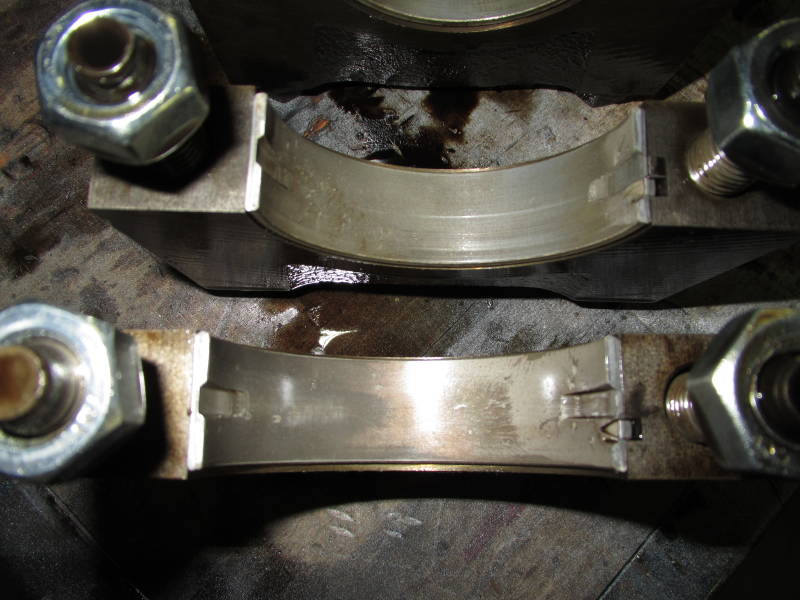
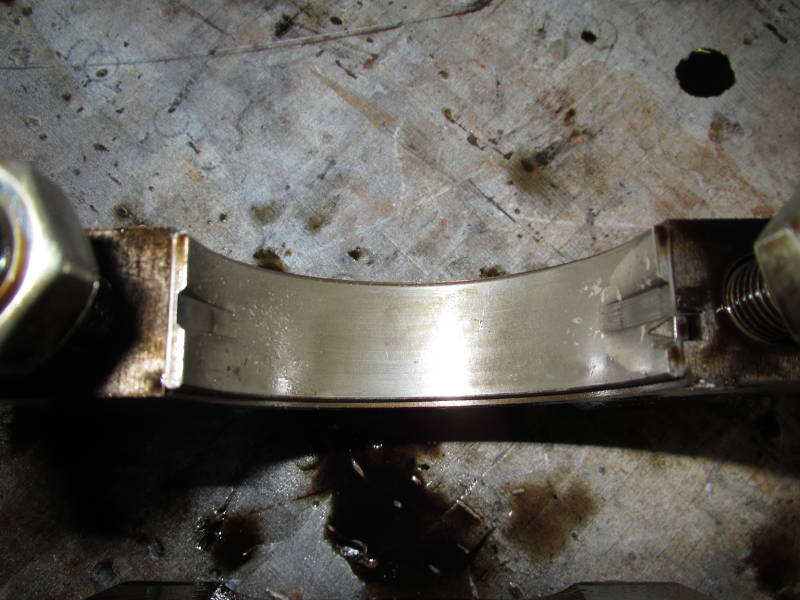
Auf den Fotos oben und unten li und re sind die Kurbelwellenlager zu sehen. Auf verschiedenen Lagern erkennt man die Lager mit dem leichten Kurbelwellenlagerschaden.
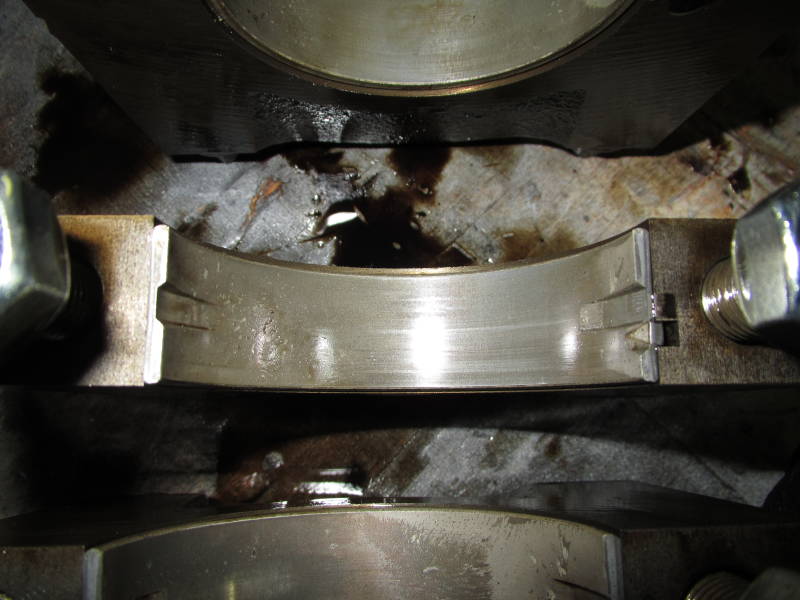
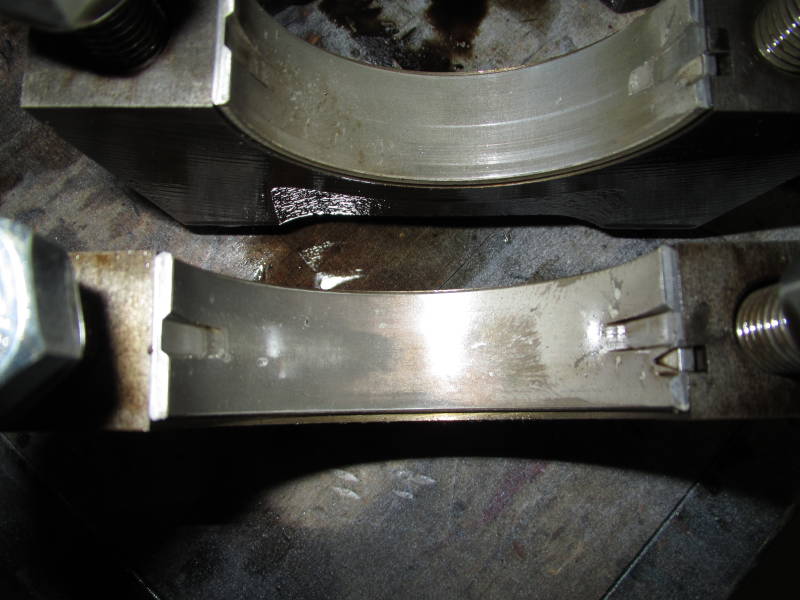
Die Kolben sind komplett ausgebaut und gekennzeichnet. Ich werde diese reinigen und neue Kolbenringe mit einem neuen Ölabstreifring montieren. Wenn diese schon ausgebaut sind, ist jetzt der richtige Zeitpunkt gekommen die Kolbenringe, Pleuellager und Kurbelwellenlager zu wechseln. Desweiteren werden alle Pleuelschrauben, Zylinderkopfschrauben gegen neue getauscht.
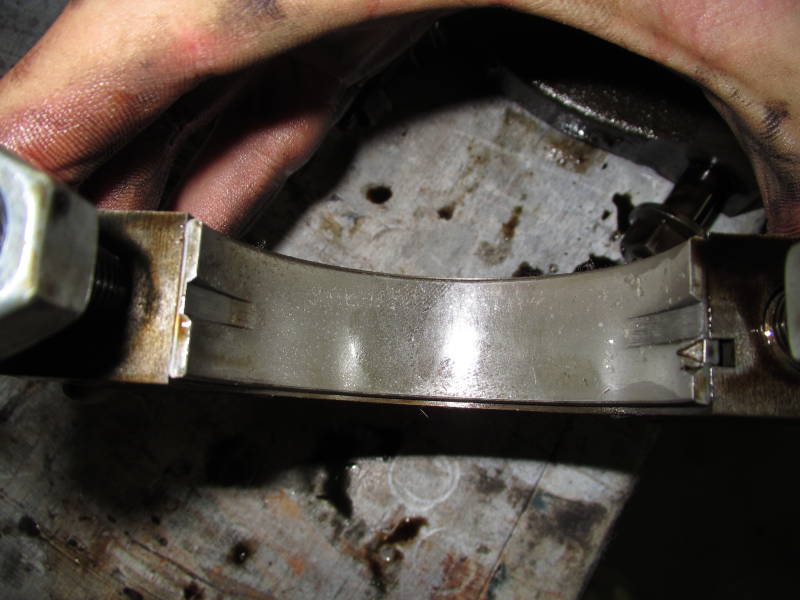
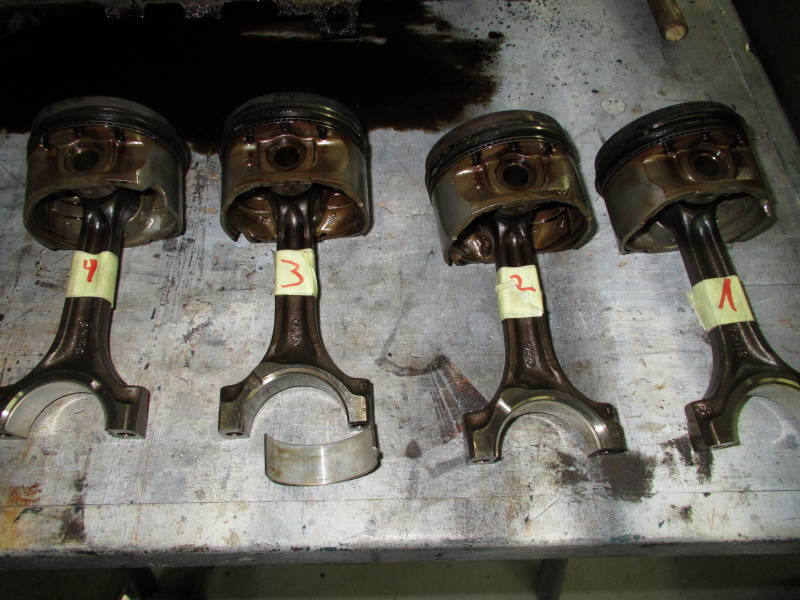
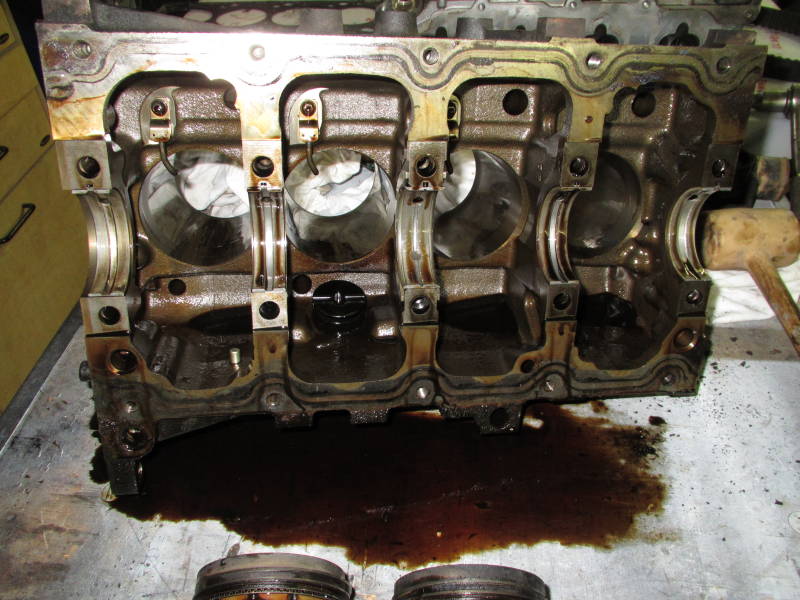
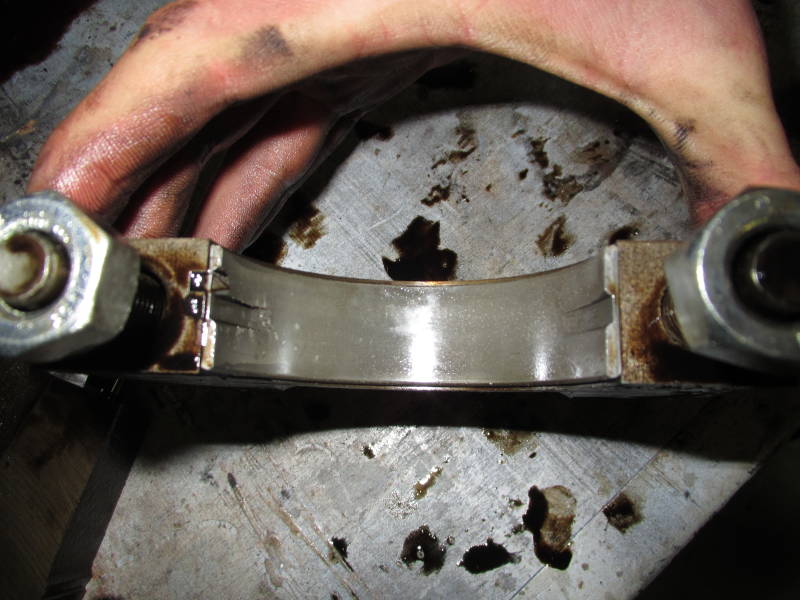
29. NOVEMBER 2015
DEMONTAGE des 1. Zetec Motor
Auf diesen Bildern erkennt man einen sehr sauberen Zetec Zylinderkopf. Die Zylinderkopfabdeckung ist schon abgebaut und man sieht die beiden Nockenwellen. Um ein Verbiegen der Nockenwellen beim Ausbau zu verhindern sollte man die Nockenwellenschalen in einer festgesetzten Reihenfolge lösen. Siehe Foto rechts. Die Schrauben der Nockenwellenschalen sollten zuerst eine halbe Umdrehung gelöst warden bis diese mit der Hand herausgedreht warden können. Die Nockenwellenschalen sind gekeinnzeichnet, nicht wie man erwartet mit 1 beginnend, sondern mit 0 beginnend! Die erste Nockenwellenhalbschale 0 befindet sich auf der Auslassseite vorne beim Zahnriemen. Das heist, auf der Auslassseite haben wir die Nockenwellendeckel von 0 – 4 und auf der einlassseite von 5 – 9. Die Deckel mit den passenden Schrauben bitte nicht verwechseln und sorgfältig ablegen.
Wichtig: Die Nummern der Nockenwellenschalen zeigen immer nach aussen!
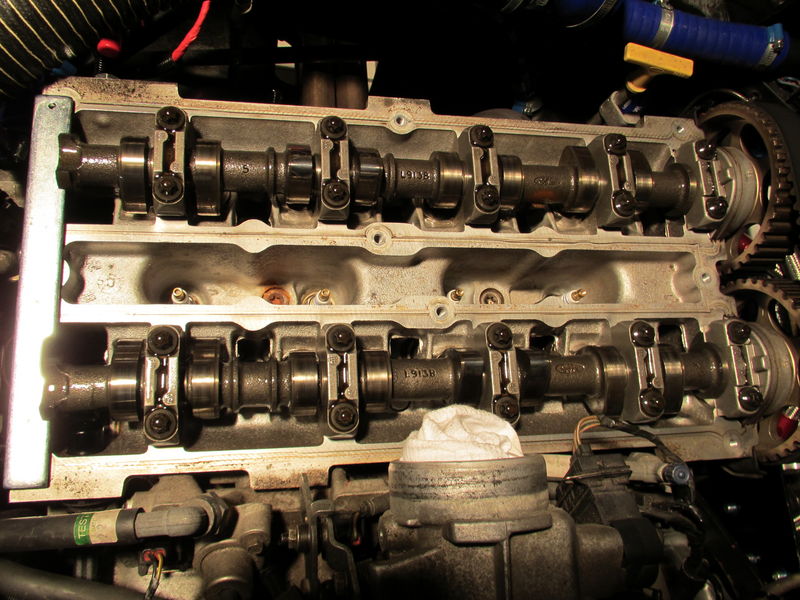
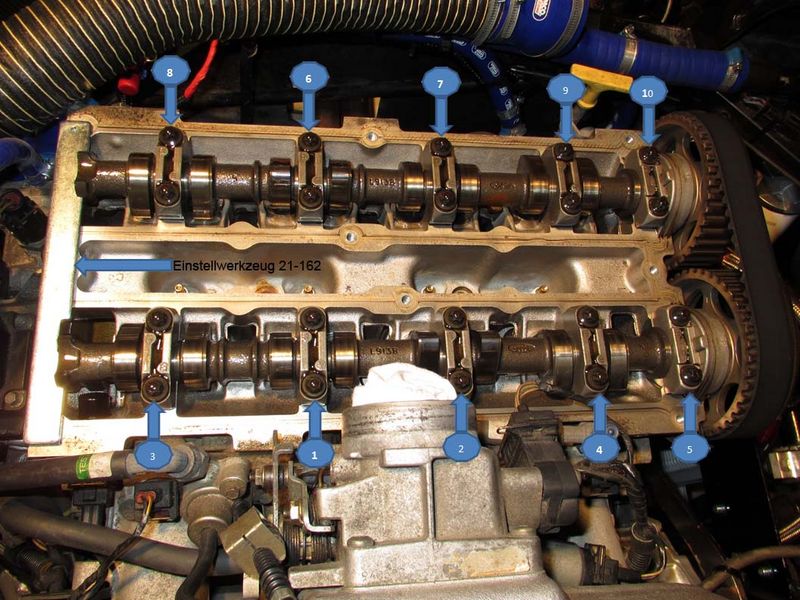
26. NOVEMBER 2015
Auf diesen Bildern erkennt man die Blindstopfen der Öleinspritzdüsen für die Kolbenbodenkühlung. Ich würde die Blindstopfen , vorausgesetzt der Motorblock des RDB Motor’s ist der gleiche wie der vom RQB Motor, gerne entfernen und durch Öleinspritzdüsen ersetzen. Ich bin mir aber nicht sicher ob dies so ohne weiteres möglich ist.
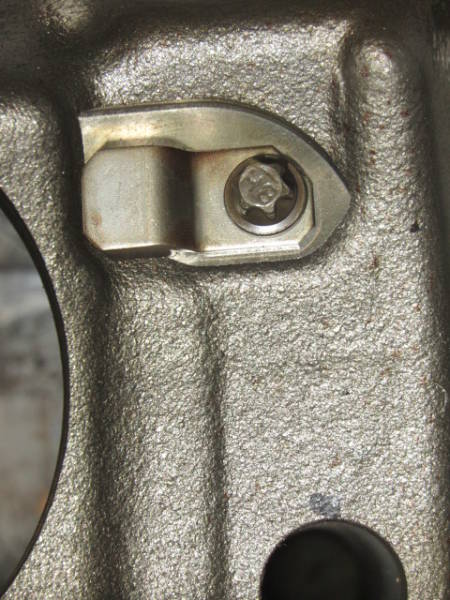
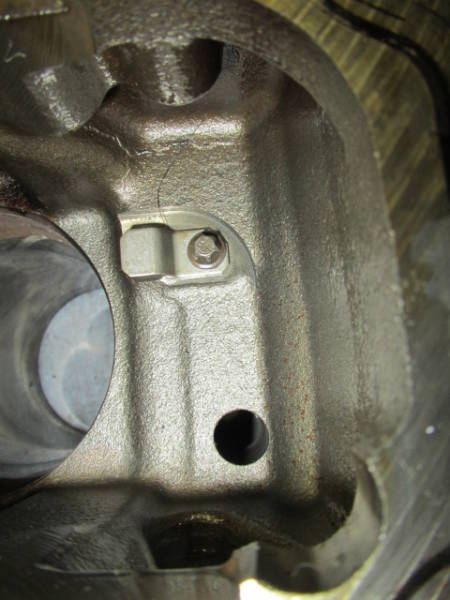
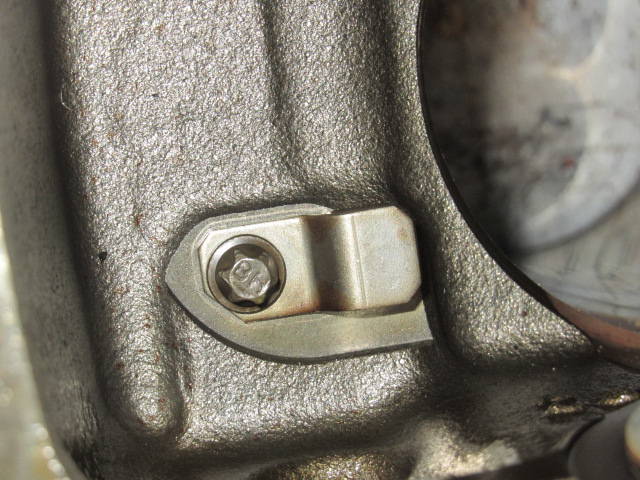
21. NOVEMBER 2015
Der komplette Block ist demontiert, alle Teile wurden gewaschen, gereinigt und vermessen. Auf den Fotos erkennt man dass die Ölwanne und das Ölleitblech , welches an den 2 Kurbelwellenlagerschalen 2 + 4 mit 4 Schrauben gehalten wird, bereits ausgebaut sind. Ich bin mir nähmlich nicht sicher dass es sich bei dem Motor um einen RQB Motor handelt. Auf dem Zylinderkopf sind die Buchstaben RDB eingestanzt, die eindeutig auf einen Fiesta III Motor hinweisen. Jedoch wurde dieser Motor in einer 105 PS und einer 130 PS Variante eingebaut. Die 130 PS Variante war im XR2i eingebaut. Im Escort XR3i hiess dieser Motor RQB. Hauptaugenmerk bei diesen Motoren waren die Öleinspritzdüsen für die Kolbenbodenkühlung.
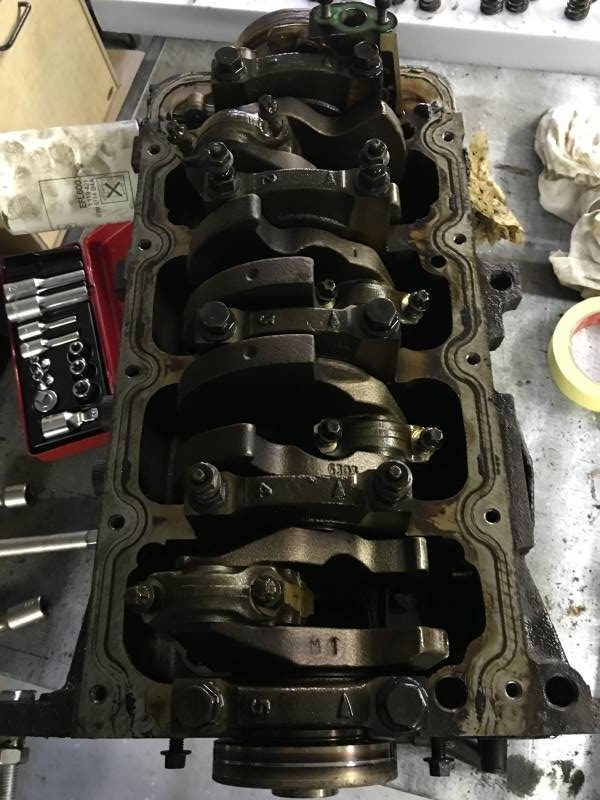
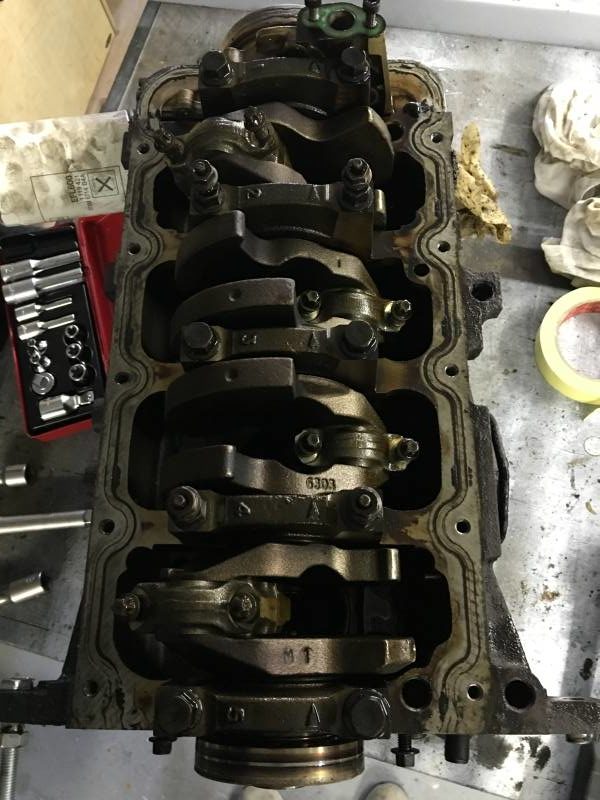
Das Ölansaugrohr ist abgebaut und man erkennt die darunter liegende Dichtung. Der Deckelflansch, der den hinteren Radialdichtring der Kurbelwelle trägt, ist ausgebaut. Der Deckelflansch wird mit 4 Schrauben gehalten. Ich habe alle Schrauben wieder in die Gewinde eingedreht damit keine Schraube verloren geht. Auf dem rechten Foto erkennt man den Flansch der das Schwungrad trägt.
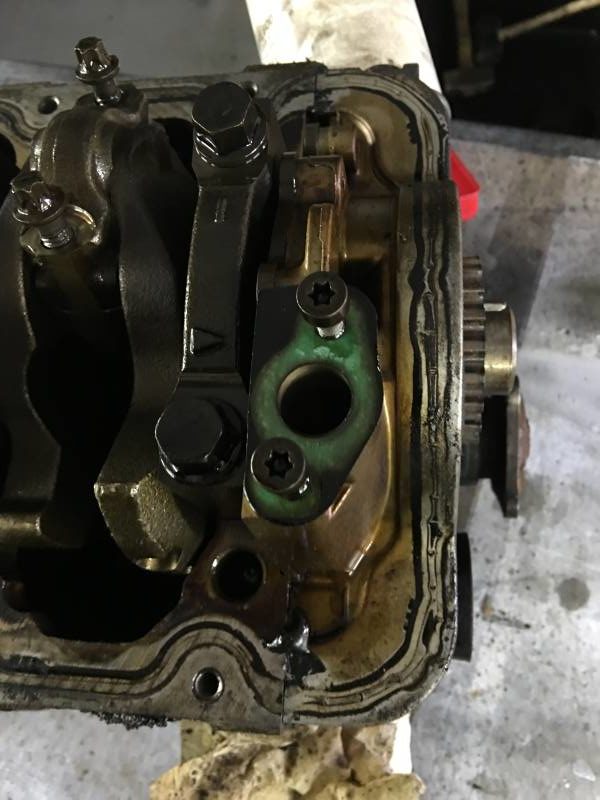
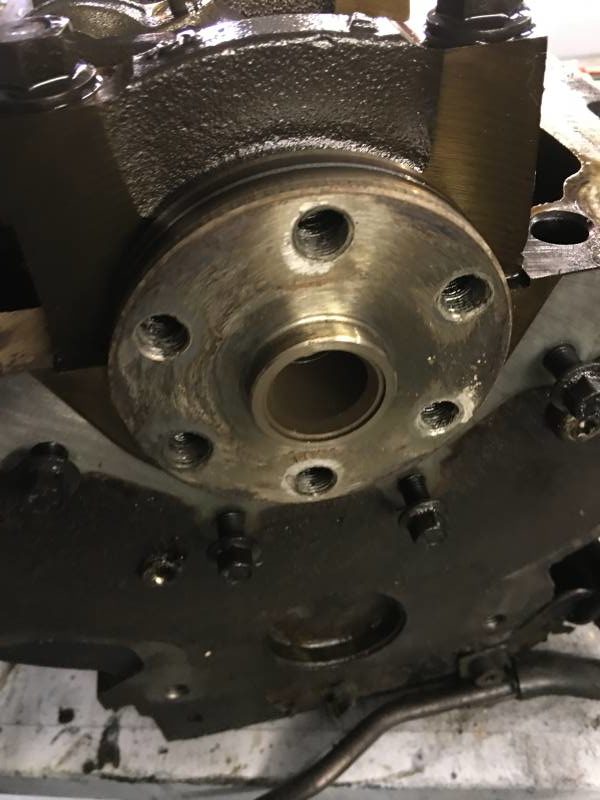
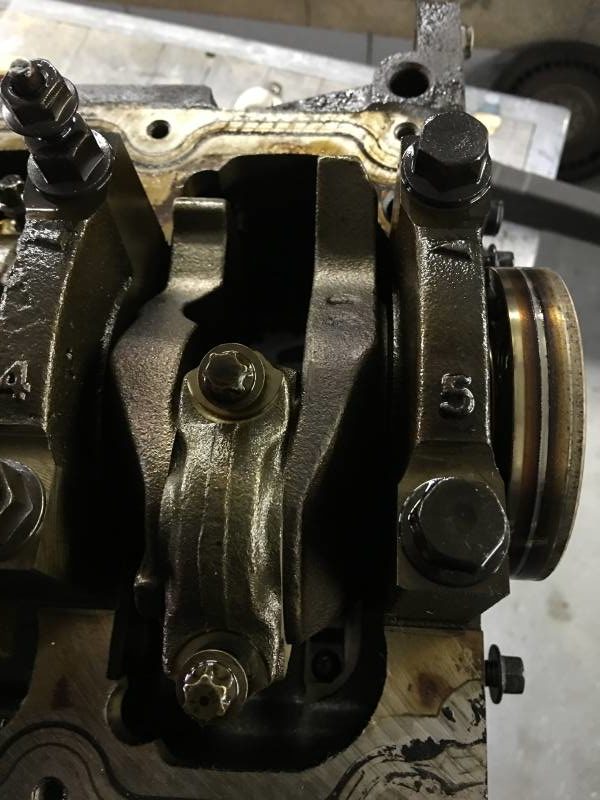
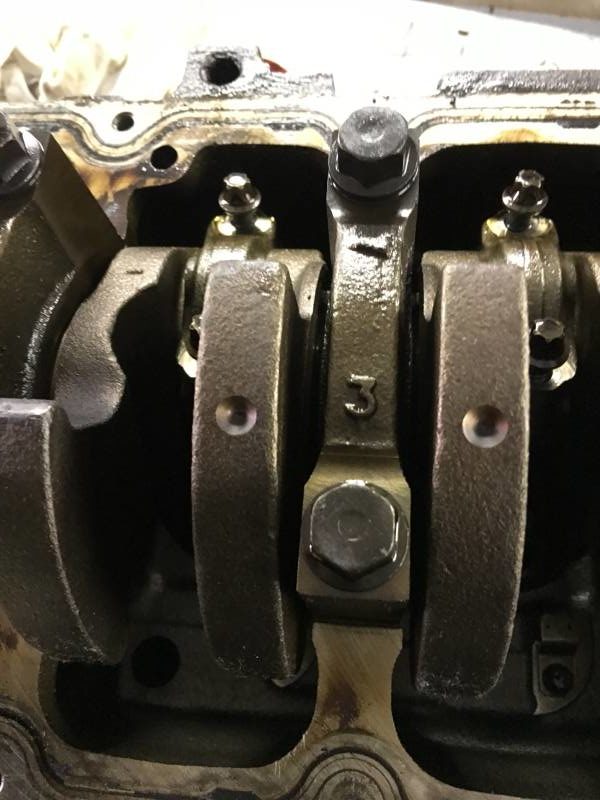
Hier erkennt man den Deckelflansch der den hinteren Radialdichtring der Kurbelwelle trägt. Ich habe diesen Deckelflansch nur provisorisch montiert da ich ein Foto von diesem machen wollte.

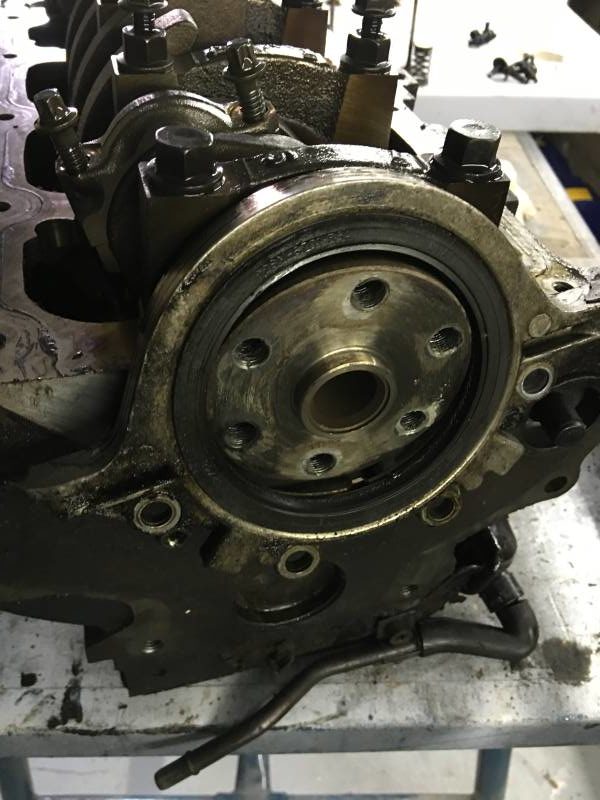
Die Kurbelwellenlagerschalen sind bereits gelöst worden und die Kurbelwelle ist fast zum Ausbau bereit. Man erkennt deutlich die Reihenfolge der Kurbelwellenschalen. Die Pfeile auf den Lagerschalen zeigen nach vorne , also in Richtung Wasserpumpe oder 1 Zylinder.
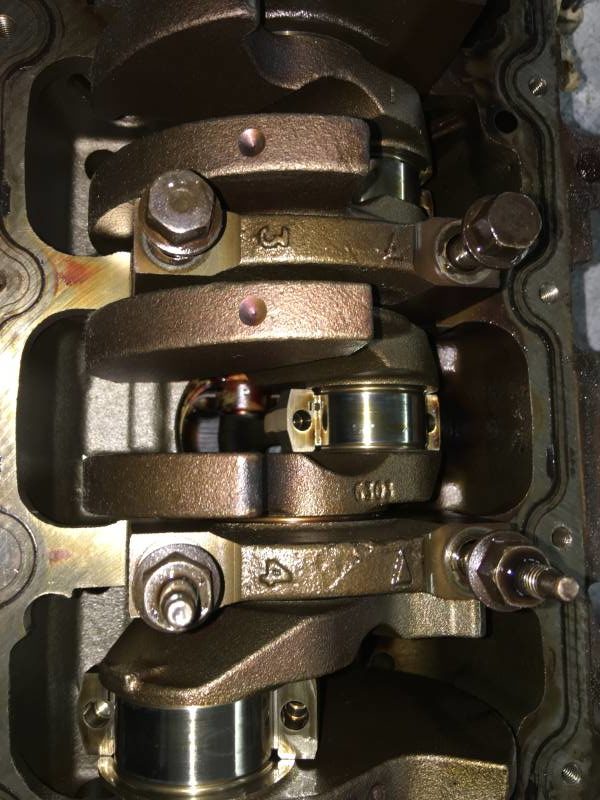
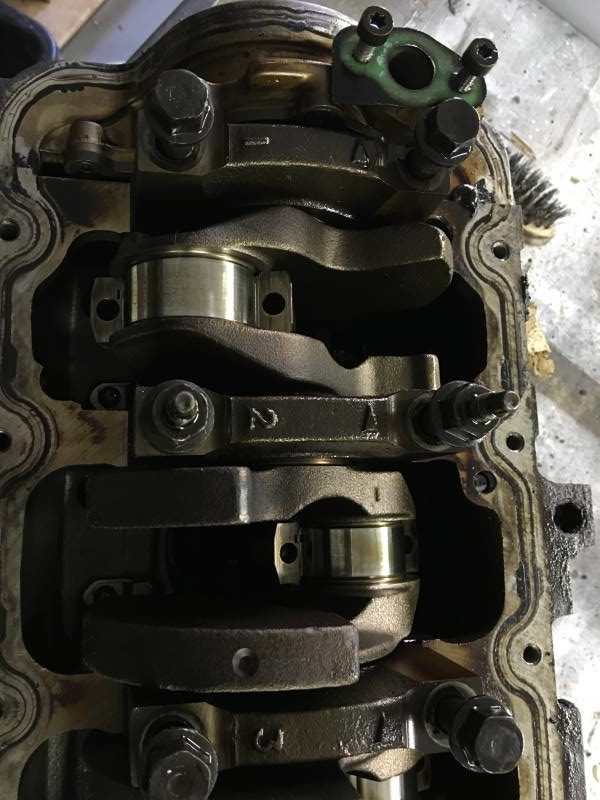
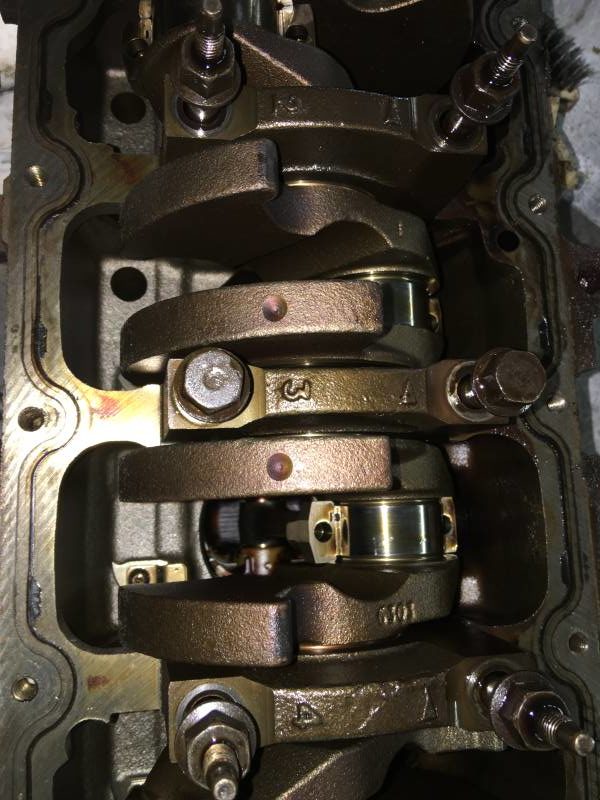
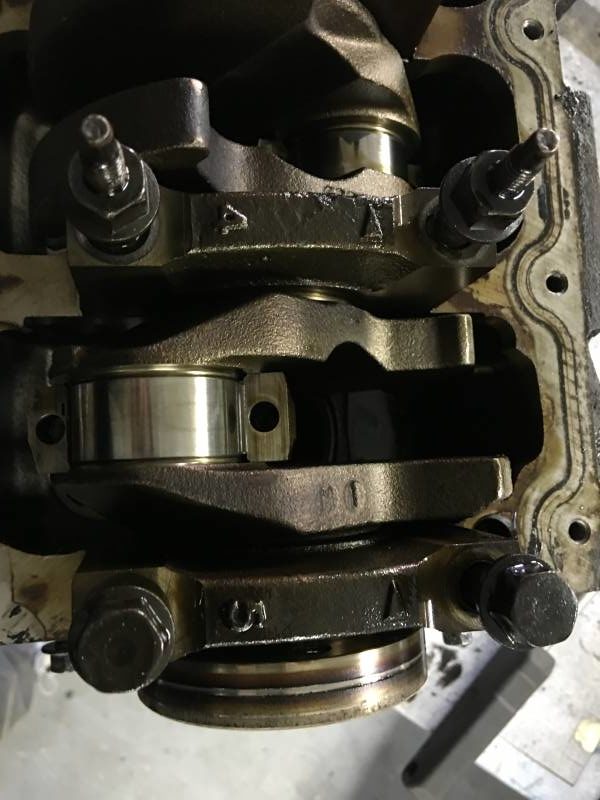
Die
Ölpumpe ist ausgebaut und wird im Kaltreinigerbad gereinigt. Die
Kurbelwellenlagerschalen sind komplett ausgebaut und die
Pleuellagerschalen sind bereits entfernt worden. Die Kolben befinden
sich jedoch noch im Block.
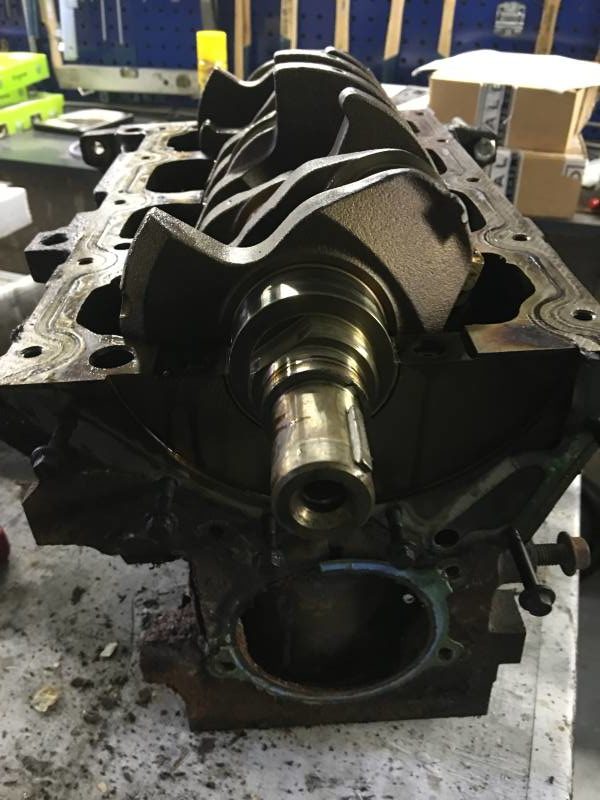
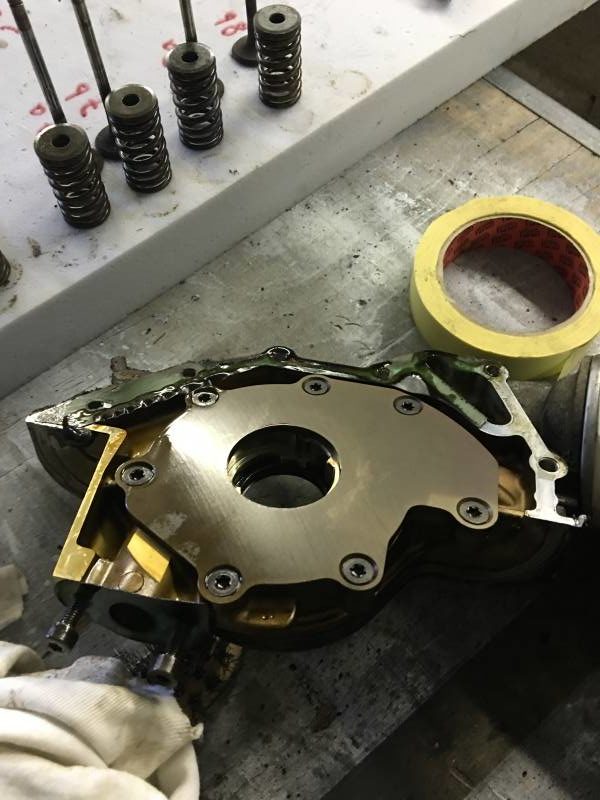
Die Kurbelwelle ist komplett ausgebaut. Die Kolben und die Pleuel sind auch ausgebaut und liegen in der richtigen Reihenfolge auf der Werkbank. Ich habe alle Pleuellager sorgfältig wieder mit dem dazugehörenden Pleuel gekennzeichnet damit ich diese beim Zusammenbau nicht verwechseln kann. Eine kleine Unsicherheit und eine Vermutung machen sich in mir bemerkbar. Ich sehe keine Öleinspritzdüsen für die Kolbenbodenkühlung. Sollte es sich wirklich bei diesem Motor um die 105 PS Ausführung handeln. Das würde den Motor für mich wertlos machen. Die ersten Anzeichen habe ich bereits beim Ausbau der Wasserpumpe entdeckt.
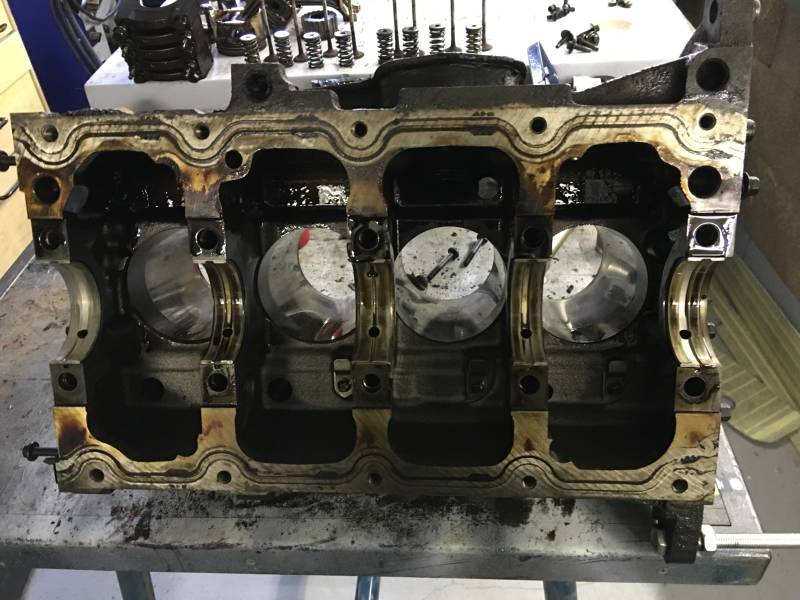
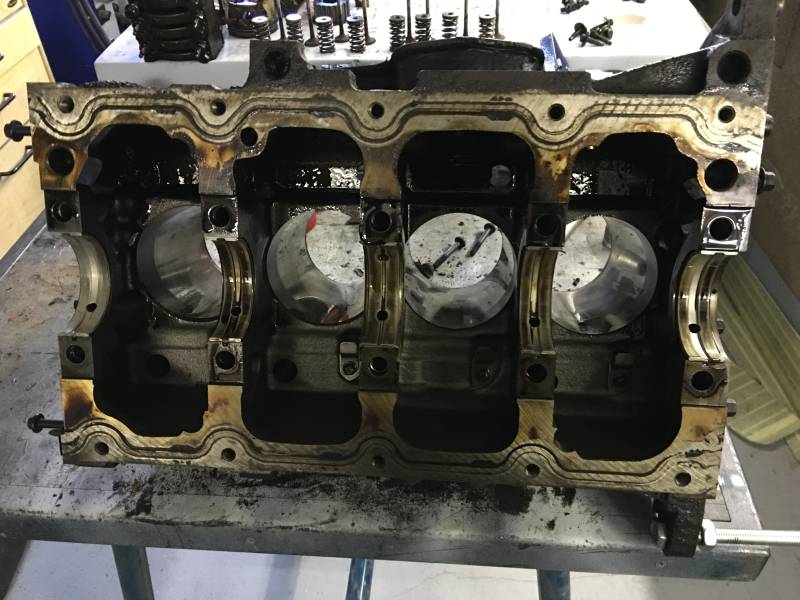
Der Block liegt in der Wanne mit Kaltreiniger. Ich habe alle Teile sorgfältig mit Kaltreiniger und einer Verdünnung gereinigt.
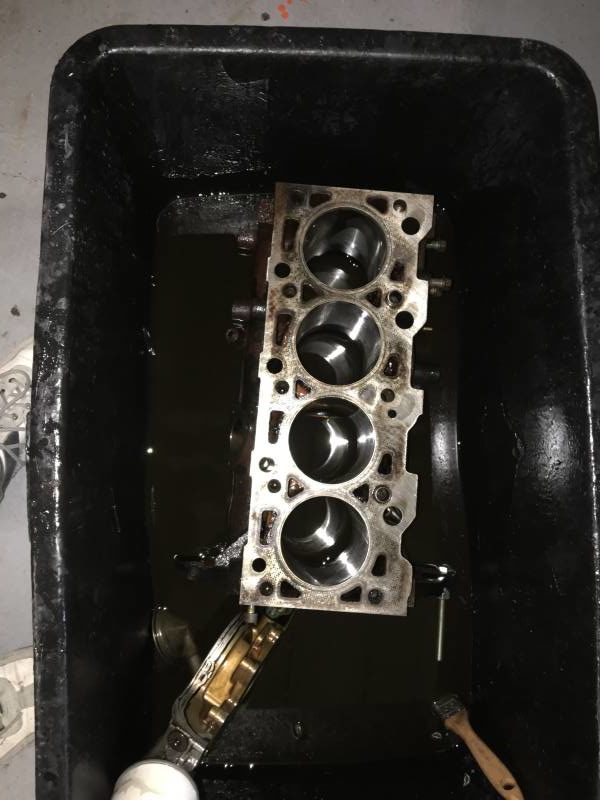
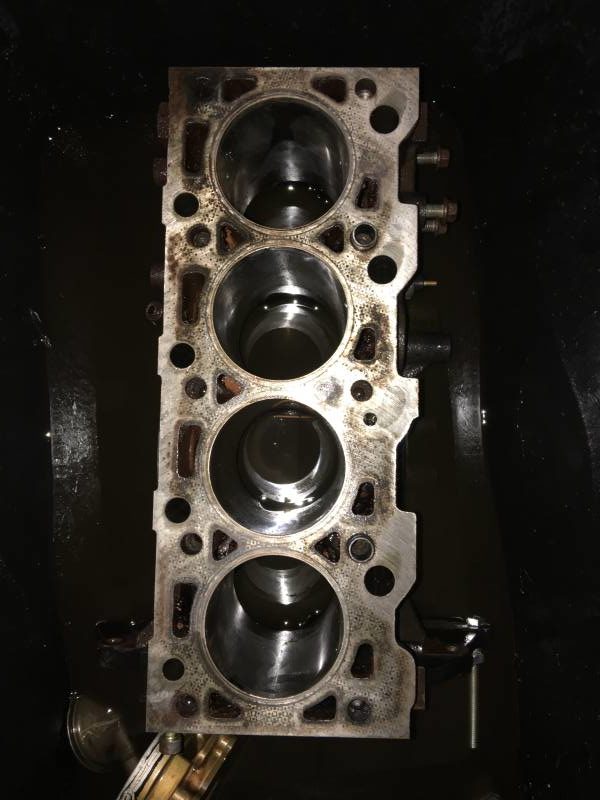
Ein
tiefer Kratzer in der Lagerschale des Kurbelwellenlagers 4. An der
Kurbelwelle ist jedoch kein Schaden feststellbar. Aber eindeutig ein
kleiner Lagerschaden am Kurbelwellenlager der Kurbelwellenlagerschale 4.
Der Kratzer ist schon tief und mit dem Fingernagel deutlich spürbar.
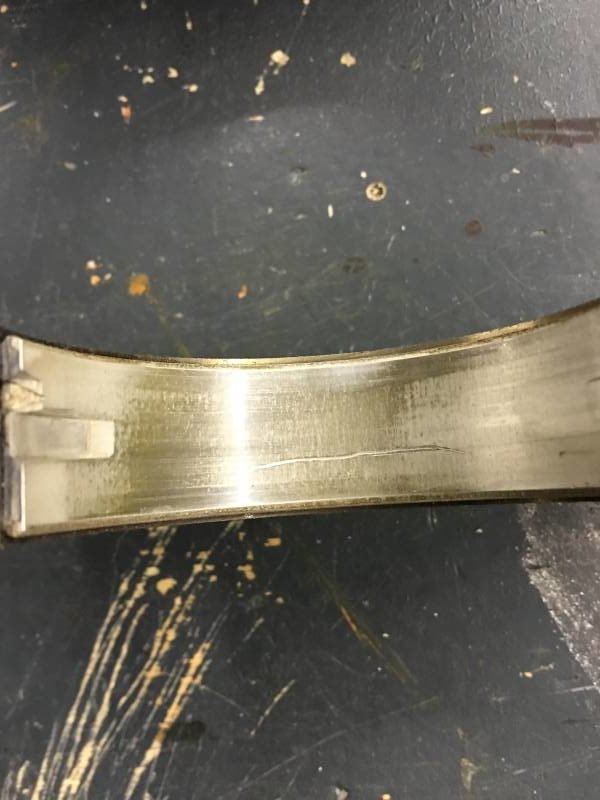
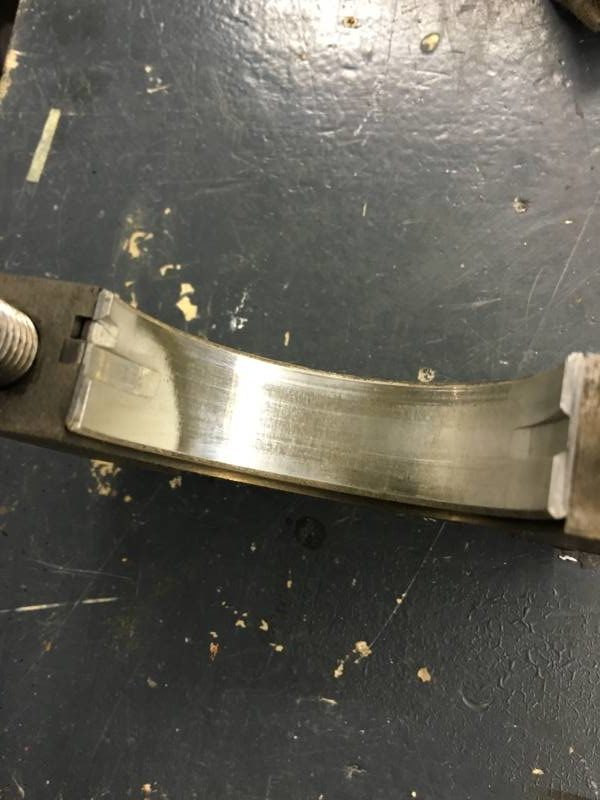
Deutliche Laufspuren an den Lagerschalen der Kurbelwellenlager 3 +4 + 5.
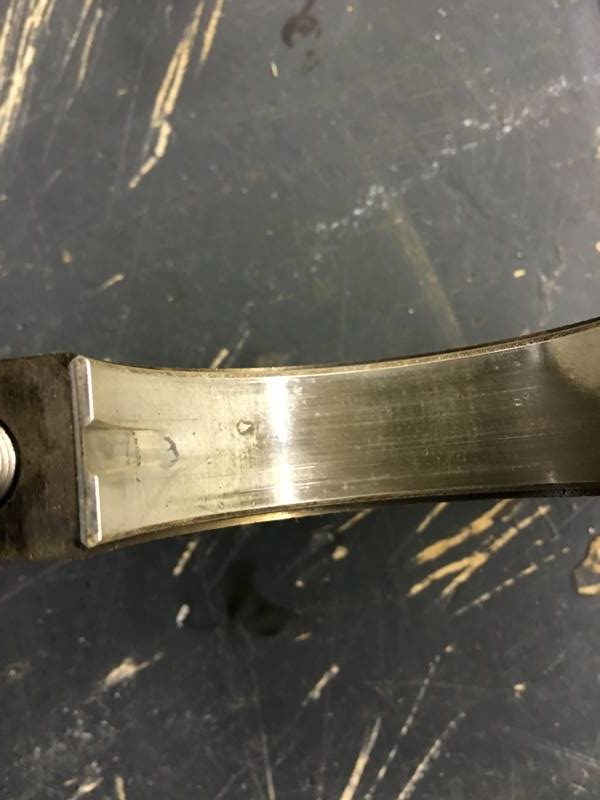
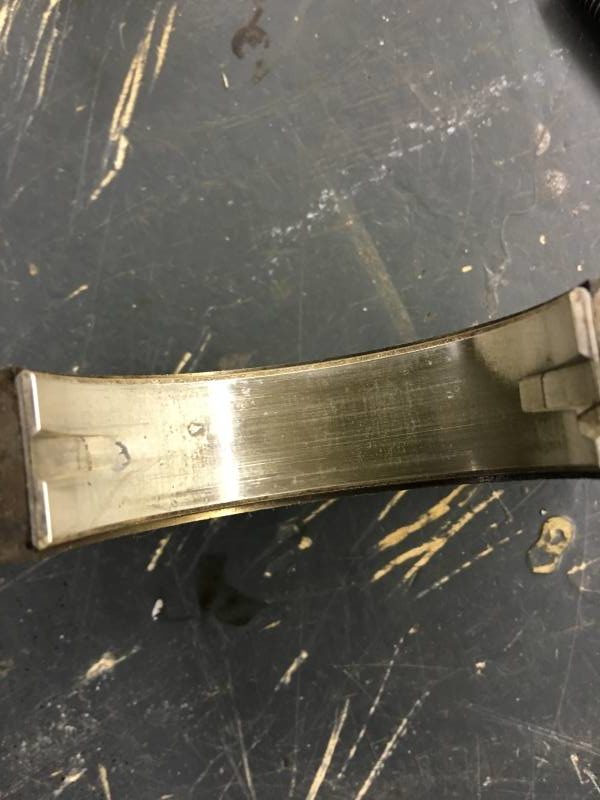
Die Kurbelwellenlager der Lagerschalen 1 +2 sehen sehr gut aus. Bei einer Laufleistung von 100.000 Km sehen diese sehr ordentlich aus.
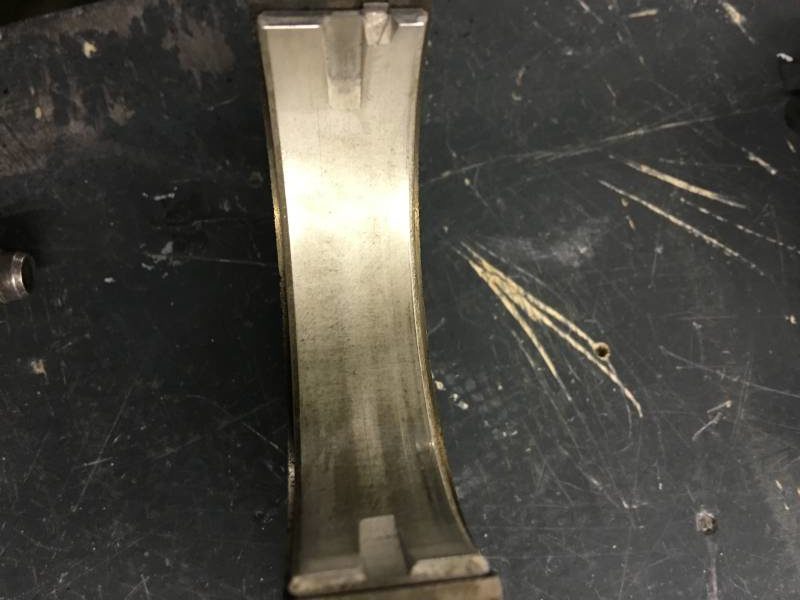
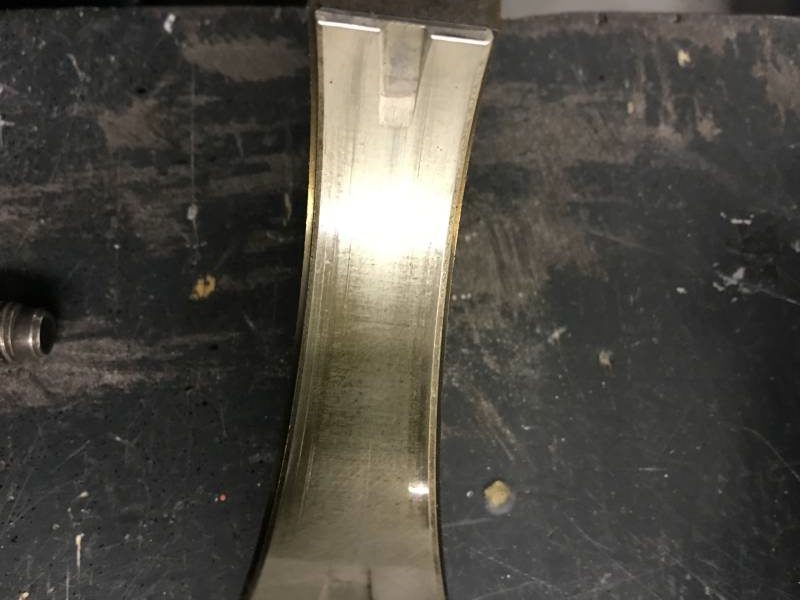
18. NOVEMBER 2015
Noch ein Versuch die Stehbolzen zu entfernen. Ich habe den Kopf im Backofen auf 280 ° erwärmt und anschliessend die Stehbolzen gekühlt. Der Versuch ist gescheitert, die Stehbolzen wehren sich hartnäckig.
17. NOVEMBER 2015
Der Zylinderkopf wurde komplett mit synthetischer Verdünnung gereinigt und mit Kaltreiniger gespült. Heute Abend wurden noch die Nockenwellenhalterungen gereinigt. Anschließend werden die Ventile mit den Ventilfedern provisorisch eingesetzt damit der Zylinderkopf zu Burton Power gesendet werden kann. Dort werden die Ventilsitze vergrößert damit die neuen größeren Ventile Platz haben. Original sind beim Zetec ein 32mm Einlassventil und ein 28mm Auslassventil verbaut. Später wird ein 33,5mm Einlassventil und ein 28mm Auslassventil eingebaut sein und die Kanäle werden auf das maximale Maß geweitet. Des weiteren werden 278 ° Nockenwellen eingebaut.
15. NOVEMBER 2015
Der Zylinderkopf ist abgebaut und liegt auf der Werkbank. Den Auspuffkrümmer habe ich mit viel Mühe und lieben Worten abgebaut. Nun muss ich noch irgendwie die Stehbolzen vom Auspuffkrümmer entfernen. Alle Versuche diese zu entfernen sind gescheitert. Ich habe folgendes ausprobiert um die Stehbolzen zu entfernen:
- 2 Stück M8 Muttern auf die Stehbolzen geschraubt und gegeneinander gekontert.
- Die Stehbolzen mit einem Hartlötbrenner erwärmt und versucht den Stehbolzen zu lösen
- M 8 Muttern auf die Stehbolzen geschweisst und versucht die Stehbolzen zu lösen
- Hammerschläge auf den Stehbolzten um diesen im Gewinde zu lösen
- Rostlöser und andere Chemikalien
- Mit mehr oder weniger guten Worten
Fazit: 5 Stehbolzen sind abgebrochen und 4 Stehbolzen wurden entfernt. Ich werde den Kopf zum Motorenbauer bringen, mal sehen ob er mir weiterhelfen kann. Der Zylinderkopf wurde anschliessend gereinigt und die Ventile ausgebaut. Heute erfolgt noch eine weitere Reinigung mit Kaltreiniger und Dampfstrahler. Anschliessend wird der Zylinderkopf mit Bremsflüssigkeit eingerieben und über Nacht stehen gelassen damit dieser einwirken kann. Dann erfolgt noch eine weitere Reinigung mit Kaltreiniger und Dampfstrahler. Der abschliessende Reinigungsvorgang erfolgt in der Spülmaschine bei 100°.
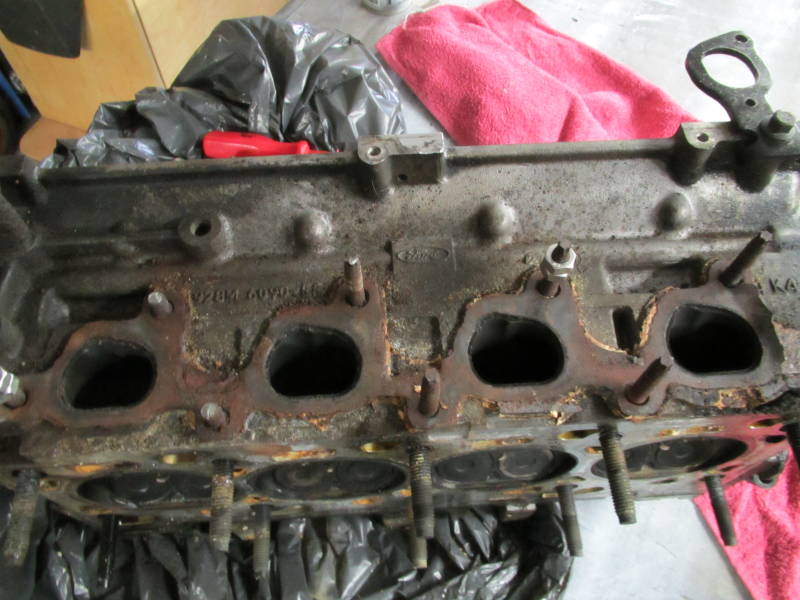
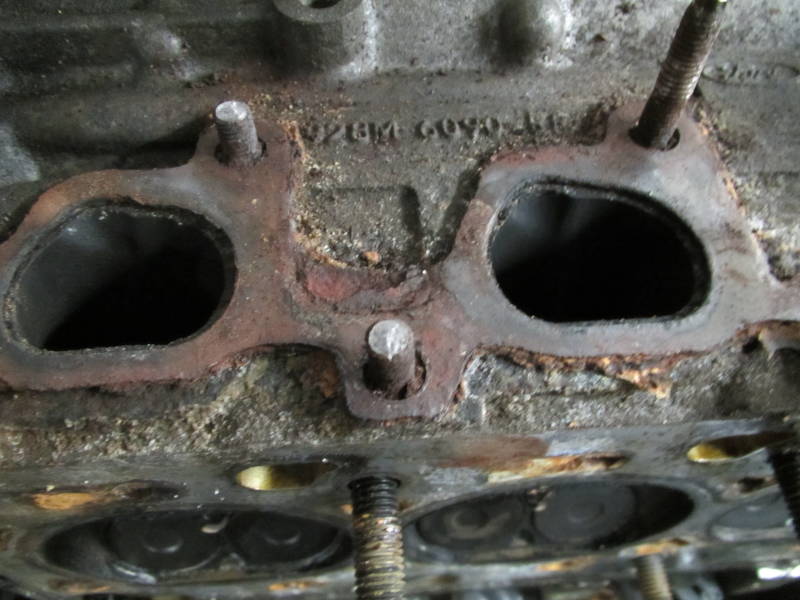
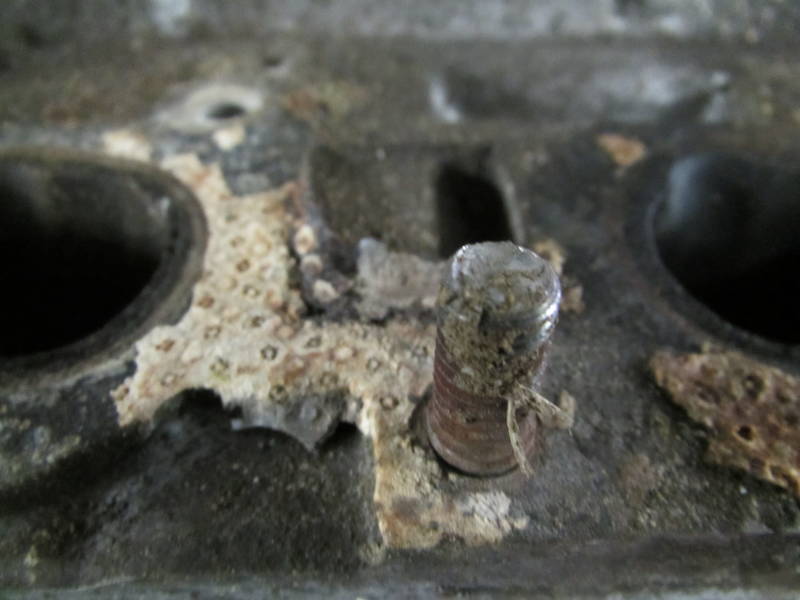
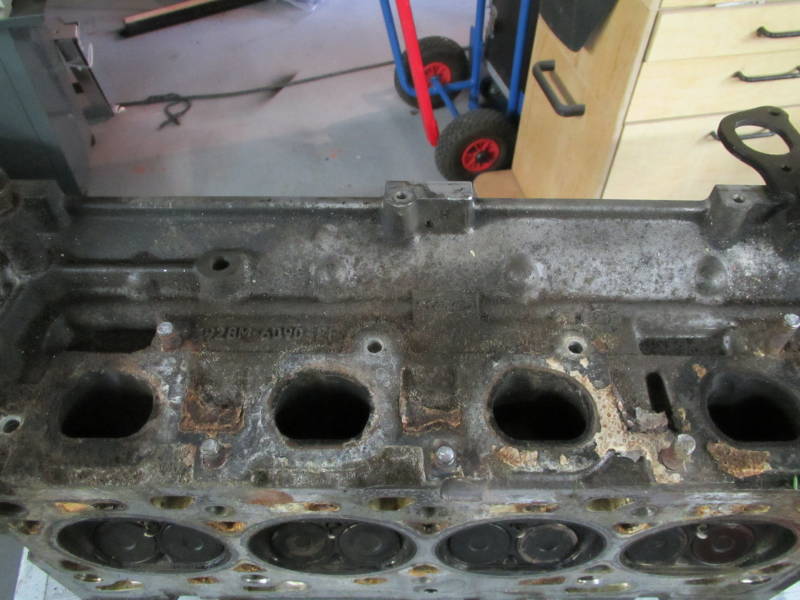
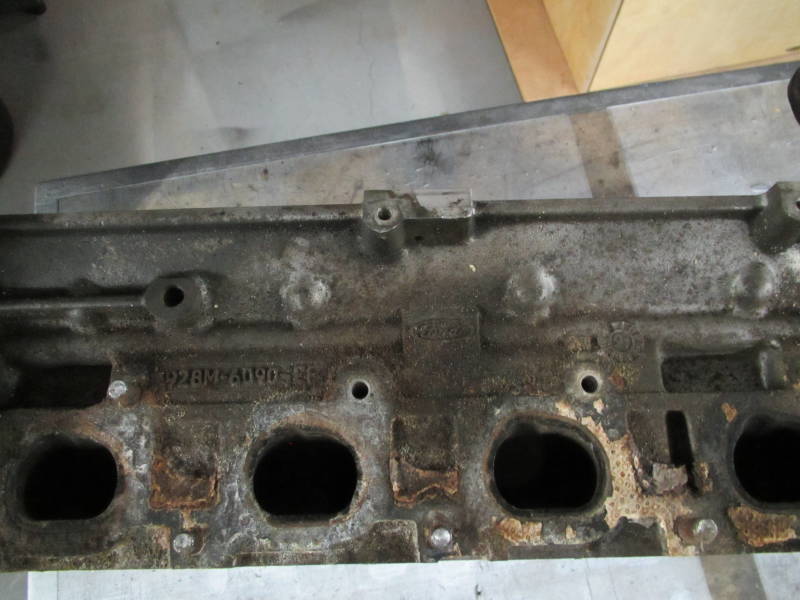
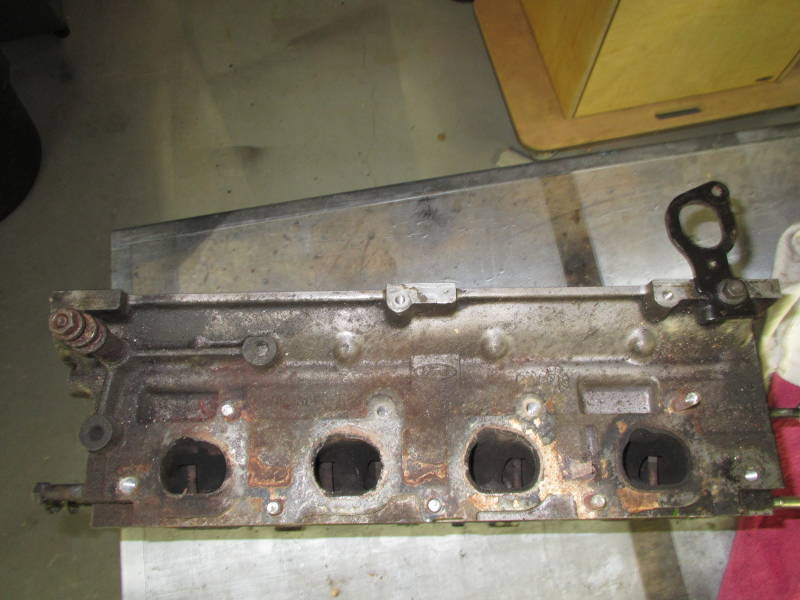
Der Zylinderkopf wurde mit Verdünnung gereinigt, alle Ölreste wurden entfernt. Alte Dichtungsreste werden später entfernt. Auf diesen Fotos sind die Ventile bereits ausgebaut worden.
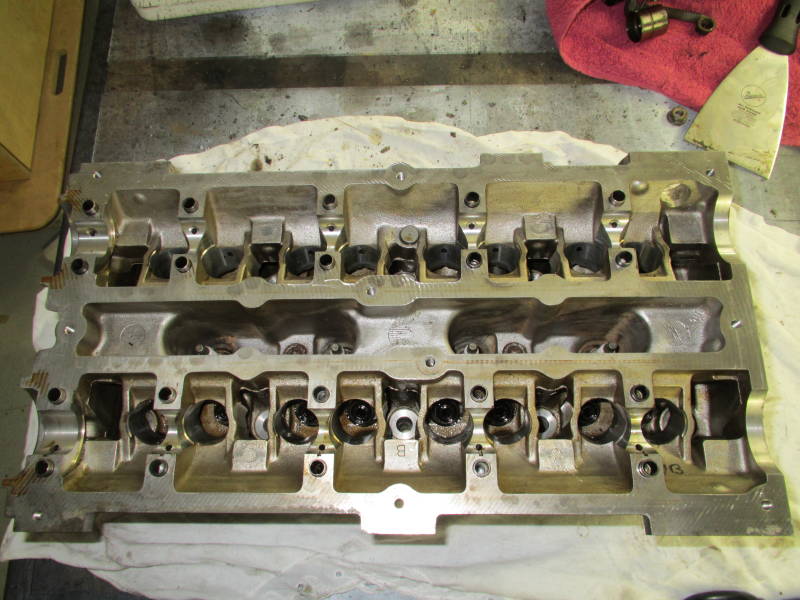
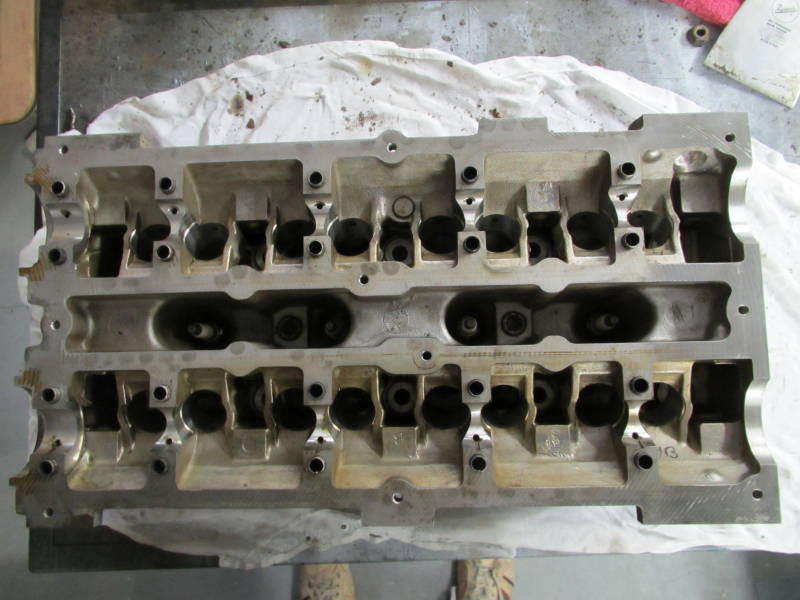
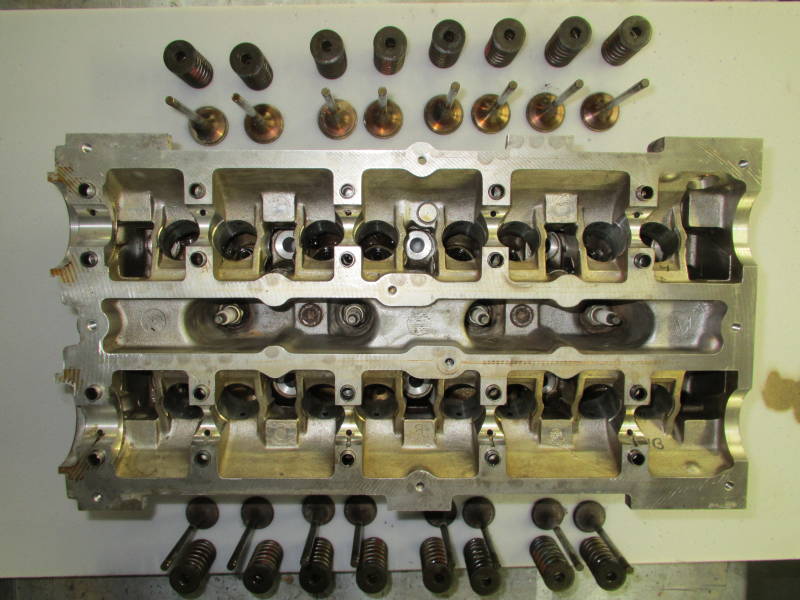
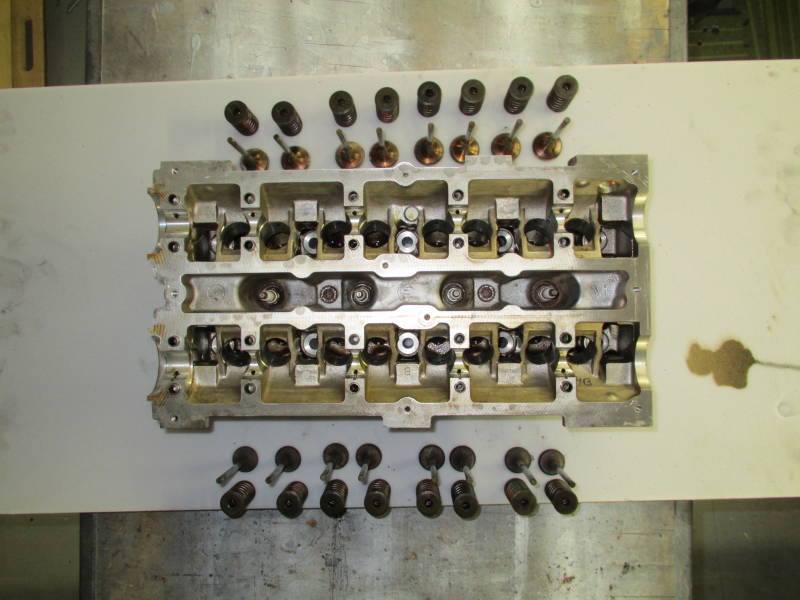
Die Einlassventile mit der Einlassseite des Zylinderkopfes
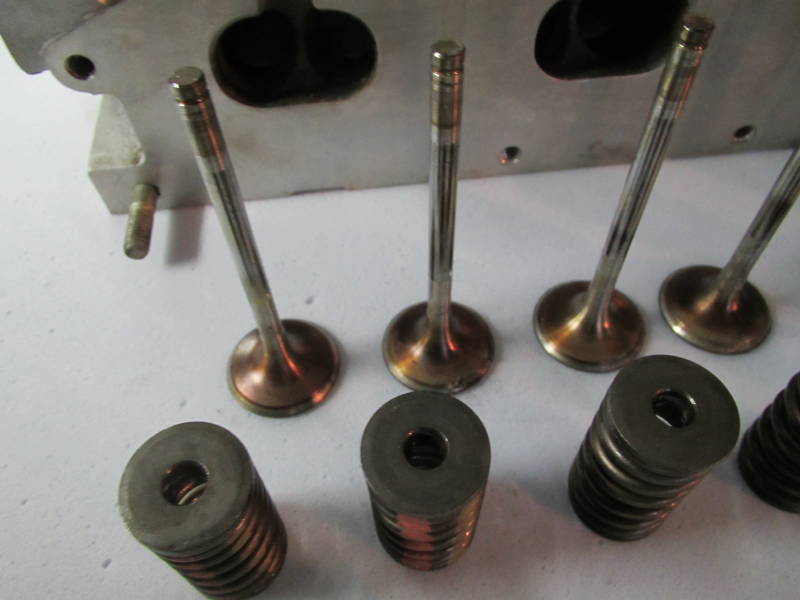
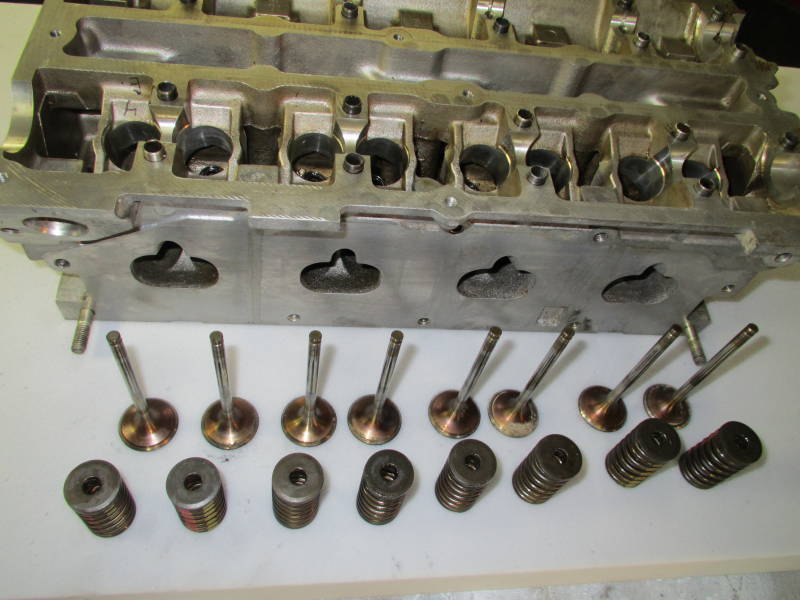
Die Auslassventile mit der Auslassseite des Zylinderkopfes
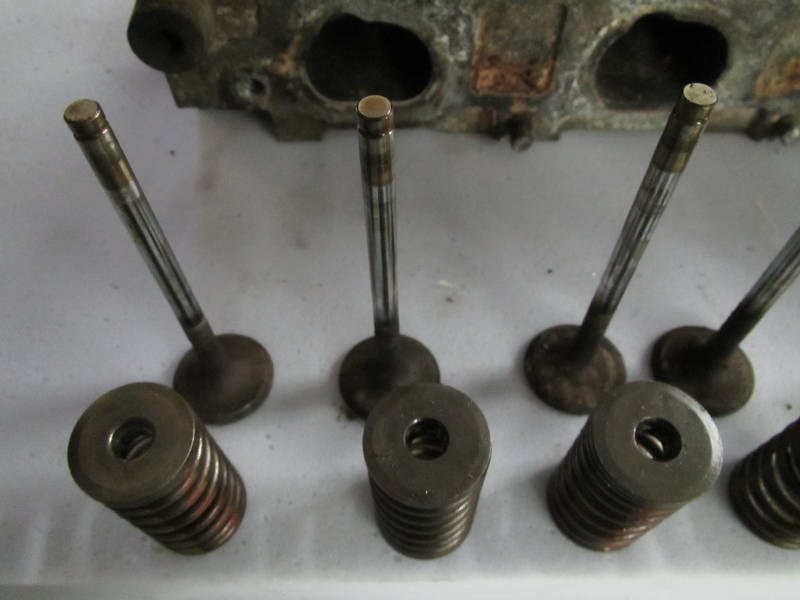
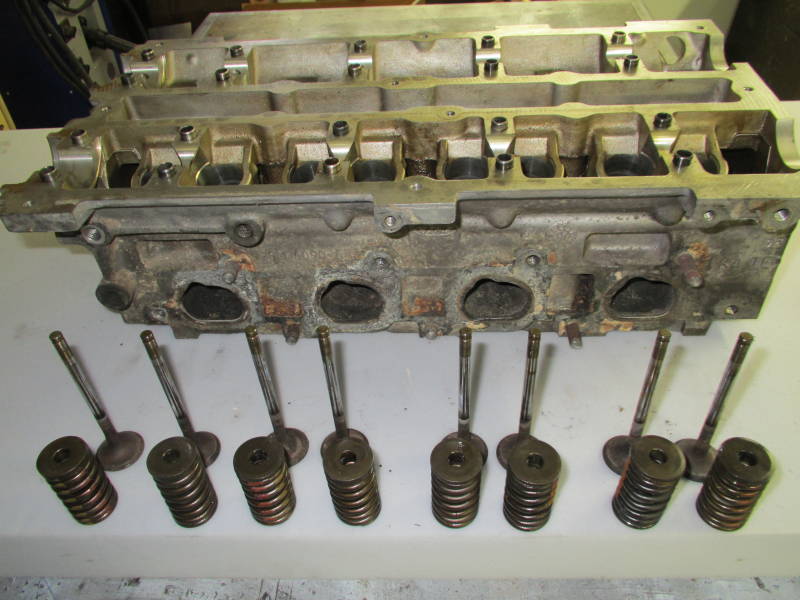
9. NOVEMBER 2015
Zerlegen des Motors:
Der
Motor wurde auf einer Palette angeliefert und das Restöl war
ausgelaufen. Der Motor wird komplett zerlegt und dann wieder neu
aufgebaut. Ich habe heute damit begonnen den Zylinderkopf abzubauen.
Zuerst wurde die EFI Ansaugbrücke mit der Benzinleiste entfernt.
Schwierigkeiten bereitet mir der Gusseiserne Auspuffkrümmer. Alle
Befestigungsschrauben sind eingerostet und beschädigt. 4 Schrauben bekam
ich gelöst, die anderen Schrauben sitzen fest und die Stecknuss passt
nicht mehr auf die Schrauben. Der Zylinderkopf mit den Nockenwellen
wurde abgebaut und wartet nun auf die Reinigung.
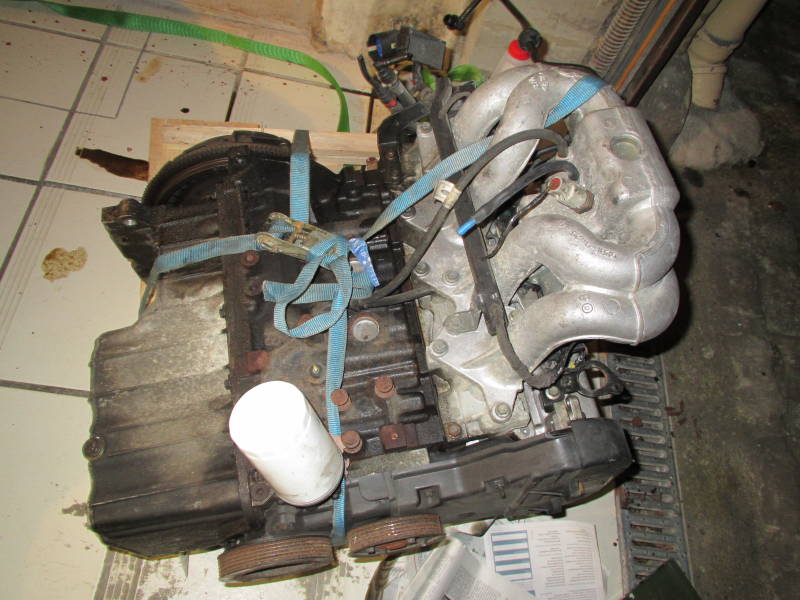
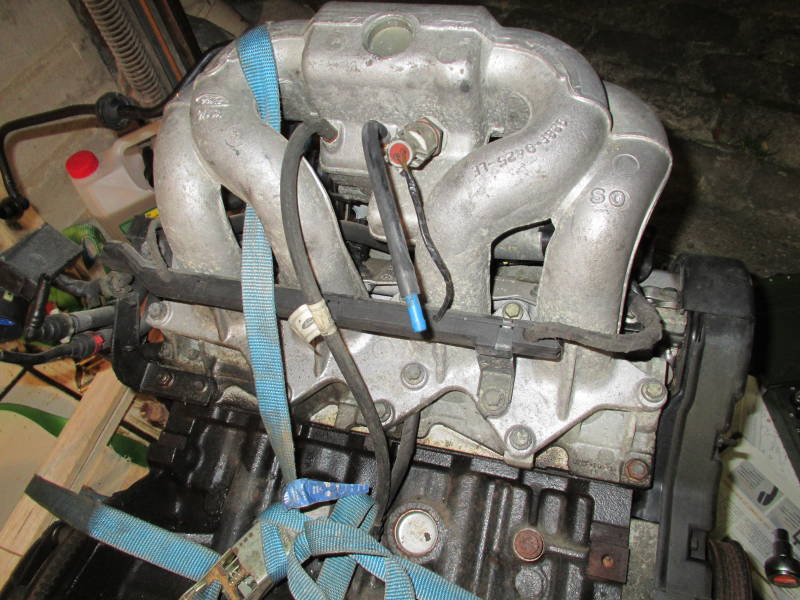
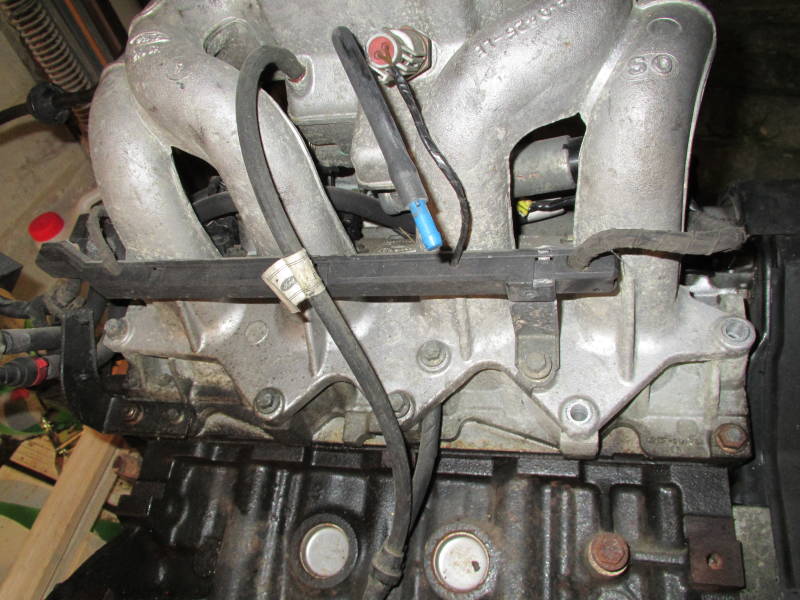
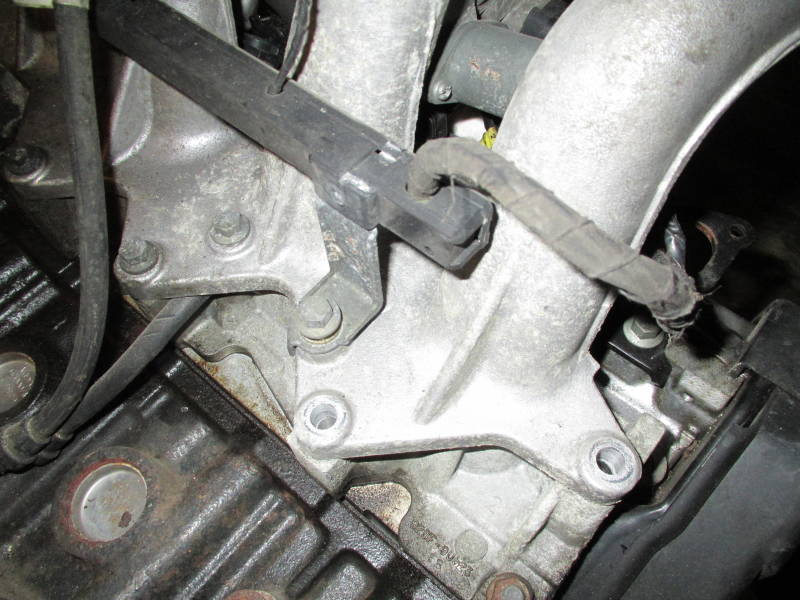
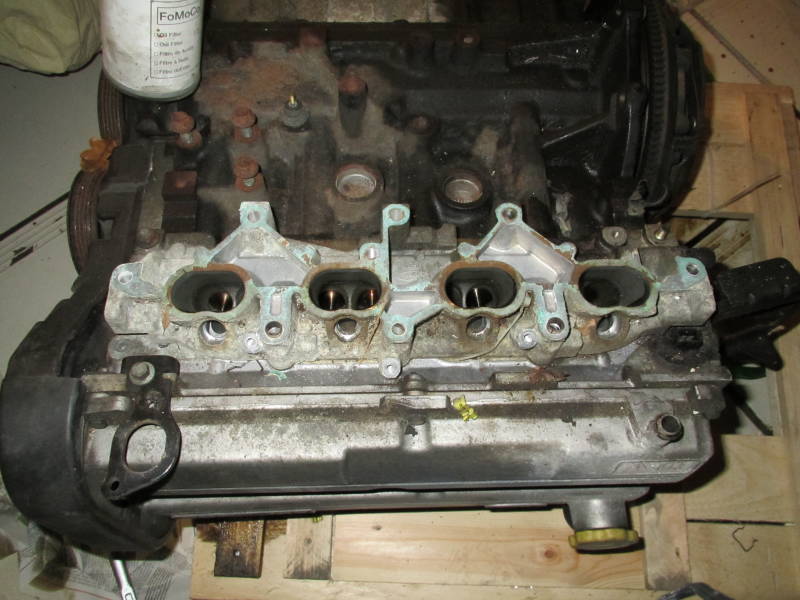
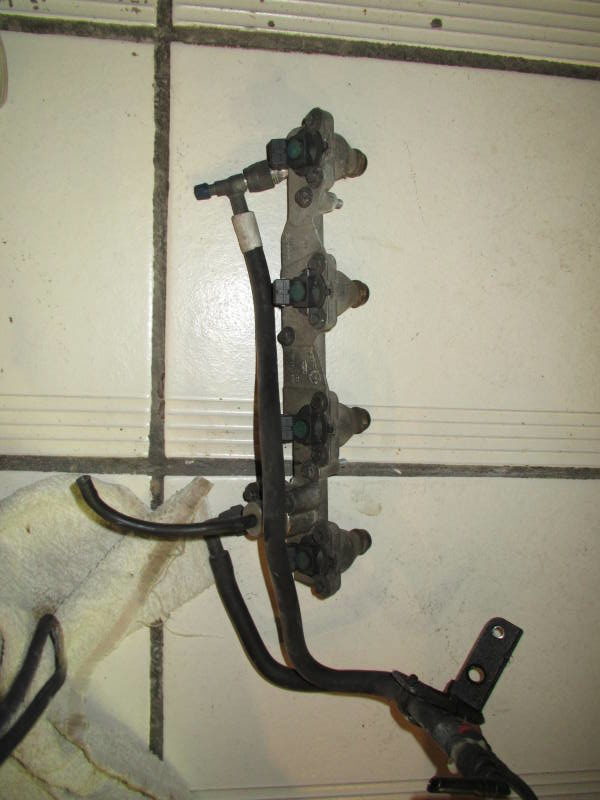
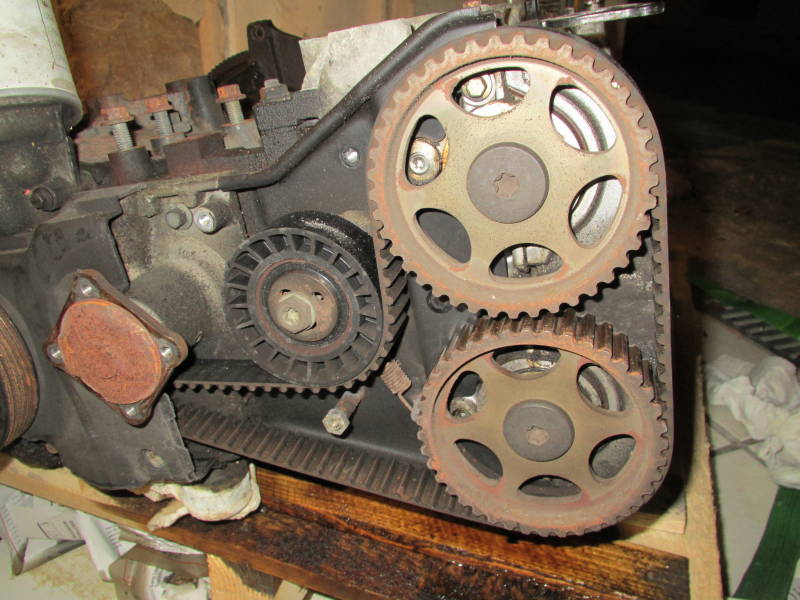
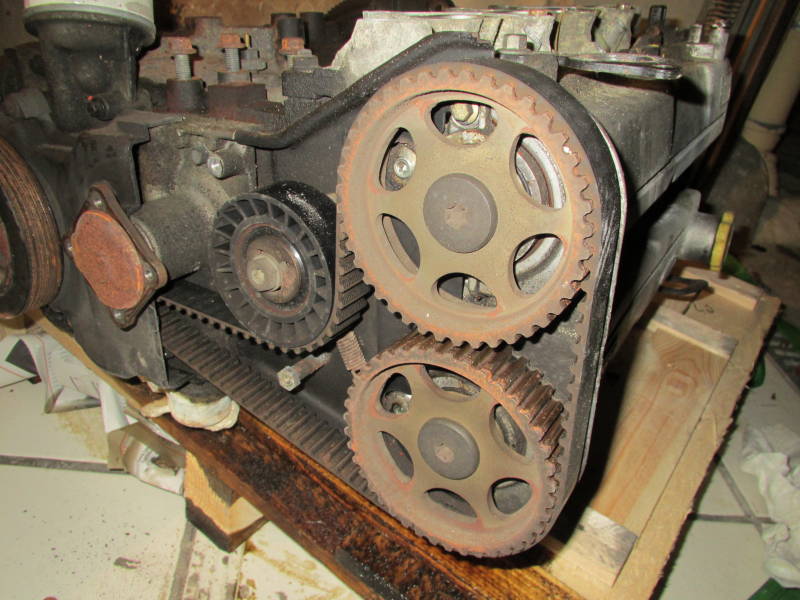
Die beiden Nockenwellen sind ausgebaut, zuerst habe ich die Auslassnockenwelle ausgebaut und diese mit 2 Kabelbindern gekennzeichnet. Das hat keine Auswirkung auf das Zerlegen des Motors, es dient lediglich als Gedächnissstütze beim späteren Zusammenbau des Motors. Rechts auf dem Foto ist der Auspuffkrümmer zu sehen. Ich habe Probleme die Befestigungsschrauben zu lösen.
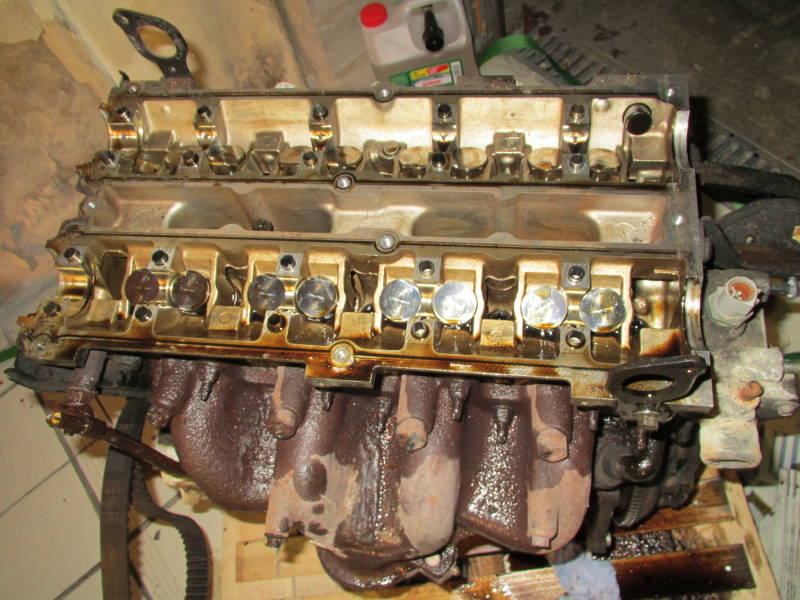
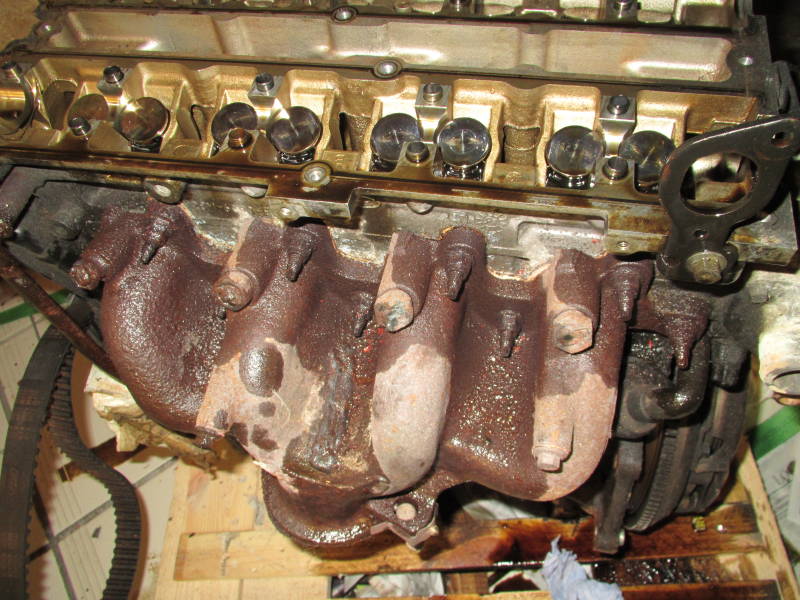
Der Zylinderkopf ist komplett abgebaut und wird gereinigt. Anschliessend wird der Zylinderkopf zu Burton Power als Austauschkopf – Zylinderkopf gesendet.
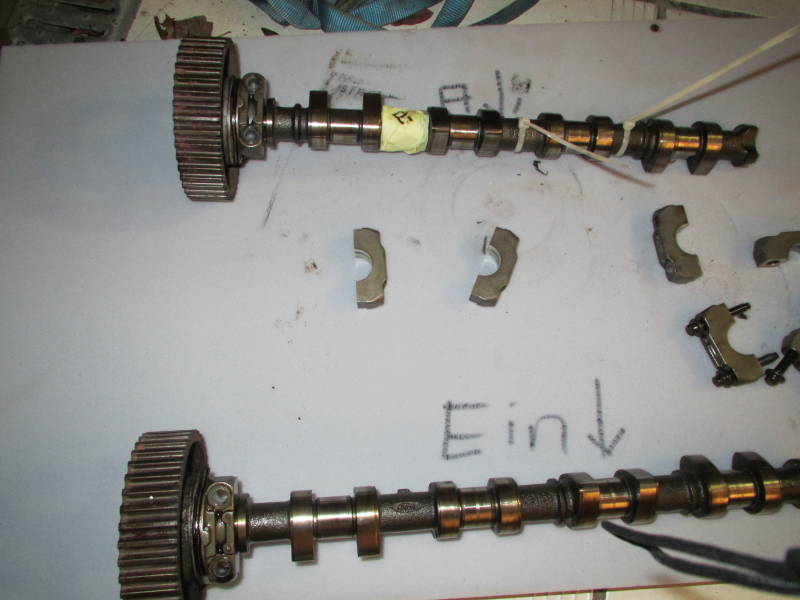
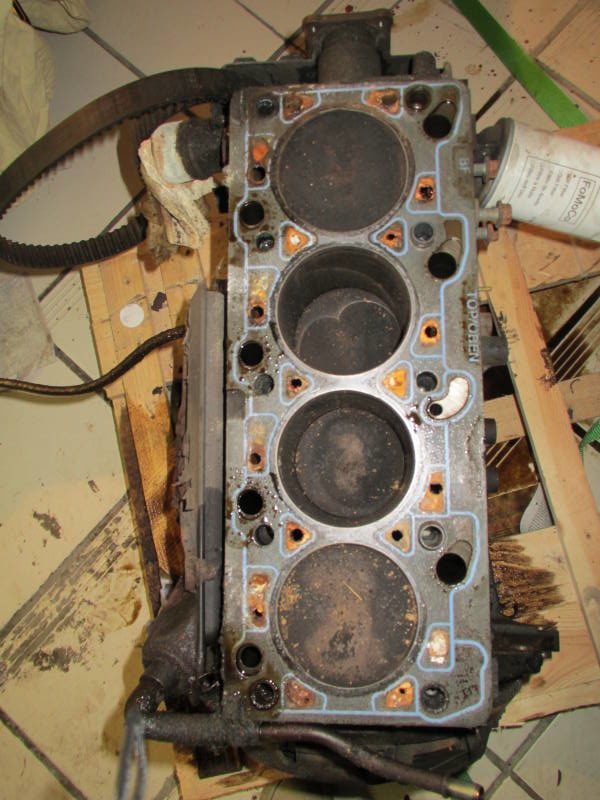
6. NOVEMBER 2015
Heute beginnt der Aufbau an meinen Zetec – Motoren.
Ich habe folgende Motoren zur Verfügung:
- Der eingebaute RQB Zetec – Motor 1.8 mit 130 PS
- Der neue Zetec RQB Zetec – Motor 1.8 mit 130 PS
Umbau – Vorhaben:
- Der eingebaute Zetec – Motor bekommt einen neuen Zylinderkopf Stage 1 von Burton – Power mit einer Nockenwelle 278 ° FZ 2002 von Kent
- Der neue Zetec – Motor bekommt einen neuen Zylinderkopf Stage 2
von Burton Power mit einer Nockenwelle von 278° FZ 2002 von Kent.
Geplant hatte ich den Einbau einer NW von Kent FZ 2003 von 304°. Diese
hat ein Drehzahlband von 3750 – 8000 U/min. Diese NW benötigt auch
andere 32mm Hydrostössel und der Zylinderkopf muss für die Aufnahme
dieser breiteren Hydrostössel in dem Bereich bearbeitet werden. Da diese
NW für den Strassenverkehr nicht mehr geeignet ist, werde ich die NW FZ
2002 mit 278 ° auch in diesen Zylinderkpf einbauen.
- Die NW von Kent 278° hat ein Drehzahlband von 2500 – 7000 U/min.
- Beide Zylinderköpfe werden mit einer Jenvey Einzeldrosseleinspritzung bestückt
- Eine frei programmierbare ECU von Emerald kommt zum Einsatz
- Ein einstellbarer Benzindruckregler wird eingebaut
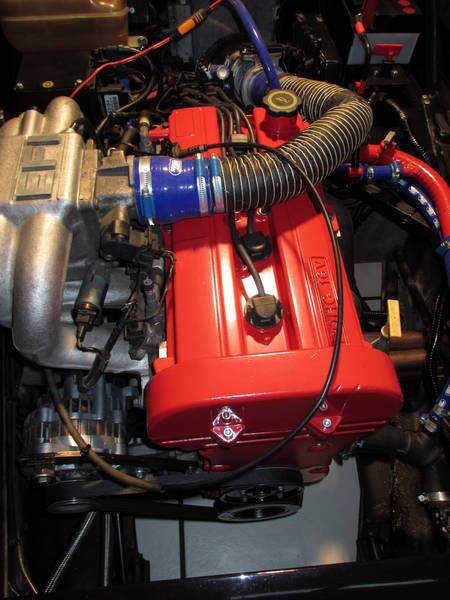
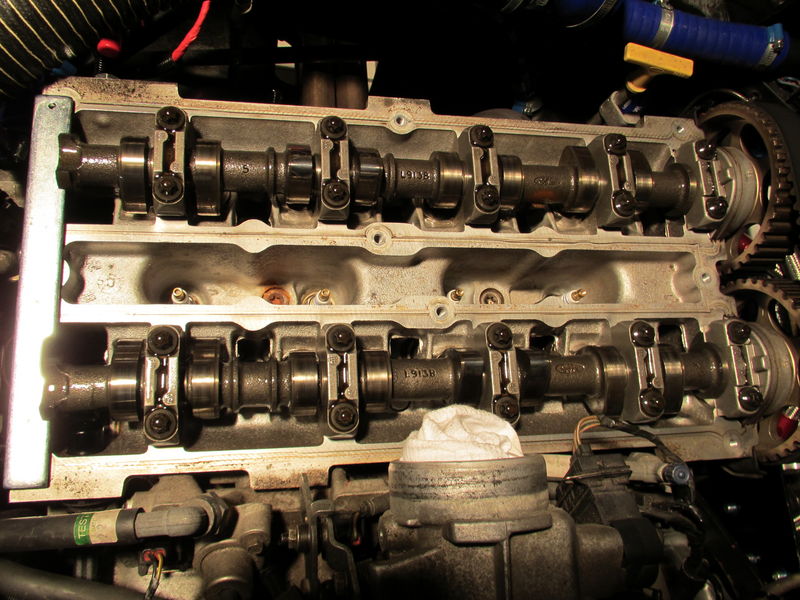
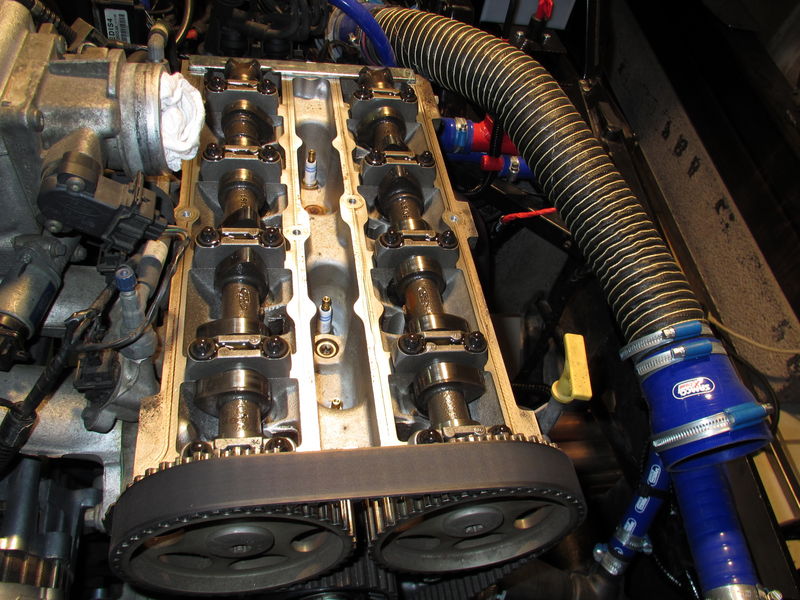
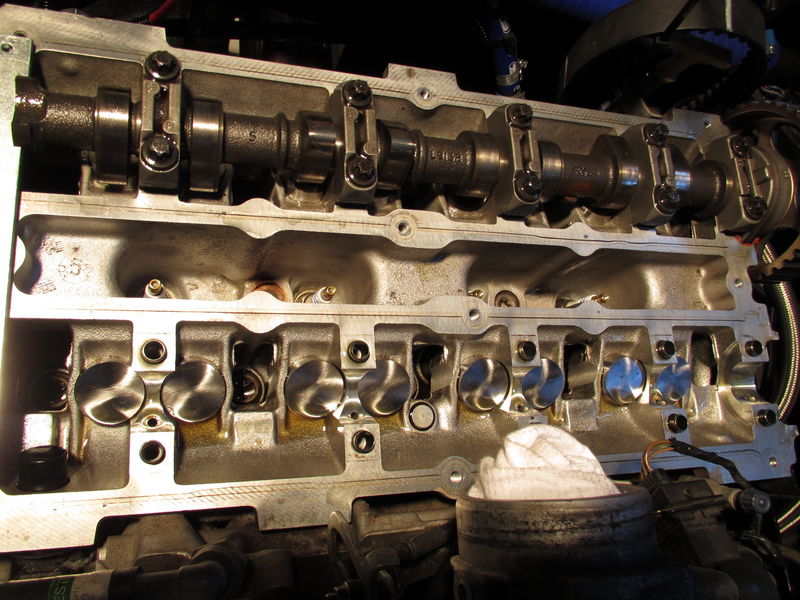

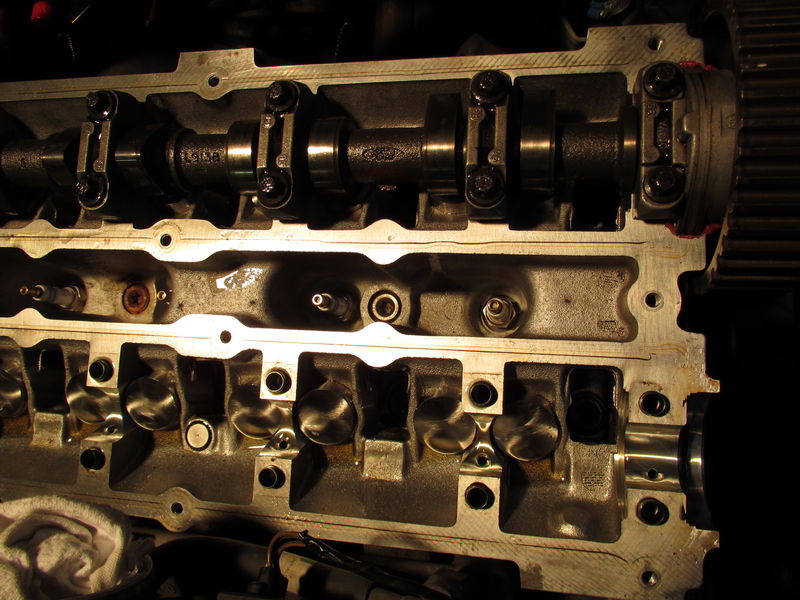
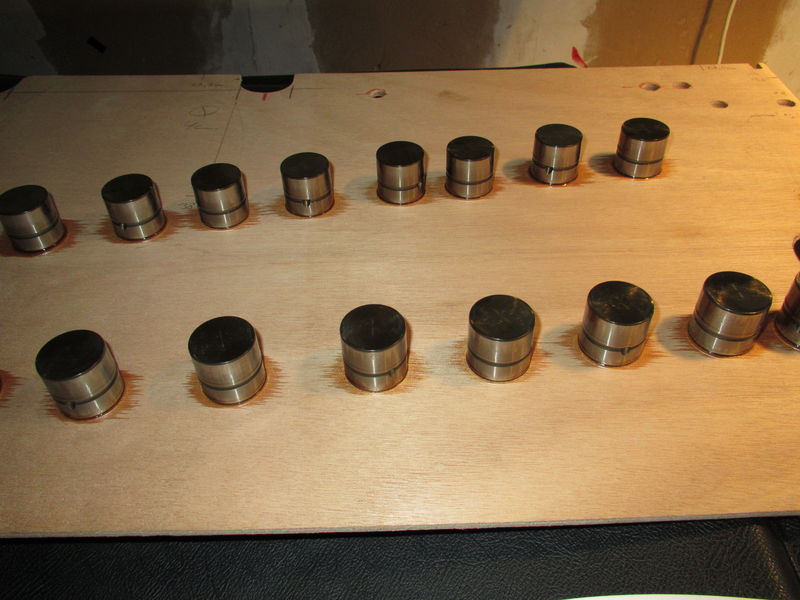
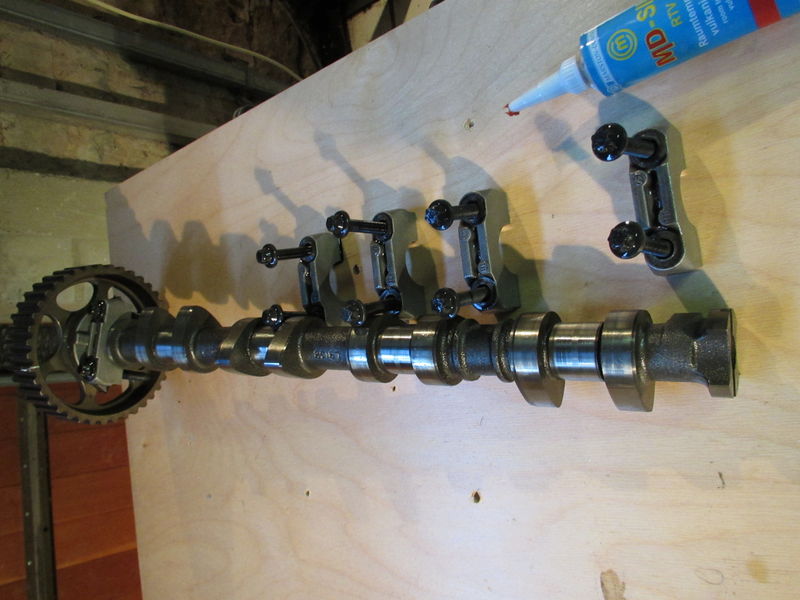