Erklärung zu den Umbauarbeiten:
Der hier beschriebene Umbau und die daraus resultierende Dokumentation stellt keine Bauanleitung oder Betriebsanweisung dar! Es ist mein Hobby, ich arbeite an meinem Fahrzeug und ich habe alle Arbeiten nach meinem Wissen und meiner Erfahrung ausgeführt. Für Fehler oder falsche Informationen auf dieser Seite kann ich keine Garantie erteilen oder haftbar gemacht werden.
12. DEZEMBER 2020
Heute stand zuerst ein Ölwechsel an. Bei der Gelegenheit wurde auch gleich, wie bei jedem Ölwechsel, der Ölfilter gewechselt. Ich habe 4,5 Liter Castrol Edge Super Car 10W 60 eingefüllt. Bemerken möchte ich jedoch dass ich den Ölkreislauf, beide Ölkühler links und rechts sowie alle zu den Ölkühlern führenden Ölleitungen mit Öl vor gefüllt habe. Diese Ölmenge muss zu den 4,5 Liter, die in der Ölwanne vorhanden sind, dazu gerechnet werden. Dann erfolgte der erste Motorstart nach dem großen Umbau. Die Überprüfung aller neu verbauten Komponenten verlief positiv. Sehr überrascht bin ich über den Lärmpegel der neuen Auspuffanlage. Viele Kollegen hatten Bedenken wegen des doch sehr kurzen Schalldämpfers und des damit verbundenen Geräuschpegels. Die Auspuffanlage ist, obwohl diese vom Durchmesser her viel grösser ist als die original verbaute Auspuffanlage, nicht viel lauter als diese. Eine kleine Änderung am Flansch vom Kat will ich dennoch vornehmen. Der Abstand zwischen beiden Flanschen, einer am Auspufftopf und einer am Kat, ist mir mit 8 mm zu groß. Es ist zwar überhaupt kein Problem, wegen dem eingebauten Flexrohr, beide Flansche miteinander zu verschrauben, aber bedingt durch den Spalt von 8 mm nehme ich dem Flexrohr auch eine gewisse Dehnungslänge oder eine Möglichkeit der Dehnung um möglichen Vibrationen entgegen zu wirken und diese zu absorbieren. Das möchte ich so nicht lassen und werde diesen Spalt durch eine kleine Maßnahme am Auspuffrohr des Katalysators verkleinern.
Nach dem Motorstart entstand eine kleine Rauchentwicklung wegen der Isolierung der Downpipe, aber das war so gewusst. Der Kleber der Isoliermatte verdunstet wegen der hohen Temperatur an der Downpipe. Aber das wird nach einiger Zeit, wenn der Motor richtig warm gefahren wurde, deutlich weniger werden.
Eine intensive Sichtkontrolle aller Dichtungen und Fittinge ergab auf den ersten Blick keine Leckage. So weit bin ich aufs erste zufrieden.
06. NOVEMBER 2020
Die Arbeiten an der Downpipe waren sehr umfangreich und anstrengend. Aus dem Grund gibt es heute nur ein kleines Update. Ich habe heute den Öldruck im Motor aufgebaut ( ohne den Motor zu starten ), um zu prüfen ob die neuen Dash 10 Ölleitungen die zu den beiden Ölkühlern links und rechts führen und die Turbolader- Ölanschlüsse am Turbolader und am Motorblock , dicht sind. Um Öldruck aufzubauen, ohne den Motor zu starten, sind jedoch folgende Vorarbeiten notwendig:
- Kurbelwellensensor abstecken, links am Übergang zum Getriebe
- Nockenwellensensor, oben links am ZK, abstecken
- Einspritzdüsenstecker der 4 Einspritzdüsen abstecken
- Zündspulen abstecken
Ich wage es fast nicht zu schreiben, da ich trotzdem ein wenig abergläubisch bin, aus dem Grund schreibe ich auch nicht dass alles dicht ist, sondern es sieht sehr gut aus. Aber fürs erste bin ich zufrieden.
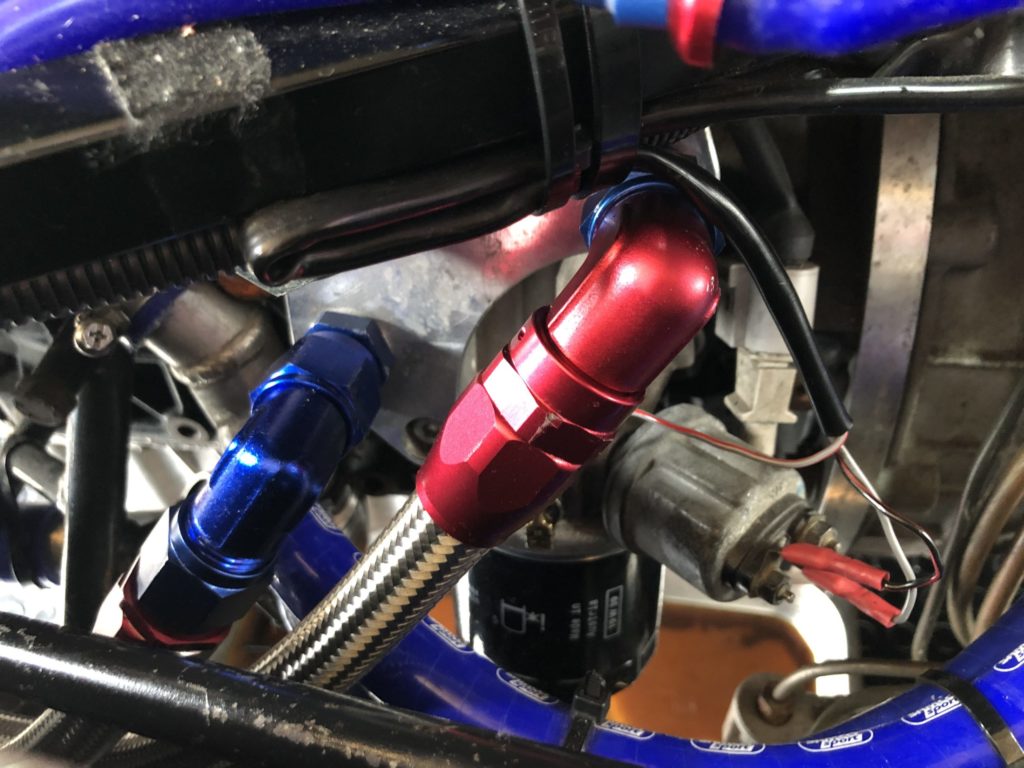
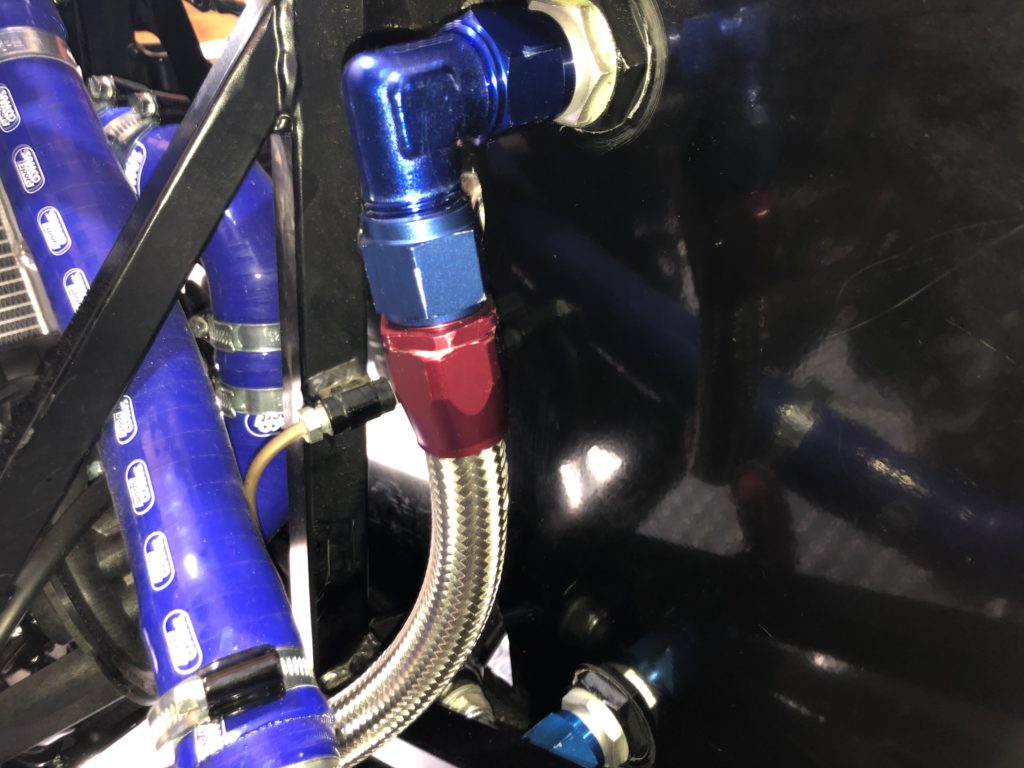
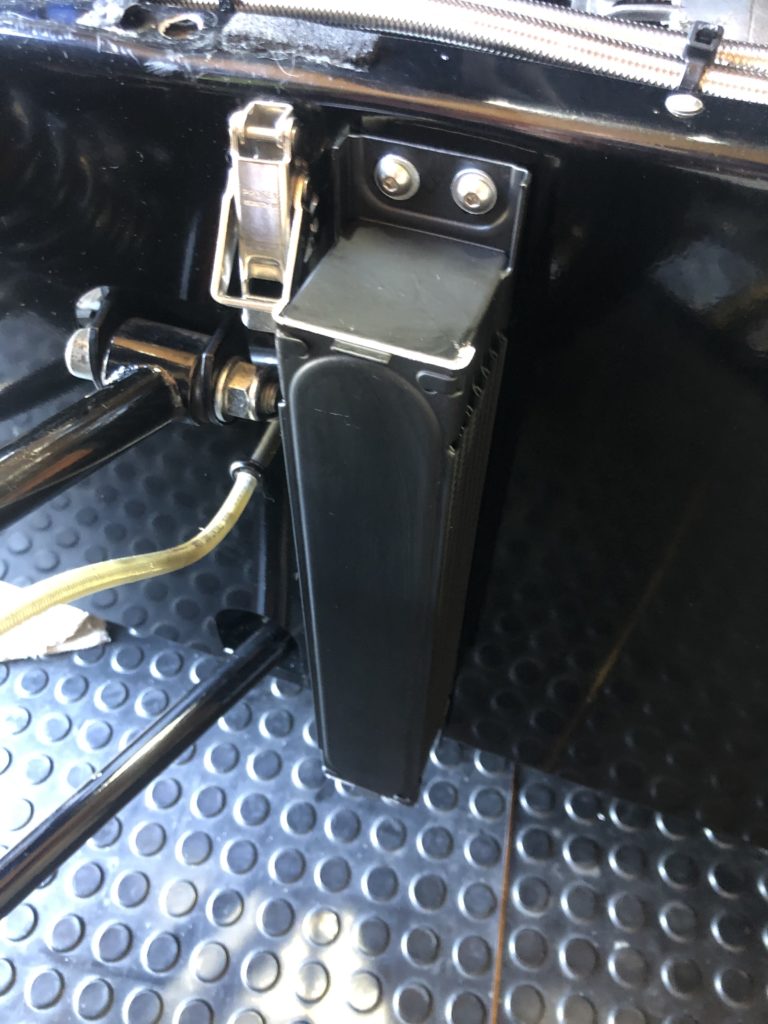
01.NOVEMBER 2020
Ich habe heute an Allerheiligen meine Ölwanne ausgebaut und diese nach einer sorgfältigen Reinigung wieder montiert. Ich habe beide Dichtflächen, am Motorblock und an der Ölwanne, mit Nitro – Verdünnung, sehr sorgfältig gereinigt, damit diese absolut fett und ölfrei sind. Das Dichtmittel habe ich wie im Reparaturhandbuch beschrieben in einer 3 mm Raupe sorgfältig aufgetragen. Anschließend habe ich die Ölwanne wieder montiert und die Befestigungsschrauben über Kreuz mit 15 Nm angezogen. Ich hoffe dass die Ölwanne nun dicht ist. Ich habe jedoch nicht wieder das weiße VW/AUDI Dichtmittel verwendet. Dieses Dichtmittel bildet bereits nach 5 Minuten eine Haut und die Ölwanne sollte innerhalb dieser Zeit montiert sein. Für mich ohne Hebebühne ist das nicht zu schaffen. Aus diesem Grund habe ich als Dichtmittel Dirko HT grau verwendet.
Hier die Vorgeschichte:
Bei der Montage der Ölwanne am 14. August 2020 ist mir leider ein Fehler unterlaufen. Nach dem Ausbau der Ölwanne sollte man vor dem Auftragen des Dichtmittels die Dichtflächen sorgfältig reinigen. Diese müssen absolut fettfrei und ölfrei sein. Ich hatte beide Dichtflächen, an der Ölwanne und am Motorblock, sorgfältig gereinigt. Aber leider mit dem falschen Produkt. Ich hatte damals Terpentin – Ersatz genommen, ohne zu wissen dass dieses Öle enthält. Also habe ich, anstatt die Dichtflächen fettfrei zu machen, diese sehr sorgfältig mit Öl eingerieben. Mit dem Resultat, dass das Dichtmittel nicht richtig abdichten konnte und meine Ölwanne Öl verlor.
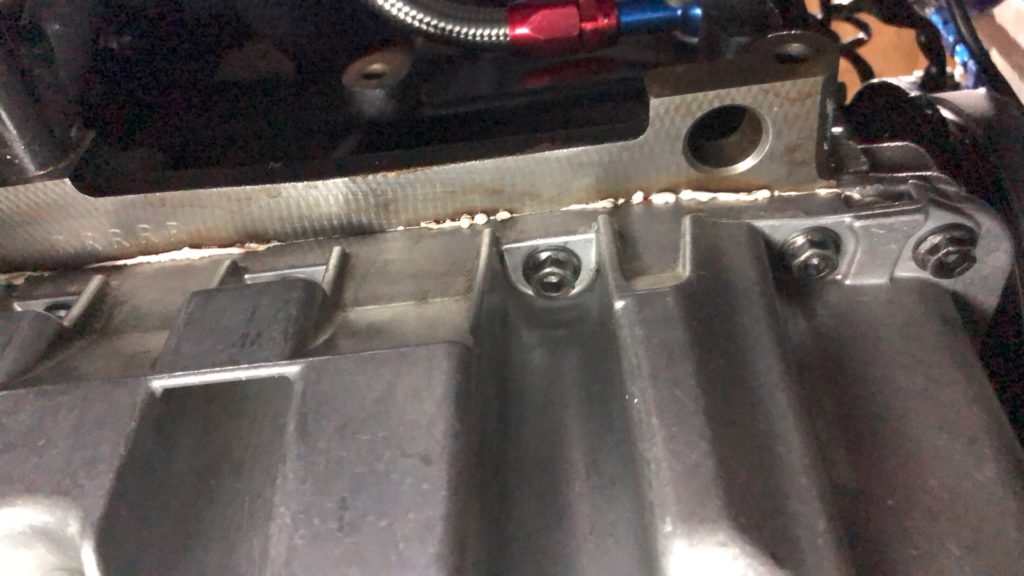
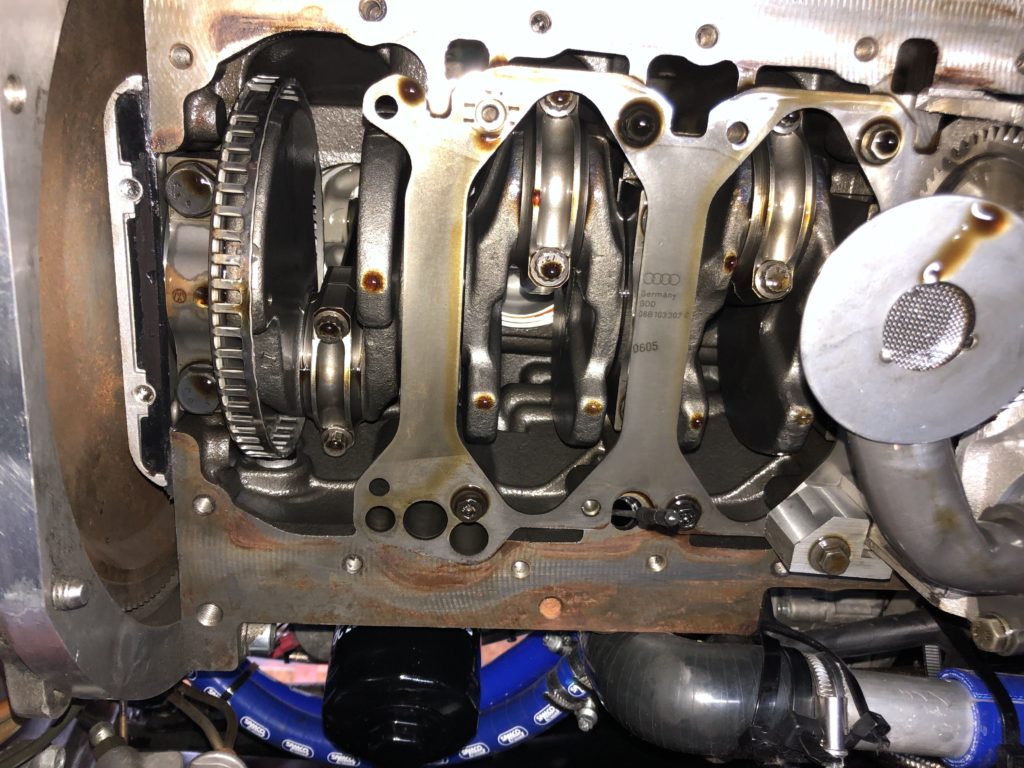
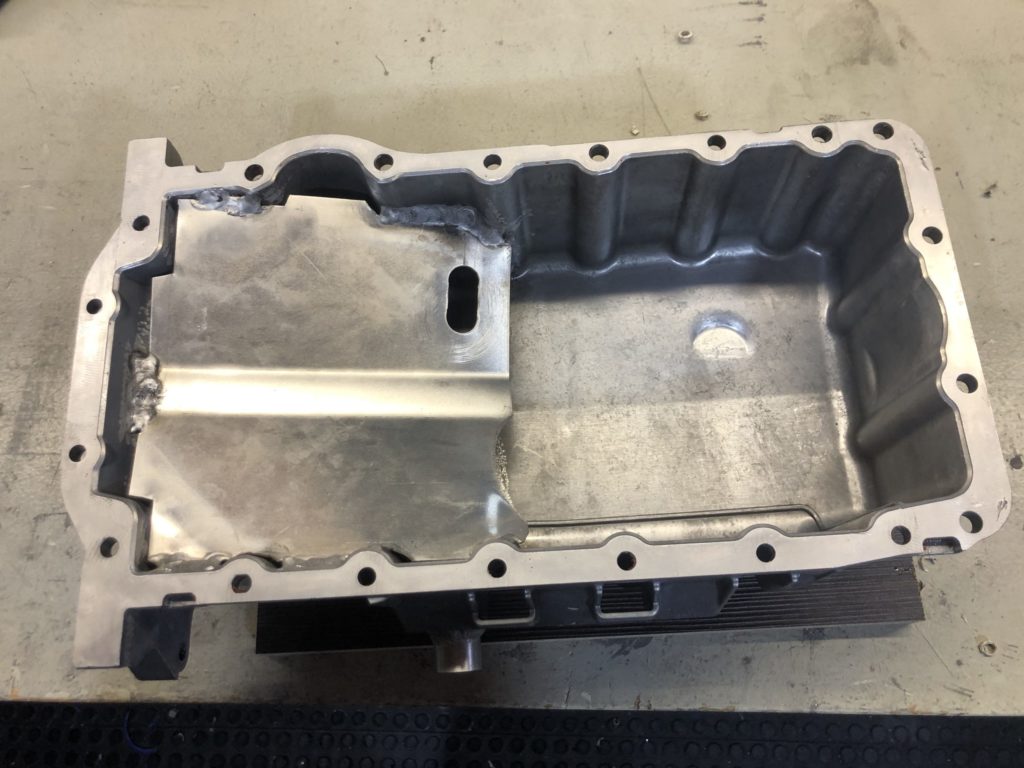
11. SEPTEMBER 2020
Als ich die beiden Ölkühler mit den Ölleitungen in Dash 10 verrohren wollte, musste ich meine Lima, wegen dem akuten Platzmangel auf der linken Seite, ausbauen. Der original verbaute „Keilriemenspanner“, wenn man die beiden Flacheisen aus Aluminium so nennen kann, am Lichtmaschinenträger, gefiel mir nicht. Ein anständiges Spannen des Keilriemens war fast nicht möglich. Des Weiteren war das Gewinde, welches die Befestigungsschraube des Keilriemenspanners am Lichtmaschinenträger halten sollte, so sehr beschädigt, so dass ich fast 3 Stunden benötigte diese Befestigungsschraube zu lösen. Das wollte und konnte ich auf keinen Fall so lassen und so beschloss ich den kompletten Lichtmaschinenträger auszubauen und mir einen anderen Keilriemenspanner zu bauen.
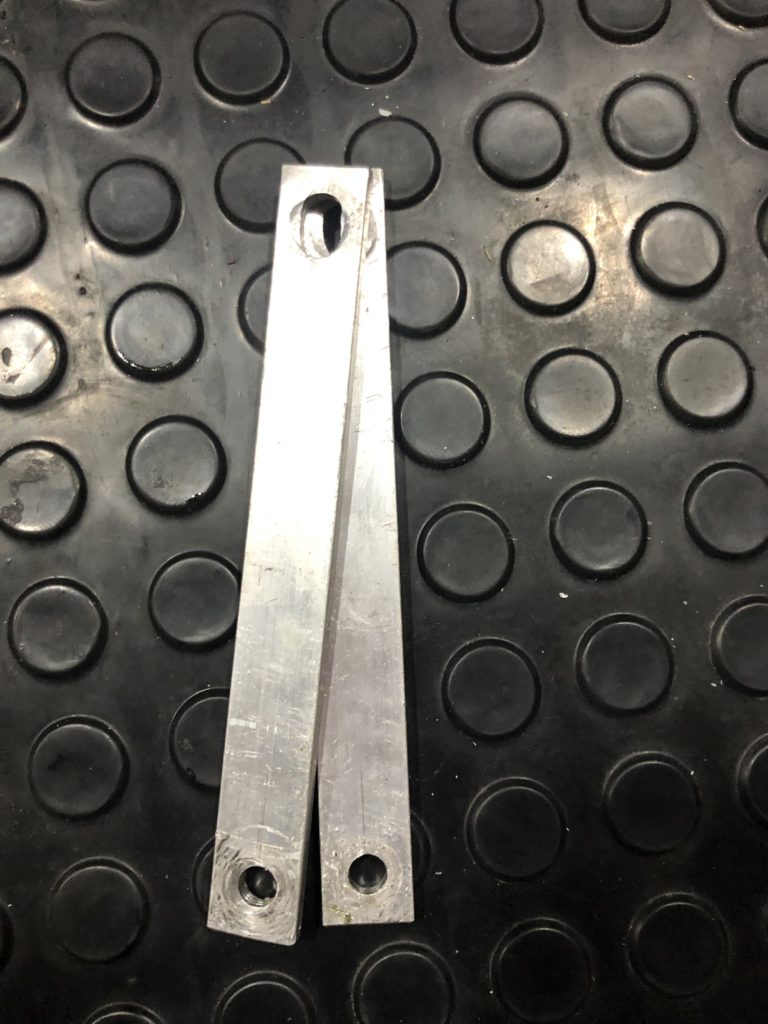
Auf dem Foto oben ist der Keilriemenspanner, der im HKT eingebaut war, zu sehen.
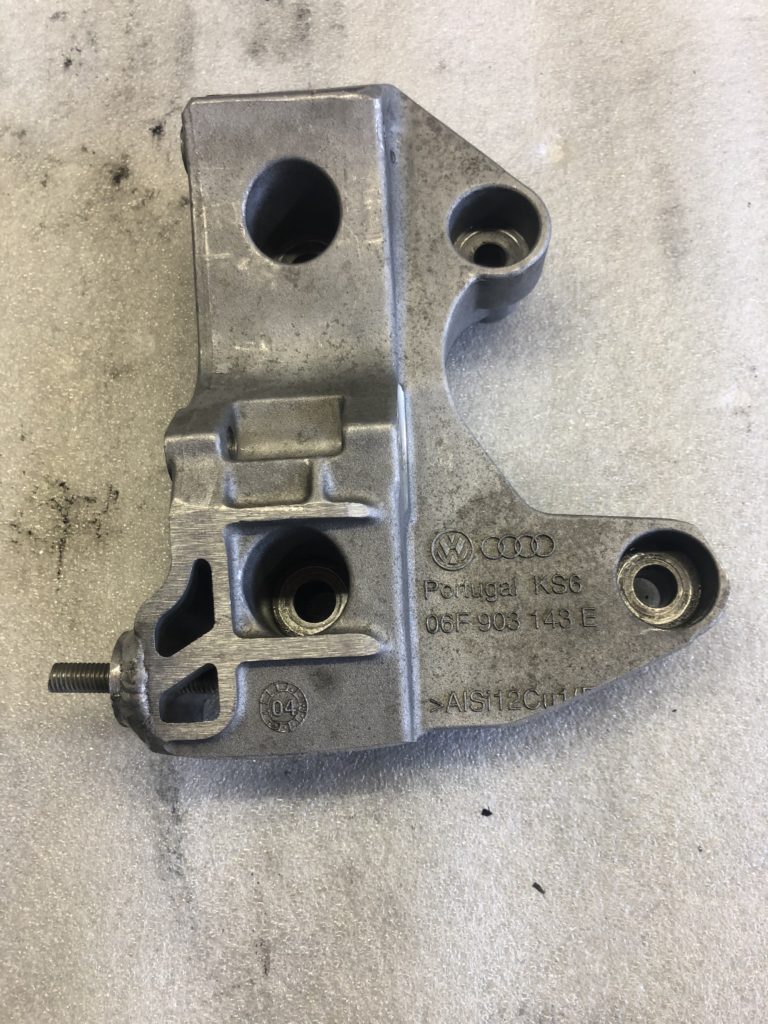
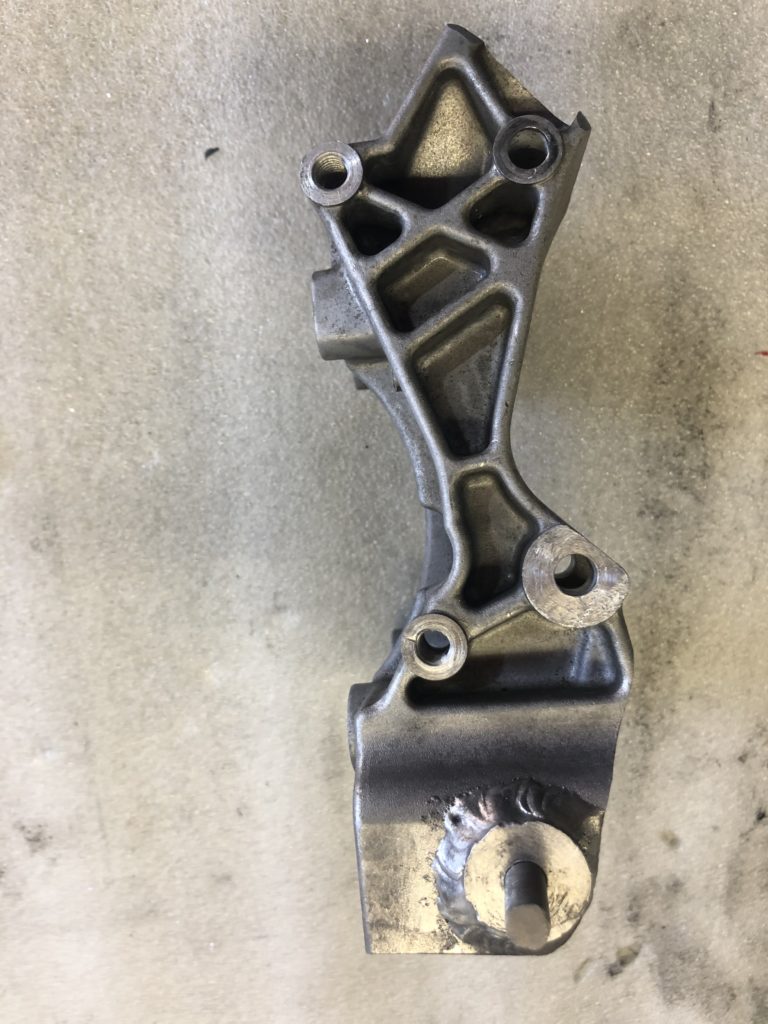
Der Gewindestift wurde an der Rückseite des Limaträgers neu befestigt.
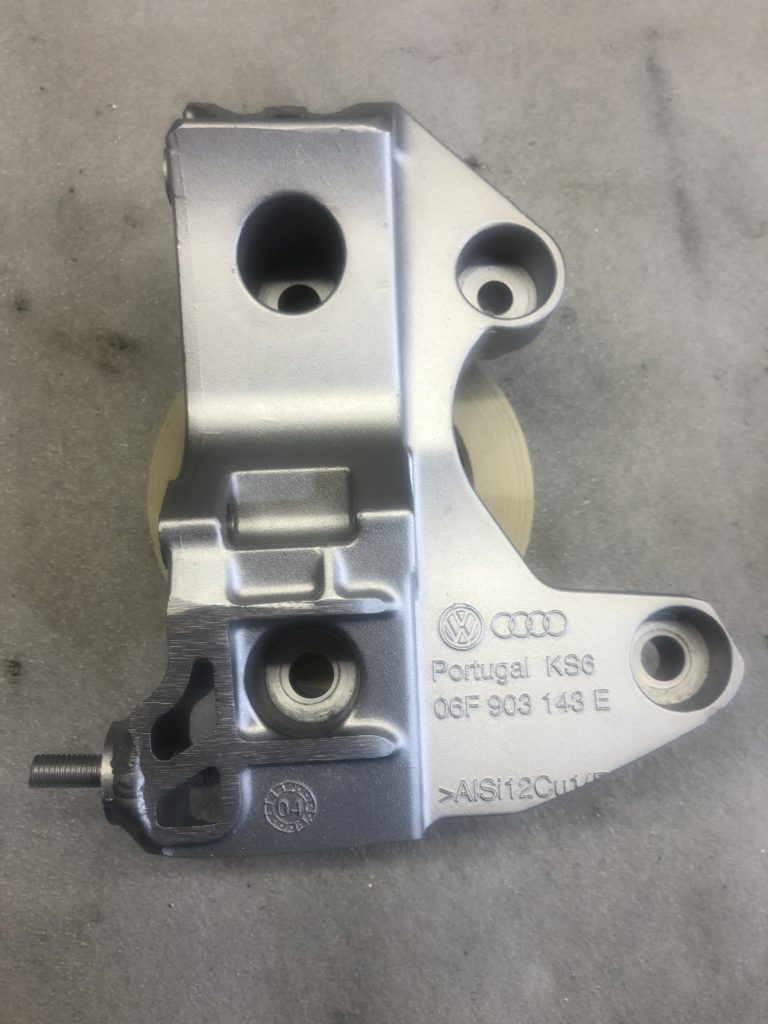
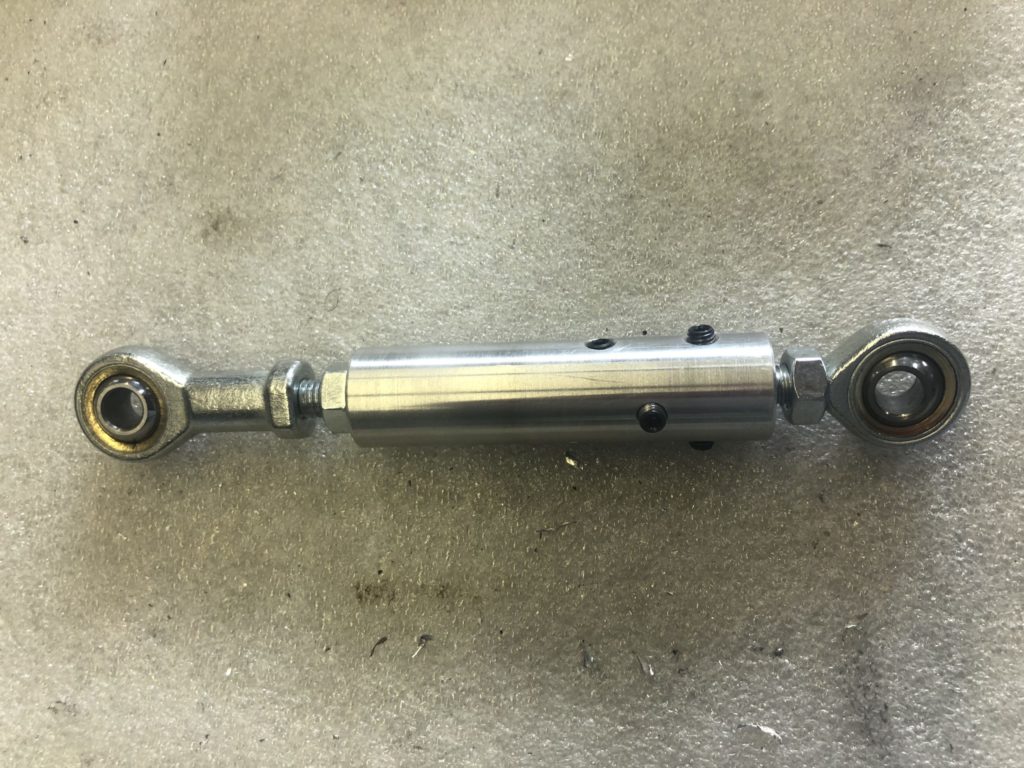
Auf dem Foto oben erkennt man den neuen Keilriemenspanner. Ich habe diesen aus einem Aluminiumstab von 20 mm Durchmesser hergestellt. Verwendet habe ich des Weiteren 2 Gelenke in 8mm mit M8 Innen und Aussengewinde.
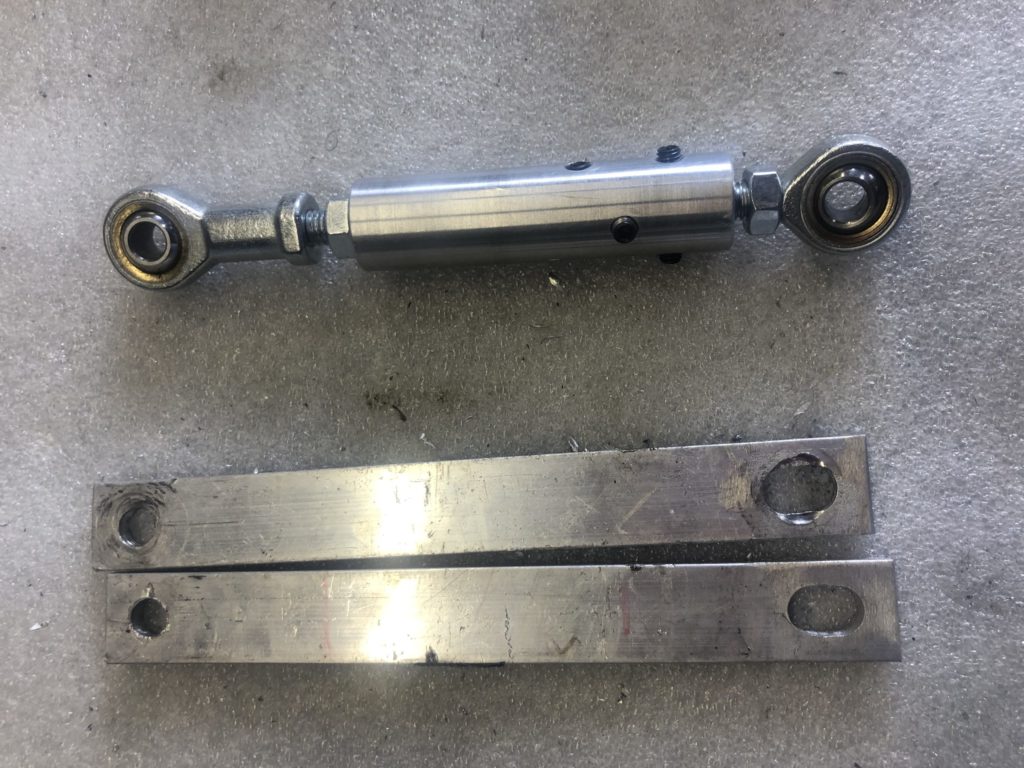
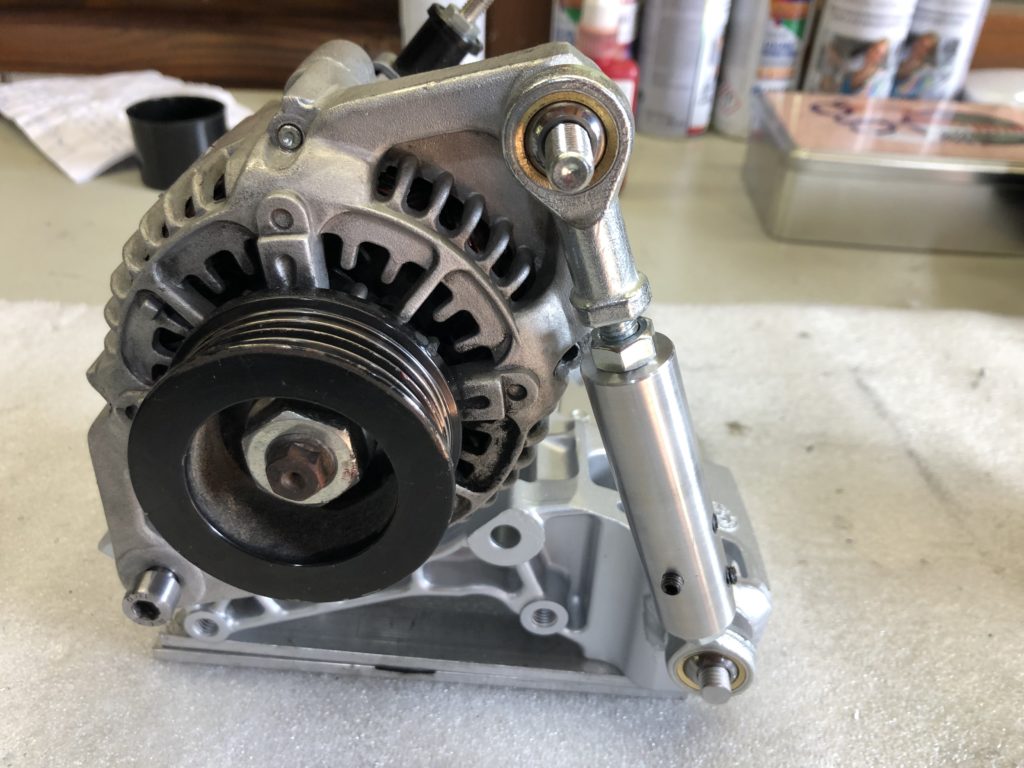
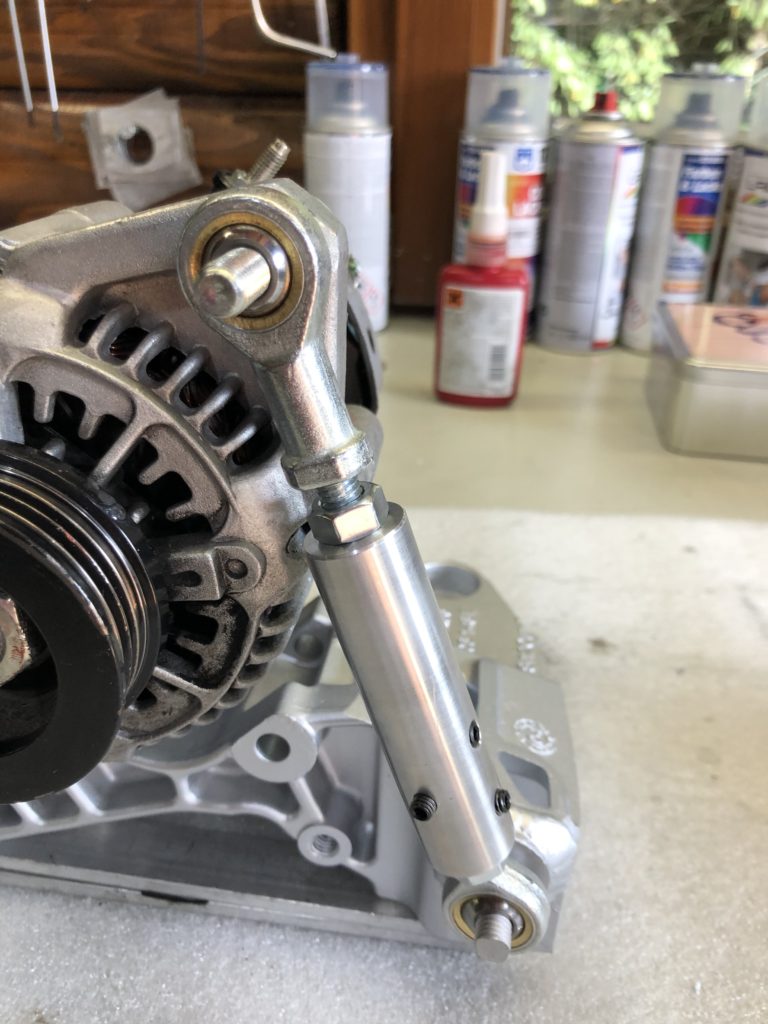
Das Ganze habe dann ich provisorisch lose zusammen gebaut. Dabei fiel mir auf dass sich die Lichtmaschine, ohne die vielen Karosseriescheiben die verbaut waren, 10 mm in jede Richtung bewegen konnte. Die vielen Karosseriescheiben wollte ich nicht mehr einbauen und so fertigte ich mir auf meiner Drehbank ein passendes Distanzstück an.
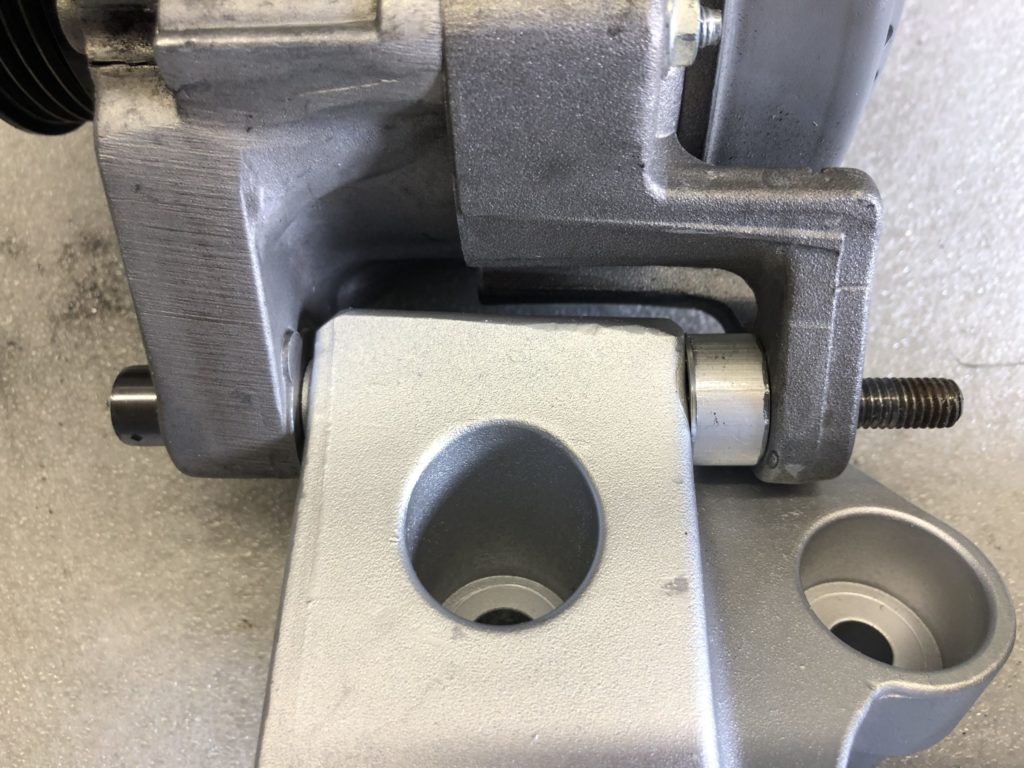
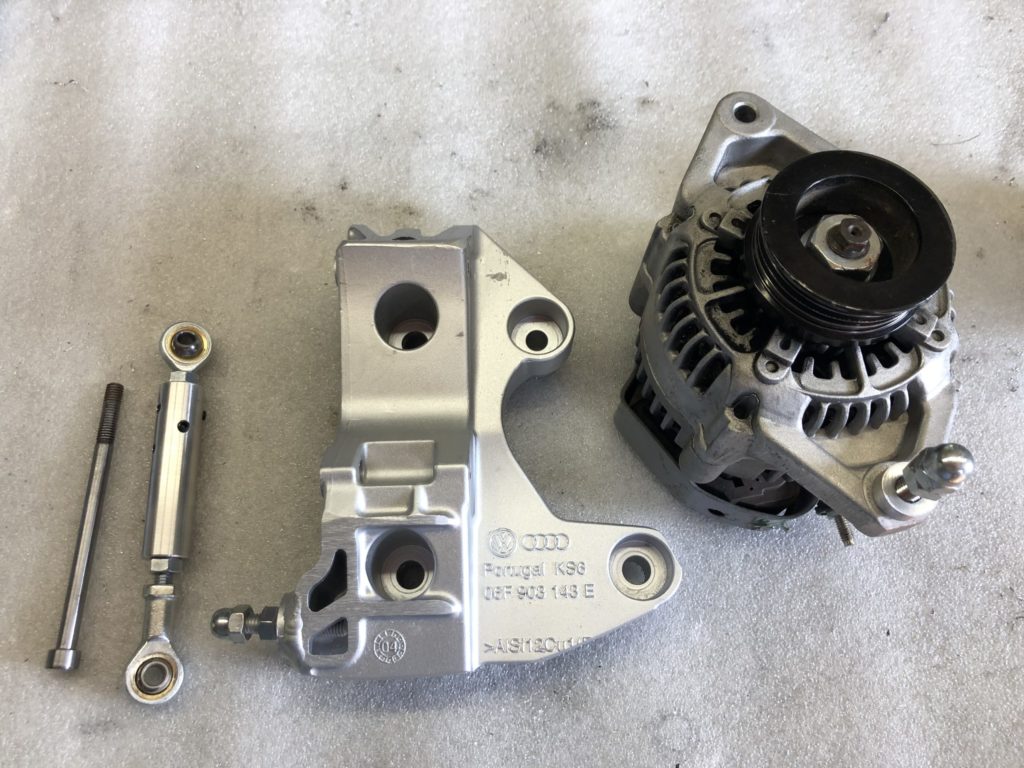
09. SEPTEMBER 2020
Es sind nun 9 Tage seit meinem letzten Eintrag vergangen. Der Ölkühler am Luftfiltergehäuse hätte funktioniert, aber ich konnte die Ölleitungen, wegen dem akuten Platzmangel, nicht fachgerecht anschließen. Also habe ich alles verworfen. Ich habe es in der Rubrik “ Lehrgeld bezahlt “ eingetragen. Was soll ich sagen, ich habe eine andere Lösung gewählt, eine Lösung die ich so, in der Form, nie mochte. Aber es ist die einzige gute Möglichkeit die Öltemperatur in den Griff zu bekommen.
Aber so einfach wie es auf den Bildern vielleicht aussieht, war es jedoch nicht. Meine Seitenpanel sind nicht teilbar wie bei anderen HKT. Das hätte die Sache bedeutend einfacher gemacht. So musste ich viele Teile, wie die Lichtmaschine, zuerst ausbauen. Aber am Ende stellte sich der Lichtmaschinenausbau als genau richtig heraus. Aber dazu kommen wir später.
Verbaut habe ich 2 Stück Setrab Pro Line 6 Ölkühler mit 7 Reihen.
Angefangen habe ich mit den Schablonen, die ich mir extra angefertigt habe. Eine Schablone mit 4 mm Bohrungen und eine Schablone mit den 38 mm Bohrungen für die Ölkühler. An dieser Schablone konnte ich testen ob meine Masse alle korrekt sind und die Ölkühler so in die Bohrungen passen.
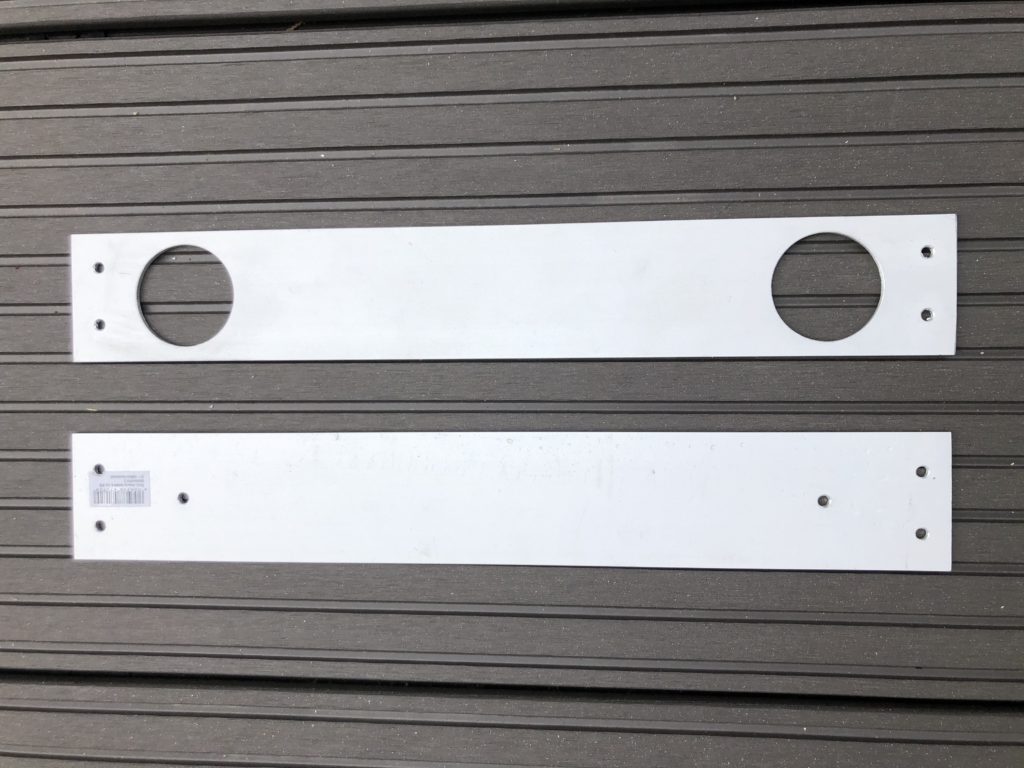
Die Schablone mit den 4 mm Bohrungen wurde an der Karosserie, die vorher mit Tesakrepp abgeklebt wurde, angepasst und genau ausgerichtet.
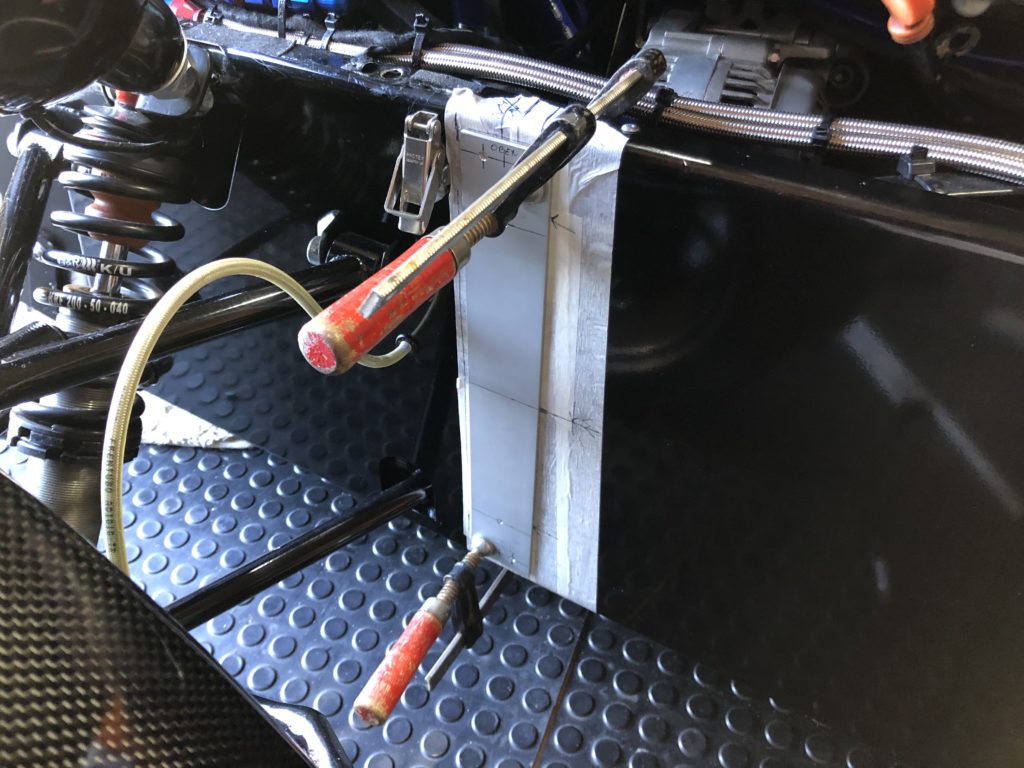
Anschließend wurde alle Bohrungen mit einem 4 mm Bohrer hergestellt.
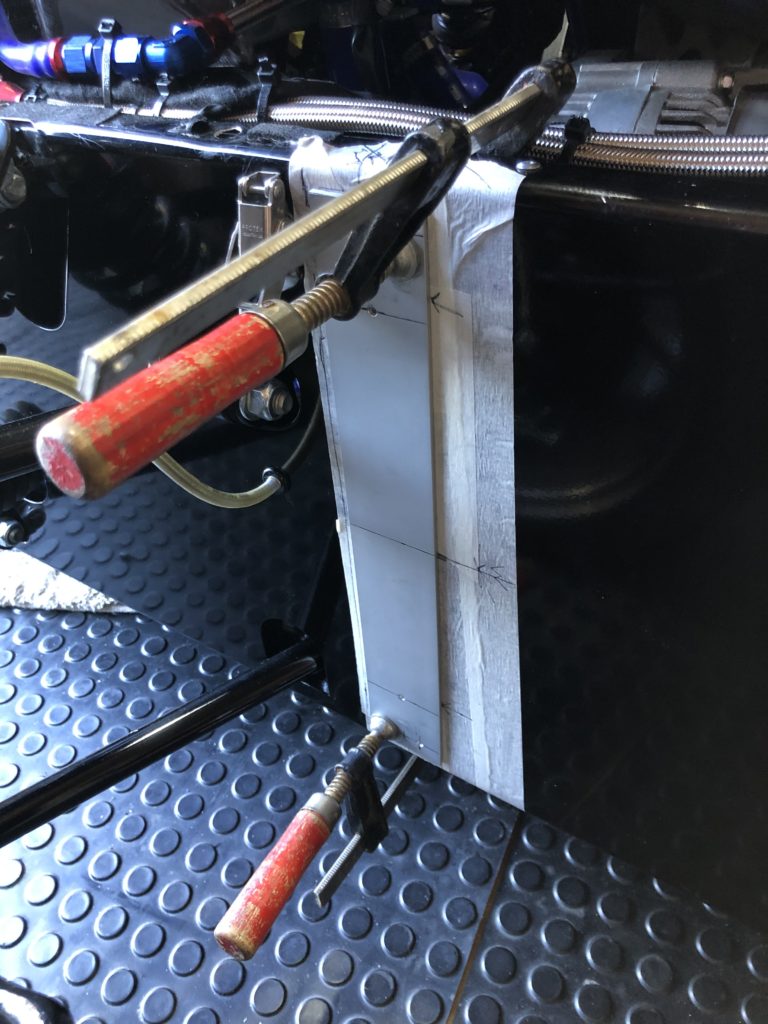
Danach wurde die Schablone entfernt und an Hand der Bohrungen konnte ich die 38 mm Rundlöcher mit einer Lochfräse sauber herstellen.
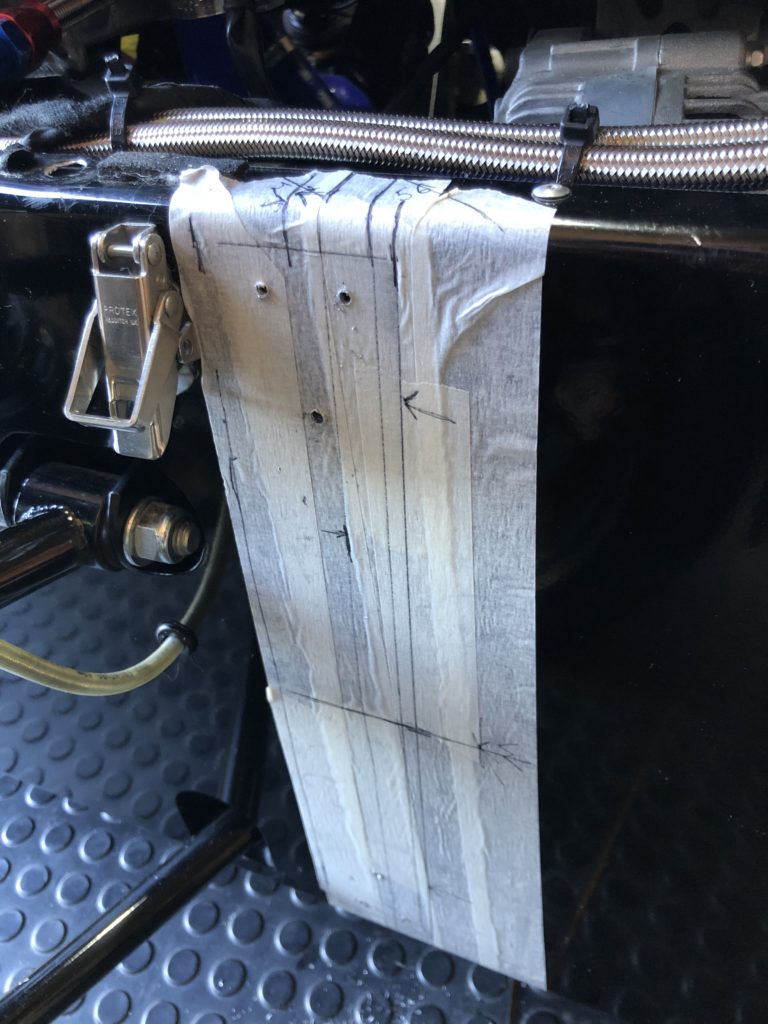
Es kostet einen schon eine Menge Überwindung die großen Rundlöcher in das tolle Seitenpanel zu bohren.
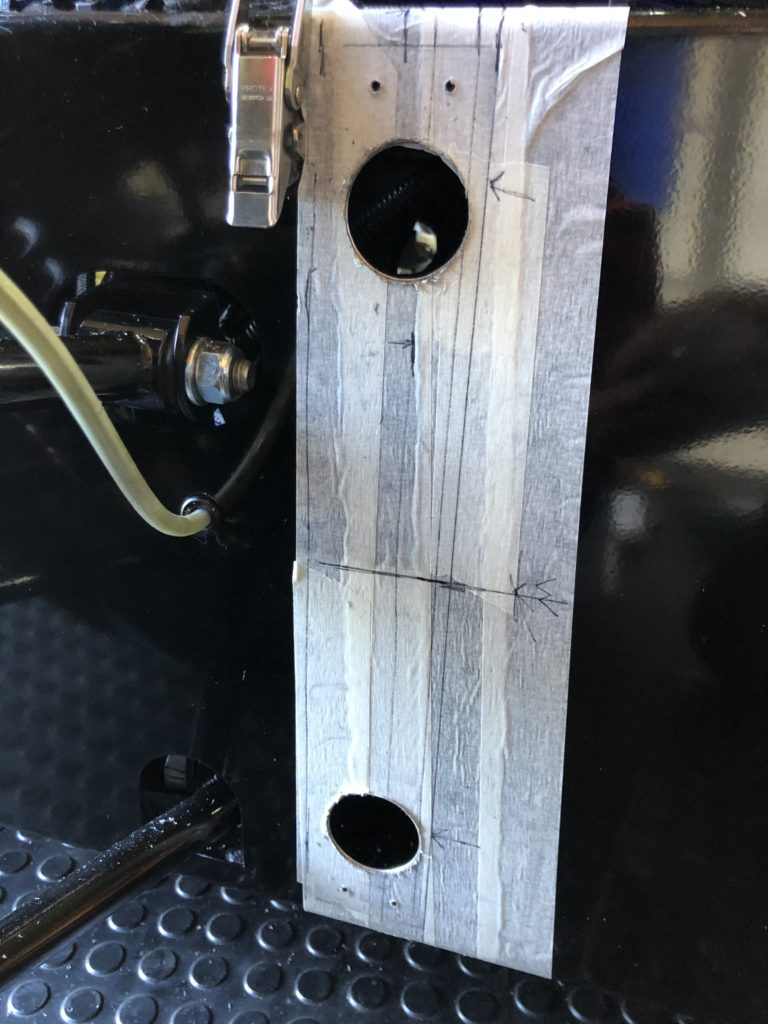
Dann konnte das Tesaband entfernt werden und das Seitenpanel wurde vor der Montage der beiden Ölkühler sorgfältig poliert. Ich bin einfach überzeugt dass wenn der Arbeitsplatz immer sauber gehalten wird, die Arbeit auch sauber ausgeführt werden kann.
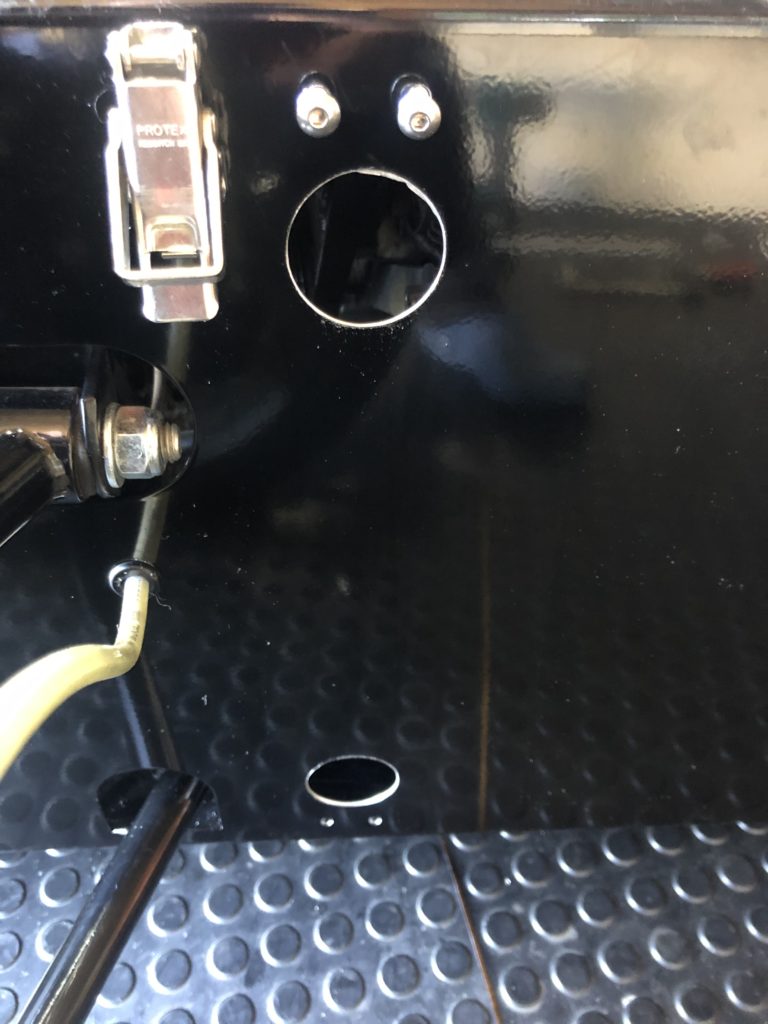
Der Ölkühler, ein Setrab Pro Line 6 mit 7 Reihen, ist montiert. Oben am Ölkühler habe ich 2 Stück M5 Gewindebohrungen im Rahmen hergestellt. Unten habe ich 2 Stück M5 Schrauben mit M5 Sicherheitsmuttern verwendet. Die beiden Befestigungsflansche am Ölkühler habe ich sauber entfernt. Die Stelle wird noch schwarz lackiert…….
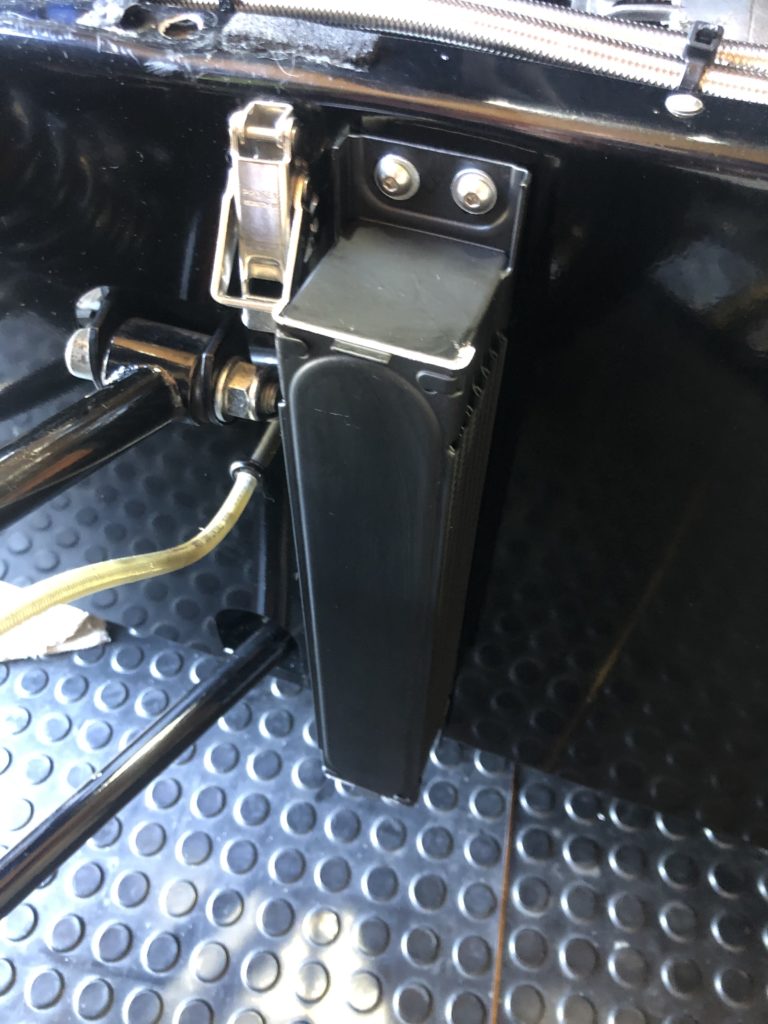
Der Ölkühler auf der linken Seite ist fertig montiert, nun geht es weiter auf der rechten Seite.
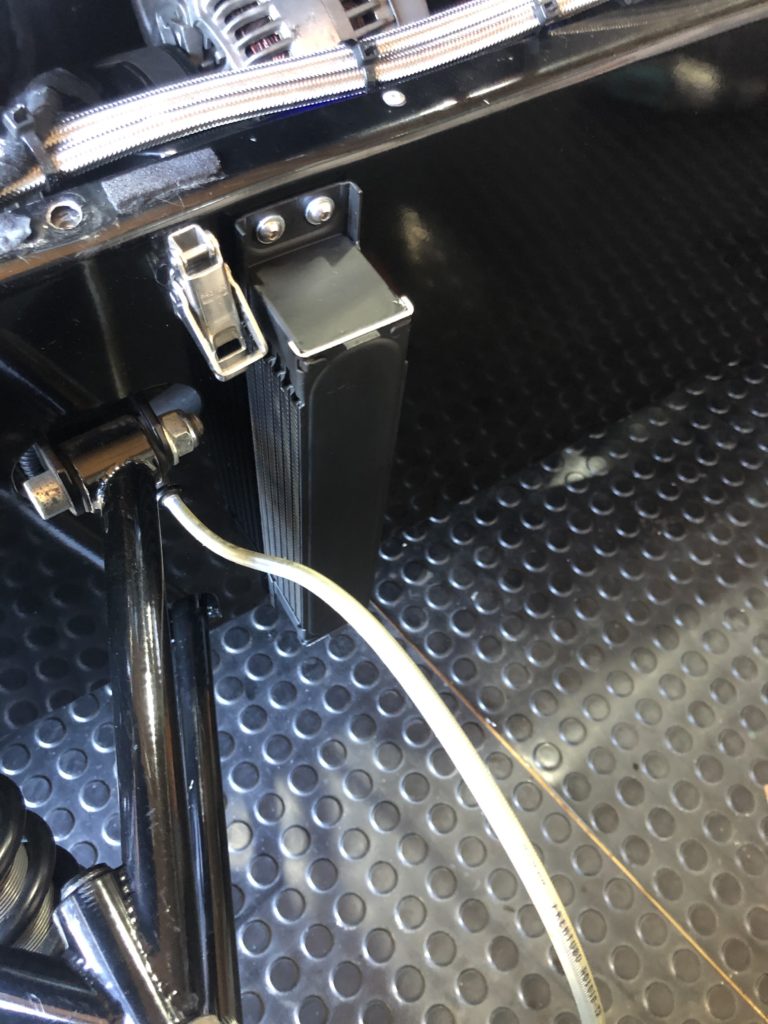
Die beiden Ölleitungen am Ölfiltergehäuse sind fertig angeschlossen. Der rote Dash 10 Fitting am Abgang des Ölfiltergehäuses ist die Ölvorlaufleitung. Der blaue Fitting ist die Ölrücklaufleitung. Der Ölvorlauf wurde am rechten Ölkühler oben angeschlossen. Vom rechten Ölkühler unten geht eine Ölleitung zum linken Ölkühler oben. Vom linken Ölkühler unten geht es wieder zurück zum Ölfiltergehäuse, an den Ölrücklauf, blauer Fitting.
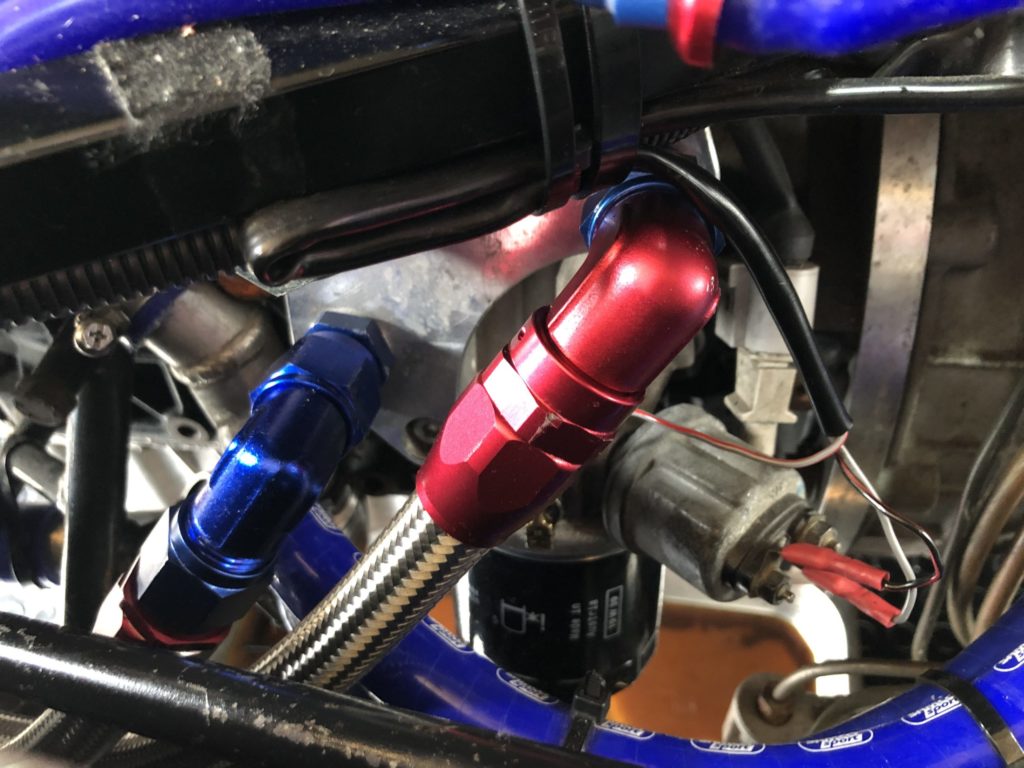
Hier erkennt man den Ölkühleranschluss auf der rechten Seite oben am Ölkühler. Zum Schluss habe ich alle Ölleitungen und Ölkühler noch mit Öl aufgefüllt.
WICHTIG: Ich habe bewusst alle Ölleitungen die zu den beiden Ölkühlern führen und beide Ölkühler, mit Öl vor gefüllt. Insgesamt habe ich so um die 1,3 – 1,5 Liter Öl in die Ölleitungen und in die beiden Ölkühler links und rechts eingefüllt. Das ist wichtig damit beim Ölwechsel der Öldruck schneller ansteht.
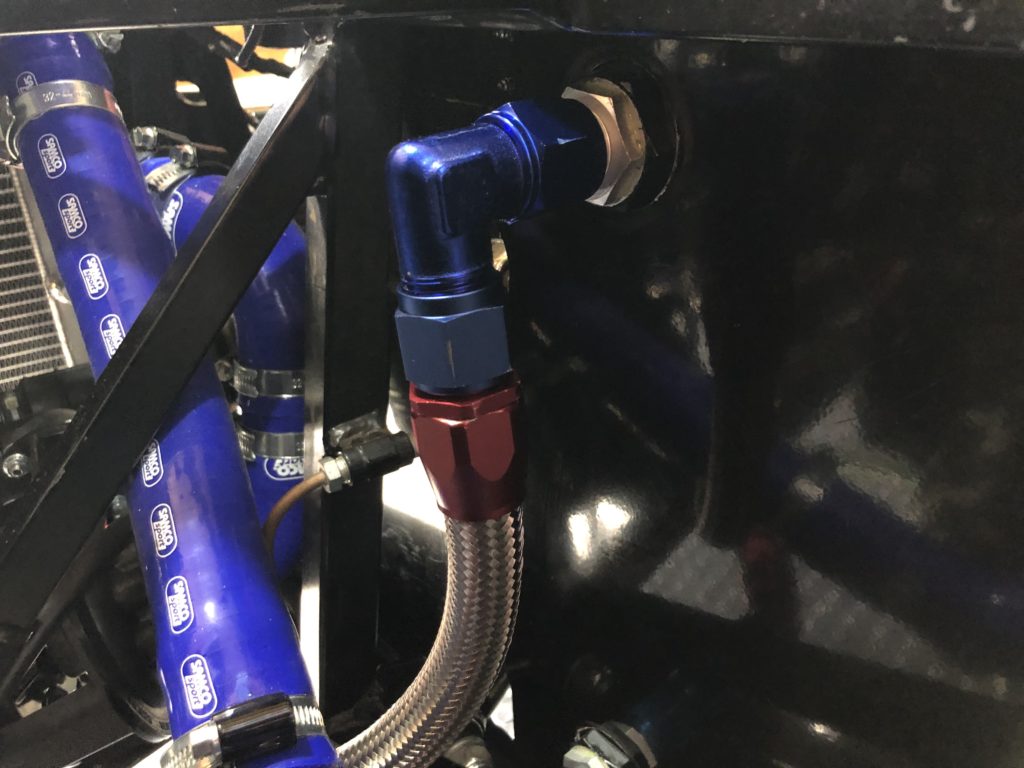
31. AUGUST 2020
Wie bereits an anderer Stelle geschrieben habe ich mir einen zweiten Ölkühler eingebaut. Fahrversuche haben ergeben dass ich die Öltemperatur mit dem zusätzlichen kleineren Setrab Ölkühler um fast 15° senken kann. Der von HKT verbaute originale Ölkühler befindet sich hinter dem Motorkühler und dem NT – Kühler des WLLK. Durch den Einbau eines grösseren Motorkühlers und dem NT – Kühler wird der Ölkühler nicht mehr optimal von der kalten Aussenluft durchströmt. Das Resultat ist, dass die Öltemperatur bei flotter Fahrt auf 110° -115° ansteigt. Zwei zusätzliche Ölkühler außen links und rechts anzubringen war für mich keine Option. So kam ich zu der Ideeeinen zusätzlichen Ölkühler vorne unterhalb der Nase unterzubringen.
Die Ölleitung mit der Ringöse am Ölfilterhalter wurde abgebaut und durch einen Dash 10 Adapter M18 x 1,5 mm ersetzt.

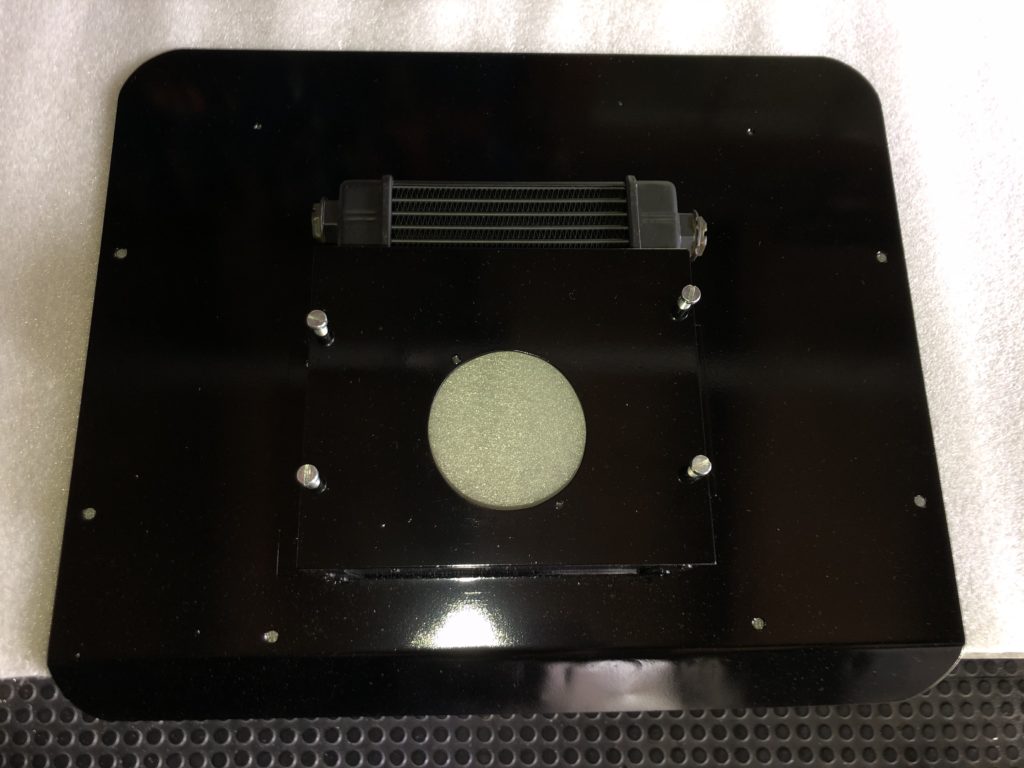
14. AUGUST 2020
Die Ölwanne ist wieder montiert. Die Ölwanne wird mit einem speziellen Dichtmittel von Audi / VW montiert. Nach dem Auftragen des Dichtmittels auf der Ölwanne sollte man zügig arbeiten. Laut Datenblatt muss die Ölwanne dann innerhalb von 5 Minuten montiert sein. Das weiße Silikon – Dichtmittel bildet bereits nach 5 Minuten eine Haut und kann in dem Fall nicht mehr 100% abdichten. Ich habe für eine Kartusche von 80 ml etwas mehr als 25 € bei Audi / VW bezahlt.
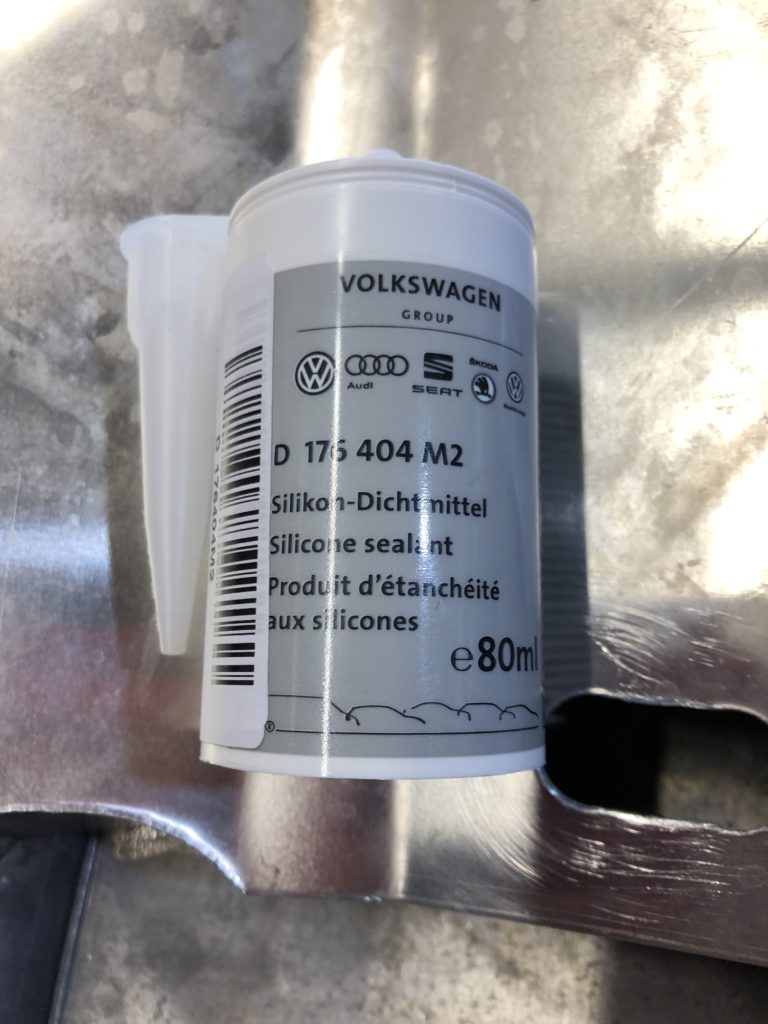
Das Dichtmittel wird auf die saubere Dichtfläche der Ölwanne aufgetragen. Im Bereich des Dichtflansches, am Übergang zwischen dem Motorblock und dem Dichtflansch, muss die Dichtmittelraupe besonders sorgfältig aufgetragen werden.
Die Dicke der Dichtmittelraupe sollte 3 mm nicht übersteigen. Wird die Raupe dicker aufgetragen kann das überschüssige Dichtmittel in der Ölwanne landen und das Ölsieb und die Ölpumpe verstopfen!
Die Ölwanne muss sofort nach dem Auftragen des Dichtmittels eingebaut werden. Dazu die Befestigungsschrauben, 20 Stück, von 1 – 20 über Kreuz mit 5 Nm anziehen. Anschließend die Befestigungsschrauben mit einem Drehmoment von 15 Nm über Kreuz definitiv anziehen.
Nach dem Einbau der Ölwanne sollte man, laut Werkstatthandbuch von Audi, mindestens 20 -40 Minuten warten bevor man wieder Öl einfüllt.
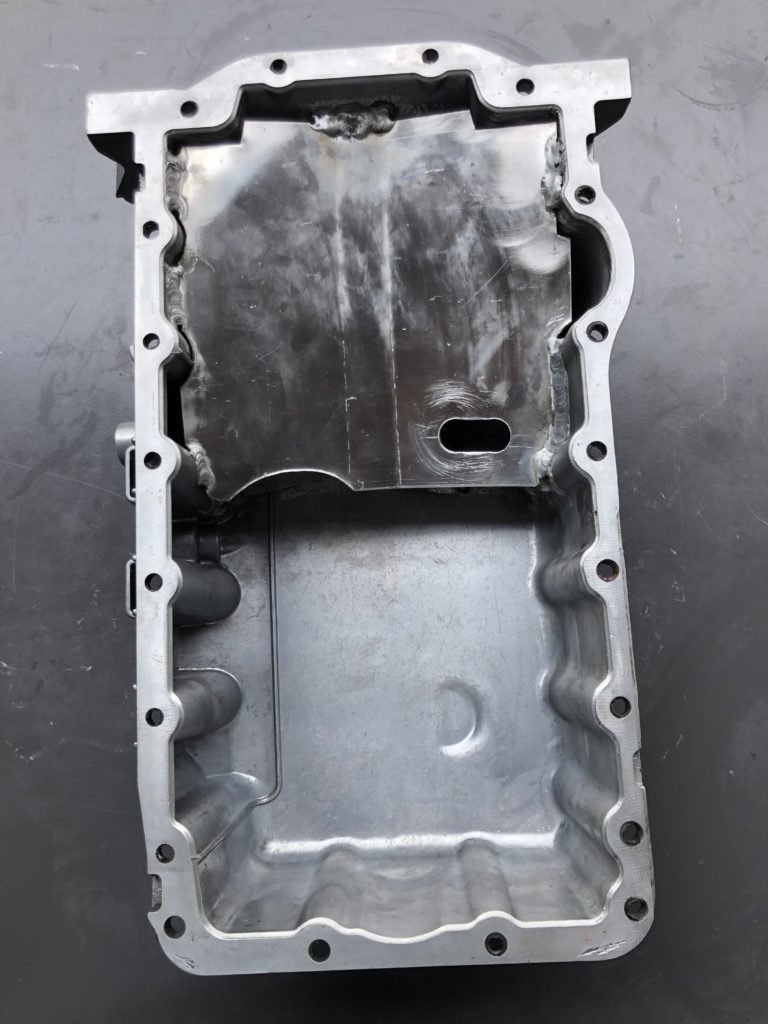
Ich musste auch mein Ölsieb am Ausgleichswellenmodul ausbauen um dieses zu reinigen. Dichtmittelreste und Aluminiumspäne hatten das Ölsieb fast verstopft. Im Ölsieb erkennt man noch einen kleinen roten Punkt, Reste von einem roten Dichtmittel……
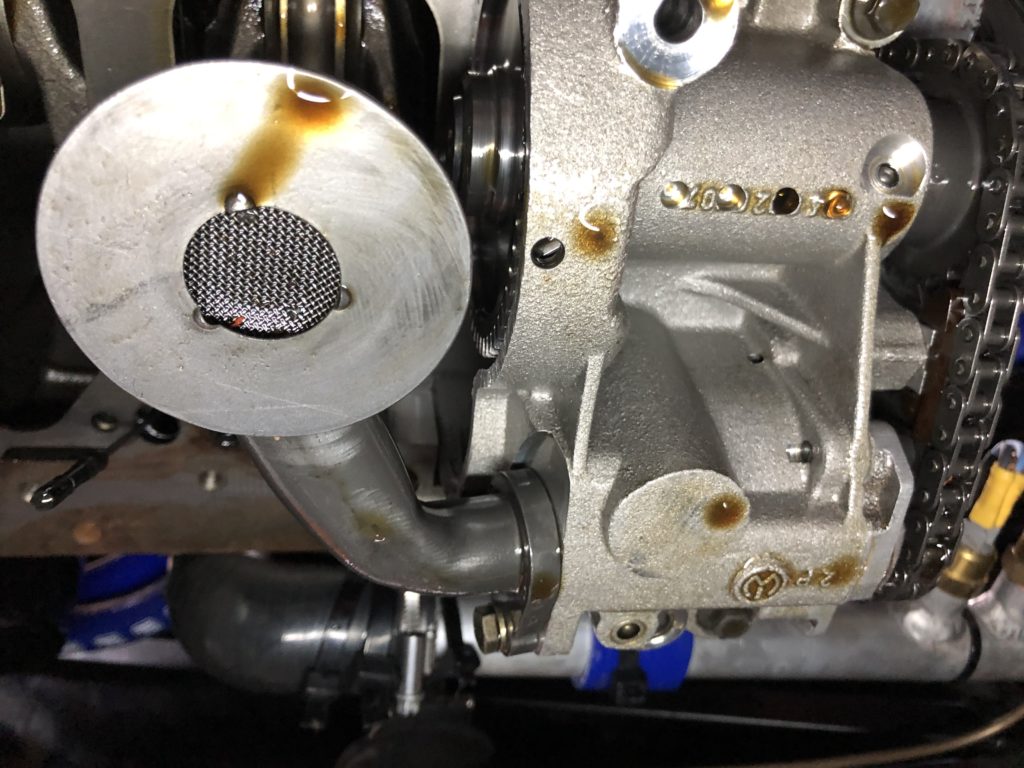
Hier erkennt man einen Teil der Dichtmittelreste und Plastikspäne die ich aus dem Ölsieb und aus der Ölwanne entfernt habe.
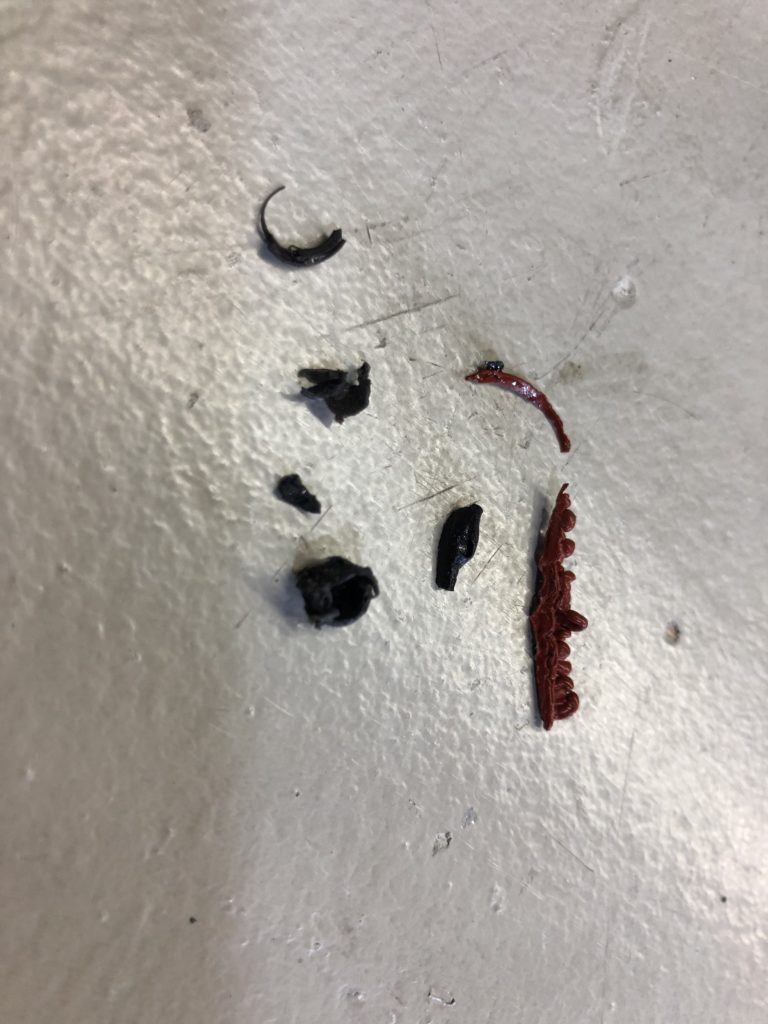
Damit der Ölstandsensor in die umgebaute Ölwanne passt, hat man diesen kurzerhand mit der Flex behandelt. An sich nicht tragisch, dieser Sensor wird nicht benötigt. Aber man hätte wenigstens den Sensor vor dem Einbau reinigen können …… So gelangten die Plastikspäne, die durch das Abschleifen oder Abflexen entstanden sind, in das Ölsieb……..
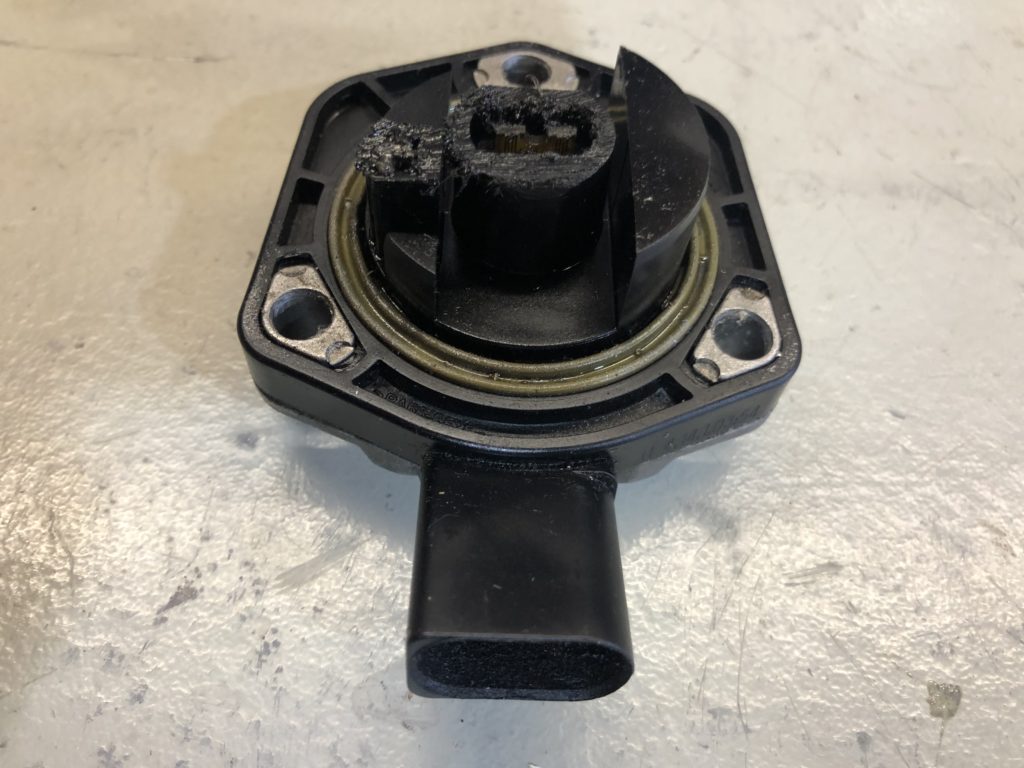
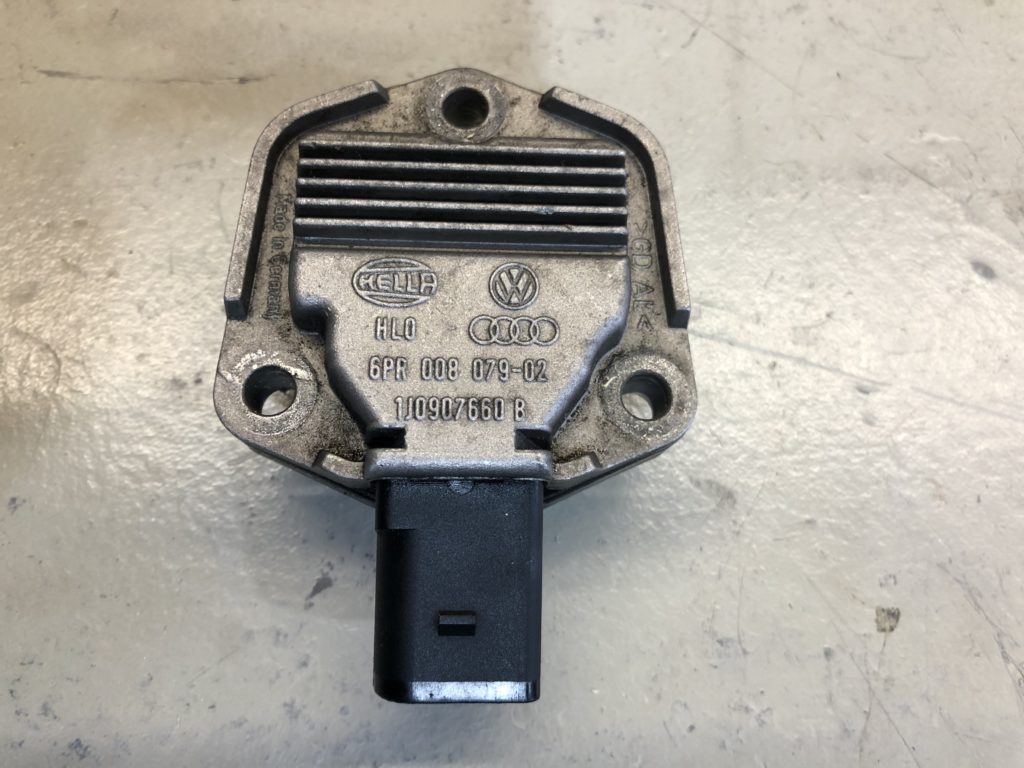
Ich habe, weil ich den Sensor nicht mehr einbauen wollte, mir eine Aluminiumplatte angefertigt. Diese habe ich am Einbauort des Sensors an der Ölwanne montiert.
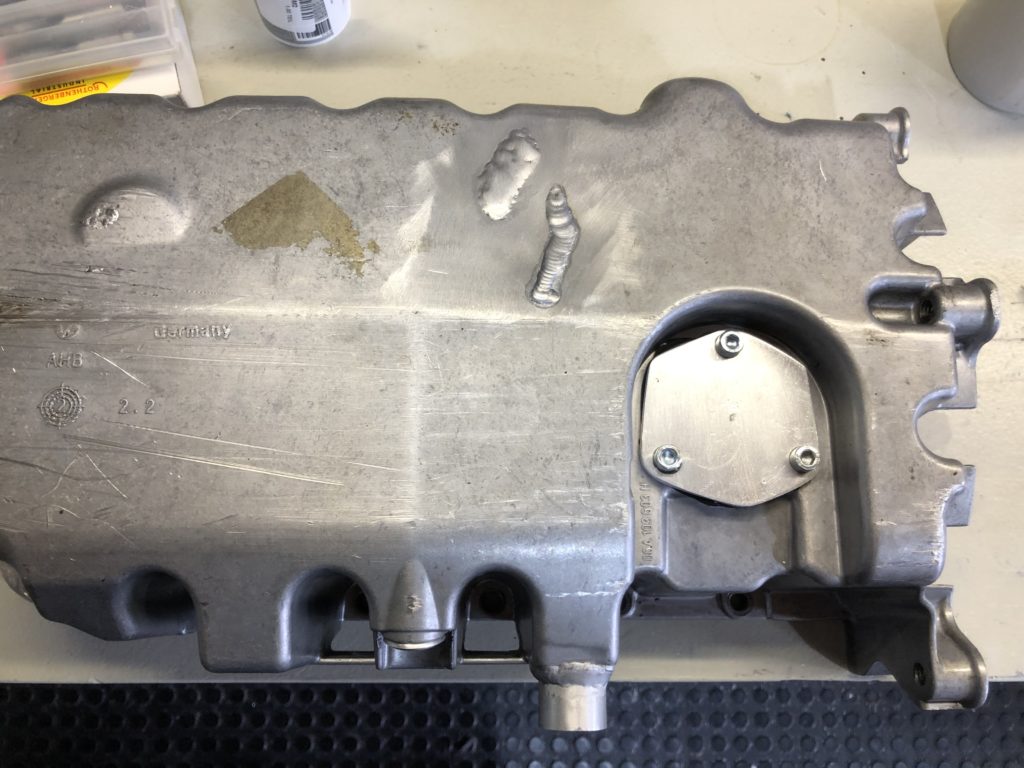
Der Aluminiumdeckel wurde mit 3 Innensechskantschrauben von M 6 X 25 mm , wie beim original verbauten Sensor, an der Ölwanne befestigt.
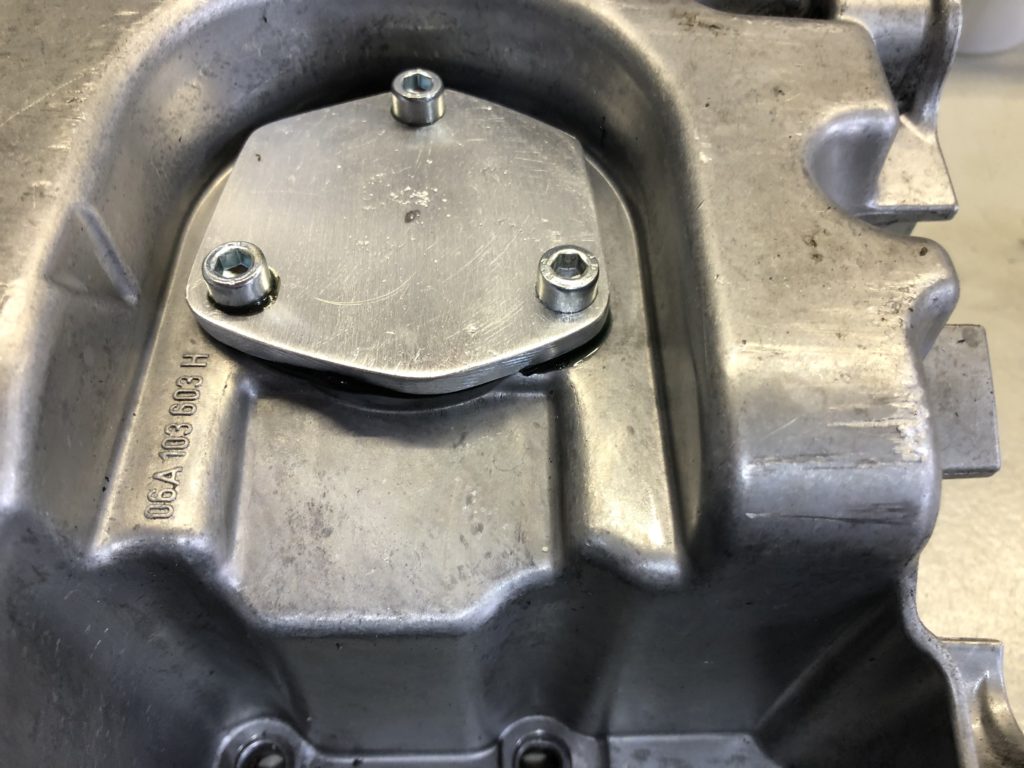
12. AUGUST 2020
Ich habe heute die Ölwanne abgebaut. Ich wollte endlich die Gewissheit haben dass in meinem Motor, für die von mir angestrebte Leistung, die benötigten Komponenten eingebaut sind. Ab einer gewissen Leistung ist mindestens der Einbau von H – Schaft Stahlpleuel absolute Pflicht. Als dann die Ölwanne abgebaut war und ich die verbauten Teile sah, war ich dann doch etwas überrascht. Wenn ich ehrlich bin, damit hatte ich nicht gerechnet.
- H – Schaft Stahlpleuel
- Blockversteifungsplatte
- Halbiertes Ausgleichswellenmodul mit Ölpumpe
Eine anständige Block – Versteifungsplatte, nicht die originale “ Audi Blech – Blockversteifungsplatte “ die in meinem Motor eingebaut ist, verhindert zu große Verwindungen des Kurbeltriebs beim Audi Turbo Motor.
Besonders bei Motoren mit einer höheren Leistungen ab 500 PS, wie beim Turbomotor, neigt die Kurbelwelle zu starken Verwindungen im Bereich vom Motorblock, welche sich auf den gesamten Motor auswirken können und zu kapitalen Schäden an Lagern und Kolben bis hin zum Bruch der Kurbelwelle oder Pleuel führen können!
Die Block – Versteifungsplatte sorgt nicht nur für eine höhere Stabilität im gesamten Motorblock, sondern übernimmt zugleich die Funktion als Ölabscheider.
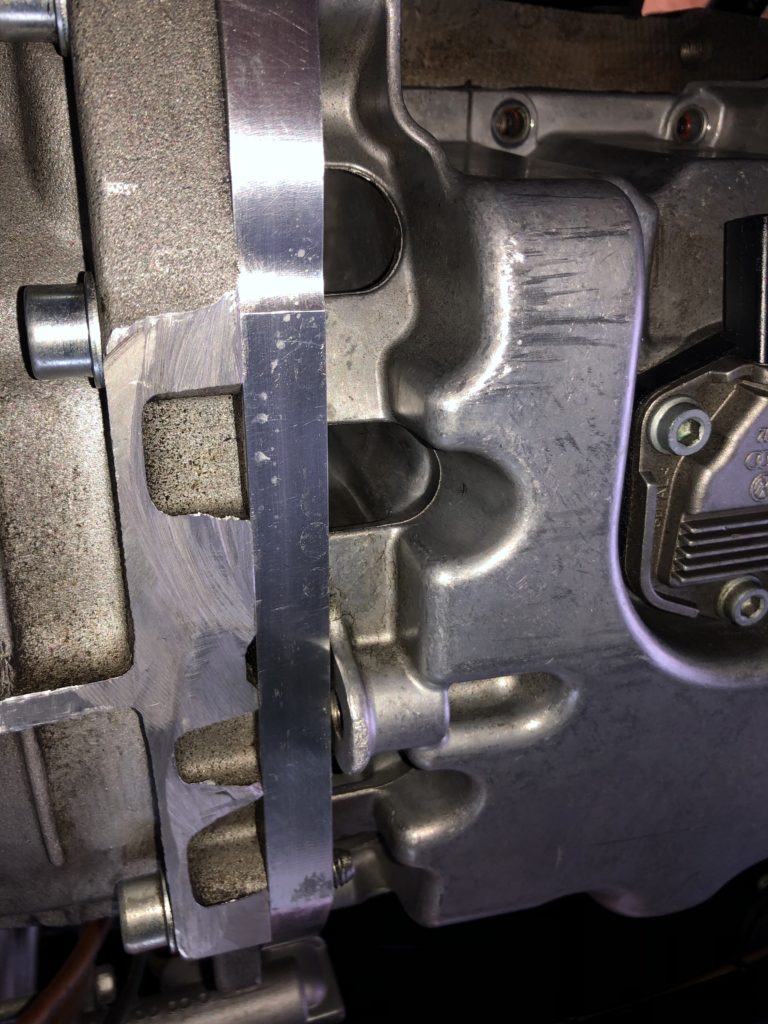
Hier erkennt man sehr gut die Blockversteifungsplatte und die eingebauten H – Schaftstahlpleuel.
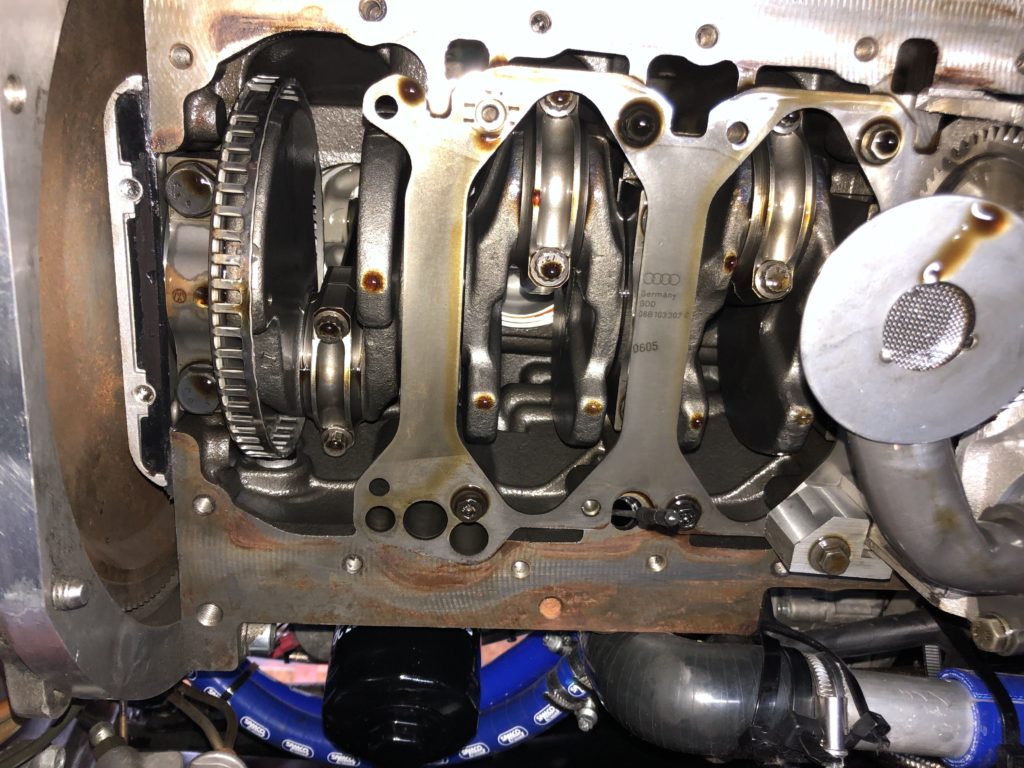
Das halbierte Ausgleichswellenmodul mit Ölsieb, ist hier auf dem Foto zu erkennen.
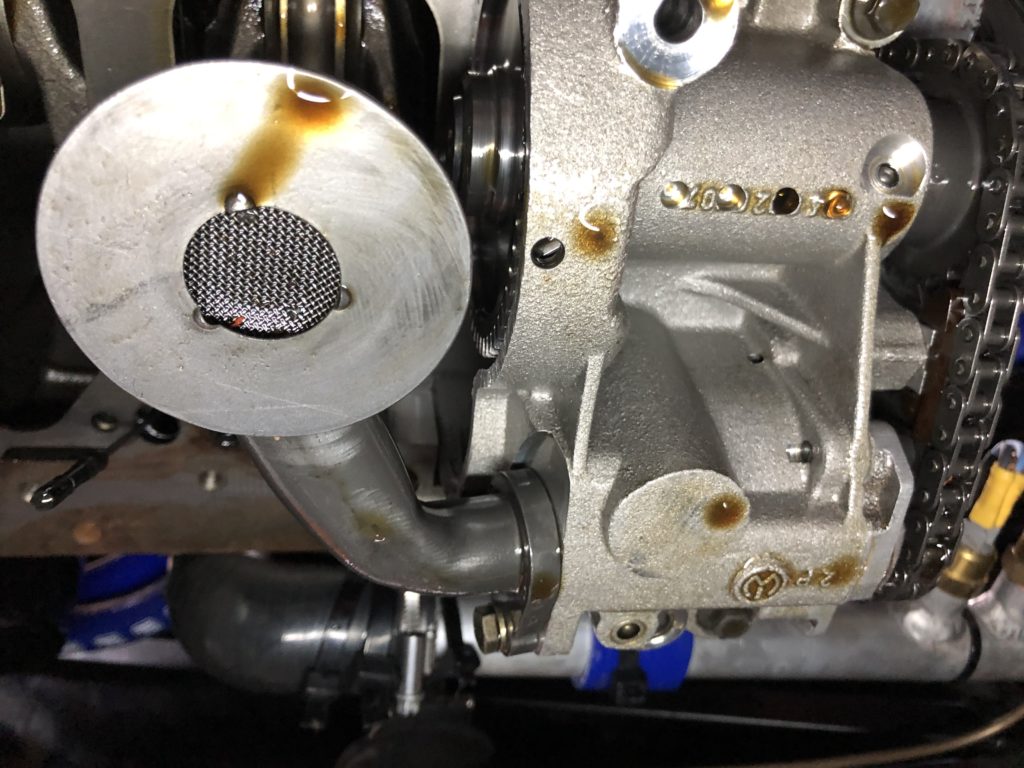
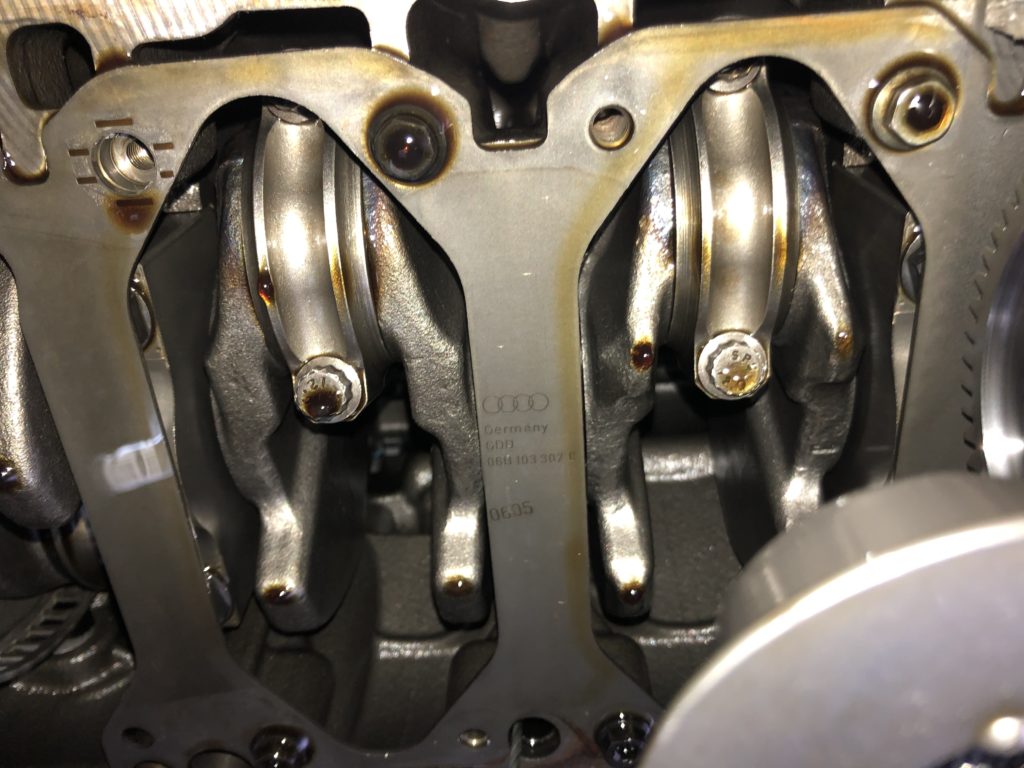
Die ausgebaute Ölwanne ist hier zu sehen. Im Innern der Ölwanne befand sich ein wenig Ölschlamm, Reste der Silikondichtung und leider auch wieder Aluminiumspäne. Grössere und kleinere Aluminiumspäne. Die meisten Aluminiumspäne befanden sich unter dem Schwallblech der Ölwanne, aber auch im Bereich vor dem Schwallblech. Das Langloch, für die Aufnahme des Ölmessstabes war nicht entgratet wie auch das andere Aluminiumblech. Am Ölsieb befanden sich Reste einer Silikondichtung aber auch Aluminiumspäne.
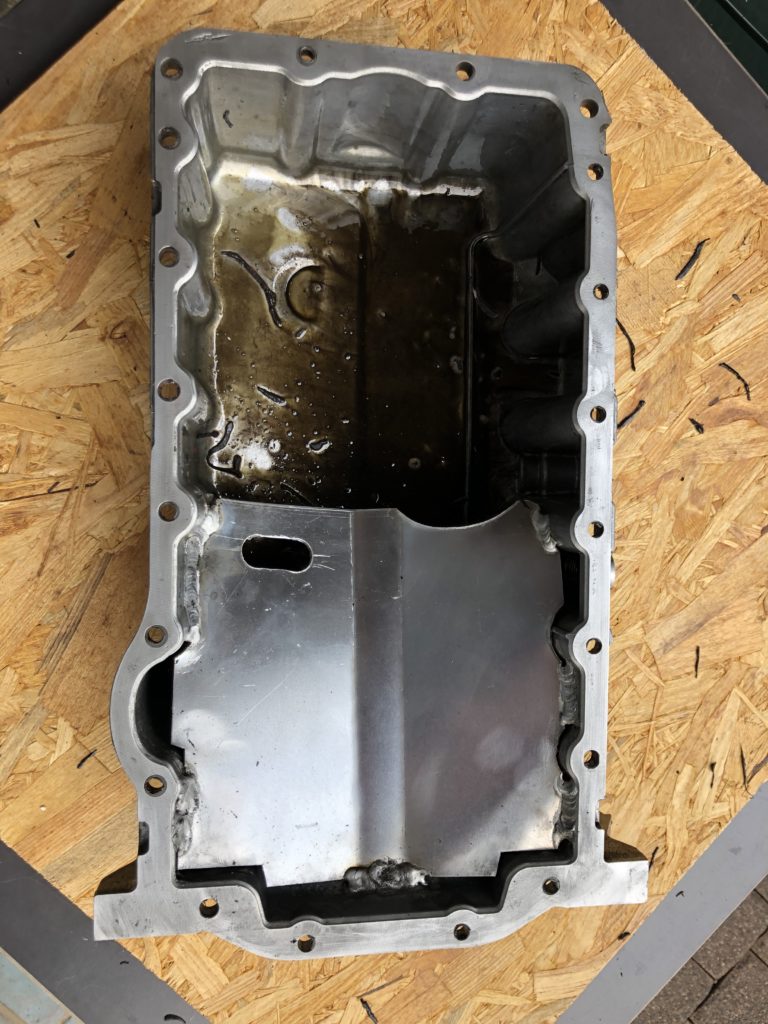
Die Ölwanne ist komplett gereinigt und alle Reste wurden sorgfältig entfernt.
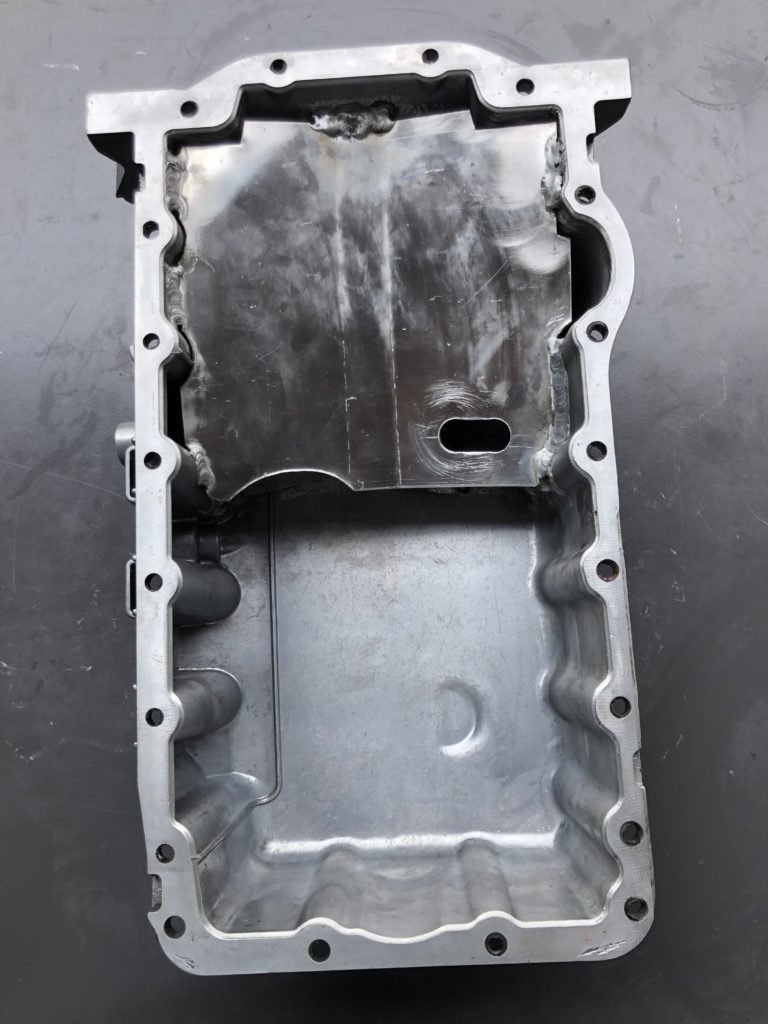
Hier auf dem Bild ist das halbierte Ausgleichswellenmodul, welches bei meinem Motor eingebaut ist, zu sehen. Danke an Marcus Juch der mich darauf aufmerksam gemacht hat.
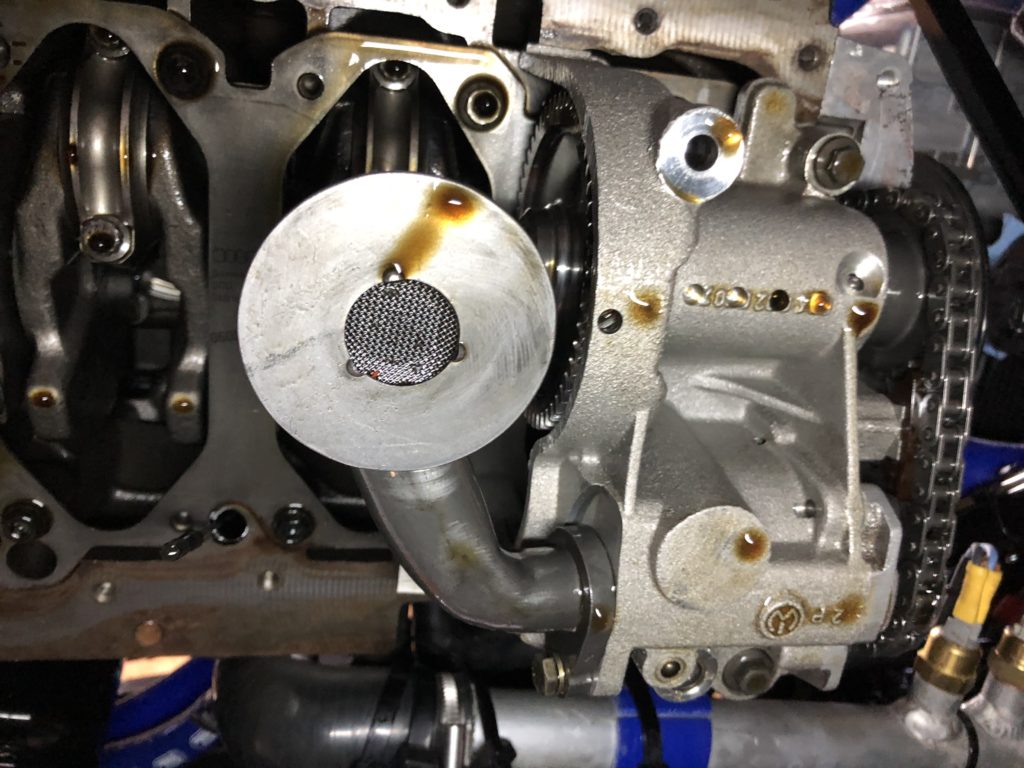
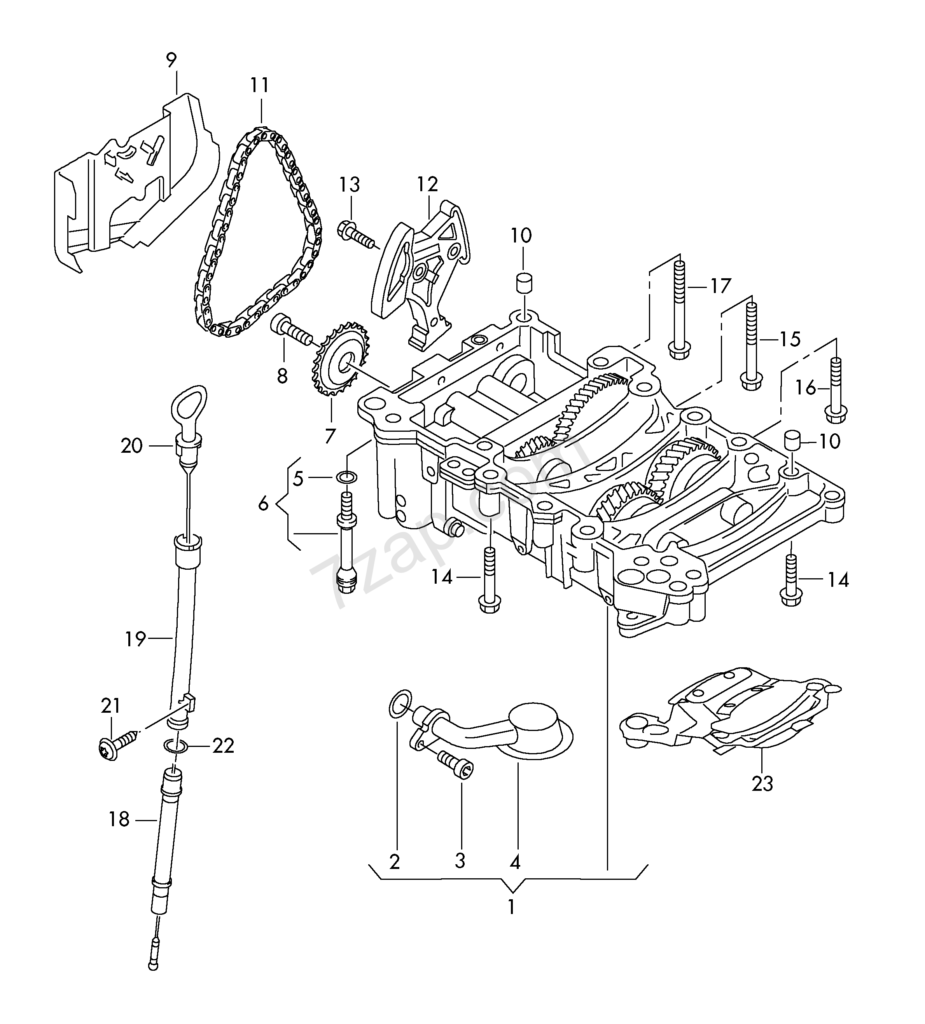