Erklärung zum Umbau:
Der hier beschriebene Umbau und die daraus resultierende Dokumentation stellt keine Bauanleitung oder Betriebsanweisung dar! Es ist mein Hobby, ich arbeite an meinem Fahrzeug und ich habe alle Arbeiten nach meinem Wissen und meiner Erfahrung ausgeführt. Für Fehler oder falsche Informationen auf dieser Seite kann ich keine Garantie erteilen oder haftbar gemacht werden.
11. MÄRZ 2021
Der neu lackierte Überrollbügel ist nun auch wieder eingebaut. Ich hatte den Überrollbügel am Montag lackiert und bis heute in der Lackier – Kabine zum Trocknen gelassen. Die elektrische Verkabelung der dritten Bremsleuchte wurde auch komplett erneuert sowie die Benzintank – Entlüftung, dessen Silikon – Schlauch durch den Überrollbügel von der linken Seite zur rechten Seite verläuft.
Das kleine Verdeck welches die Kofferraum – Wanne schließt bekommt an der Stelle, dort wo die beiden Streben durch das Verdeck gehen, einen kleinen Reißverschluss. Das Verdeck befindet sich zur Zeit beim Sattler um die beiden Reißverschlüsse einzunähen. Das kleine Verdeck kann dann nächste Woche auch wieder eingebaut werden. Das Tape, welches an der Stelle oft verwendet wird, wollte ich so nicht haben. Das sollte schon sauber aussehen.
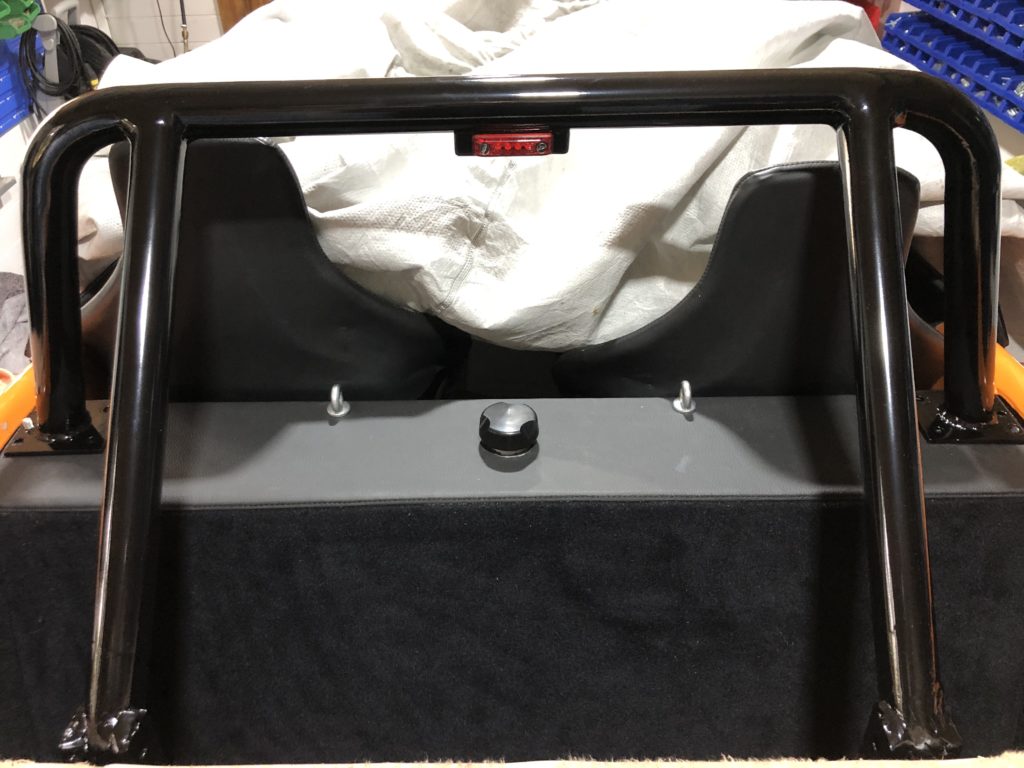
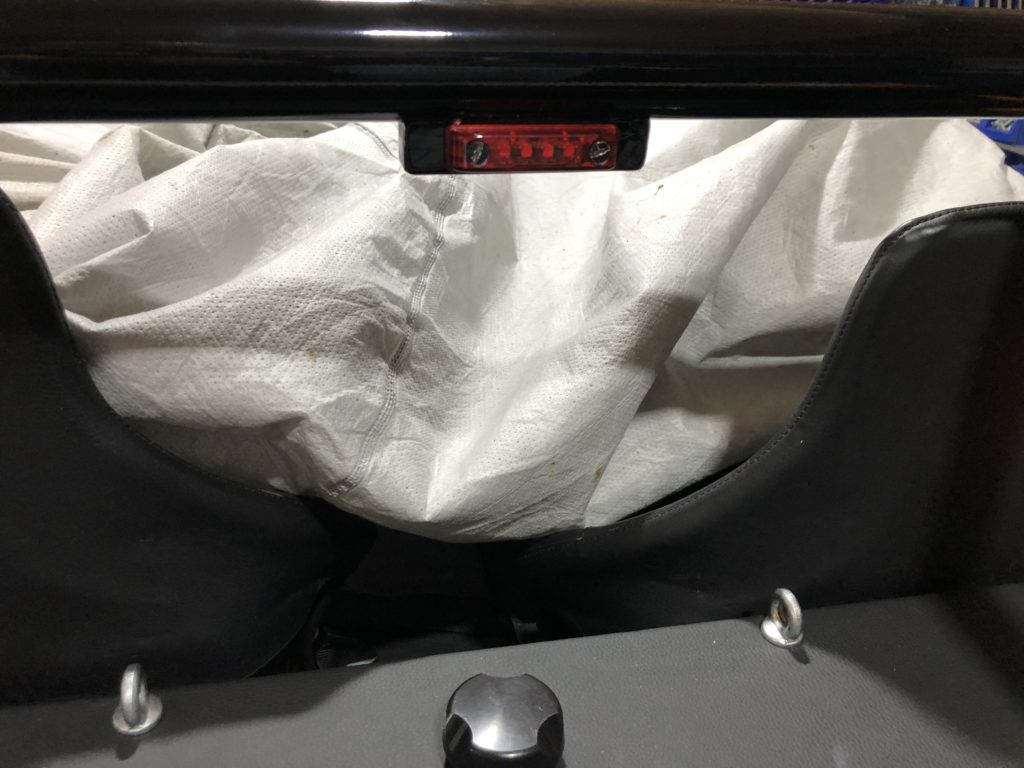
18. DEZEMBER 2020
Ich habe heute aber auch etwas getan was mich die letzten Jahre immer nervte wenn ich den HKT polierte. Ich habe die lästigen und hässlichen Aufkleber hinten am Heck links und rechts entfernt.
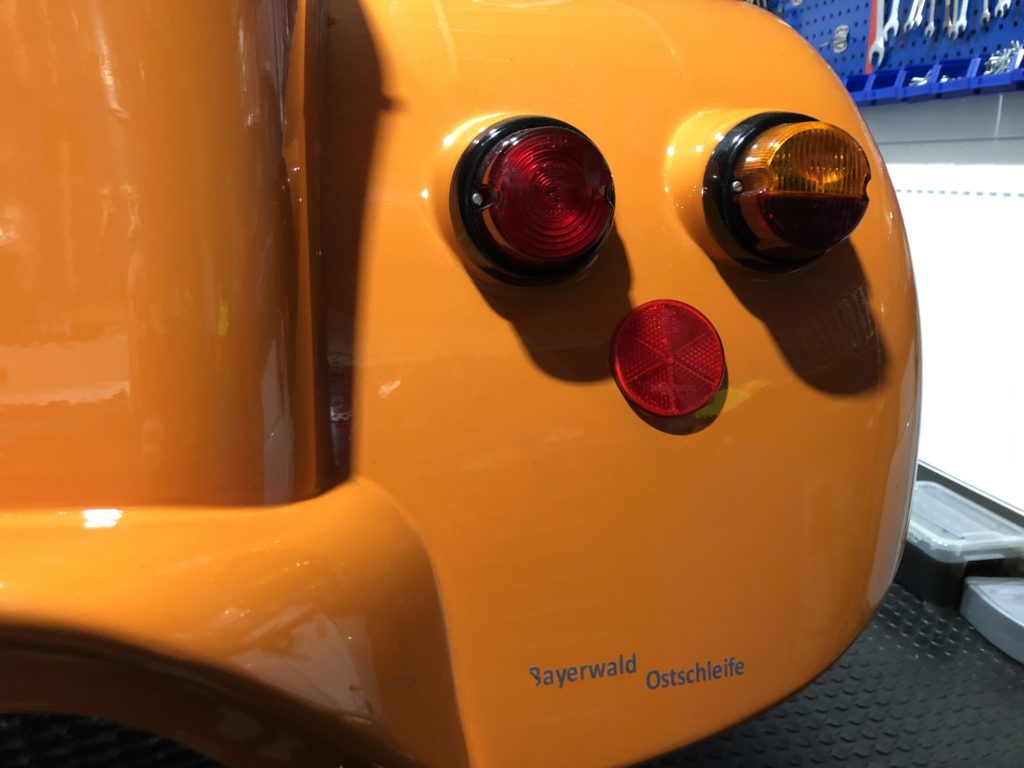
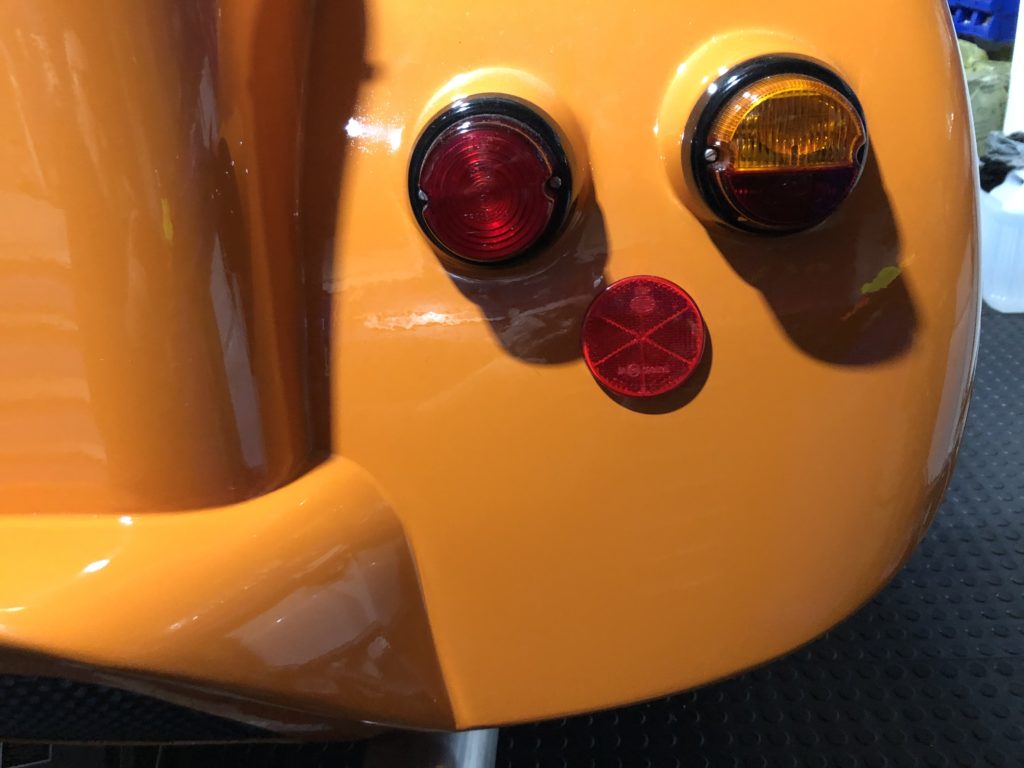
Ich hatte meinen Überrollbügel noch einmal ausgebaut, Der Grund war dass ich noch zwei Ankerpunkte am “ Kreuz “ anbringen wollte. Diese Ankerpunkte wurden am “ Kreuz “ verschweißt und verhindern später ein “ Wegknicken “ des Überrollbügels und erhöhen die Festigkeit bei einem Heckaufprall. Nach dem Schweißen musste der Überrollbügel dann wieder neu lackiert werden.
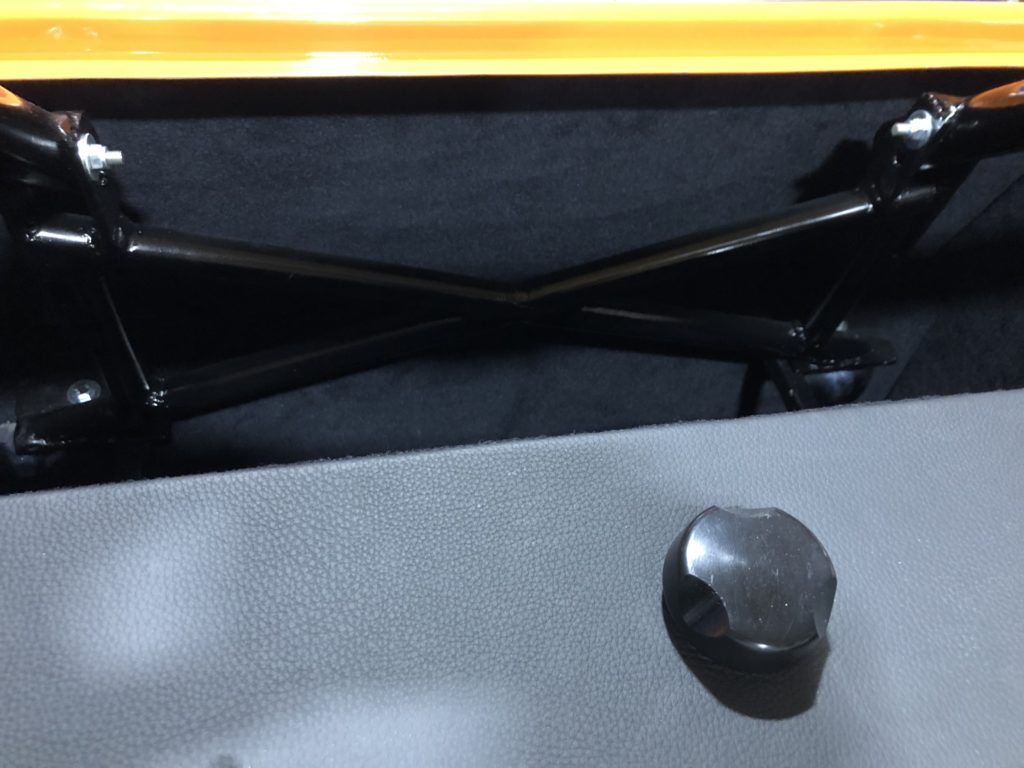
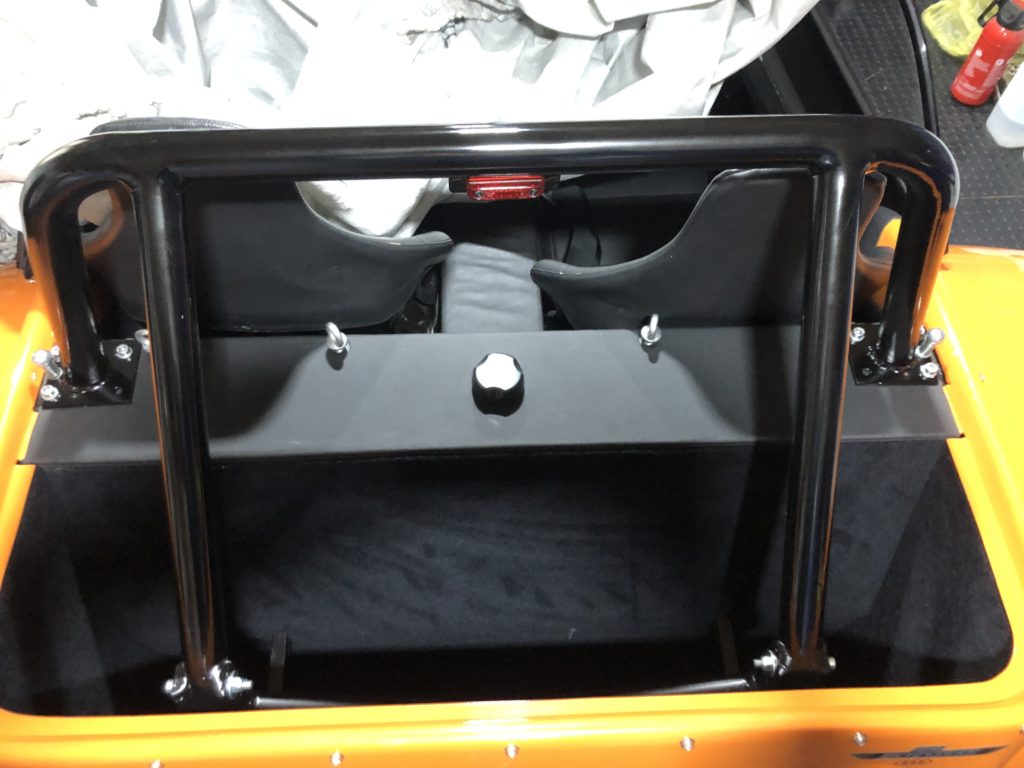
23. NOVEMBER 2020
Der Überrollbügel ist komplett, mit dem “ Kreuz “ eingebaut. Wie bereits vor einigen Tagen geschrieben, habe ich auf eine Spannungsfreie Montage aller Teile geachtet. Das setzt jedoch eine Passgenaue Anfertigung aller Komponenten, oder Teile, voraus. Die beiden M 8 x 70 mm Befestigungsschrauben, der beiden Streben die am “ Kreuz “ befestigt werden, wurden mit einem Drehmoment von 15 Nm angezogen. Die dritte Bremsleuchte ist nun auch elektrisch verkabelt und definitiv angeschlossen worden.
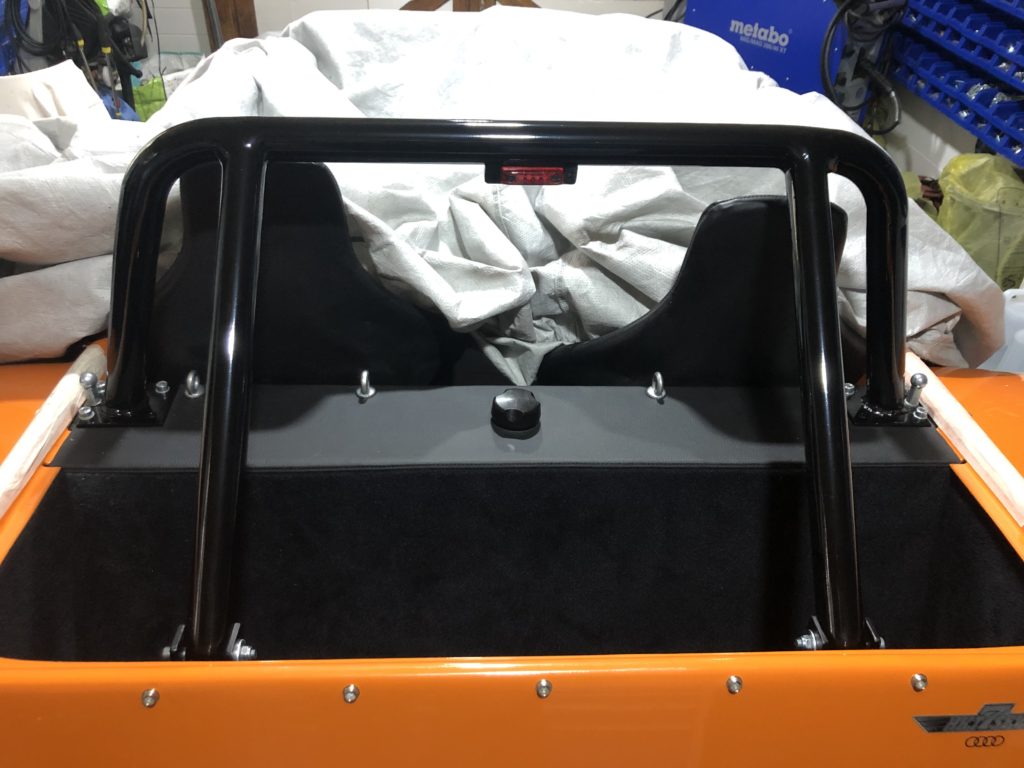
Hier erkennt man sehr gut wie und wo die beiden Streben befestigt werden.
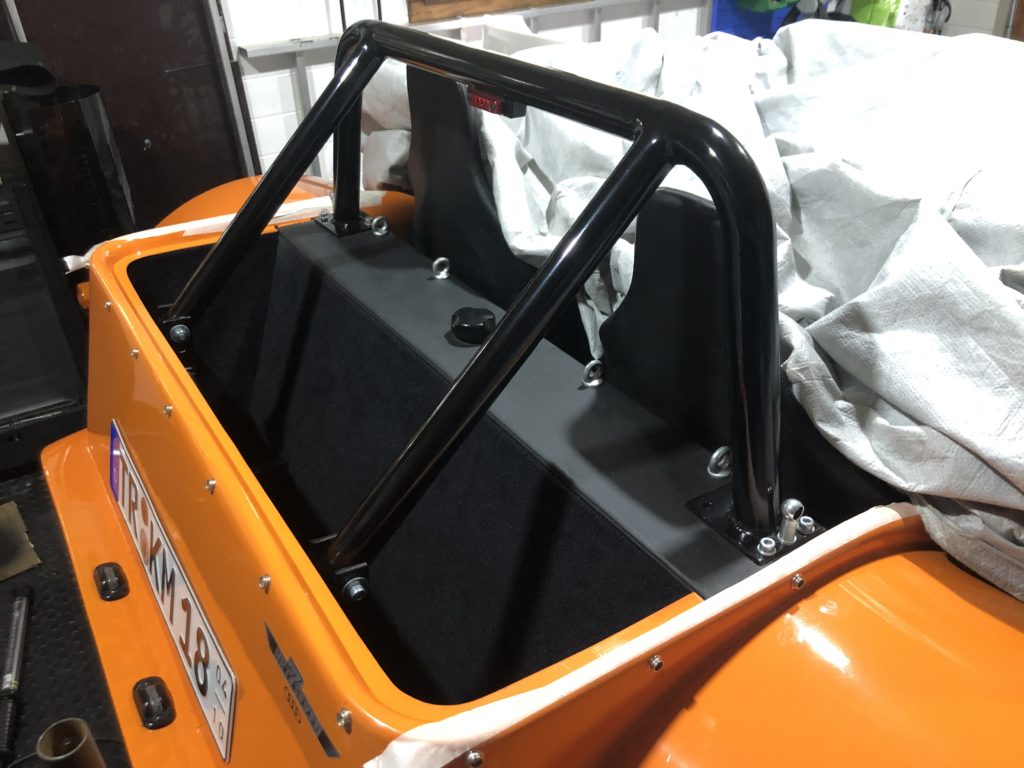
Die dritte Bremsleuchte, eine LED Leuchte von Hella, leuchtet sehr hell.
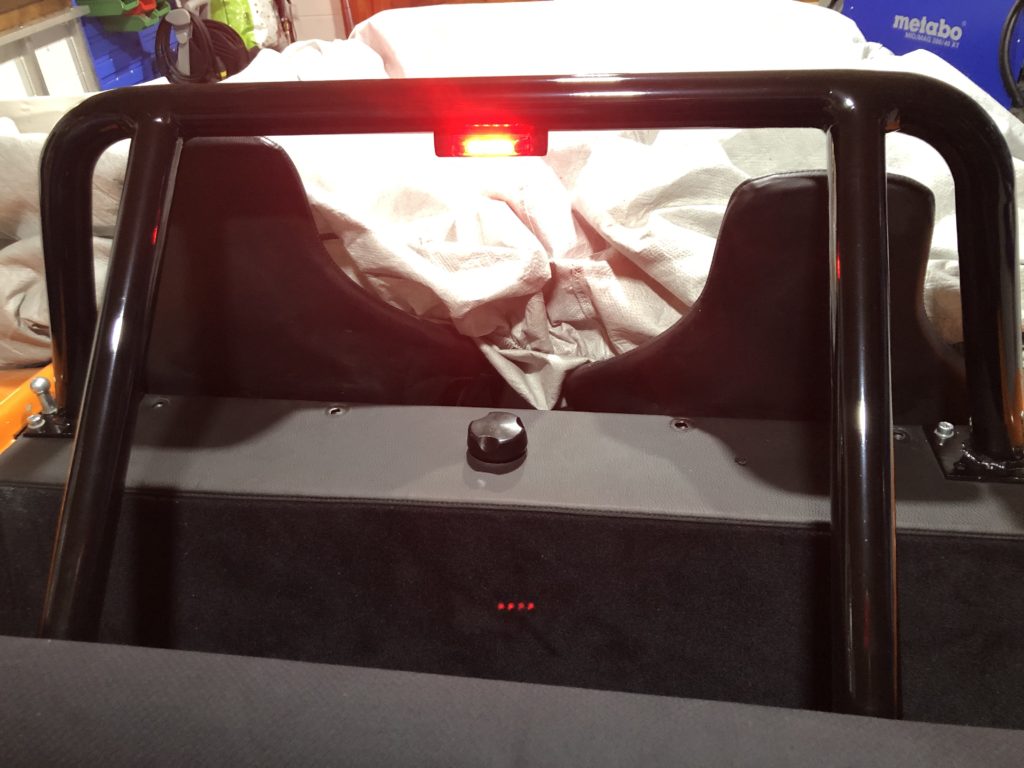
Die beiden Streben wurden am “ Kreuz “ mit 2 Innensechskantschrauben M 8 x 70 mm und mit einem Drehmoment von 15 Nm festgeschraubt.
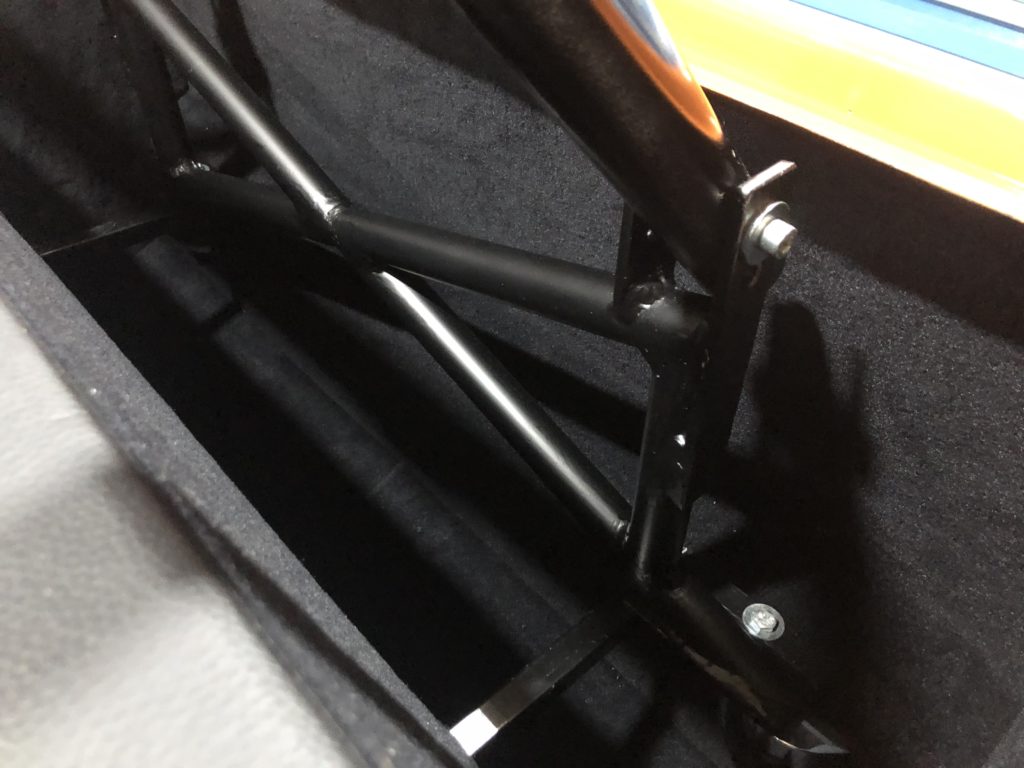
Beide Streben sind am “ Kreuz “ festgeschraubt. Das Kreuz wurde mit 2 M 8 x 35 mm Schrauben befestigt. Der Neigungswinkel des “ Kreuzes “ beträgt genau 22°.
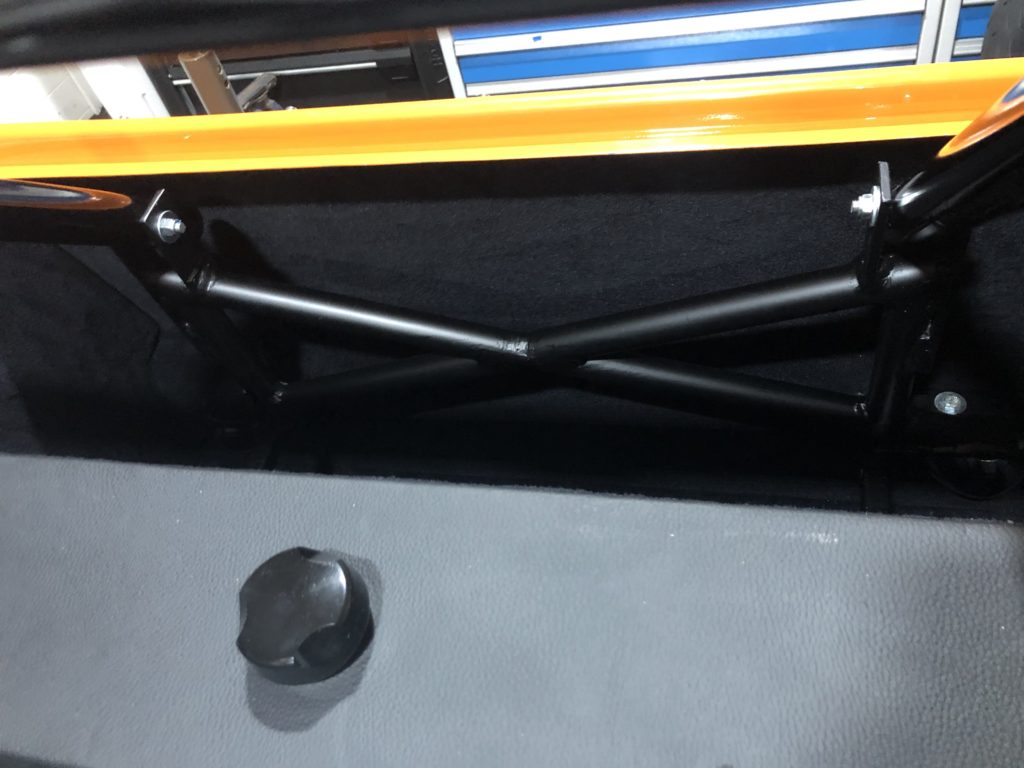
Der Überrollbügel ist montiert. Im Innern des Überrollbügels verläuft der Schlauch der Benzintank – Entlüftung und die Kabel der dritten Bremsleuchte.
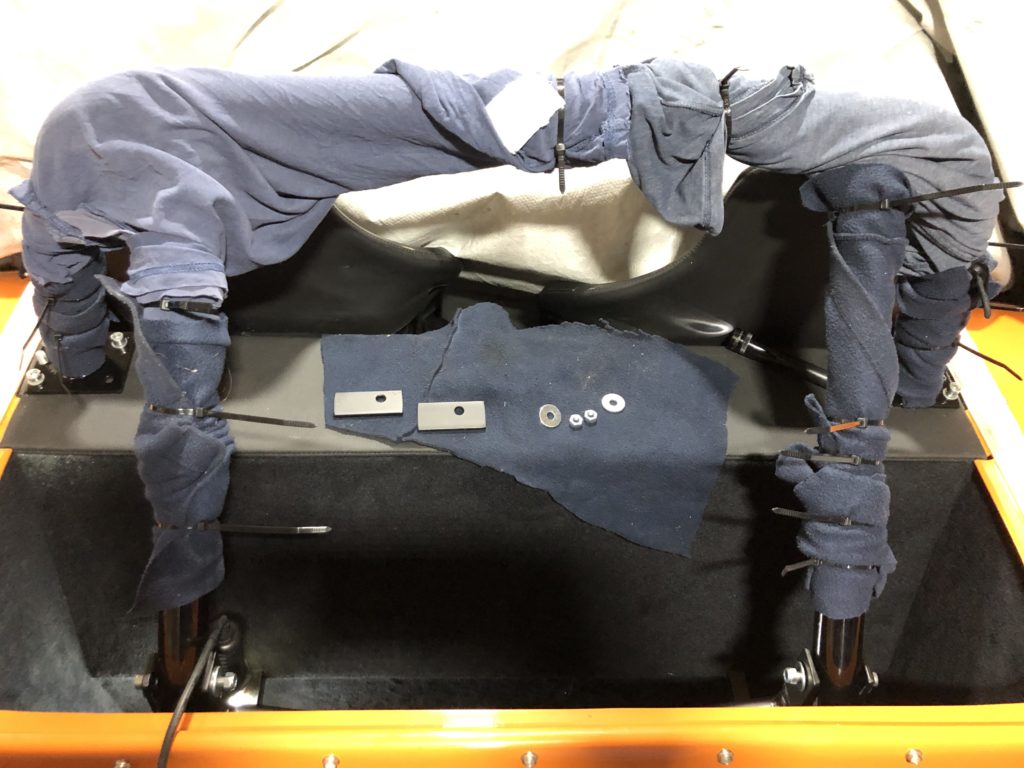
Ich habe Lappen um den Überrollbügel gewickelt um diesen vor Beschädigungen bei der Montage zu schützen.
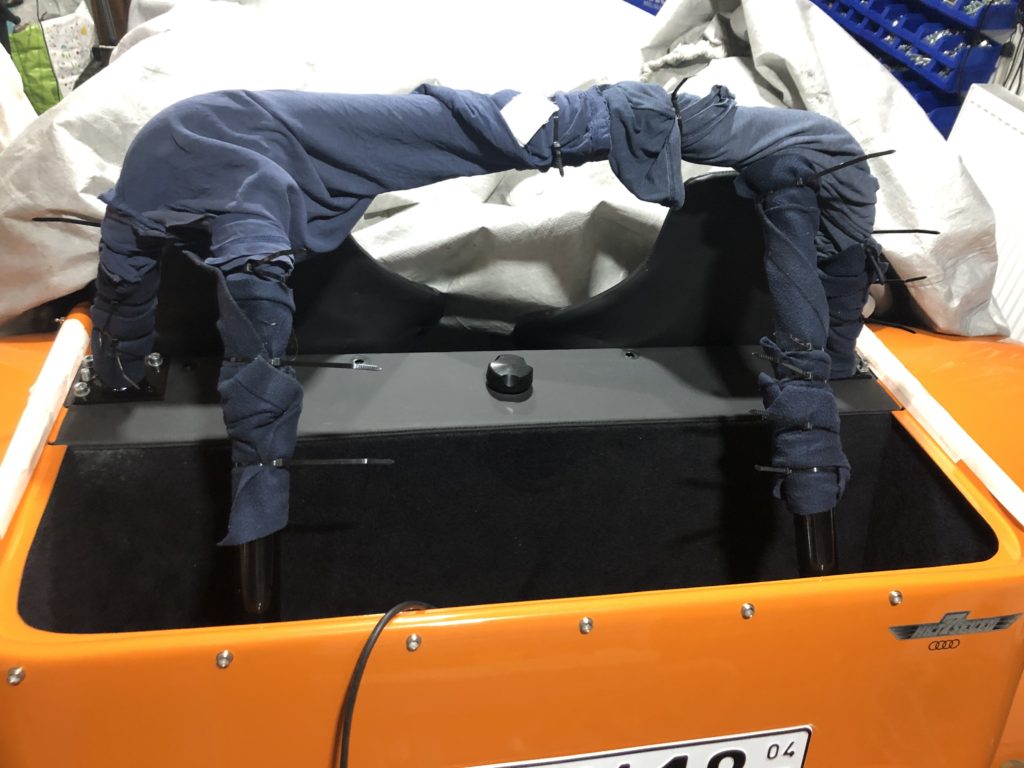
20. NOVEMBER 2020
Die dritte Bremsleuchte ist eingebaut und funktioniert sehr gut. Vor 2 Tagen wollte ich den schlauch der Benzintankentlüftung durch den Überrollbügel ziehen. Nach 2 Stunden gab ich es auf. Ich bekam den Schlauch einfach nicht mehr durch den Überrollbügel gefädelt. Ich hatte 2 Bohrungen von 40 mm in den Überrollbügel gefräst und die beiden Streben in diese Bohrungen gesteckt und festgeschweißt. Also war ich der Meinung, dass das der Grund sei, warum der Schlauch nicht mehr durch den Überrollbügel passte. Heute, nachdem ich die Bremsleuchte montiert hatte, habe ich erneut versucht den Schlauch durch den Überrollbügel zu ziehen. Und siehe da, beim ersten Versuch kam der Schlauch auf der anderen Seite des Überrollbügels wieder raus.
Die elektrischen Kabel für das dritte Bremslicht sind bereits bis zum Bremslicht auf der linken Seite verlegt worden. Dort wird das + Kabel der dritten Bremsleuchte angeschlossen.
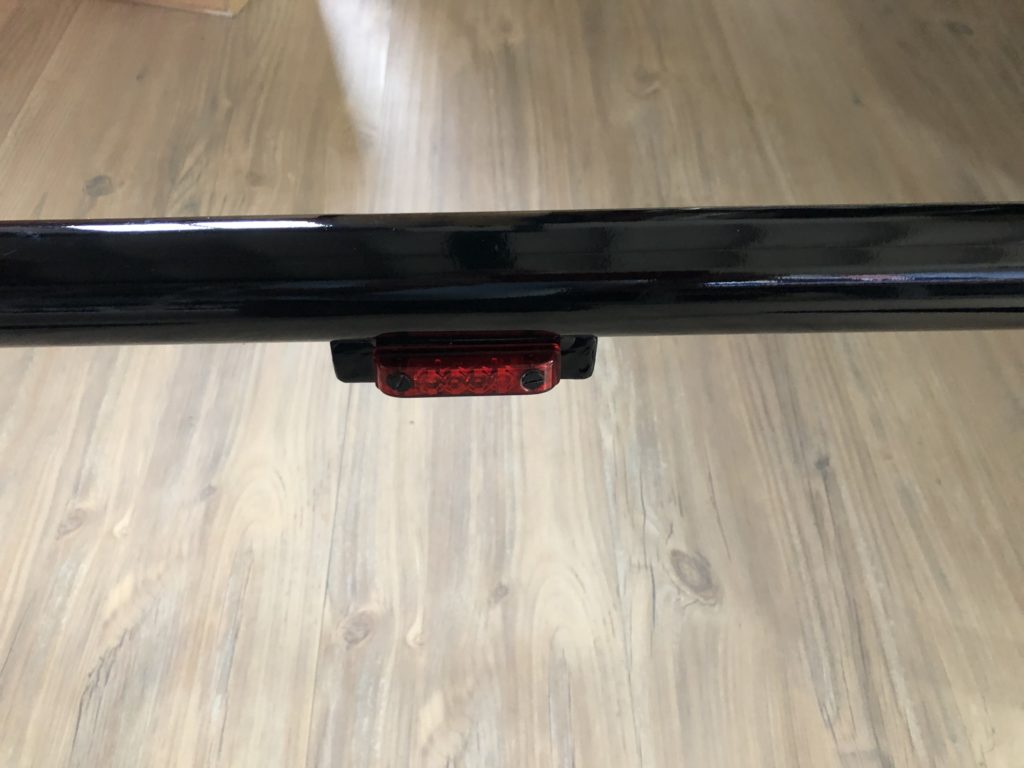
Der Teppich im Heckkasten ist nun endlich sorgfältig verlegt und auch anständig verklebt. Der gesamte Heckkasten ist gesäubert und die Verkleidung des Benzintankes ist auch wieder montiert. Gut zu sehen sind beide Benzintank – Entlüftungsschläuche, links und rechts. Der Benzintank – Entlüftungsschlauch, der durch den Überollbügel verläuft, wird am linken Schlauchstutzen angeschlossen, verläuft durch den Überrollbügel zur rechten Seite, wird dort an diesem Schlauchstutzen auf der rechten Seite Seite angeschlossen und endet in der Nähe des rechten Hinterrades. Siehe Beitrag: HKT Benzinanlage
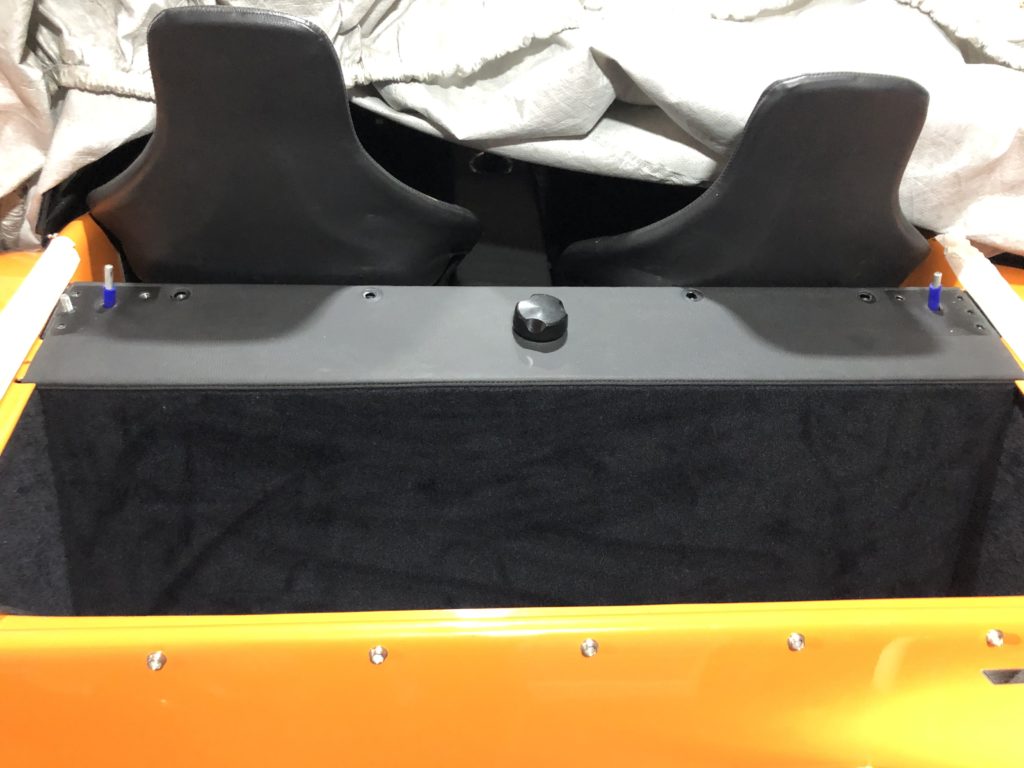
Hier erkennt man die Benzintank – Entlüftung die an den Benzintank – Entlüftungsschlauch, der durch den Überrollbügel verläuft, angeschlossen wird.
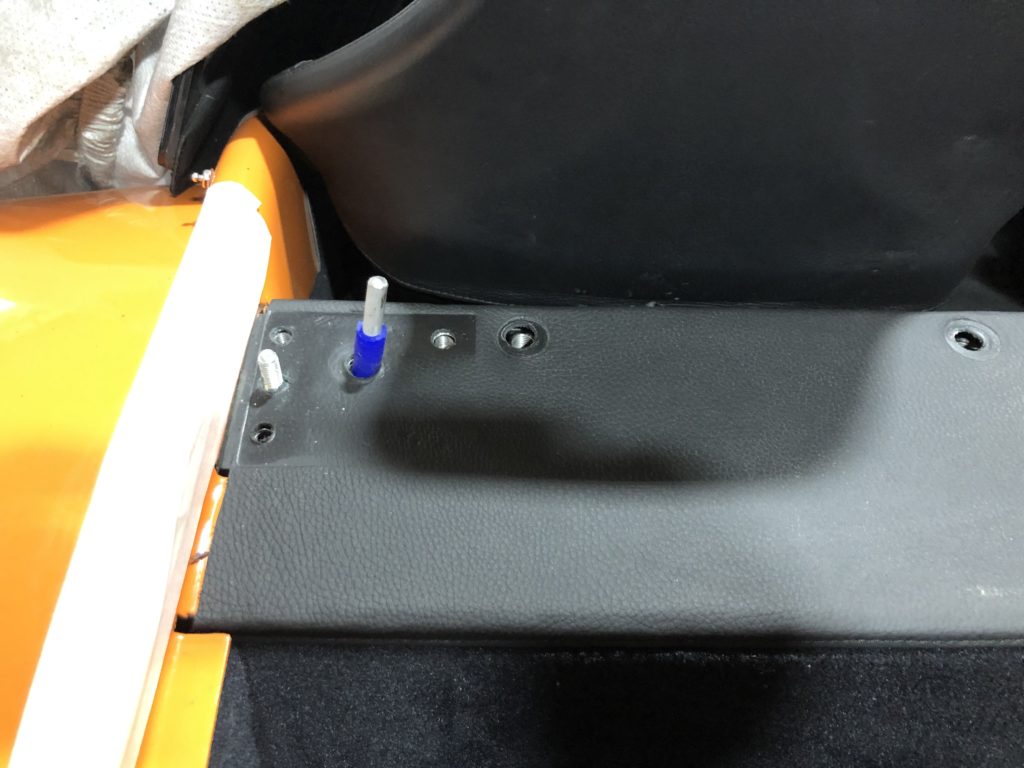
19. NOVEMBER 2020
Der Überrollbügel ist fertig. Ich habe diesen heute morgen lackiert. Vor dem eigentlichen Lackierauftrag habe ich noch eine Schicht Füllprimer aufgespritzt. Nach der Trocknung des Füllpromers habe ich alles mit 400er Sandpapier nass geschliffen, entfettet und anschließend schwarz lackiert.
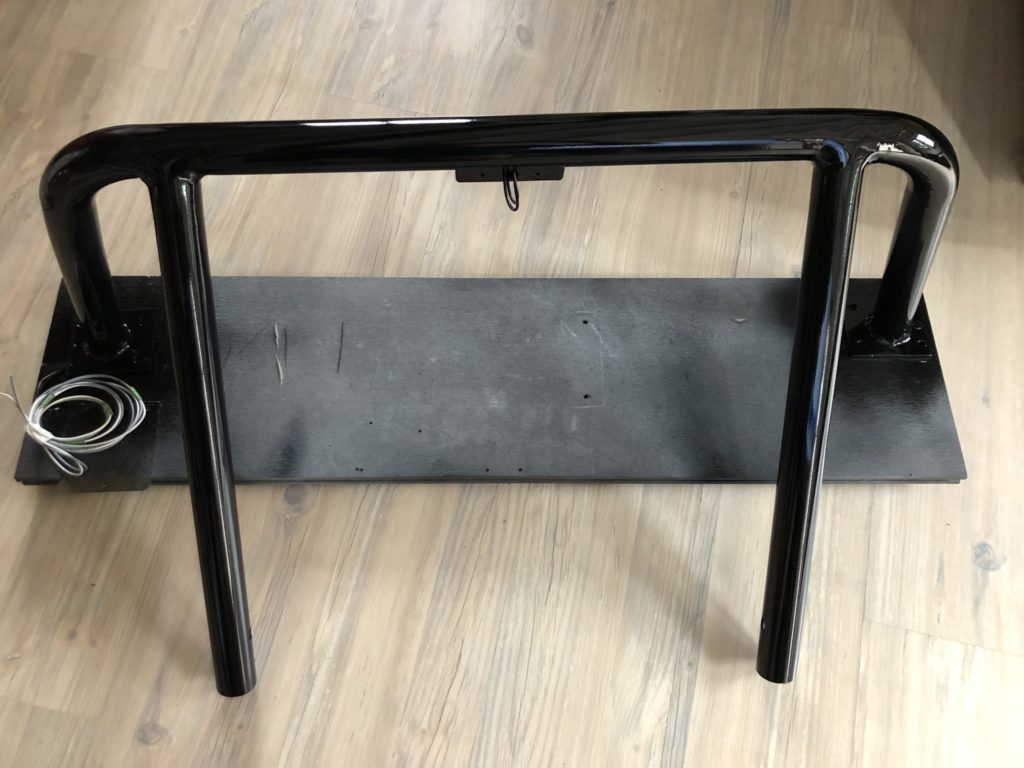
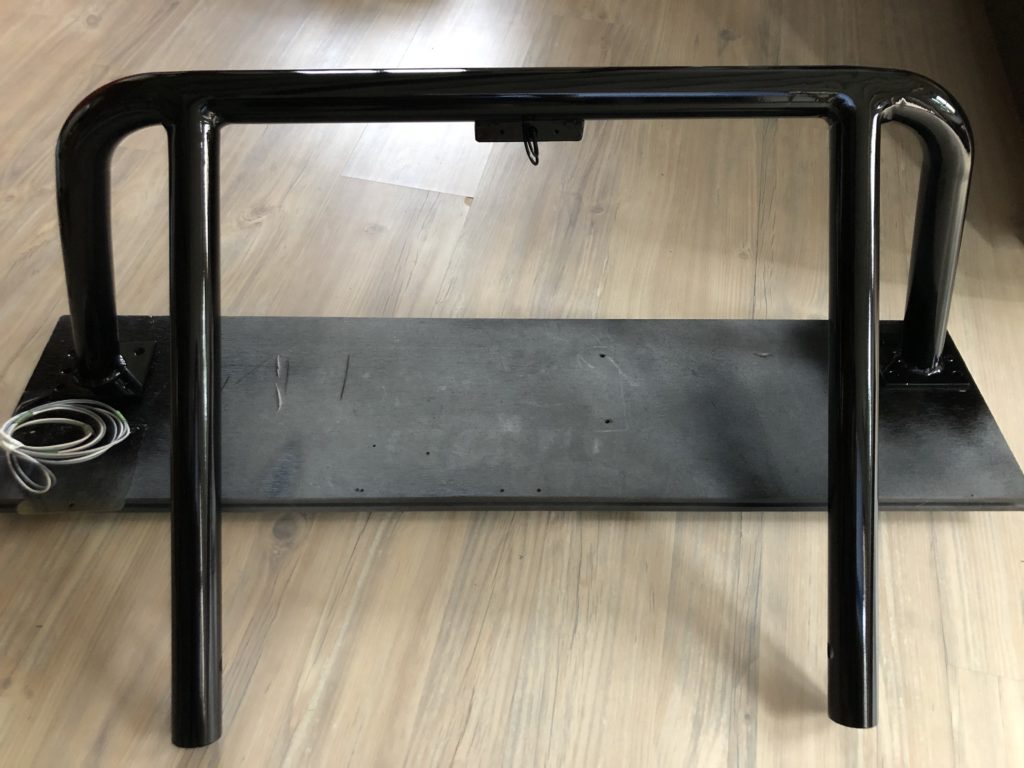
Hier wurde der U-Bügel mit einem Füllprimer lackiert und nach der Trocknung noch einmal mit 400er Sandpapier nass geschliffen.
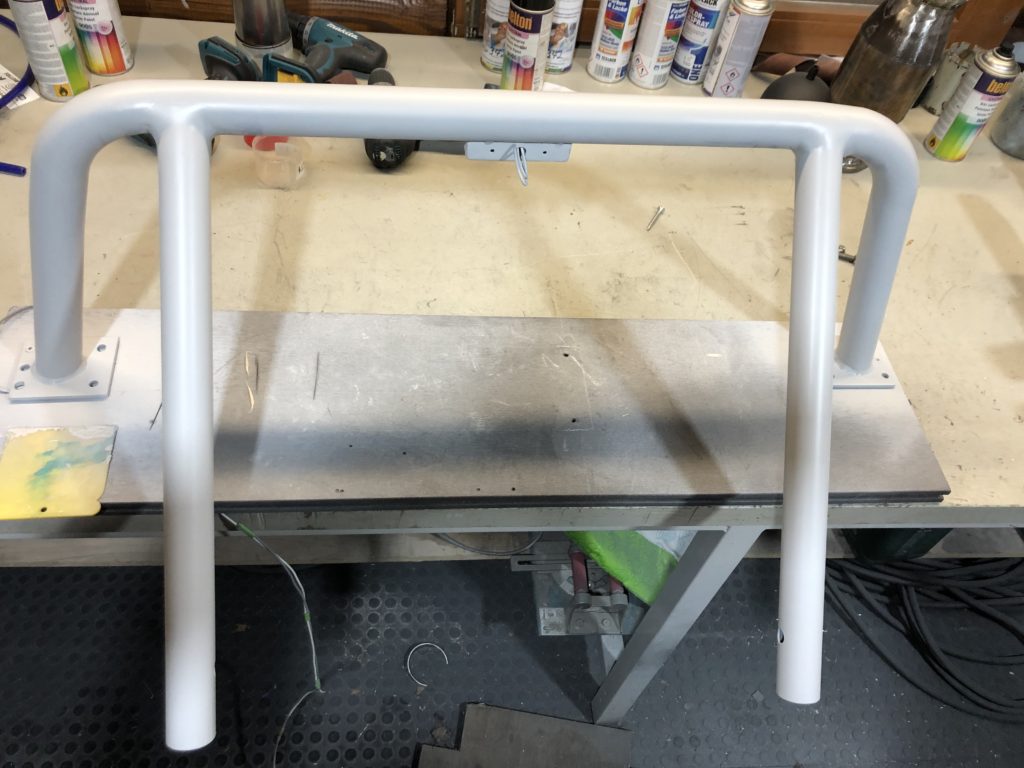
Der Teppich im Heckkasten hatte sich gelöst. Das sind die Dinge die mich einfach ärgern, weil es einfach sch…. aussieht und einen ungepflegten Eindruck hinterlassen. Ich habe den Teppich komplett gelöst, die Fläche sorgfältig gereinigt, mit Kleber eingestrichen, den Teppich wieder anständig verlegt und verklebt.
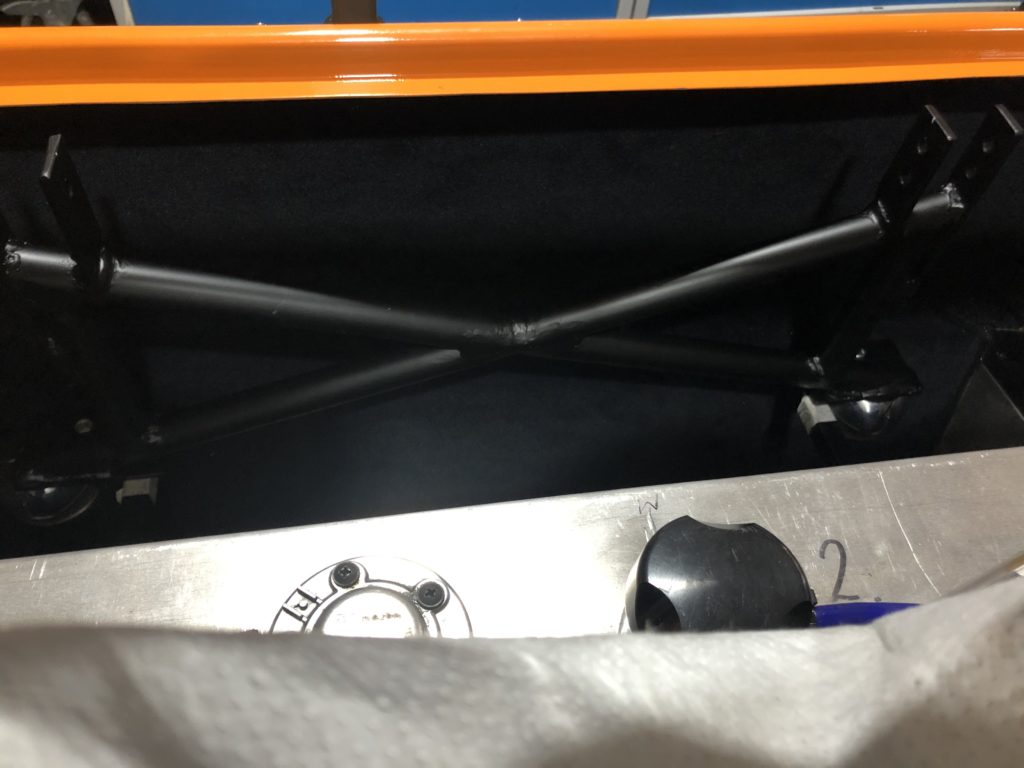
18. NOVEMBER 2020
Heute ging es weiter mit dem Verschweißen der Rohre. Der letzte Schweißvorgang von insgesamt 3 Schweißvorgängen habe ich heute erledigt. Ich habe mir aber auch einen Halter für die dritte Bremsleuchte, unterhalb des U – Bügels, angefertigt. Ich habe ein LED – Bremslicht von Hella ausgesucht. Die filigrane Konstruktion dieser Bremsleuchte gefiel mir und die Lichtstärke ist enorm. Das Bremslicht ist +/- 60 mm lang und 15 mm breit . Ich hatte jedoch 2 LED – Bremslichter von Hella zur Auswahl. ( siehe erstes Foto oben ) Gewählt habe ich, wie bereits geschrieben, das linke kleinere Bremslicht. Die elektrischen Kabel habe ich im Innern U – Bügel verlegt.
Da mir meine Freundin im Tiguan, im letzten Sommer in Oberhausen, fast ins Heck des HKT geknallt ist, war mir klar dass ich eine dritte Bremsleuchte haben wollte. Sie hatte mich an der roten Ampel, weil Sie im Tiguan viel höher sitzt, schlicht und einfach übersehen.
Ich habe nach dem Schweißen den U – Bügel und das “ Kreuz “ ein weiteres Mal im HKT eingebaut. Ich wollte sicher gehen dass sich nichts, auf Grund der Hitze beim Schweißen, verzogen hatte. Mir war wichtig dass alle Teile ohne Spannungen passen. Jede Schraube, jeder Bolzen muss leichtgängig, ohne Hammerschläge, in die dafür vorgesehenen Bohrungen passen. Da ist schon sorgfältiges Arbeiten notwendig und ich wollte mir ausreichend Zeit nehmen die Teile anzufertigen.
Anschließend, nach dem “ Probe-Einbau “ aller Teile im HKT, wurde der Überroll – Bügel sehr sorgfältig geschliffen und bei einer Profi – Schweißfirma auf Risse überprüft. Ich wollte 100% sicher sein dass meine Schweißnähte in Ordnung sind. Es ist ja schließlich ein Überrollbügel der im Falle eines Überschlages halten muss! Die Schweißnähte waren alle in Ordnung, weitere zusätzliche Schweißvorgänge waren nicht mehr notwendig. Nach dieser Prüfung habe ich dann alles nochmals mit 400 er Sandpapier sorgfältig geschliffen und grundiert.
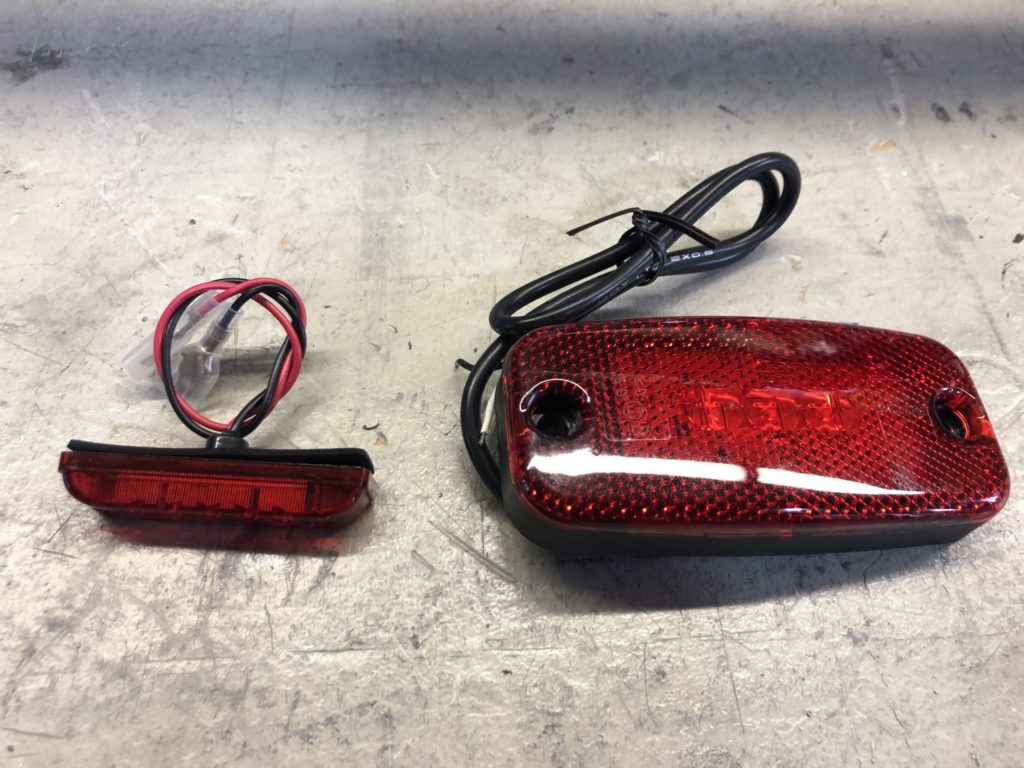
Hier auf diesem Foto ist der U – Bügel nach dem ersten Schweißvorgang zu sehen. Nach jedem Schweißvorgang wurde alles provisorisch geschliffen.
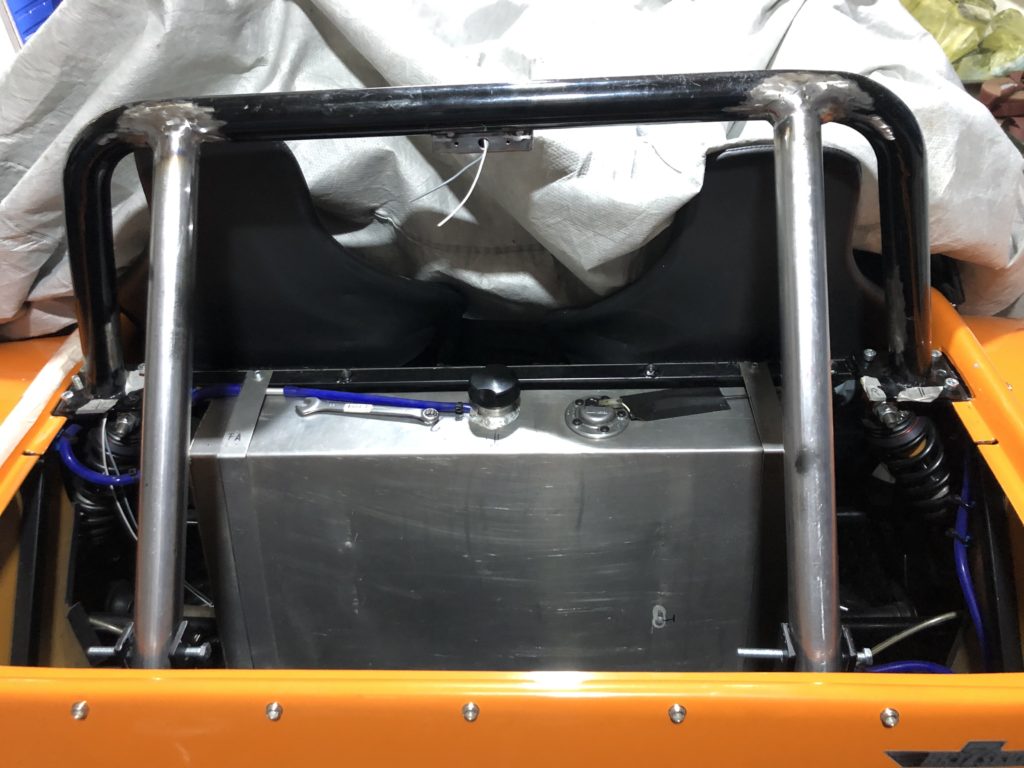
Hier wurde bereits der zweite Schweißvorgang vorgenommen.
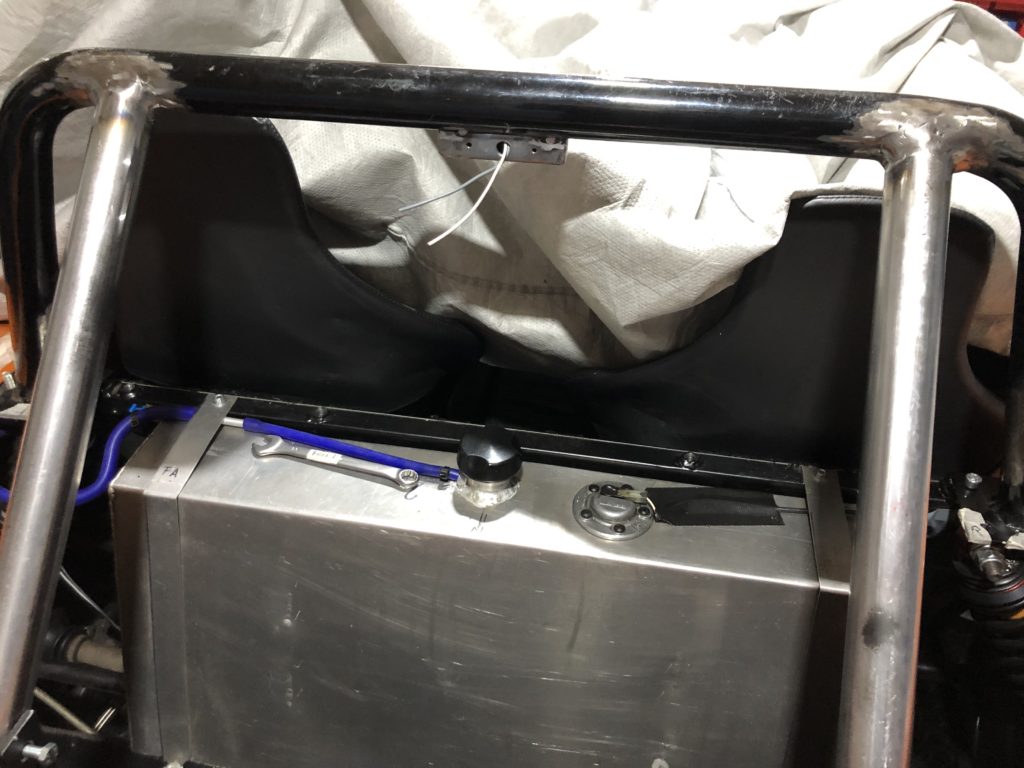
Hier sieht man meinen Sockel für die dritte Bremsleuchte unterhalb des U – Bügels.
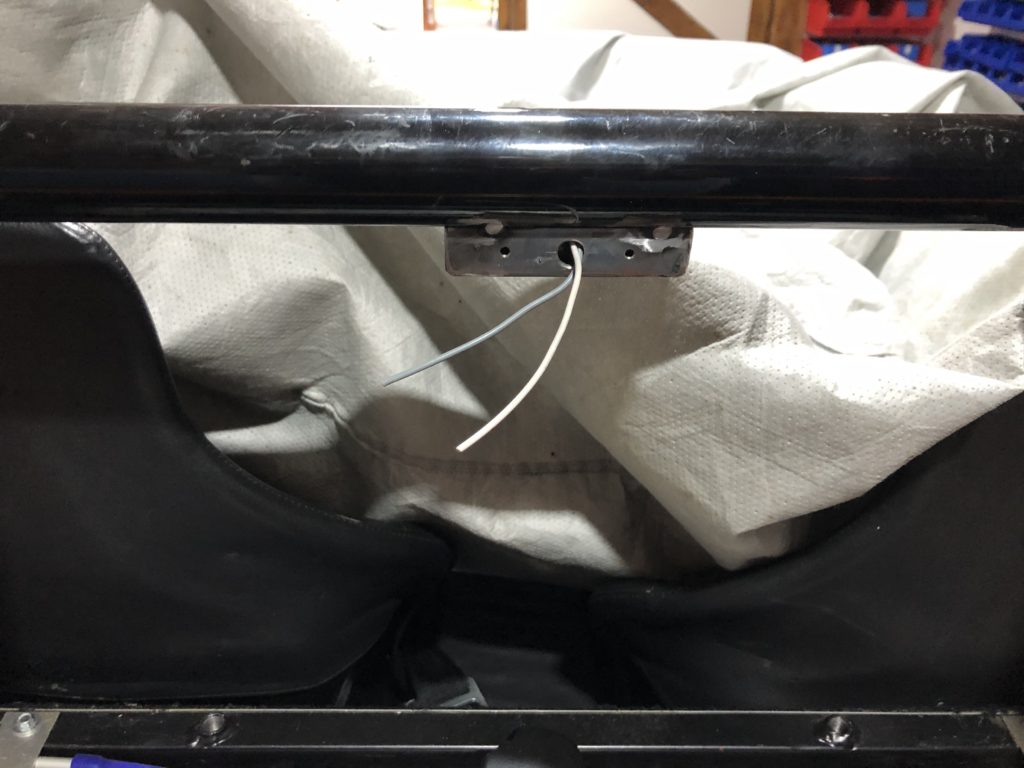
Der U – Bügel ist sauber geschliffen und konnte anschließend grundiert werden.
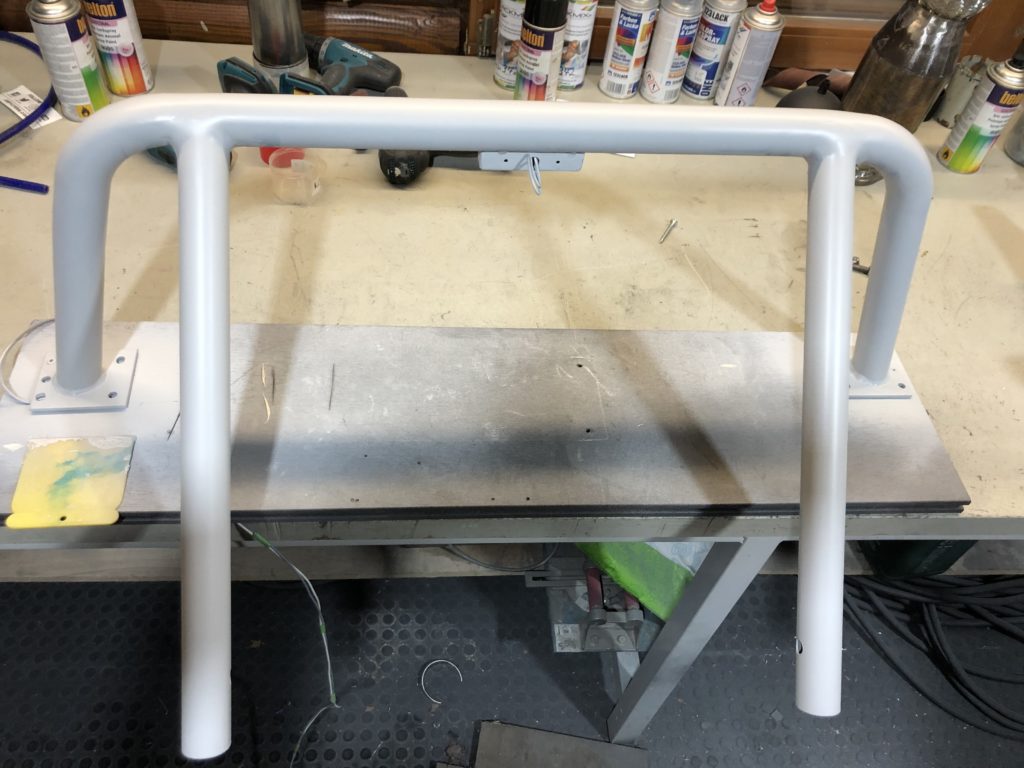
17. NOVEMBER 2020
Die Streben die zum Kreuz führen sind befestigt worden. Da ich auf keinen Fall bei eingebautem U – Bügel im HKT an diesem schweißen wollte, musste eine andere Lösung her. Ich habe mir eine Lehre, ein Flacheisen, am U-Bügel provisorisch angeschweißt. An beiden Streben habe ich auch ein Flacheisen angeschweißt und anschließend das Ganze im eingebauten Zustand mit M 8 Schrauben, mit dem Flacheisen am U-Bügel verschraubt. So konnte ich das Ganze zusammen bauen und nach dem Verschrauben entfernen um dieses dann in der Werkstatt zu schweißen.
Auf diesem Foto sieht man die erste Strebe die dann später am Kreuz befestigt wird.
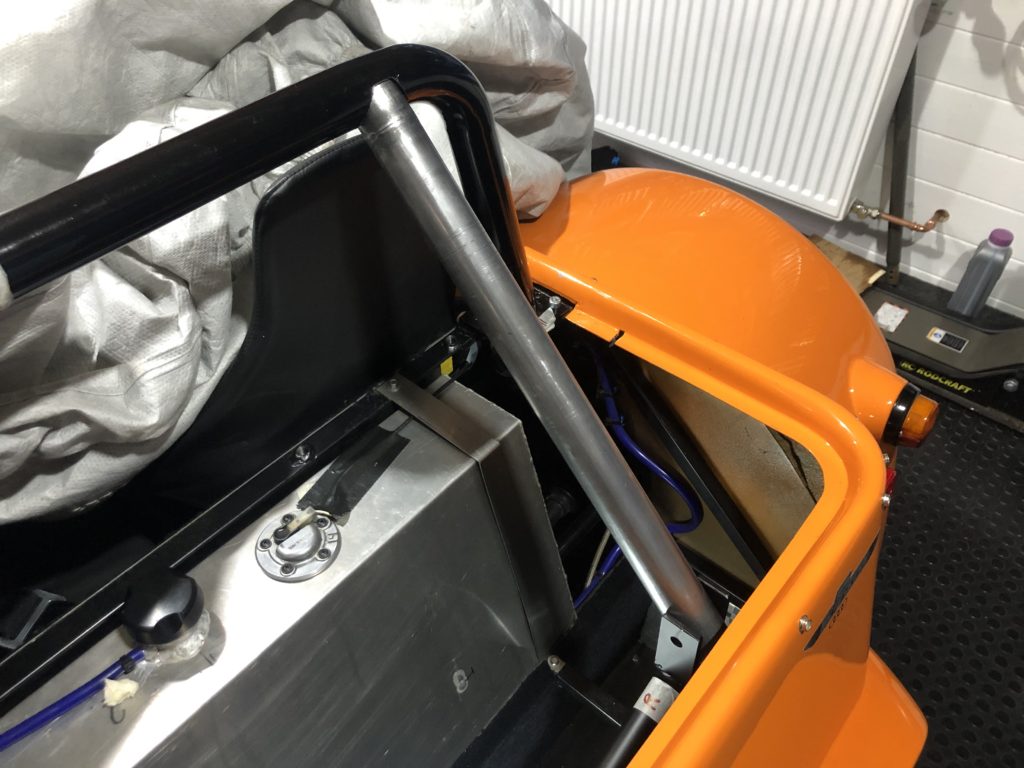
Die Strebe wird mit dem Kreuz verschraubt und mit dem angeschweißten Flacheisen mit dem U-Bügel verbunden.
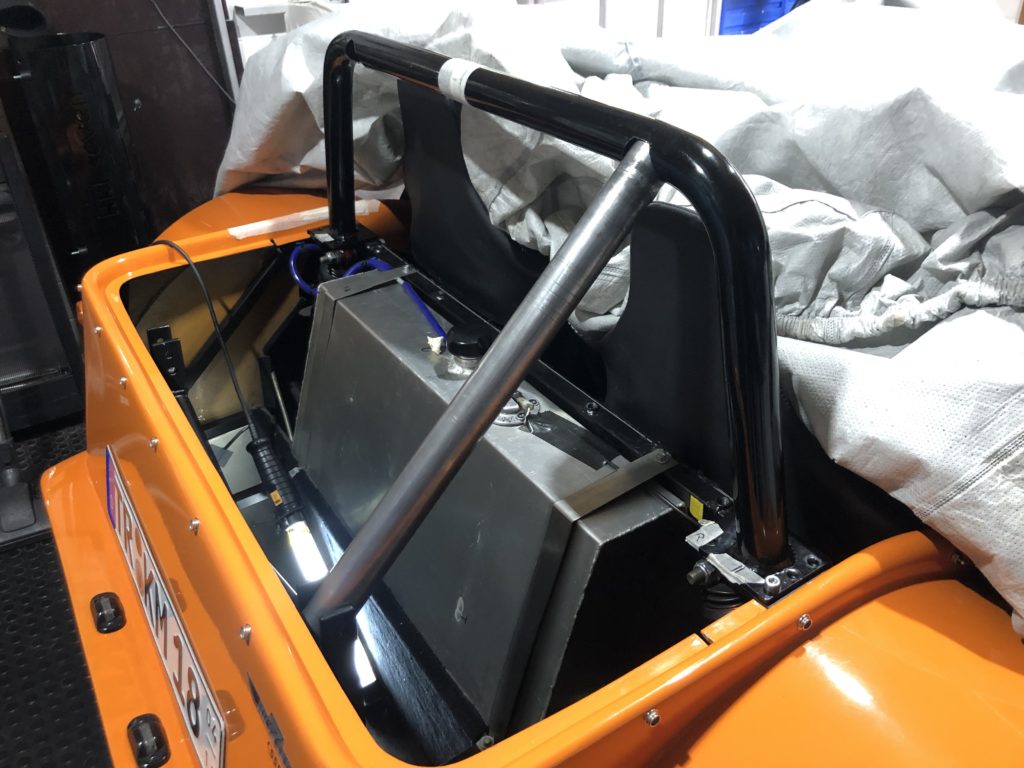
Hier erkennt man das Flacheisen am U-Bügel welches an beiden Seiten des U-Bügels provisorisch angeschweißt wurde. An diesem Flacheisen wurden zwei weitere kleinere Flacheisen angeschweißt. An diesen werden die beiden Streben links und rechts befestigt.
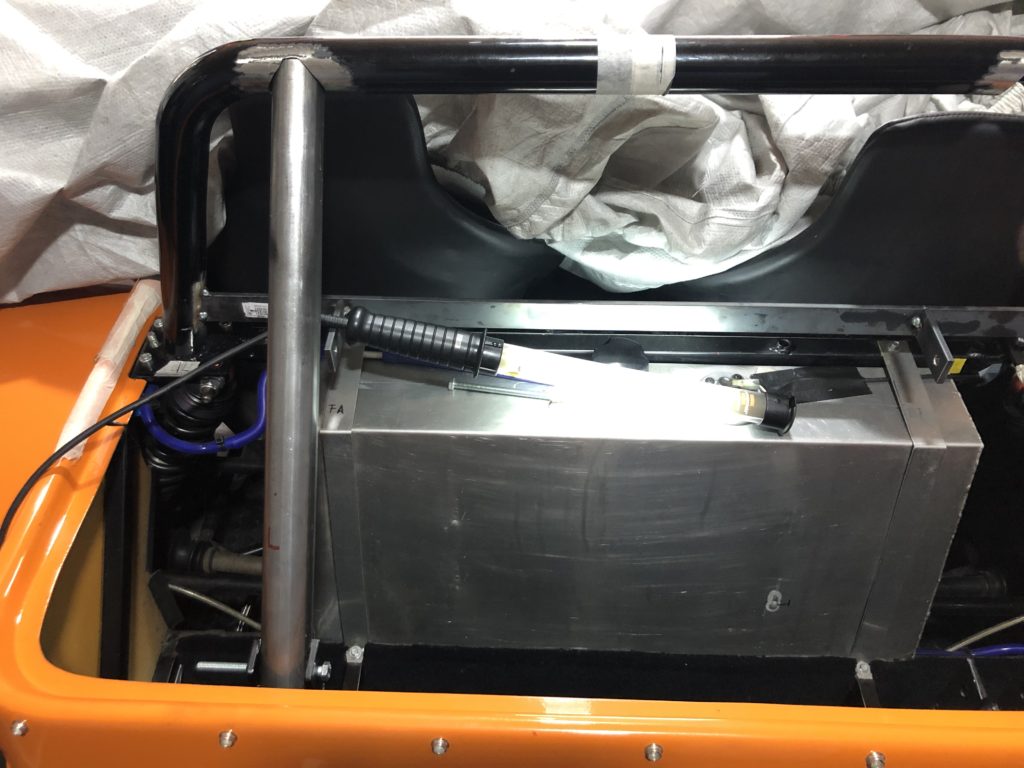
Auf diesem Foto ist das Flacheisen am U-Bügel deutlich zu sehen. Dort sind auch die beiden kleineren Flacheisen, mit denen die Streben verschraubt werden können, zu sehen.
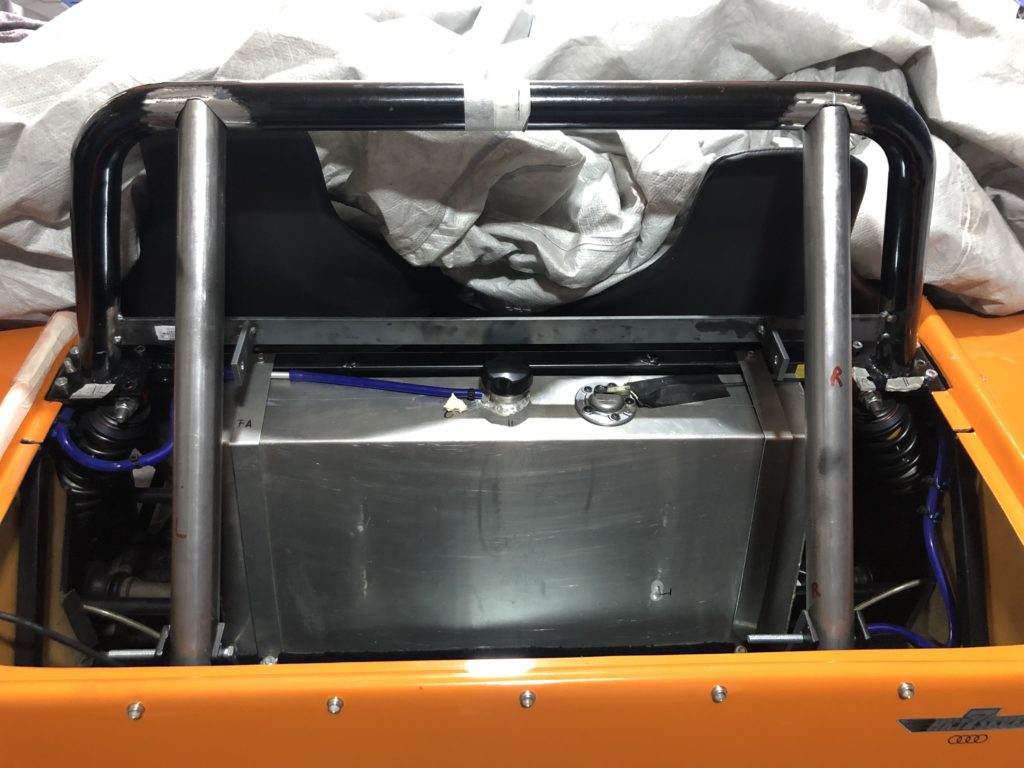
Beide Streben sind provisorisch montiert und können nun verschraubt werden.
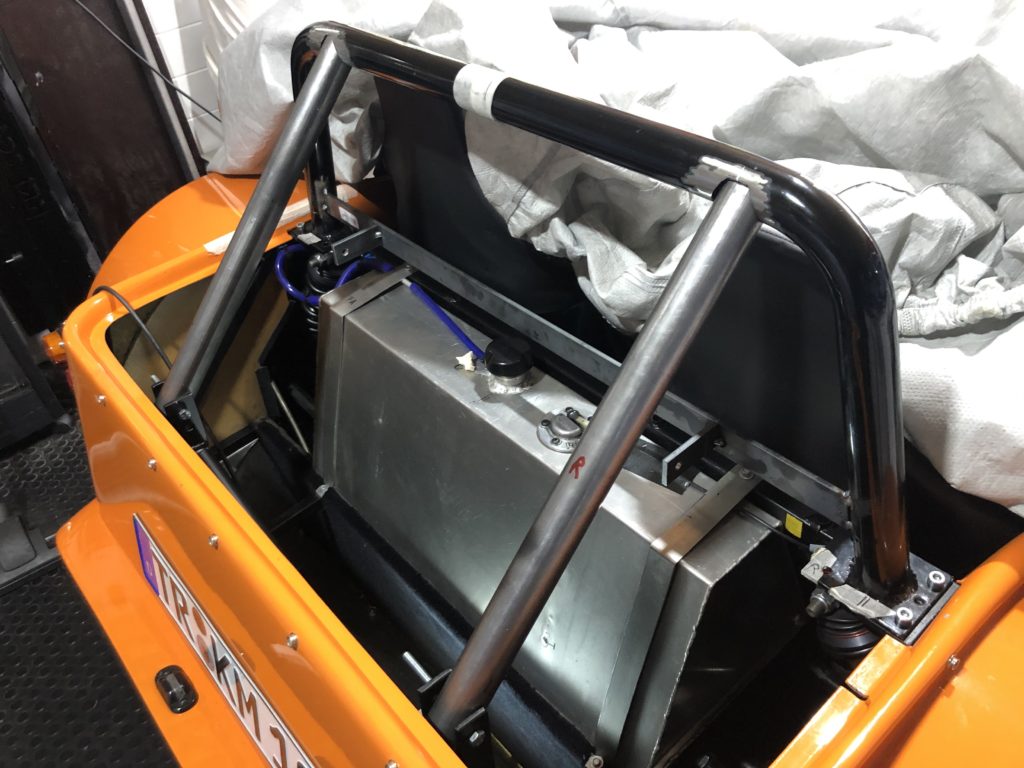
Auf diesem Foto erkennt man die Befestigung der Strebe mit dem Flacheisen des U-Bügels deutlich. An der Strebe ist auch ein Flacheisen befestigt, welches mit dem Flacheisen am U-Bügel, verschraubt wird.
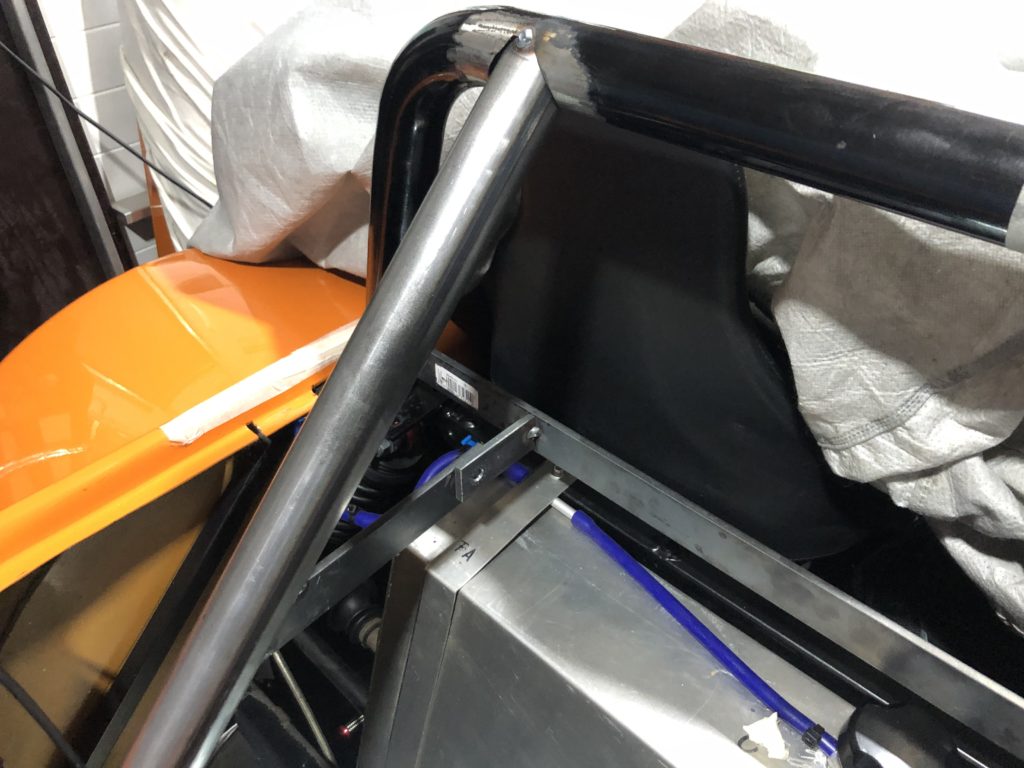
Nachdem alles verschraubt war, wurde das Ganze komplett ausgebaut und in der Werkstatt provisorisch gepunktet. Das Anbringen der Lehre mit den Flacheisen war eine deutliche Mehrarbeit, aber es ermöglichte mir, den genauen Winkel der beiden Streben, im eingebauten Zustand festzulegen um das Ganze dann außerhalb des HKT zu schweißen.
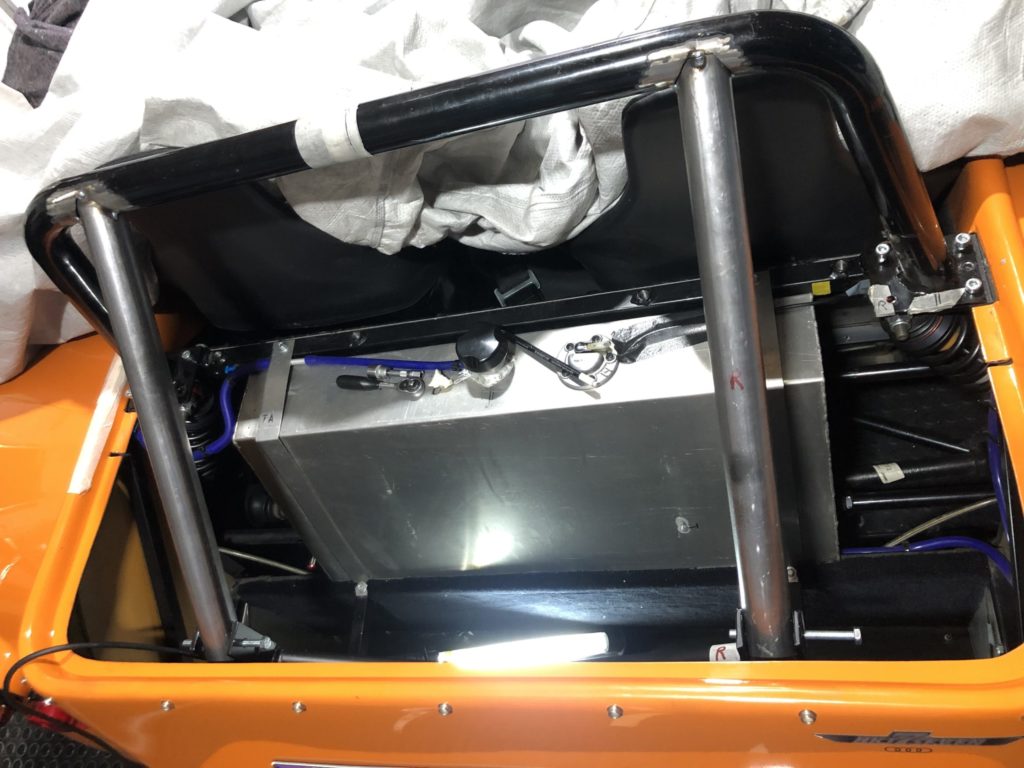
14. NOVEMBER 2020
Es geht weiter mit dem Umbau des Überrollbügels. Der Überrollbügel macht, ohne Abstützung zum Heck, nicht wirklich Sinn. Die Aufnahmepunkte des Überrollbügels am HKT Rahmen sind schwach ausgelegt. Der Überrollbügel wird an einem “ L “ befestigt. Der eine Schenkel des “ L “ hat eine Breite von 25 mm Breite und der andere Schenkel ist etwas breiter, 35 mm. Eine grössere Aufnahmefläche am Rahmen, für den Flansch des Überrollbügels, wäre durchaus sinnvoll gewesen. Das Ganze wäre am nackten Rahmen schnell erledigt gewesen. Man hätte einfach eine Stahlplatte von 10 x 10 x 0,5 cm mit einer Bohrung von 30 mm , für das Stossdämpferauge, oben am Rahmen, da wo jetzt der Überrollbügel befestigt wird, anschweißen können. Bei einem Überschlag wird dieser, ohne Abstützung, einfach wegknicken. Das Wegknicken des Überrollbügels aber auch einen Überschlag möchte ich auf jeden Fall verhindern. Aber sollte es passieren, dann möchte ich dass der Überrollbügel die Kräfte die entstehen können, aufnehmen kann, ohne dass dieser wegknickt. Da ich auf jeden Fall Schweißarbeiten am Rahmen vermeiden will, muss eine andere Lösung her.
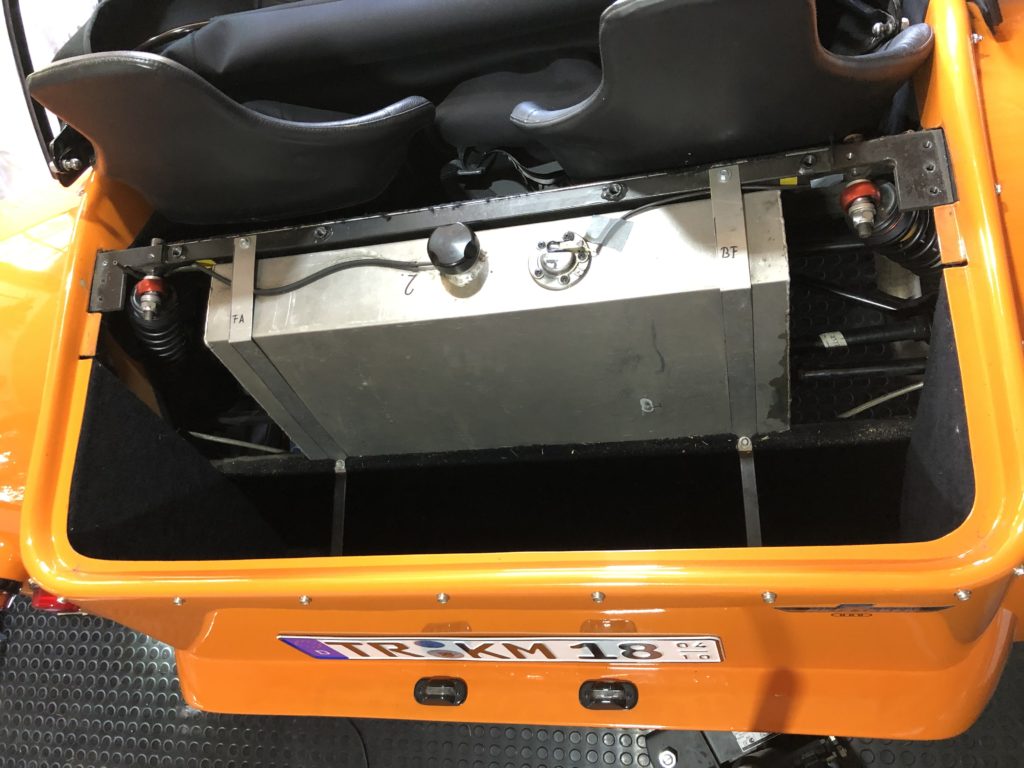
Hier erkennt man die zu schmale Auflagefläche für den Überrollbügel sehr gut.
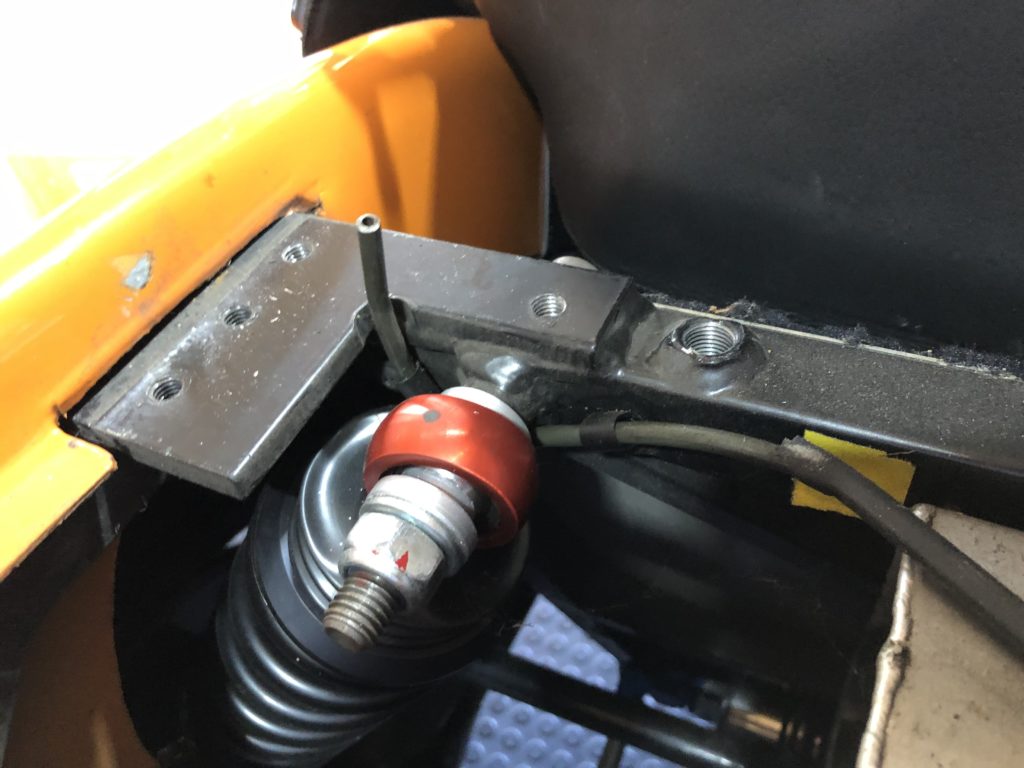
Die letzten Tage habe ich mit dem Zuschneiden der Rohre und mit dem Verschweißen der Rohre verbracht. Es war eine Menge Arbeit das erste Teil, ich nenne es “ Kreuz „, herzustellen. Das “ Kreuz “ wurde heute im HKT eingebaut und ausgerichtet. Das “ Kreuz “ steht nicht in einem Winkel von 90° zum Rahmen. Ich habe bewusst einen bestimmten Neigungswinkel gewählt. So werden die Kräfte, die im Unglücksfall auftreten können, an der Konstruktion gleichmäßig aufgeteilt und zu beiden Seiten hin verteilt. Ich will verhindern dass an der Rahmenbefestigung, links und rechts, eine zu hohe Punktlast am Rahmen auftritt.
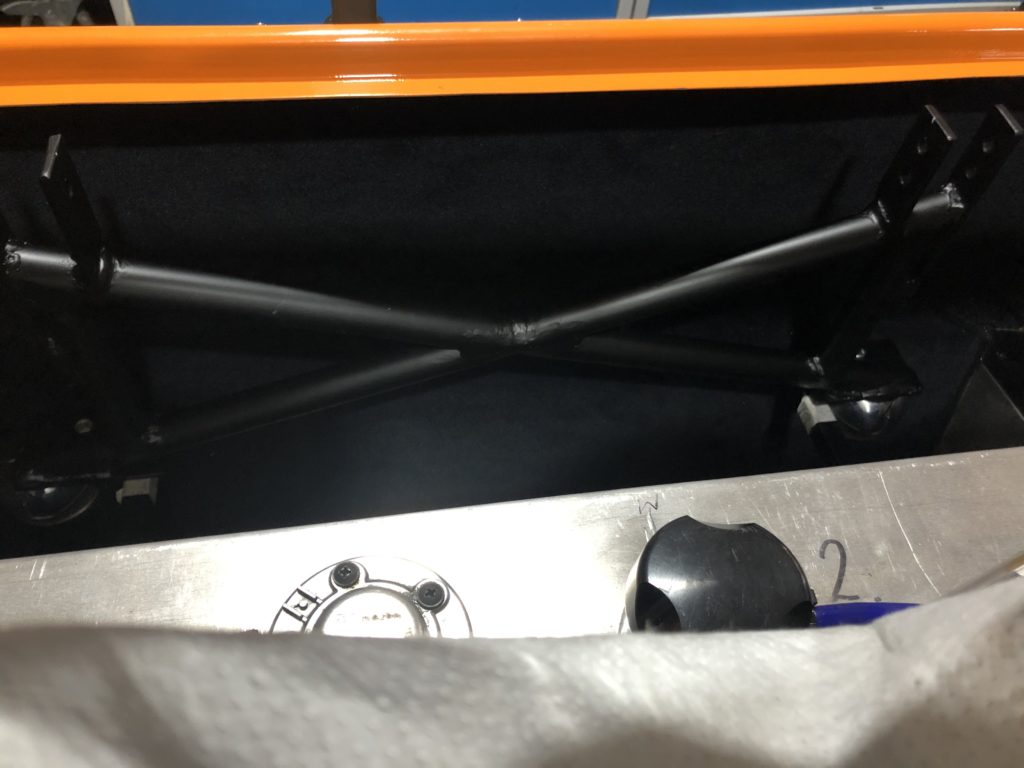
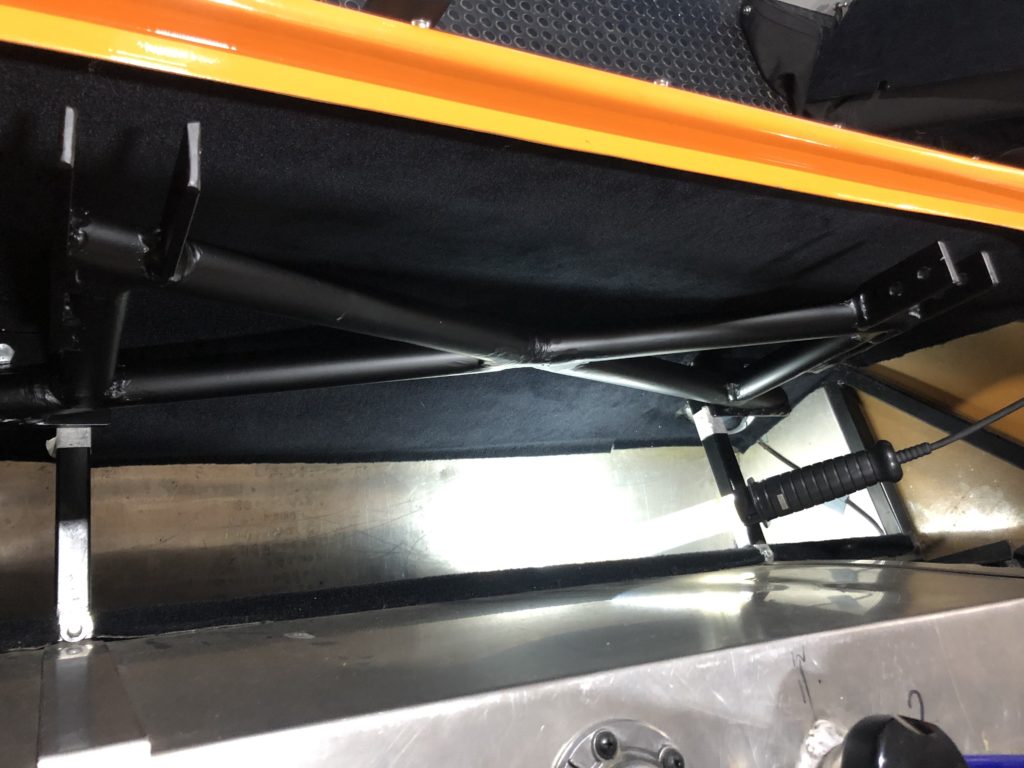
13. MÄRZ 2018
Die Kotflügel sind fertig montiert und innen an den laminierten Flächen schwarz lackiert worden. Die Carbon – Kotflügel sehen fantastisch am HKT aus und ich bin mehr als zufrieden.
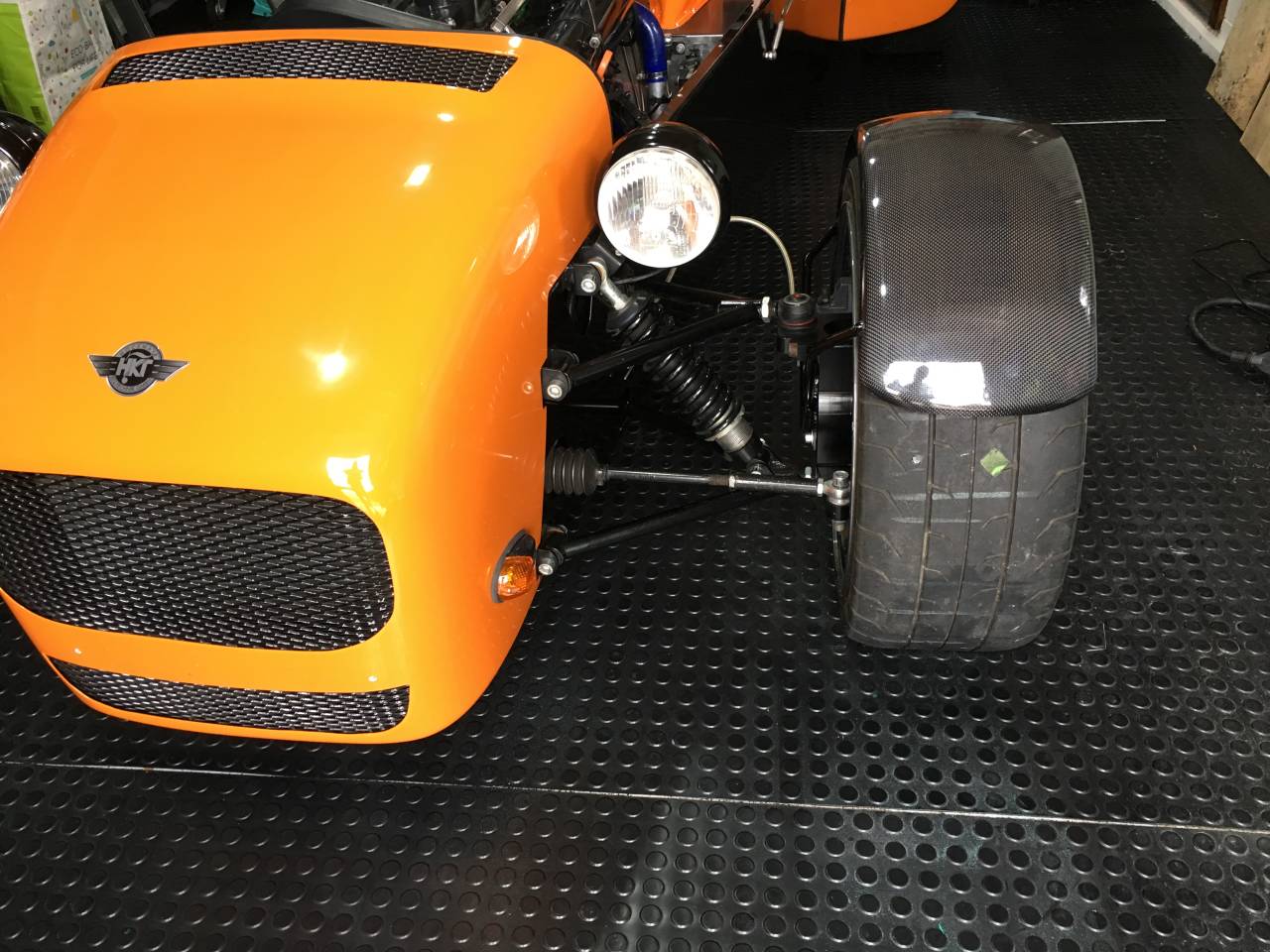

9. MÄRZ 2018
Ich habe heute begonnen die neuen Carbon – Kotflügel von Christof Rothe anzubauen. Die Halter hatte ich schon im Vorfeld selbst angefertigt. Ich habe einen Abstand vom Boden zur unteren Kante des Kotfllügels von 19 cm gewählt. Es gibt widersprüchliche Aussagen in diversen Foren wegen der Anbauhöhe der Kotflügel. Vorher waren es bei meinem HKT 26 cm und das schien mir defintif zu hoch da mir laufend Steine ins Cockpit flogen. Ich wollte die Carbon – Kotflügel auch nicht mit Schrauben befestigen. Das Resultat ist bekannt, ich hatte einen Kotflügel verloren der sich unter das Vorderrad schob. Aus dem Grund kam für mich nur die Variante die Kotflügel mit Polyesterspachtel zu fixieren in Frage. Die andere Variante, die Kotfllügel mit Sikaflex 252 zu montieren, war mir auch zu unsicher.
Die schwierigste Aufgabe bestand darin den Kotflügel auf dem Halter genau auszurichten. Ich habe darauf geachtet dass die Räder mit den Reifen komplett abgedeckt sind. Ich habe aus dem Grund das Ganze provisorisch mit Tesa Band fixiert und die Ausschnitte vom Halter auf das Tesa – Band eingezeichnet. Dadurch ist gewährleistet dass die Kotflügel auf dem Halter schön eben auf der Innenseite des Kotflügels anliegen. Die Ausschnitte an den Kotflügeln habe ich mit einer Rundfeile angefertigt. Ab jetzt suind keine Korrekturen mehr möglich.
Den Halter habe ich blank angeschliffen und anschliessend mit Verdünnung gereinigt.
WICHTIG: Die Innenseite des Carbon – Kotflügels, da wo der Halter am Kotflügel mit Polyesterspachtel befestigt wird, gut anschleifen damit die beim Giessen entstandene Parafinschicht entfernt wird. Ohne dieses Schleifen kann das Polyesterharz und der Polyesterspachtel nicht haften und die Glasfasermatte nicht auf dem Carbon halten.
MONTAGE:
Benötigt werden:
- Polyesterspachtel mit Härter
- Polyesterharz mit Härter
- Glasfasermatte feingerippt
- Plastikspachtel, Sandpapier, Tesaband, verschiedene andere Werkzeuge.
Ich habe den Kotflügel auf dem Halter in seiner definitiven Position mit Tesaband fixiert. Der Abstand vom Boden bis zur hinteren Unterkante des Kotflügels beträgt genau 19 cm! Innen am Kotflügel habe ich die Position des Halters eingezeichnet. Die Innenseite des Kotflügels im Bereich des eingezeichneten Halters wurde sorgfältig angeschliffen. Die beim Giessen entstandene Parafinschicht muss durch das Schleifen entfernt werden. Das Ganze wieder gut reinigen! Anschließend habe ich auf dem Halter Polyesterspachtel auf der ganzen Breite aufgetragen und den Kotflügel in den Polyesterspachtel gedrückt. Anschließend habe ich das Ganze wieder mit Tesa auf der definitiven Position provisorisch fixiert und aushärten gelassen. Zügig arbeiten ist angesagt, man hat zwischen 4 und 7 Minuten Zeit den Polyesterspachtel zu verarbeiten. Nun kommt die 2.Schicht Polyesterspachtel auf die erste Schicht. Diesen 2. Auftrag so spachteln dass vor dem Halter ein kleines Dreieck oder einen kleinen Hügel mit Polyesterspachtel gebildet wird. Das ist wichtig damit später die Glasfasermatte oder Glasfaservlies schön glatt anliegt und nicht bis unter den Halter gedrückt werden muss. Den Polyesterspachtel habe ich nach dem Aushärten glatt geschliffen und gut gereinigt damit ich das Polyesterharz mit Glasfasermatte in das Harz einbetten konnte. Das Polyesterharz mit einer Plastikspachtel zügig auftragen. In dieses feuchte Polyesterharz das Glasfaservlies einbetten. Das überschüssige Polyesterharz mit der Spachtel zügig glatt spachteln, so dass das gesamte Glasfaservlies bedeckt ist. Dabei dürfen keine Blasen im Polyesterharz entstehen! Blasenfrei arbeiten ist ganz wichtig! Ich habe auf das Ganze 2 Lagen Glasfasermatten eingebettet die gut mit Polyesterharz durchtränkt waren. Polyesterharzpfützen verbessern die Haftfähigkeit nicht! Das Polyesterharz trocknet nach 20 Minuten aus.
Ich habe die Anbauanleitung von Christof Rothe genommen die den Carbon – Kotflügeln beilag.
Nach Austrocknung des Harzes werde ich die Innenseiten der Kotflügel noch schwarz lackieren.
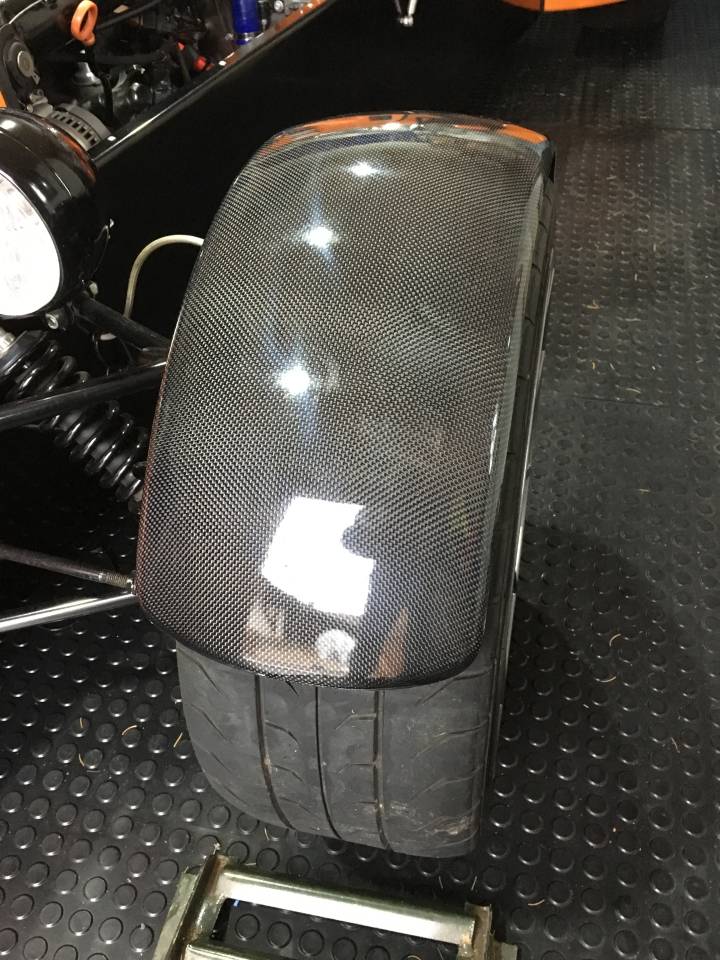
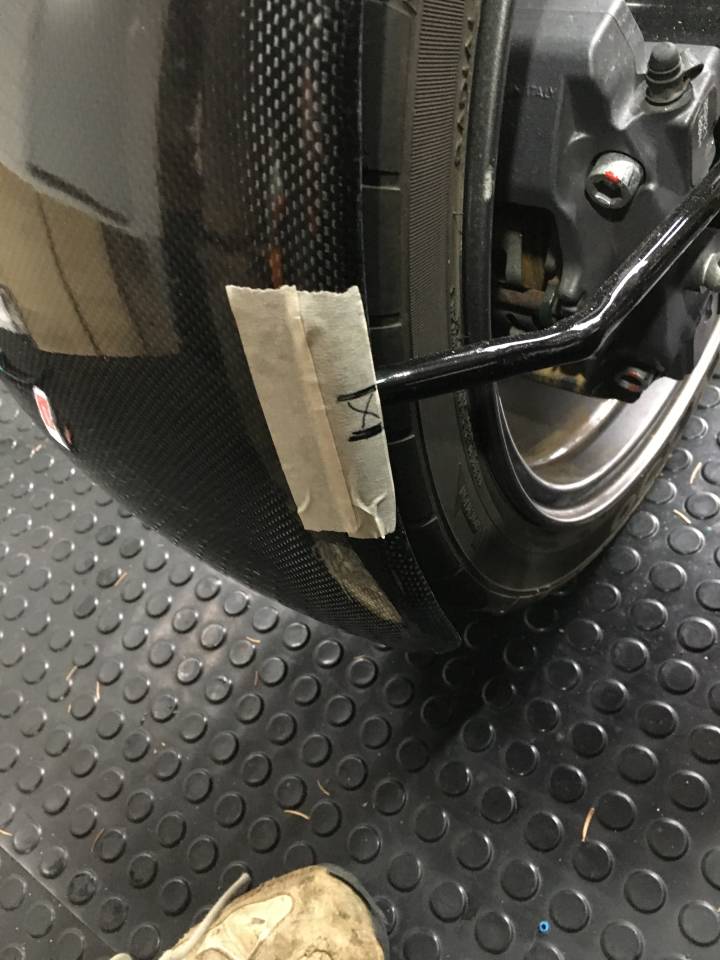
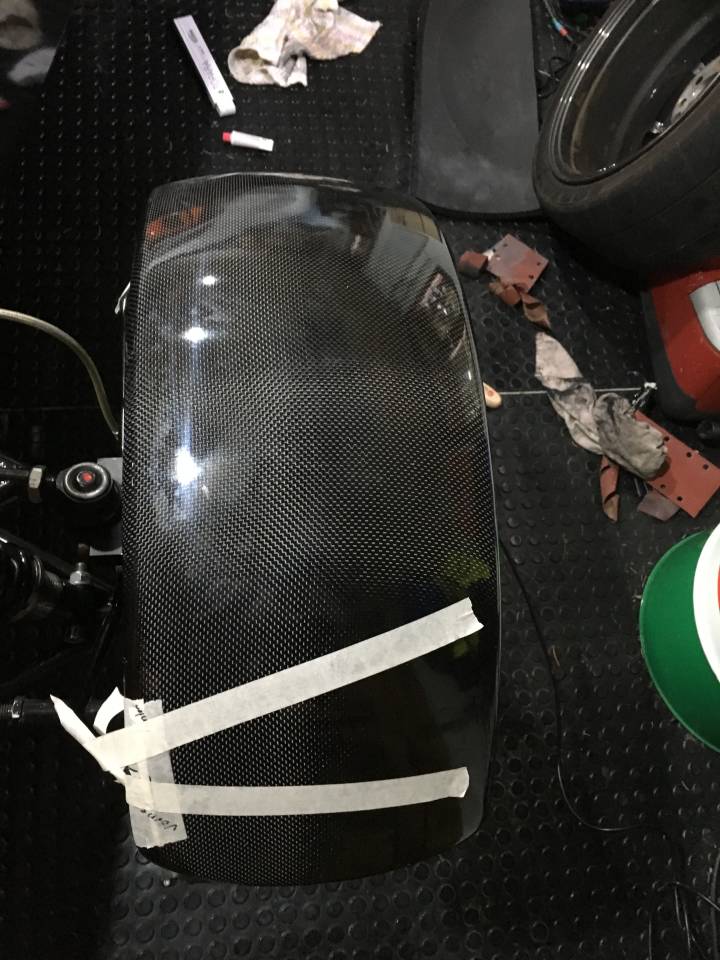
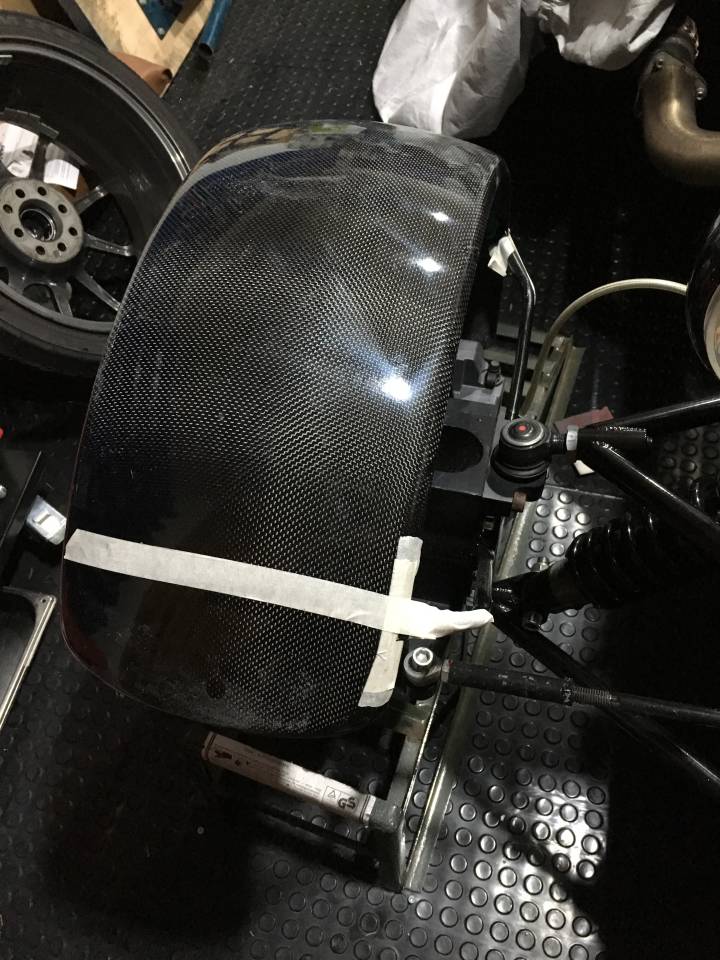
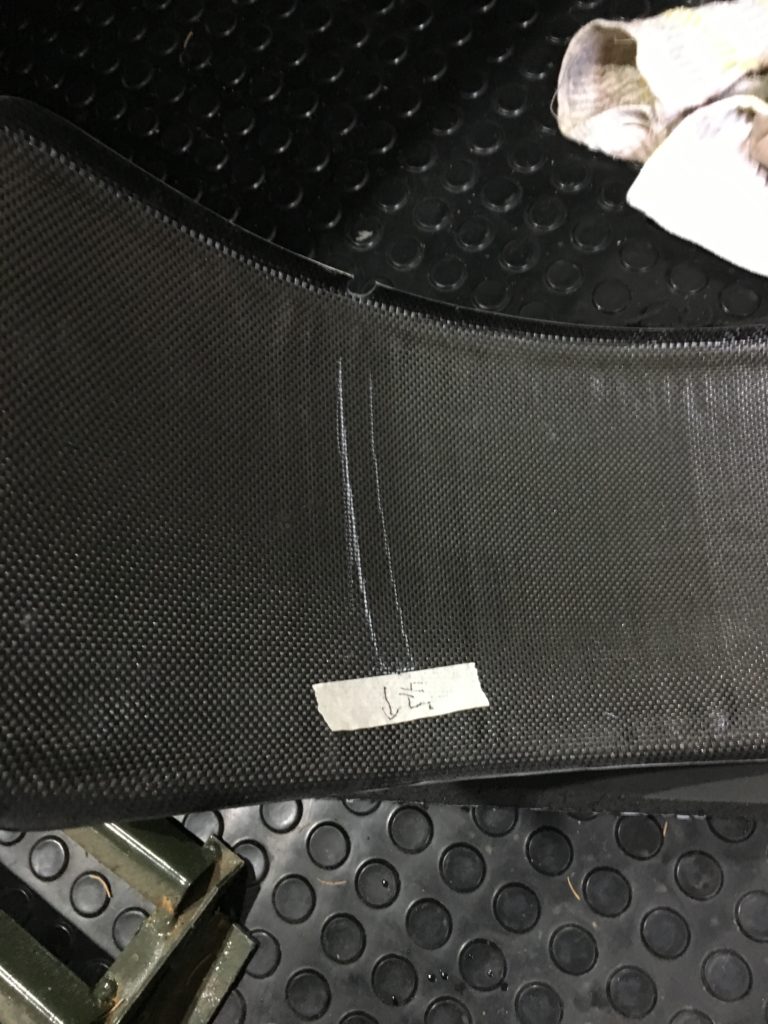
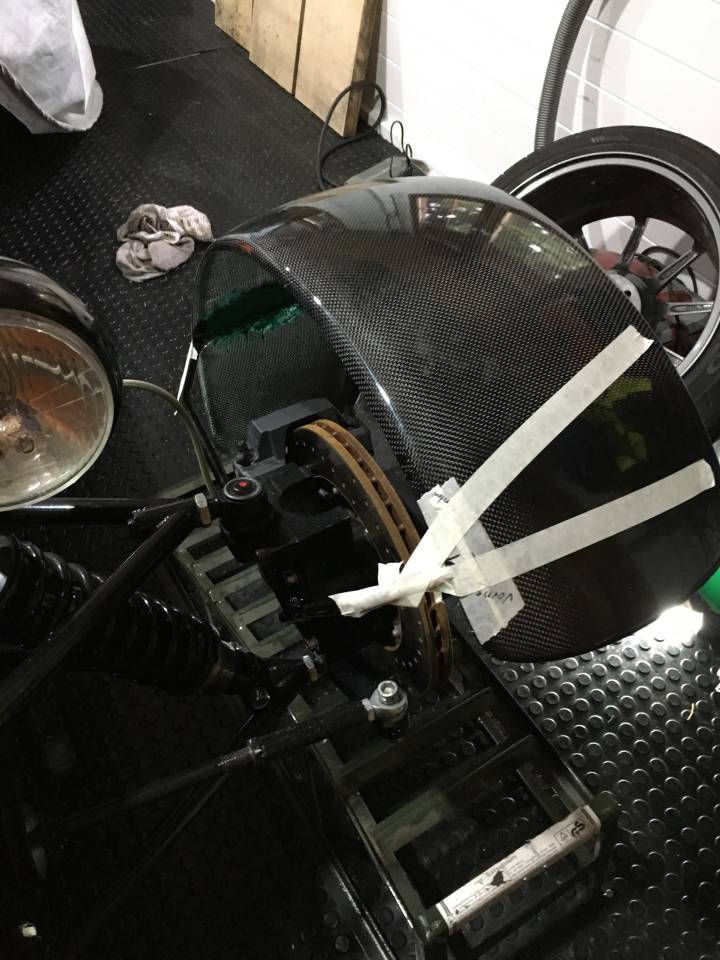
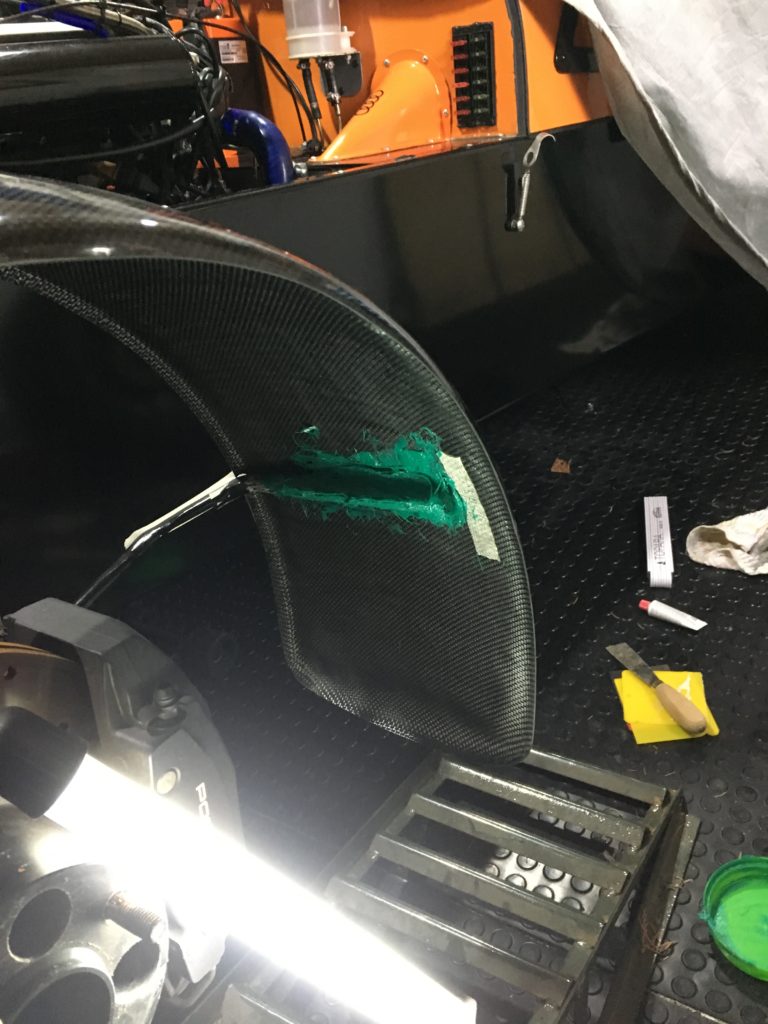
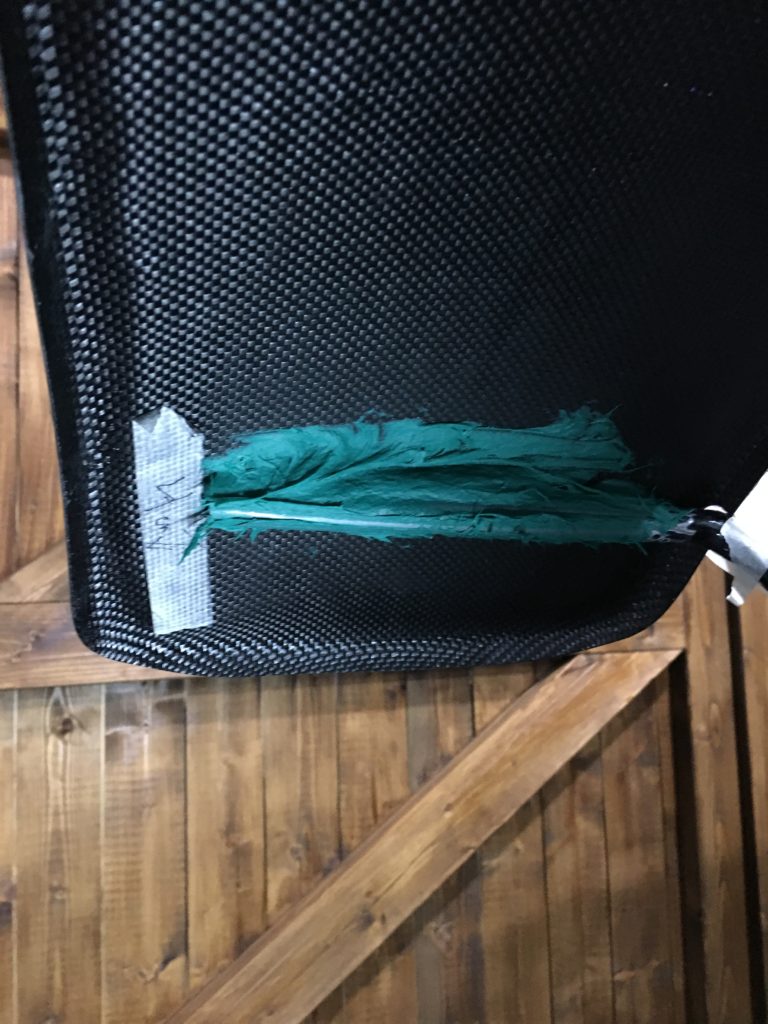
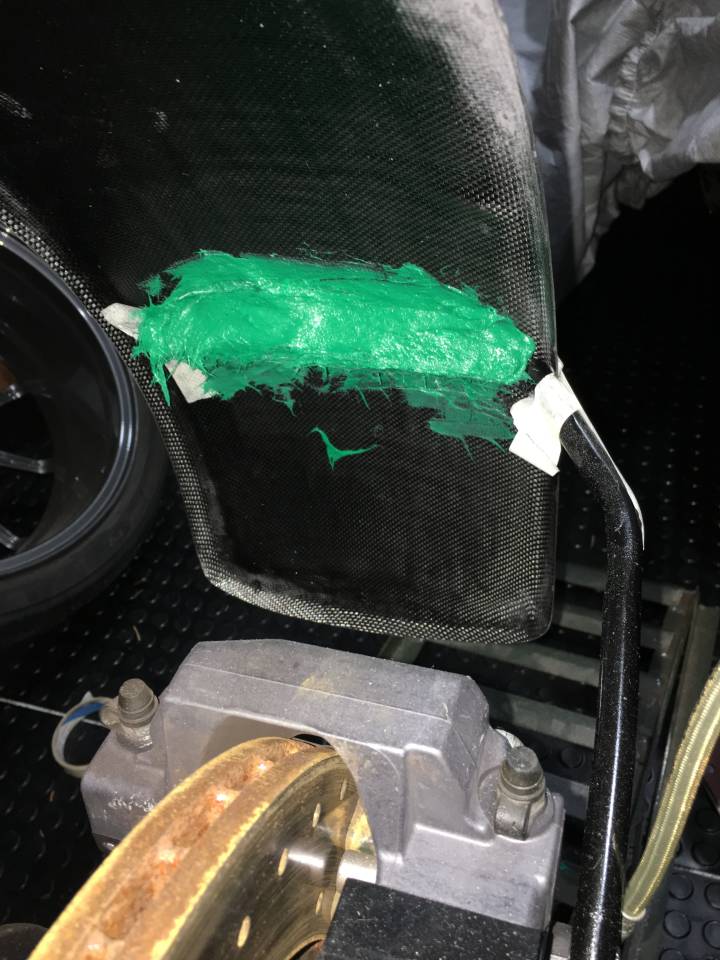
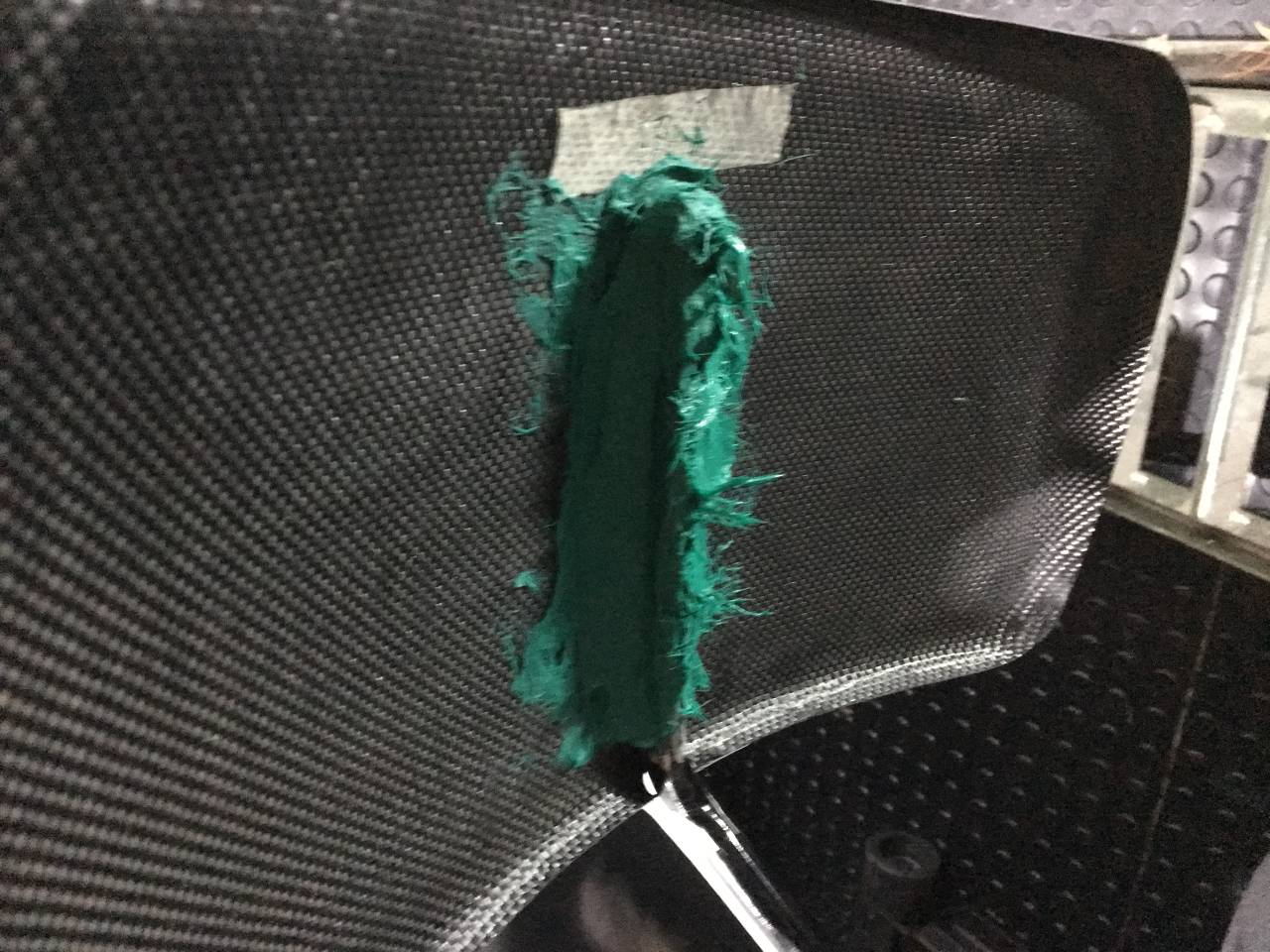
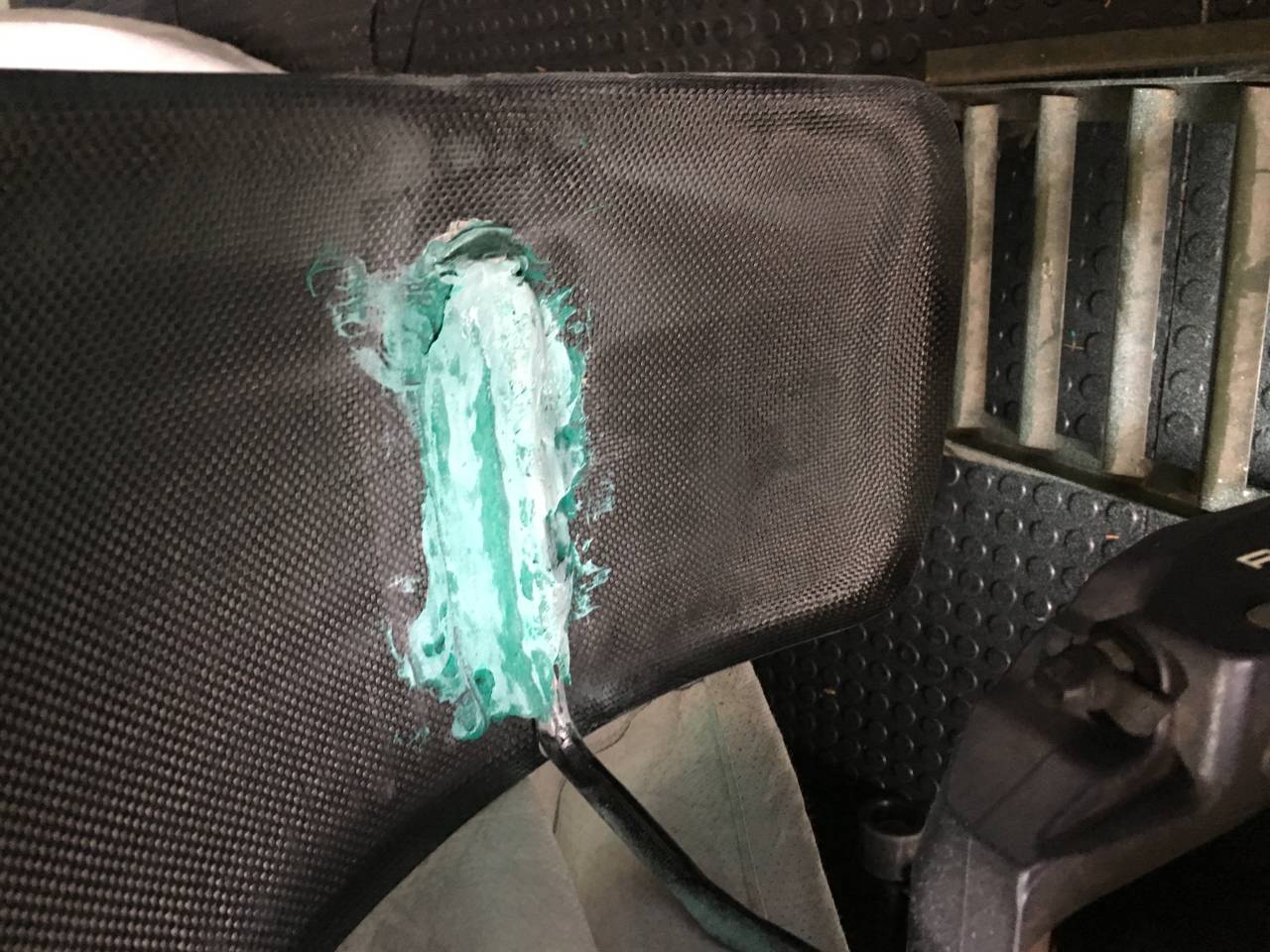
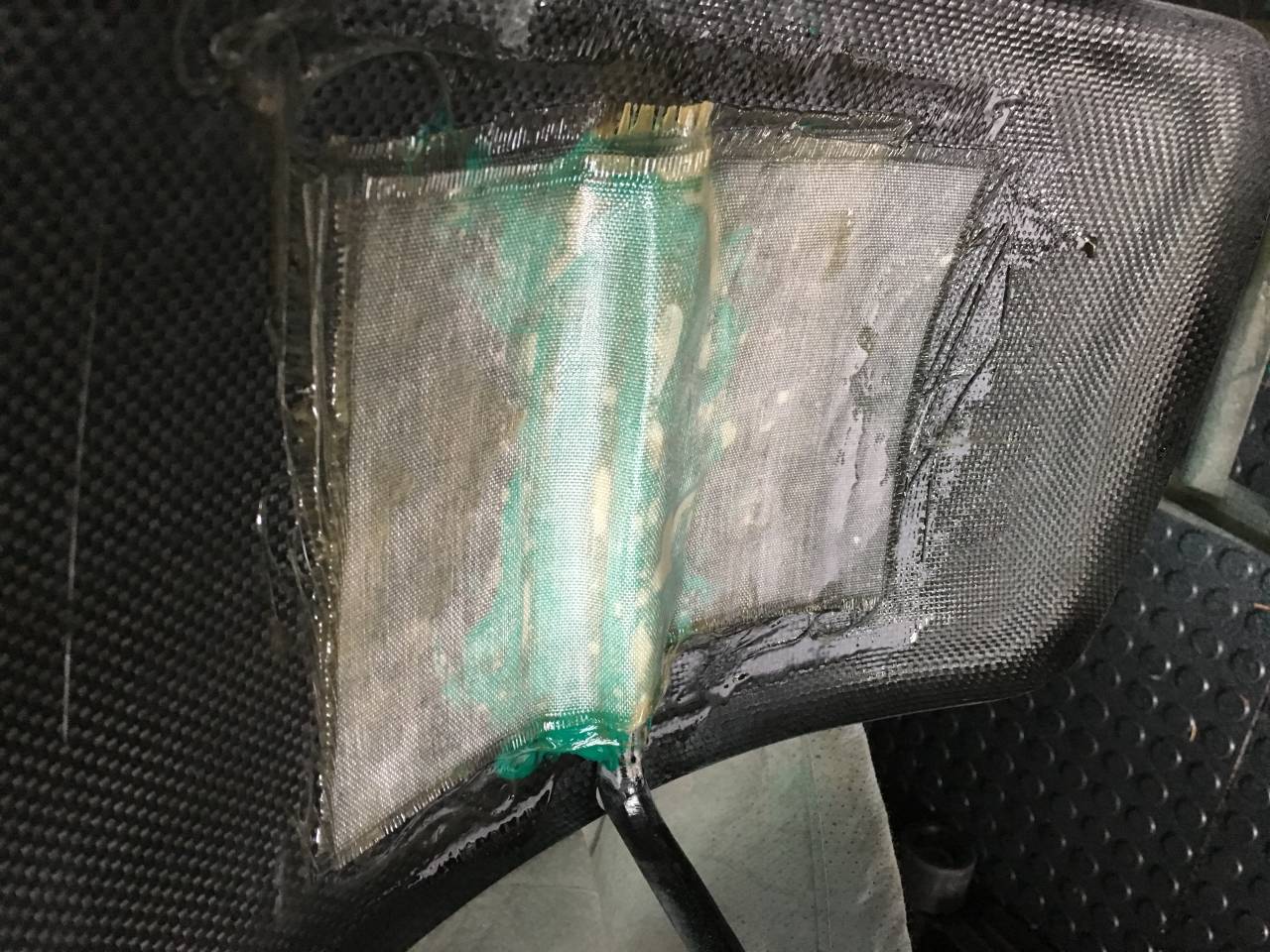
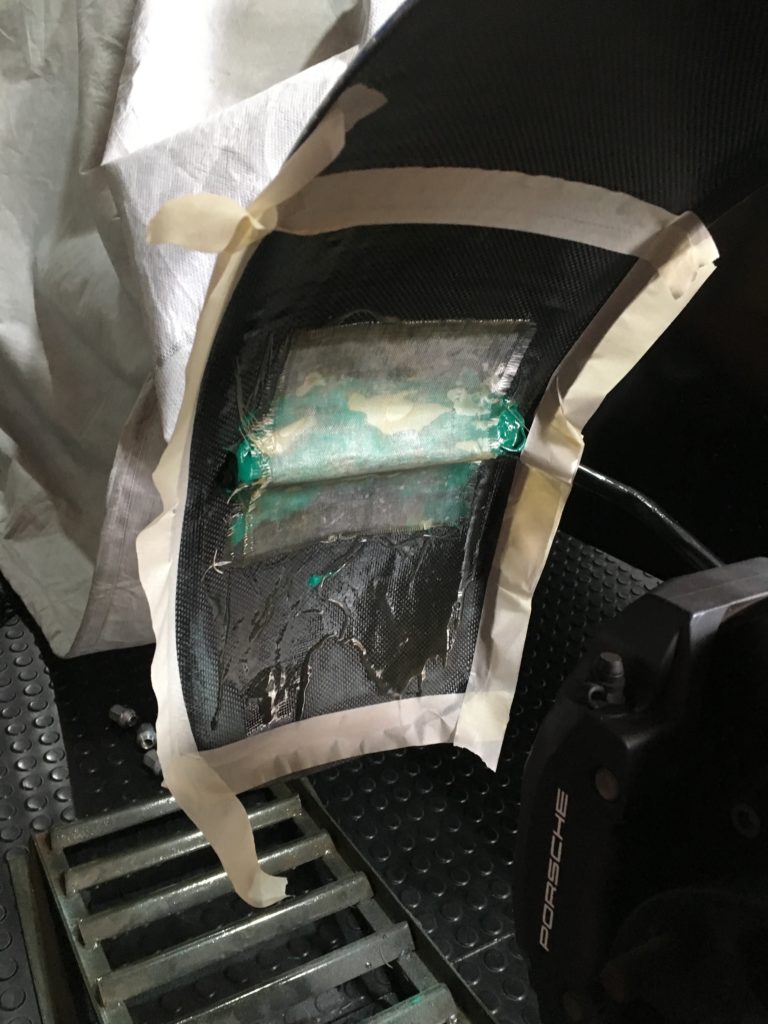
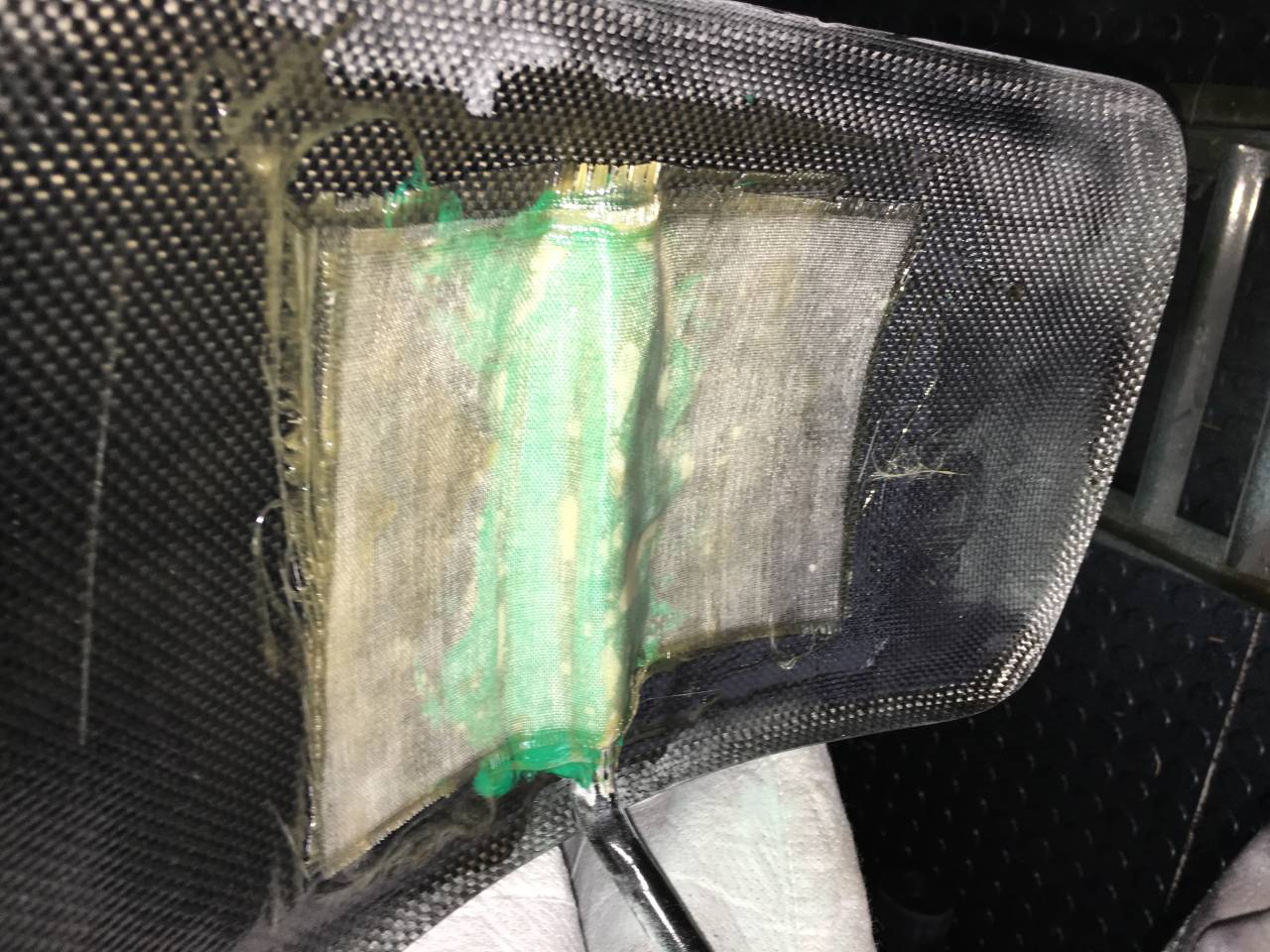
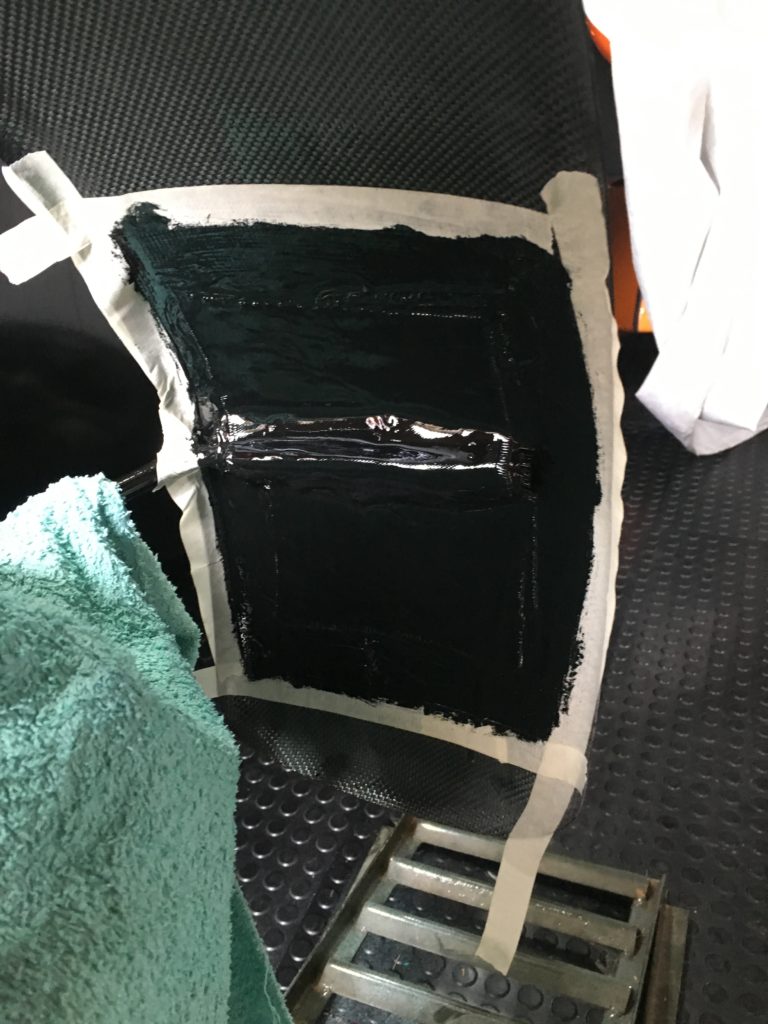
28. OKTOBER 2017
Kotflügelhalter :
Der Kotflügelhalter ist wieder gebrochen und ich hatte fast einen Unfall da sich der Kotflügel bei hoher Geschwindigkeit unter das Vorderrad schob und der HKT dadurch nicht mehr lenkbar war! Der Halter verbog sich dabei komplett und schleifte am Vorderradreifen. Der Grund war dass die Kotflügel nicht richtig am Übergang zwischen dem Rundstahl zum Flachstahl verschweißt waren. Genau an der Stelle ist der Halter zweimal gebrochen. Nicht von großen Vorteil für die Festigkeit der Kotflügelhalter ist auch die Tatsache dass man sich wohl ein paarmal bei der Befestigung der Kotflügel geirrt hatte. Genau an der Stelle, an der die 2 Bohrungen oben am Halter angebracht wurden, ist der Halter gebrochen. Der Kotflügel richtete sich durch den enormen Fahrtwind auf , berührte den Reifen und durch die Drehgeschwindigkeit des Reifens wurde der Kotflügel samt Halter unter das Vorderrad gezogen. Nach einer gefühlten Ewigkeit brach dann endlich der Halter komplett und gab den Kotflügel unter dem Vorderrad frei, der dann sich im hohen Bogen in einem Acker definitiv verabschiedete. Mit diesen Kotflügelhaltern möchte ich nicht mehr fahren. Aus dem Grund baue ich mir meine Kotflügelhalter nun selbst, das kann ich auf jeden Fall besser.
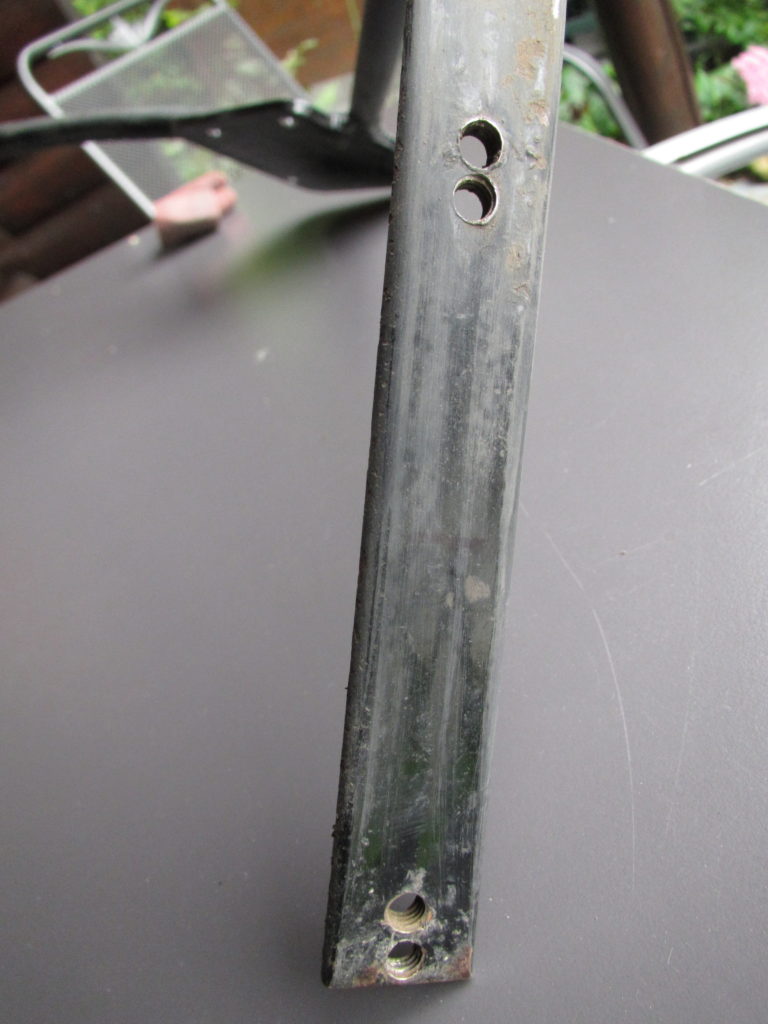
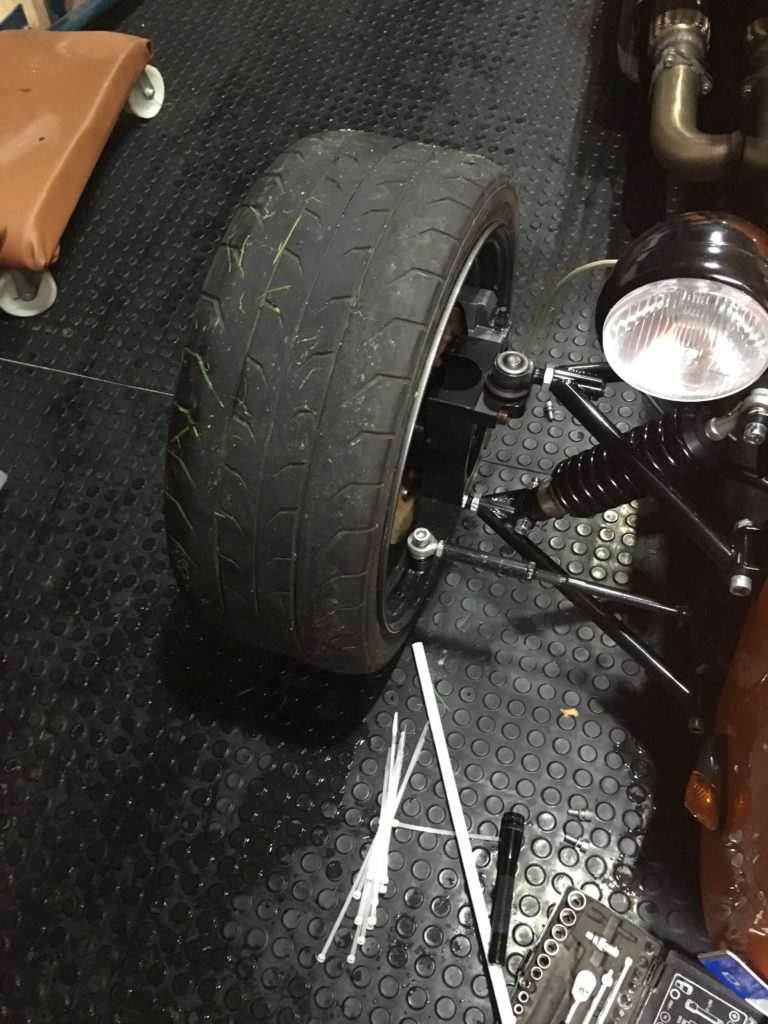
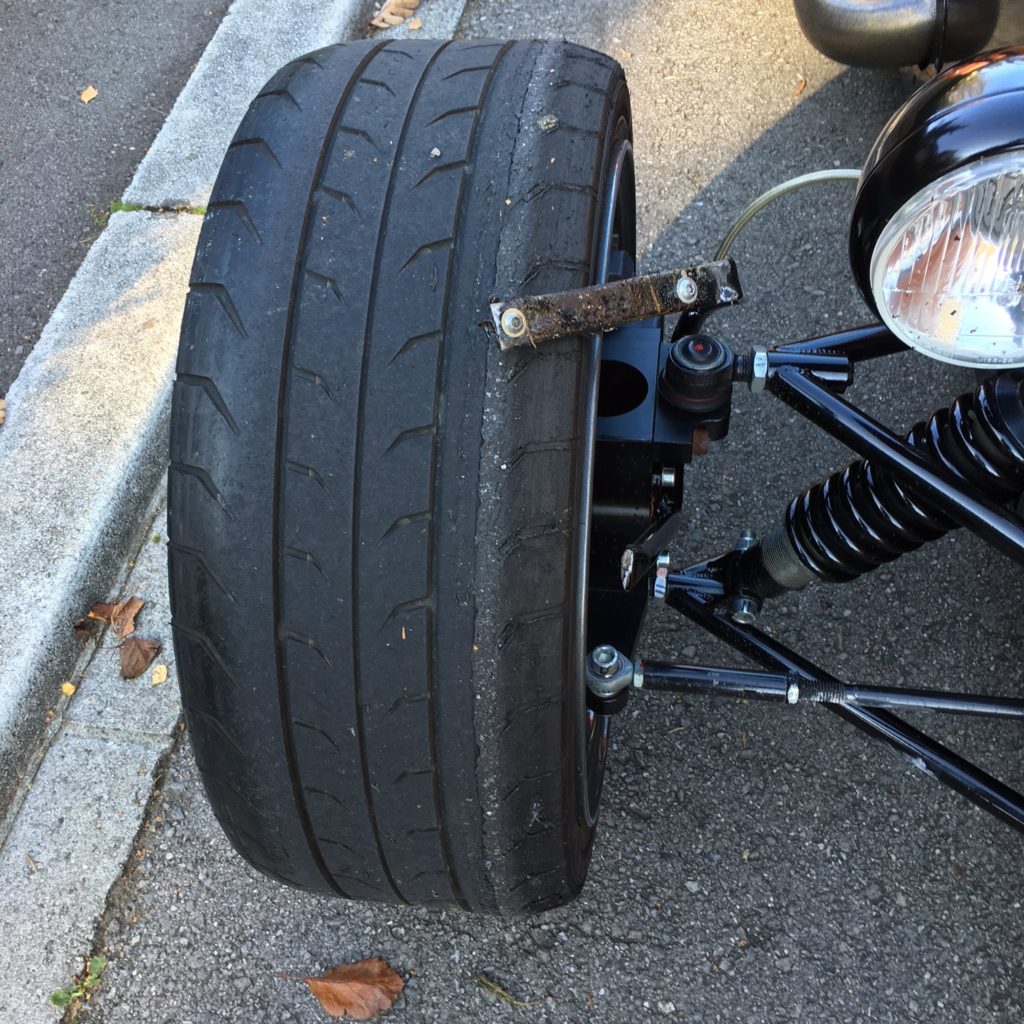
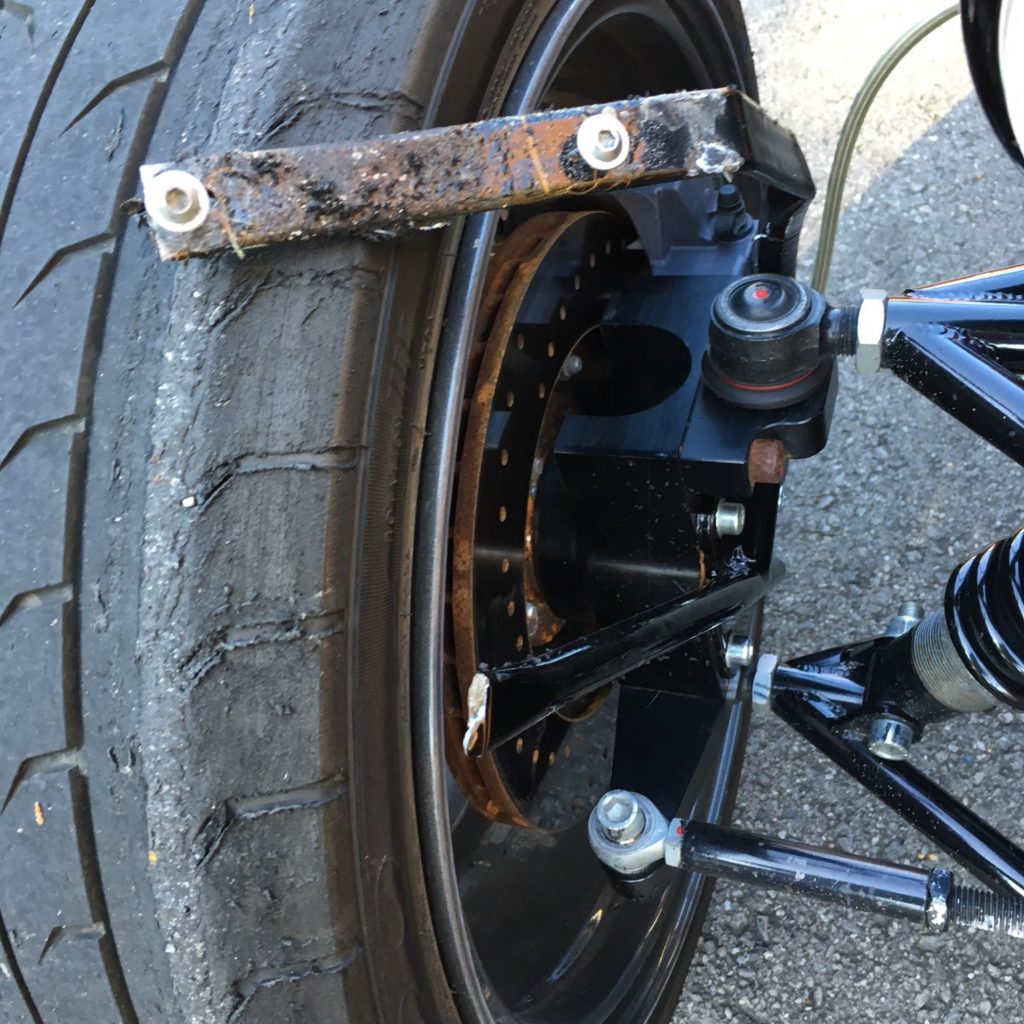
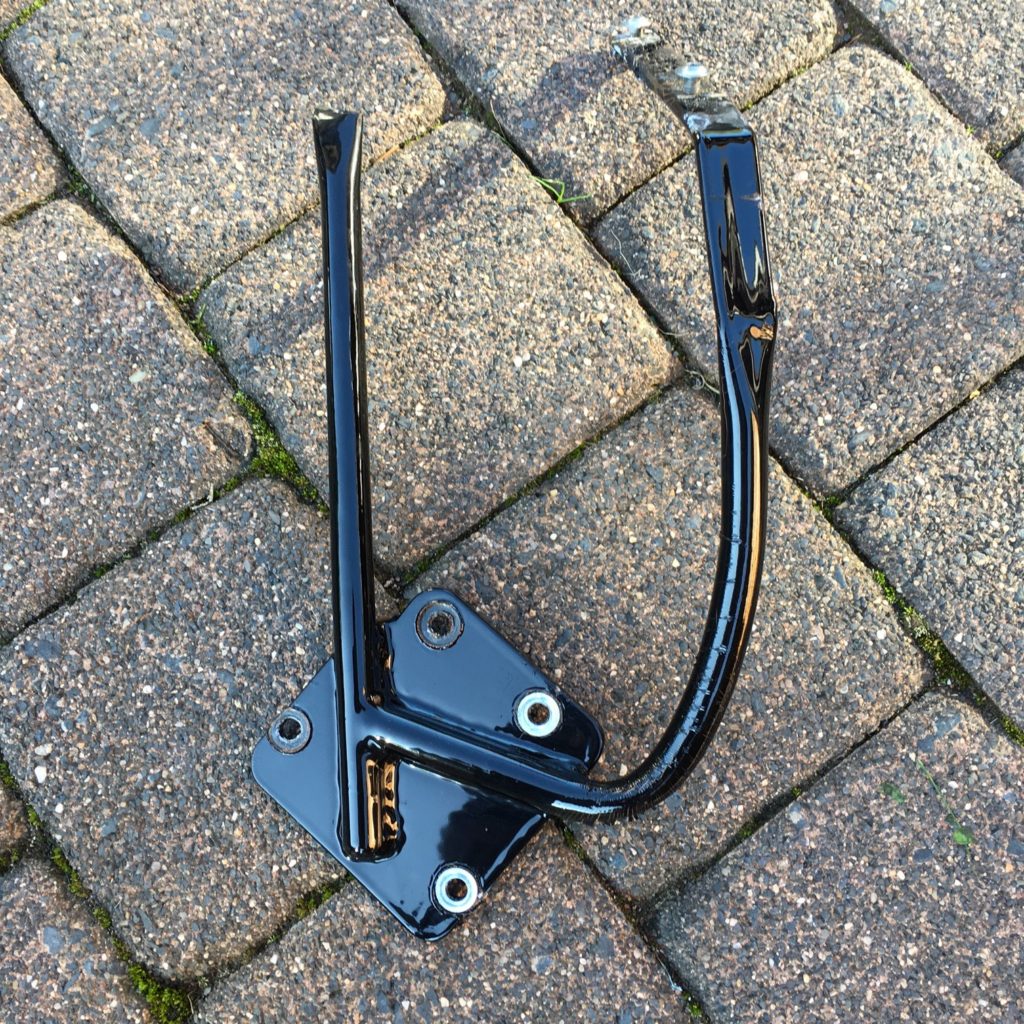
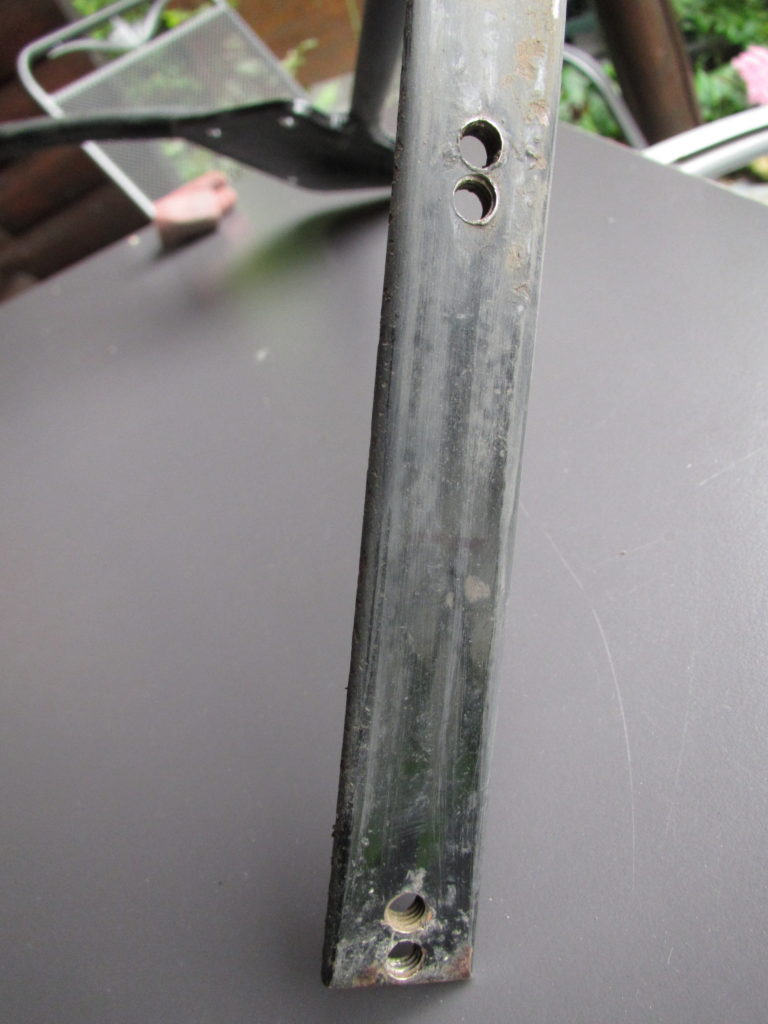
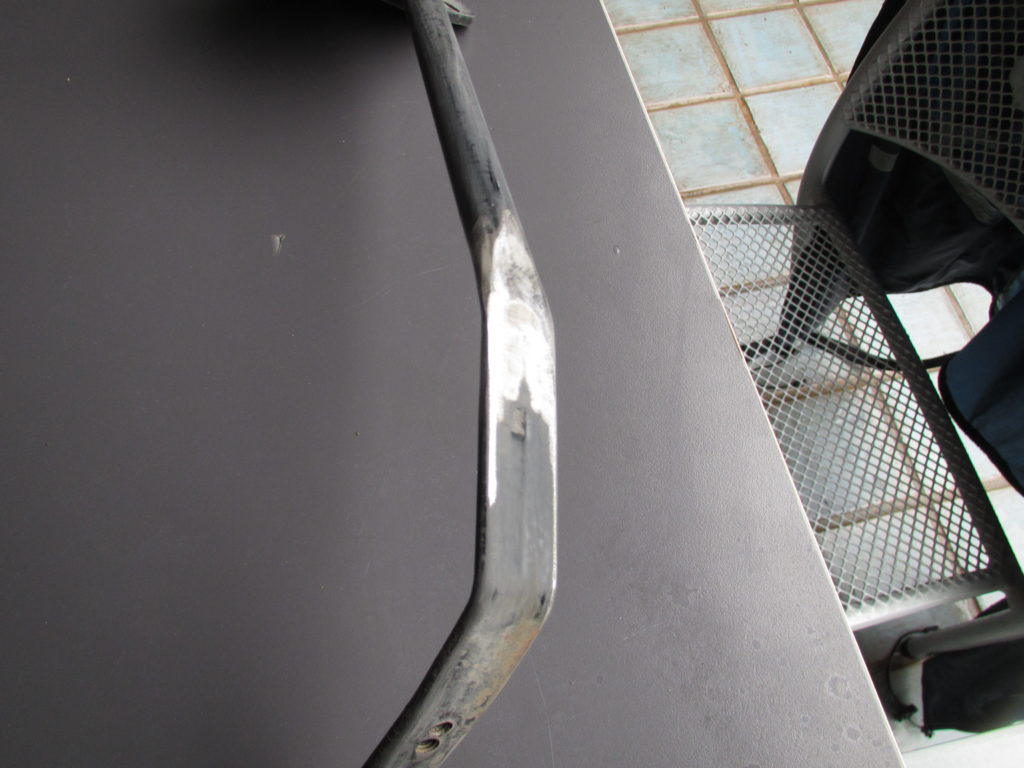
Auf den Fotos oben erkennt man den alten Halter. Weiter unten erkennt man die neuen Halter, noch nicht fertiggestellt, aus 12 mm Rundstahl.
Kotflügelhalter: Ich habe die bestehende Halteplatte weiter verwendet. Der original an den Kotflügelhaltern des HKT verwendete Rundstahl wurde bis an den Rand der Halteplatte abgeschnitten und auf 12 mm aufgebohrt. In diese Bohrung von 12 mm konnte ich die neuen eigentlichen Halter einstecken und neu verschweißen. Ich habe die Lösung mit der Bohrung gewählt da diese einen weiteren Halt des Rundstahls garantiert. Den Rundstahl stumpf anschweißen wollte ich nicht. Der Rundstahl für die eigentlichen Kotflügelhalter wurde nicht gebogen! Sämtliche Teile des Kotflügelhalters wurden ausgemessen, auf Gehrung geschnitten und verschweißt. Das hört sich jetzt aufwendig und mühsam an. Ist es auch, man misst gefühlte 100 Mal……… Aber ich hatte mir große Gedanken über die Herstellung der Halter gemacht und wie man sich die Arbeit leichter machen kann.
Ganz einfach. Ich habe 2 Holzklötze, die den genauen Abstand des Kotflügels zum Reifen simulierten, mit Tesa oder einem breiten Stoffklebeband auf dem Reifen befestigt. Auf der Oberkante der Holzklötze habe ich mit der Silikonkartusche ein wenig Acryl -Dichtmasse aufgetragen und den Kotflügel exakt in der definitiven Position festgeklebt. Acryl -Dichtmasse weil diese nicht so fest klebt wie Silikonkleber oder ähnliches und auch keine hartnäckigen Rückstände am Kotflügel hinterlässt die dann wieder aufwändig am Kotflügel entfernt werden müssen. Man kann auch an der Kotflügel – Unterseite ein Klebeband anbringen um den Kotflügel später leichter von den Holzklötzen zu entfernen. Für den Abstand des Kotflügels vom Boden, also der Strasse, hab ich von der Unterkante des Kotflügels bis zum Boden, 19 cm gewählt. Ist der Kotflügel so erstmal fixiert, lassen sich alle Winkel und Abmessungen des Kotflügelhalters leichter ausmessen und übertragen.
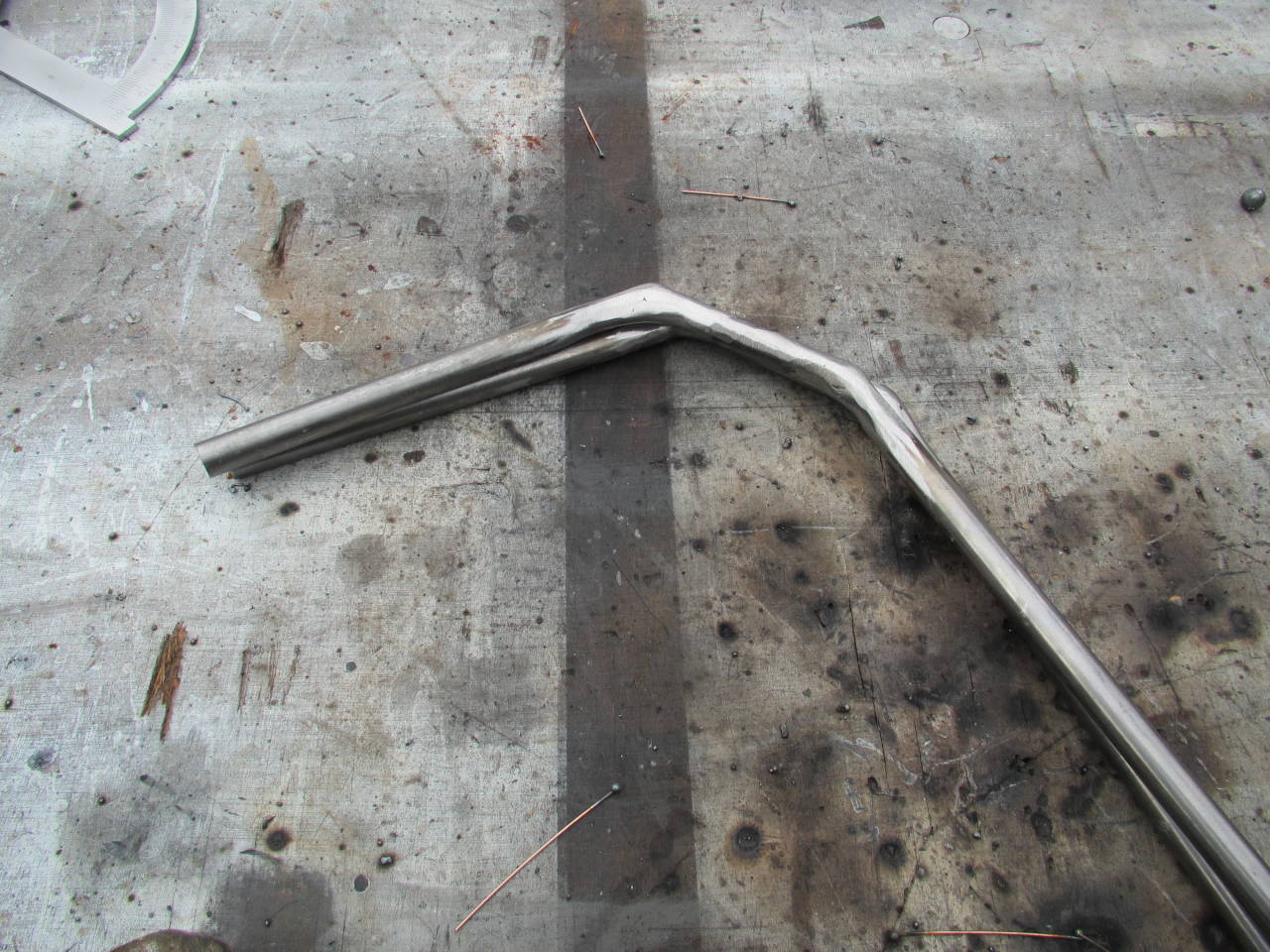
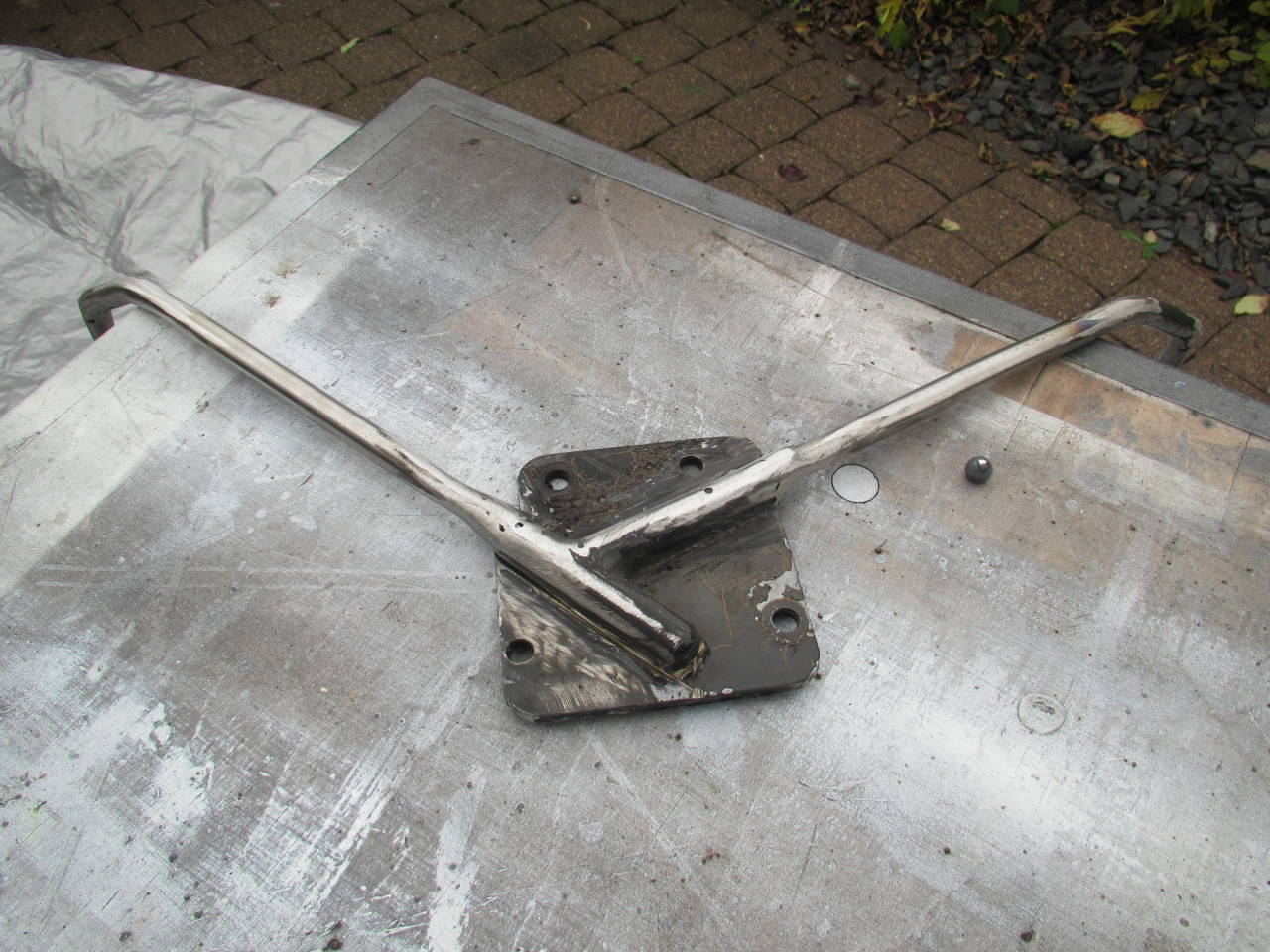
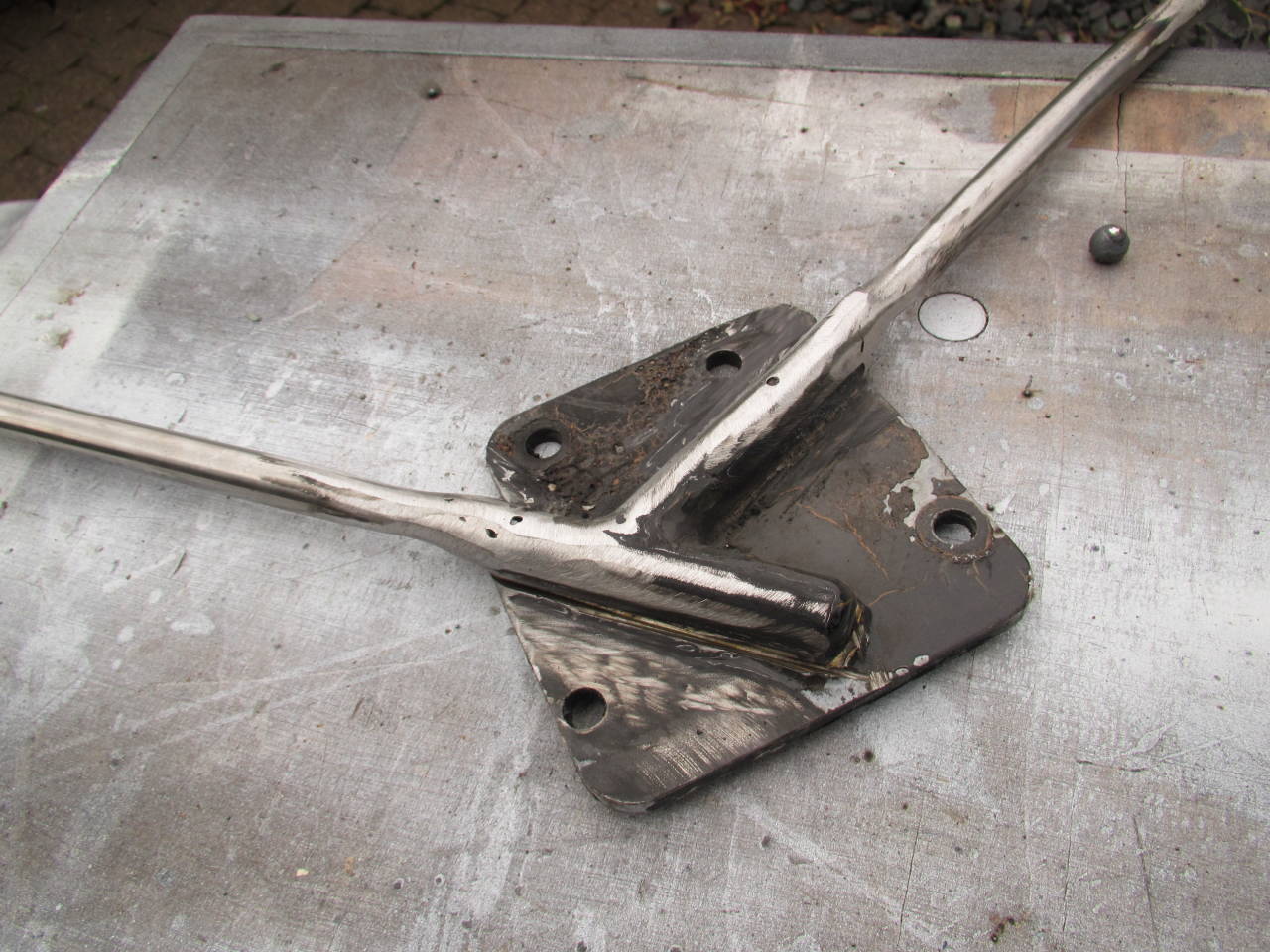
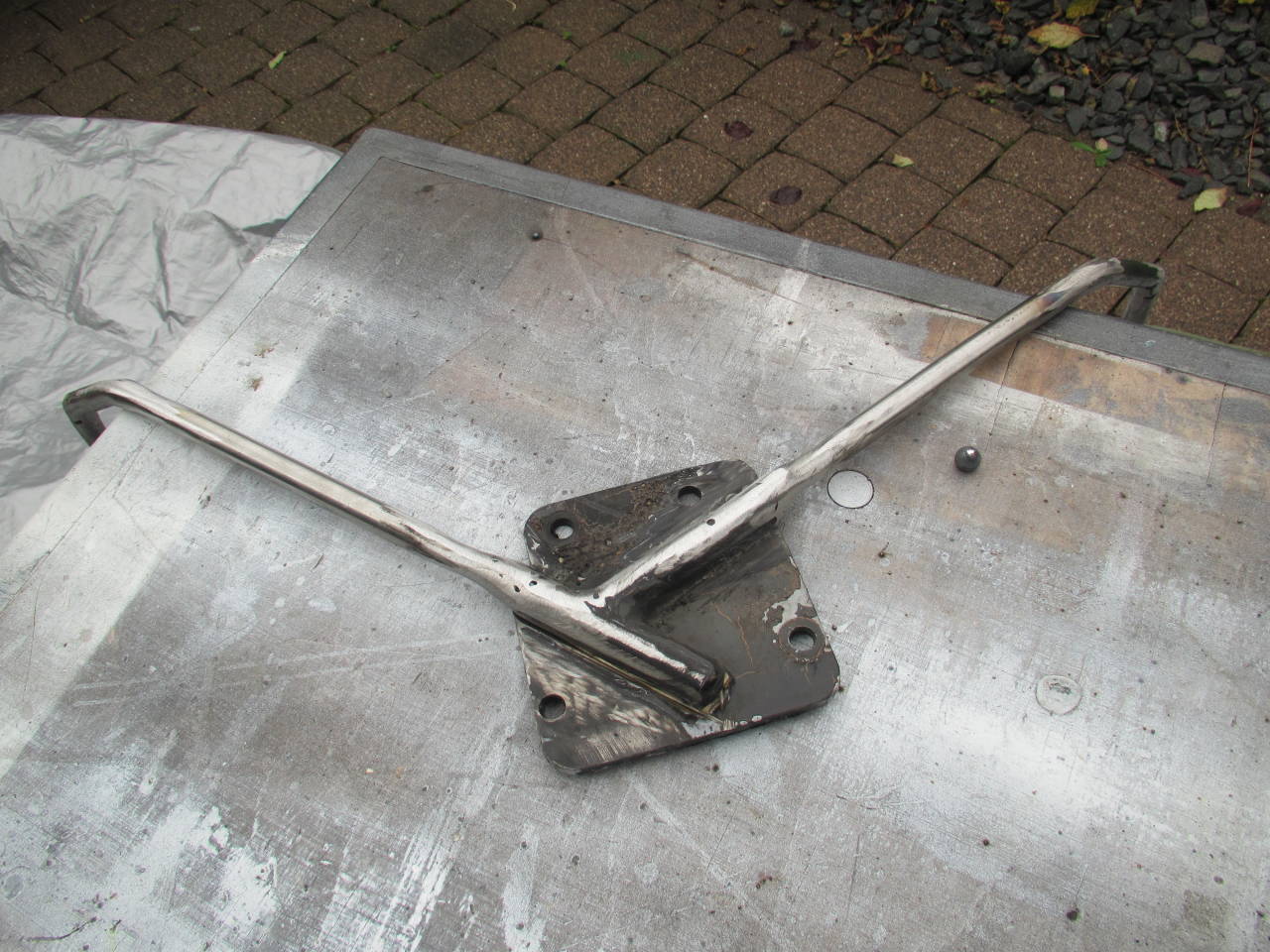
Hier erkennt man die neuen Halter fertig lackiert und zum Einbau bereit. Die neuen Innensechskantschrauben sind bestellt und so kann der Halter, wenn die bestellten Schrauben eingetroffen sind, am HKT montiert werden
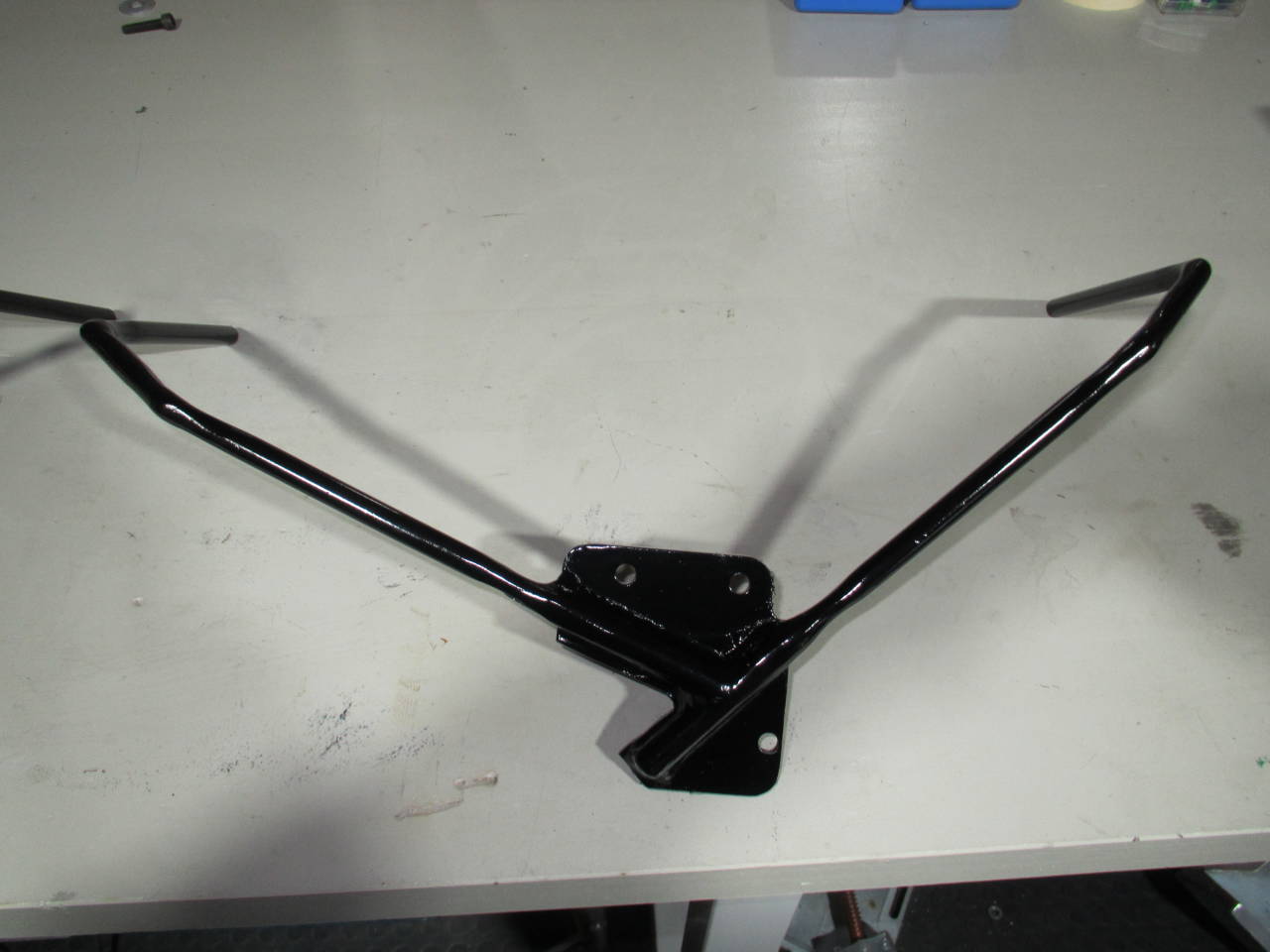
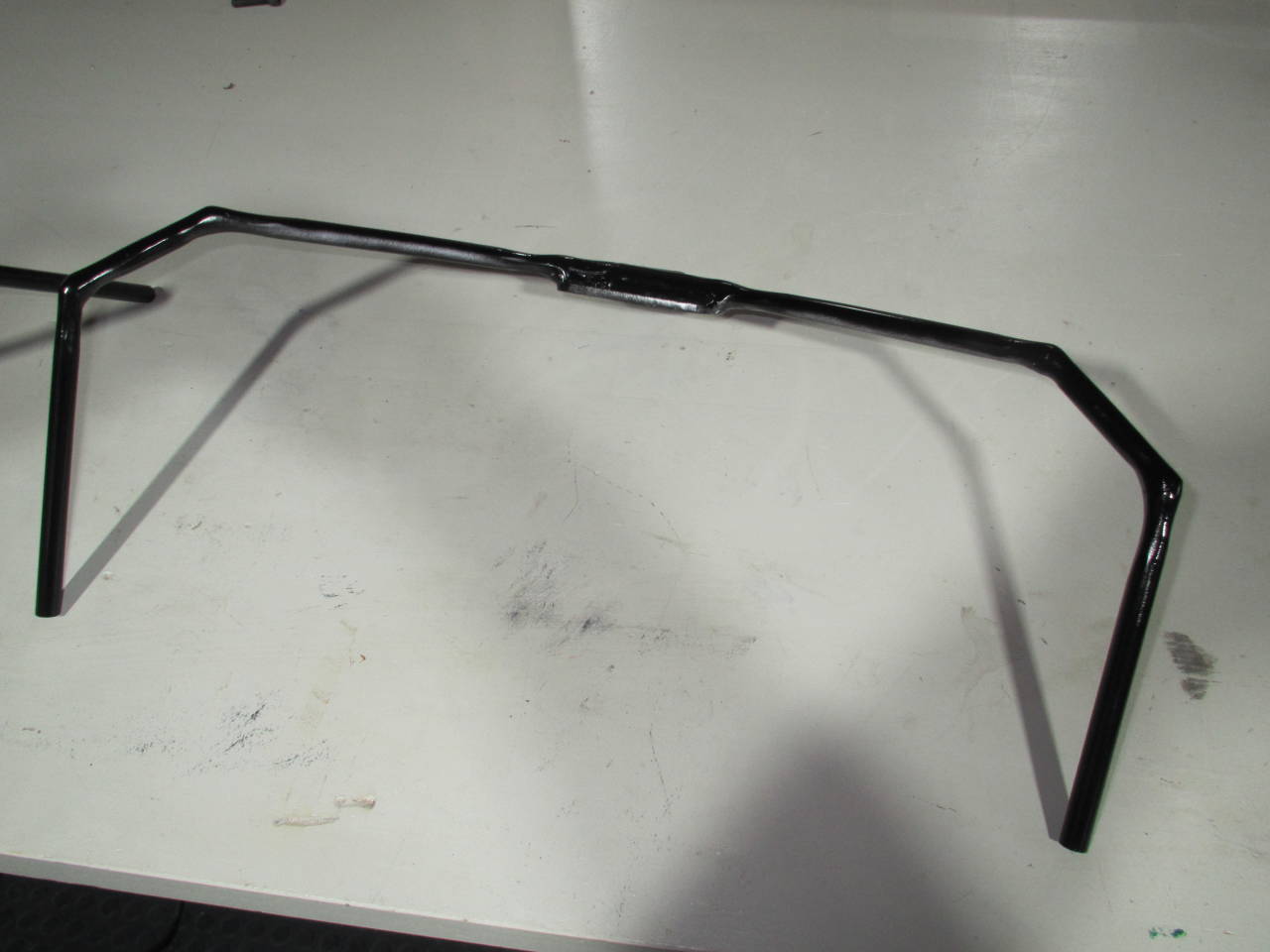
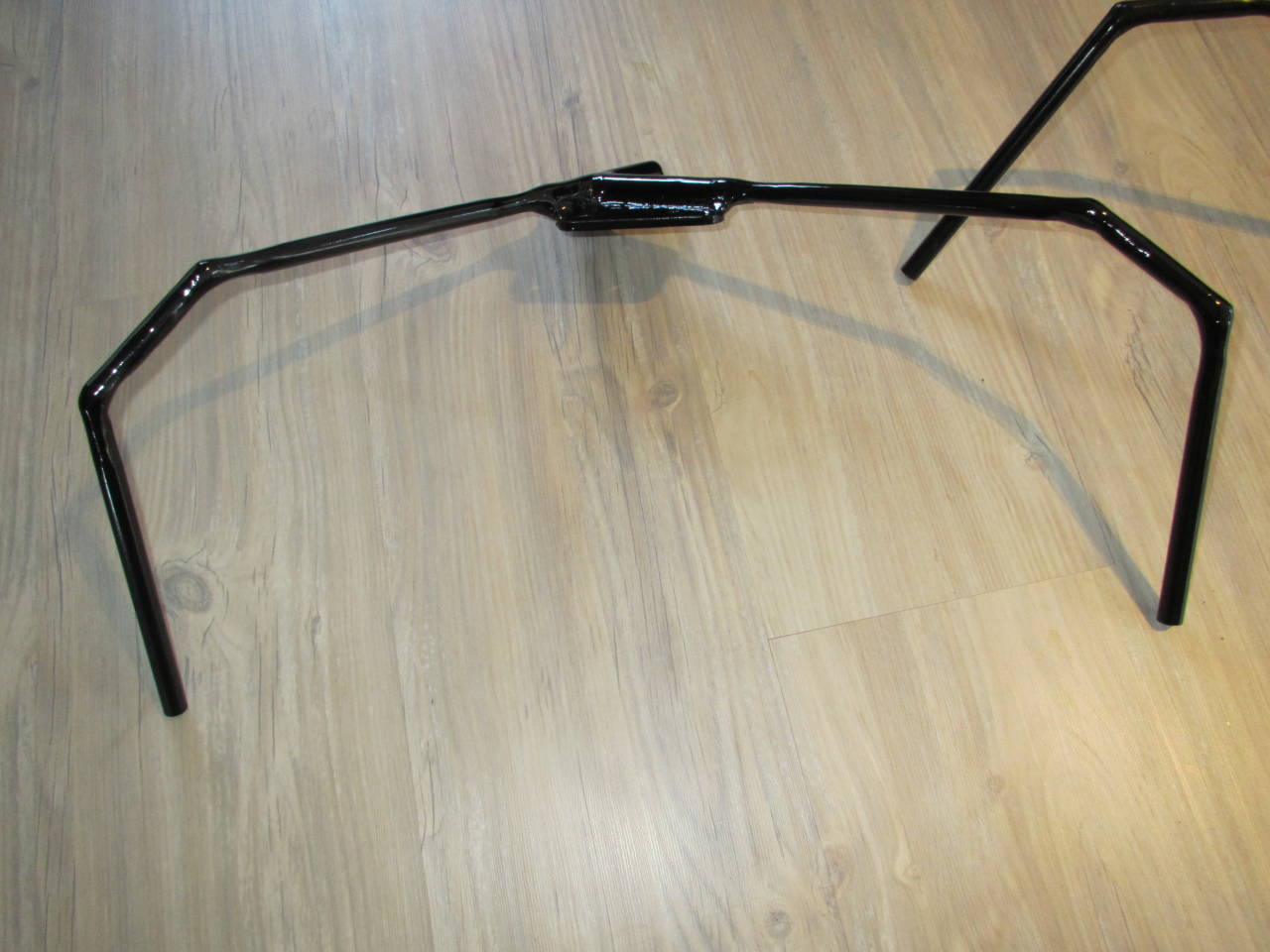
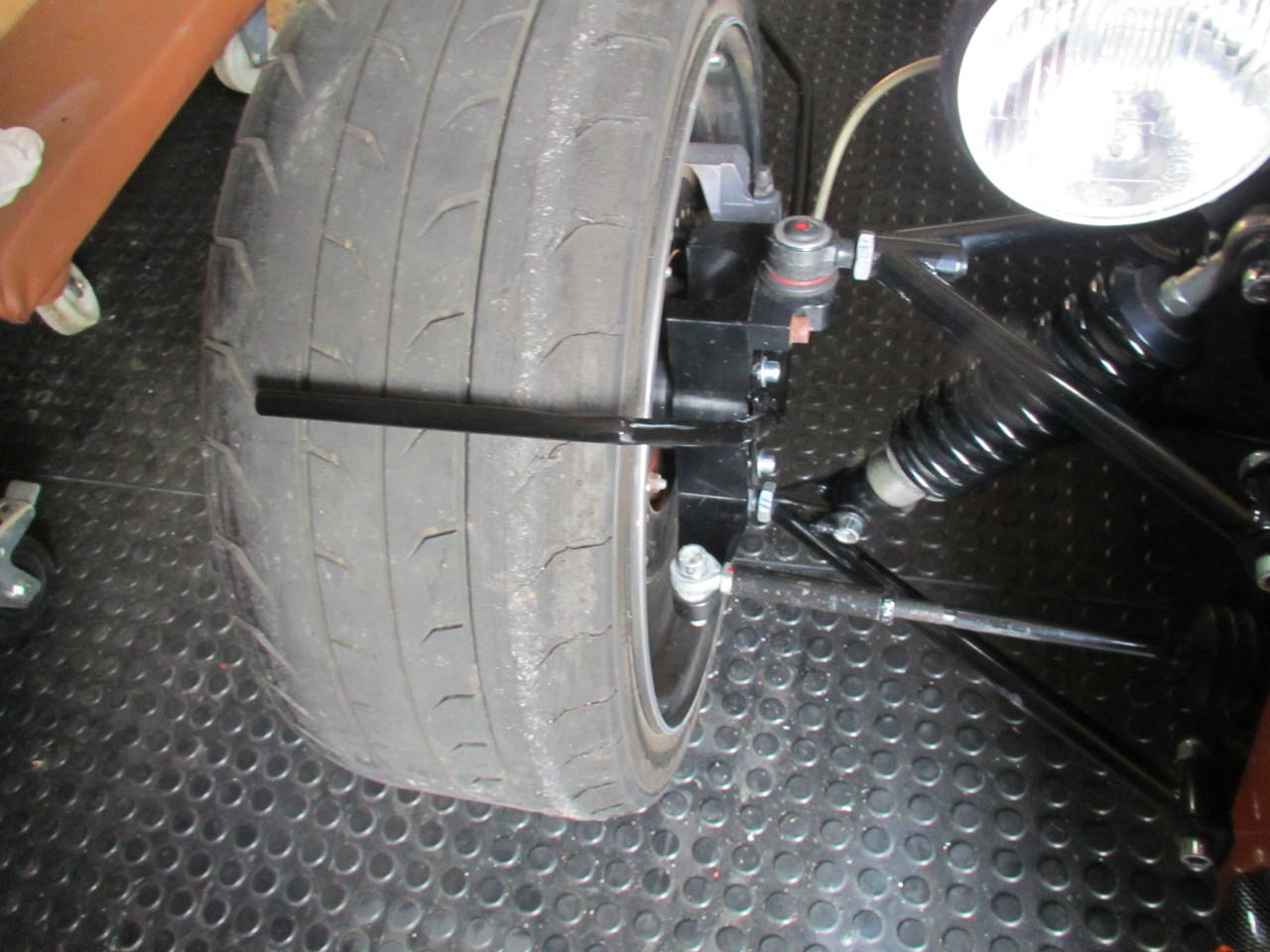
Die neuen Halter sind am Fahrzeug montiert worden. Jetzt fehlen nur noch die Carbon – Kotflügel. Diese sind bereits bei CR-Modelltechnik Christoph Rothe bestellt. Die Montage der Carbon Kotflügel wird im Menüpunkt: “ HKT Laufende Arbeiten “ erklärt.
23. OKTOBER 2017
Auf der Heimfahrt von Essen nach Trier ist mir der Kotflügelhalter am Übergang vom Rundstahl zum Flachstahl gebrochen und ich musste diesen auf dem Autobahnseitenstreifen mit meiner Ratschenverlängerung und Kabelbinder reparieren. Zu Hause angekommen, habe ich den Halter geschweißt und neu lackiert. Trotzdem stellte ich mir die Frage, welche Kräfte dort wirksam sein müssen um ein Flacheisen an dieser Stelle zu brechen.
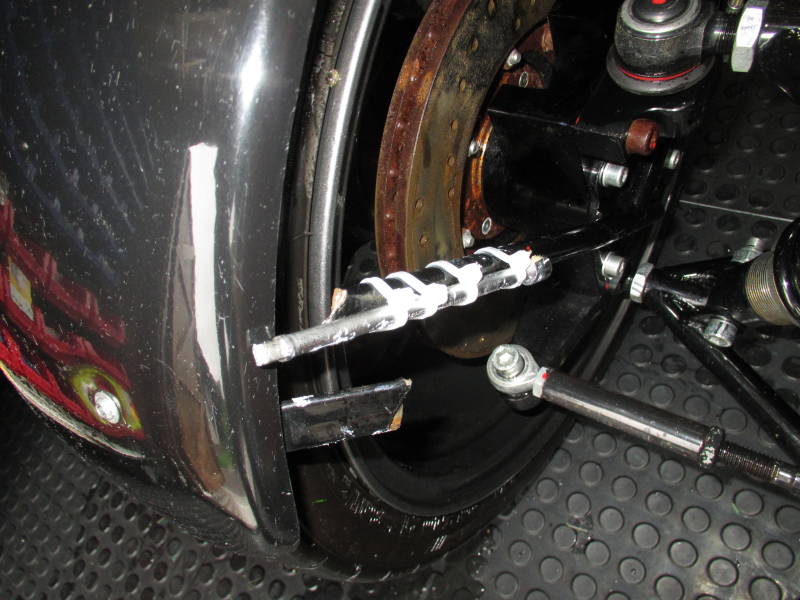
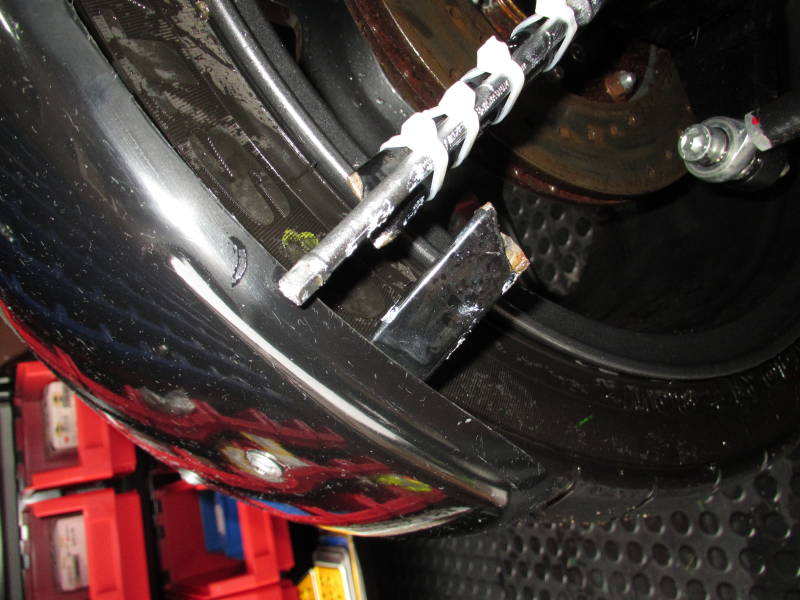
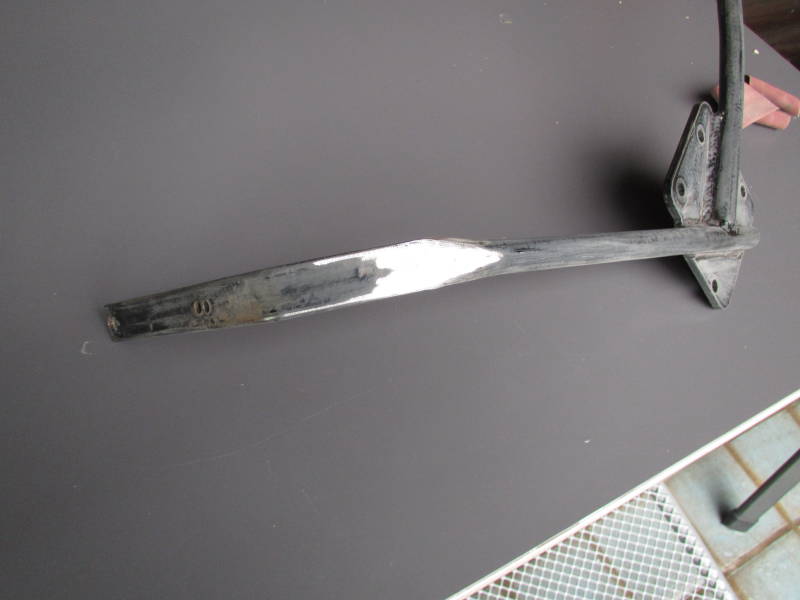